Lead Proponent: Enerkem Inc
Location: Westbury, Quebec and Edmonton, Alberta
ecoEII Contribution: $ 2,913,000
Project Total: $ 10,287,850
Project Background
Enerkem, a company headquartered in Montreal, developed a proprietary thermochemical technology platform that powers the production of renewable biofuels and chemicals from waste rich in biogenic carbon. Over the past ten years, the company has been validating its gasification technology by sourcing municipal solid waste (MSW) from numerous municipalities, and other types of biomass feedstocks, and using it to produce a synthetic gas (syngas) that can then be further processed into chemicals. Enerkem has developed processes and business models to profitably produce cellulosic ethanol from MSW - a new paradigm in the waste valorization business.
Enerkem operates a commercial demonstration facility in Westbury, its first full-scale commercial waste-to-biofuels plant opened in June 2014, in Edmonton, Alberta. The company plans on developing similar facilities in Varennes (Quebec), Rotterdam (The Netherlands), Barcelona (Spain) and several other locations in the USA. These plants will produce methanol and ethanol and enable Enerkem to enter the fuels and commodities market.
The company recognized an opportunity to further evolve and adapt its technology to serve a new market - remote off-grid communities and industries. To that end, Enerkem proposed the project “Modular Compact Combined Heat and Power (CHP) Using Heterogeneous Biomass Wastes” for ecoEII funding. The project was awarded $2.913M to determine whether the use of syngas derived from a mixed feedstock that is typical of that available in remote communities, could fuel an internal combustion engine (ICE) and produce combined heat and power – a low GHG alternative to existing diesel fueled systems.
Results
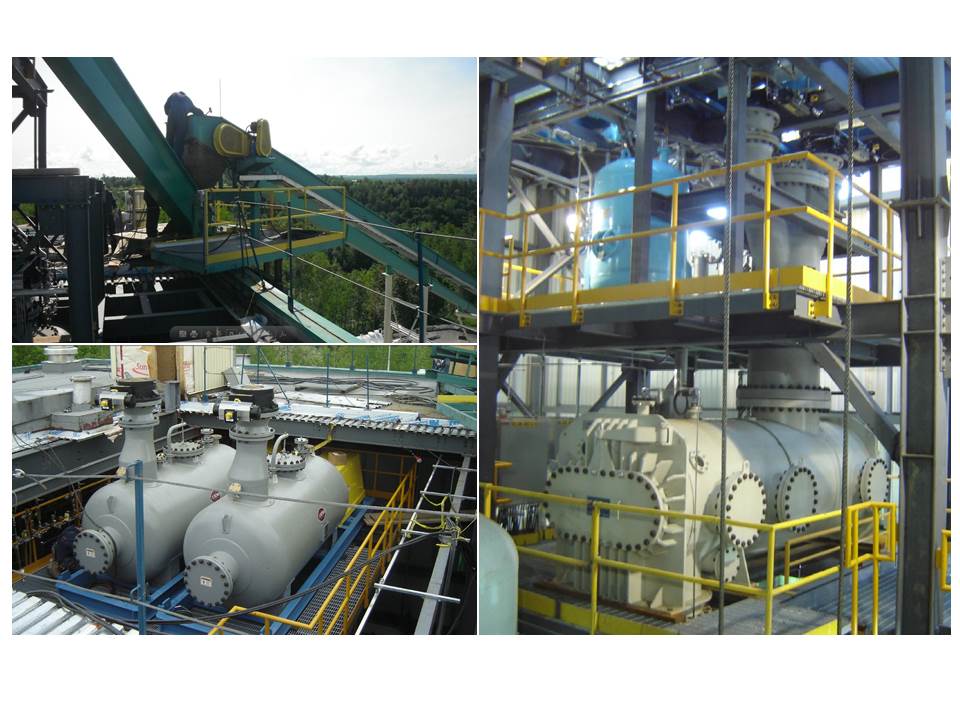
Components of the innovative feeding system: peripherals (top left); paddle mixers (bottom left); and chute and weight belt conveyor (right)
A simulated mixed feedstock was prepared using available biomass and waste representative of that generated by a typical remote community. Source materials were procured in the Eastern Townships (Quebec), at close proximity to Enerkem’s Westbury gasification demo plant. A processing or “finishing step” was then implemented and the result was a rather uniform shredded fluff. The fluff was introduced into Enerkem’s Westbury plant via an innovative feeding system, which eliminated the need for the feed to be pelletized. Pelletization would to be too costly and cumbersome to implement in remote locations. Gasification of the prepared fluff was performed by Westbury’s bubbling fluidized bed gasification reactor, with air as the partial oxidation agent. A low calorific (<6 megajoule per normal cubic meter) clean bio-syngas was obtained.
A GE-Jenbacher ICE was purchased and installed. Low calorific bio-syngas from the gasifier was used to fuel the ICE. Systematic tests were conducted for a total of 355 hours. Coupling of the three process steps (materials preparation and feeding; gasification and syngas cleaning; and use of low calorific syngas to fuel the ICE) was proven to be technically feasible. However, it was observed that the use of low calorific syngas resulted in a 30-40% derating of the ICE’s nominal power output, as compared with that from hydrocarbon fuels such as natural gas.
A cost benefit analysis of the approach taken was performed. It was estimated that the 422kW demonstration project costed $12M, and a new scaled-up 1MW system would cost $15M in capital expenditures. Procurement, storage and preparation of mixed feedstock from local biomass and waste would account for a large part of the capital and operating expenditures of any such project. For example, approximately 8000 tonnes (anhydrous basis) of biomass and waste material would be required per year to power a 1MW system. Communities in extreme northern regions may not have sufficient local biomass to feed such a system. It was therefore determined that the production of biofuels would be more cost effective done on a larger scale, at central conversion hubs (much like Enerkem’s plant in Edmonton). Distribution to remote communities could then be achieved by way of existing fossil fuel transportation networks.
Benefits to Canada
The use of biofuels in place of diesel fuel to power ICEs in remote communities has the potential to reduce greenhouse gas (GHG) emissions - by 1.72 tonnes CO2e per hour for each MWe of power produced, or 13,760 tonnes per year (over 8,000 operating hours).
Next Steps
Enerkem intends to further develop and optimize their gasification platform and pursue the installation of a methanol powered ICE demonstration system at a remote community.