HiPrOx technology for industrial heat and power with CCUS
Project location: CanmetENERGY Ottawa
Timeline: 3 years (2019 to 2022)
Program: Carbon Capture, Utilization and Storage (CCUS)
Project description
High Pressure Oxy-fired (HiPrOx) technology involves the thermal conversion of a fuel in the presence of pure oxygen, under a pressurized environment. Although this form of thermal conversion technology is energy intensive (by requiring pure oxygen and operating at elevated pressures), it offers significant benefits in its ability to process materials that would otherwise be considered problematic. The presence of pure oxygen at elevated pressures allows for the conversion of “hard-to burn” fuels such as petroleum cokes or even pure carbon, in the form of graphite or carbon black. Additionally, by oxy-firing, we eliminate the cooling effect Nitrogen otherwise has when using air-fired combustion. This allows for higher peak temperatures near the flame, which has shown promise in processing applications for very high melting point solids, such as iron ore. The final benefit of oxy-firing technology is the ability to produce a reasonably pure effluent gas stream that contains mostly CO2. This allows for integration of HiPrOx technologies with geologic formation sequestration options or utilization options such as enhanced oil recovery.
Our operating experience; extensive pilot plant design; and Integrated High Pressure Energy Conversion Laboratory, equipped with state-of-the-art infrastructure to support the testing of pressurized, oxy-fired technologies distinguish us in this field. These strengths make our Advanced Combustion and Energy Systems team uniquely positioned to lead significant advances in high thermal efficiency, low-or-no-emissions heat and power cycles.
Our team is also working on pressurized, oxy-fired technology applications for Canadian heavy industries such as the iron and steel, and other mining sectors.
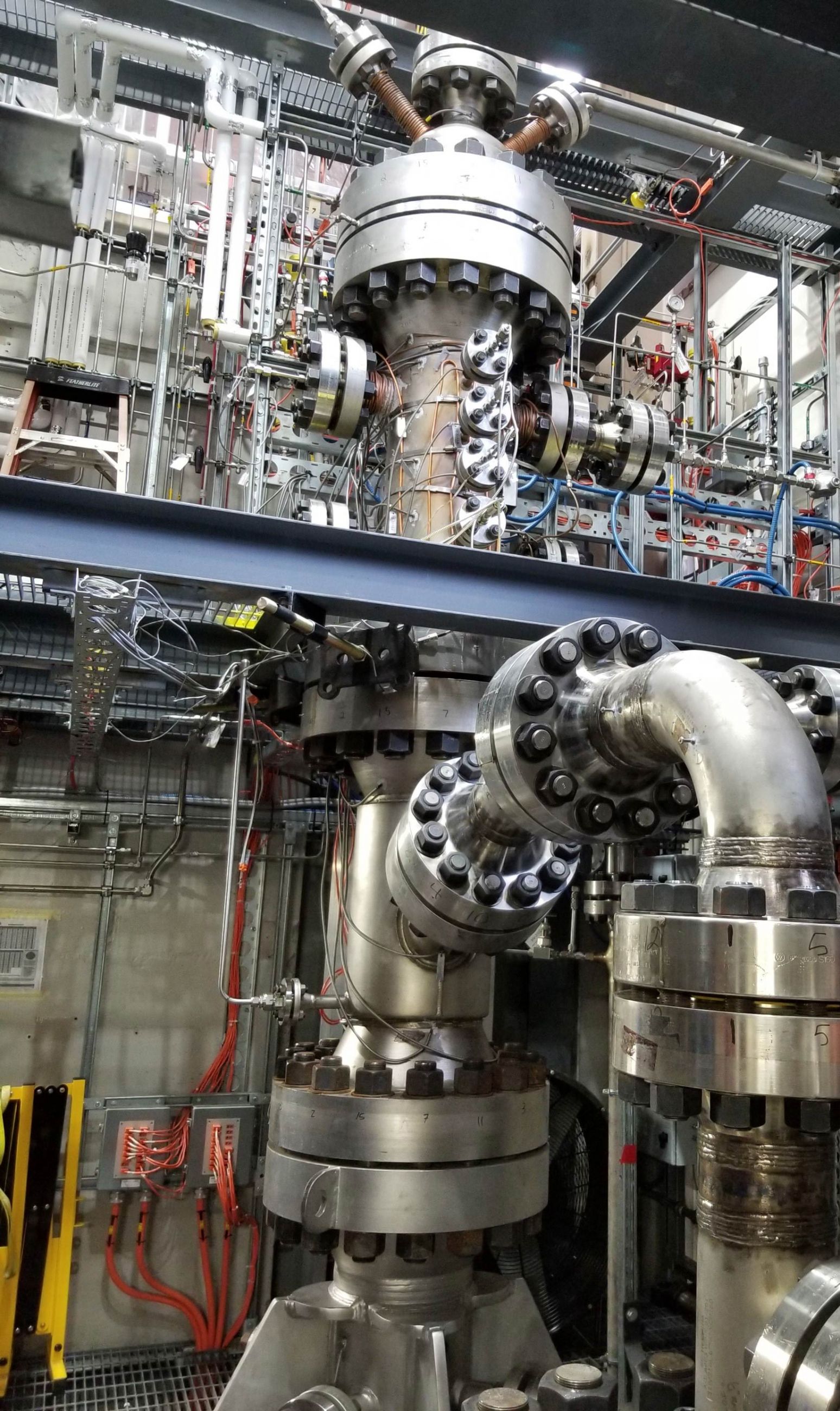
Figure 1: High-pressure oxy-fired reactor (down-fired, entrained flow) at CanmetENERGY Ottawa.
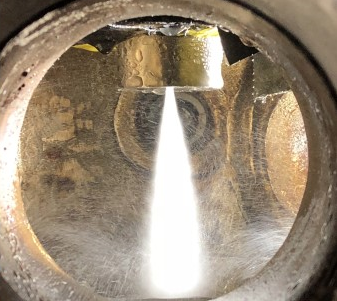
Figure 2: High-pressure spray characterization of Direct Contact Steam Generation (DCSG) burner, at CanmetENERGY Ottawa.
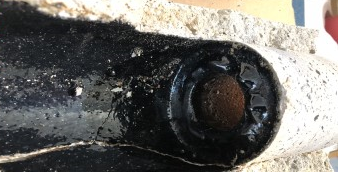
Figure 3: Reactor liner with glassy material around burner entry nozzle, indication of flowing slag in DCSG testing for industrial wastewater treatment.
Contact CanmetENERGY in Ottawa
To learn more about this project, email our Business Office.
Page details
- Date modified: