Lead Proponent: Combustions Solutions Inc. (CSI)
Location: Calgary, AB
ecoEII Contribution: $ 2,147,000
Project Total: $ 4,698,000
Project background
The use of thermal technologies for stimulating recovery of oil from CHOPS (cold heavy oil production with sand) wells has significant potential to increase Canadas’ recoverable oil reserves in the heavy oil basin around Lloydminster. Steam is a typical input for the recovery processes, requiring the use of fresh water and fuel. In most cases, treated fresh water (plus some recycled produced water) is used in 85% efficient gas fired boilers to produce high pressure steam. The process wastes more than 15% of the energy input while producing considerable greenhouse gases (GHG) and releasing nitrous oxides into the atmosphere. An improved method of steam production is therefore required. Recognizing the need, FERST Environmental Inc. developed the concept of using steam and flue gases to stimulate enhanced recovery from CHOPS wells. Of prime importance was the use of a direct contact high pressure burner to vaporize raw untreated produced oilfield water in a reactor at 100% energy efficiency (effectively), while providing maximum well stimulation and recovery. FERST approached Combustion Solutions Inc., a company with considerable burner and combustion experience, and together they developed and proposed the project “Submerged Combustion Vaporizer for Heating and Pressurizing Hydrocarbon Reservoirs” for ecoEII funding. The project was awarded $2,147K to develop, manufacture and operate a high pressure burner where the flue gases are in direct contact with raw untreated water.
Results
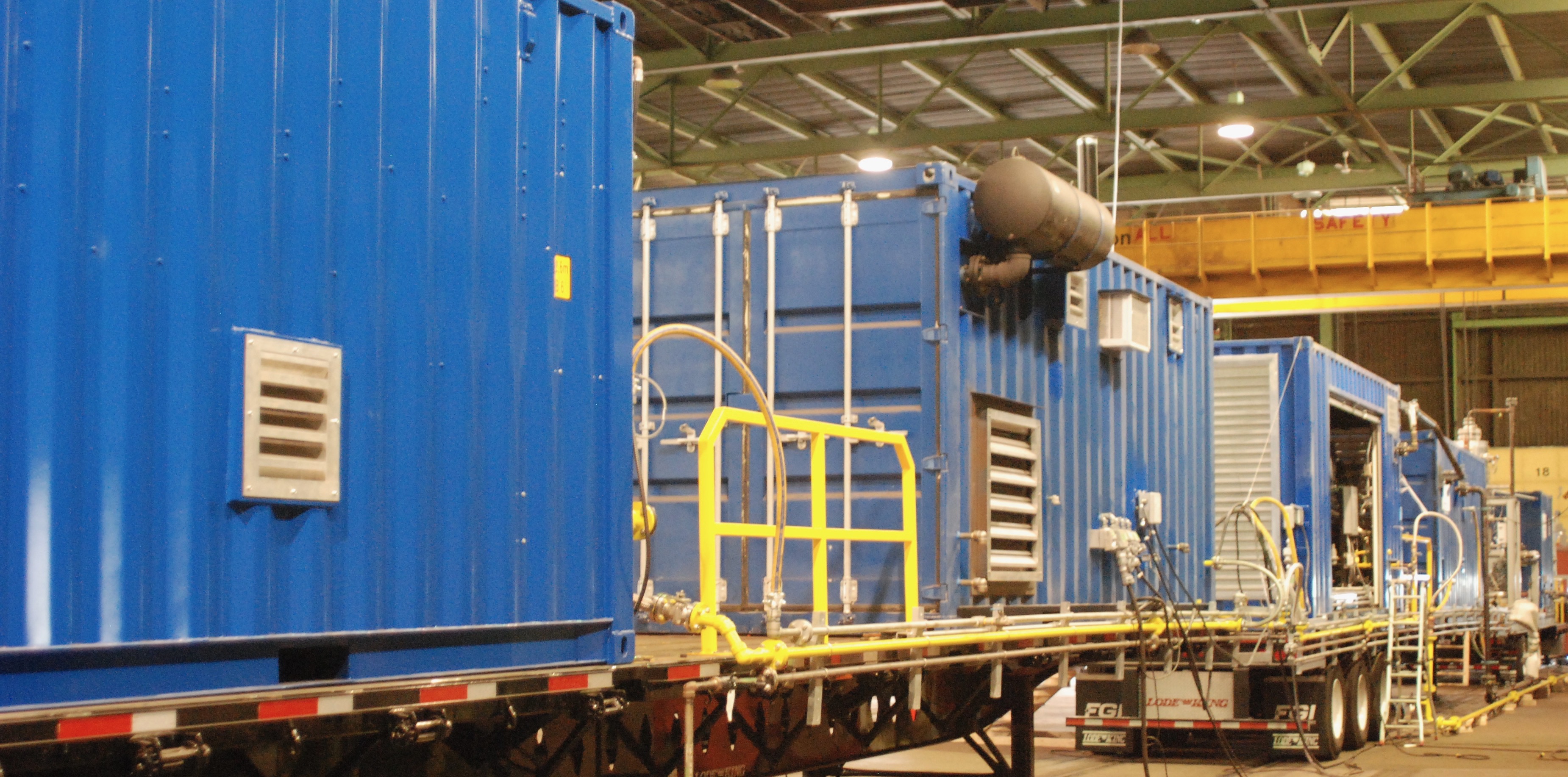
Text version
External view of interconnecting piping and cabling alongside the containerized units for natural gas compression, power generation, electrical room, utilities, combustion air compressor, control room and SCV skid as installed on a series of two 53’ flat deck trailers and one 53’ step deck trailer.
CSI conducted extensive 3D modelling and Computational Fluid Dynamics (CFD) studies to inform the design and development of prototype submerged combustion burner and vaporizer vessels. A key burner design requirement was the use of air cooling to avoid scale buildup inherent in a water cooled heat exchange surface. A second design requirement was the use of combustion gases to provide circulation of water around the burner and separation of the solids, liquids and vapors in the vessel. An initial prototype was fabricated from quartz in order to visualize flame behaviour and confirm accuracy and applicability of CFD simulations. A second similar prototype was fabricated in order to verify temperature profiles of different burner parts.
An alpha prototype was designed and fabricated from carbon steel to the exact geometry and dimensions of the alloy vessel planned for field testing. However, it was decided that the burner would utilize corrosion resistant materials in order to ensure sufficient longevity for the test. The alpha prototype burner and vessel were subjected to extensive testing and used for development of operating procedures. The tests were performed at reduced pressures (<1 barg) and firing rates, as the carbon steel vessel was not capable of meeting full pressure and temperature design conditions. Nevertheless, important findings were revealed from this alpha prototype.
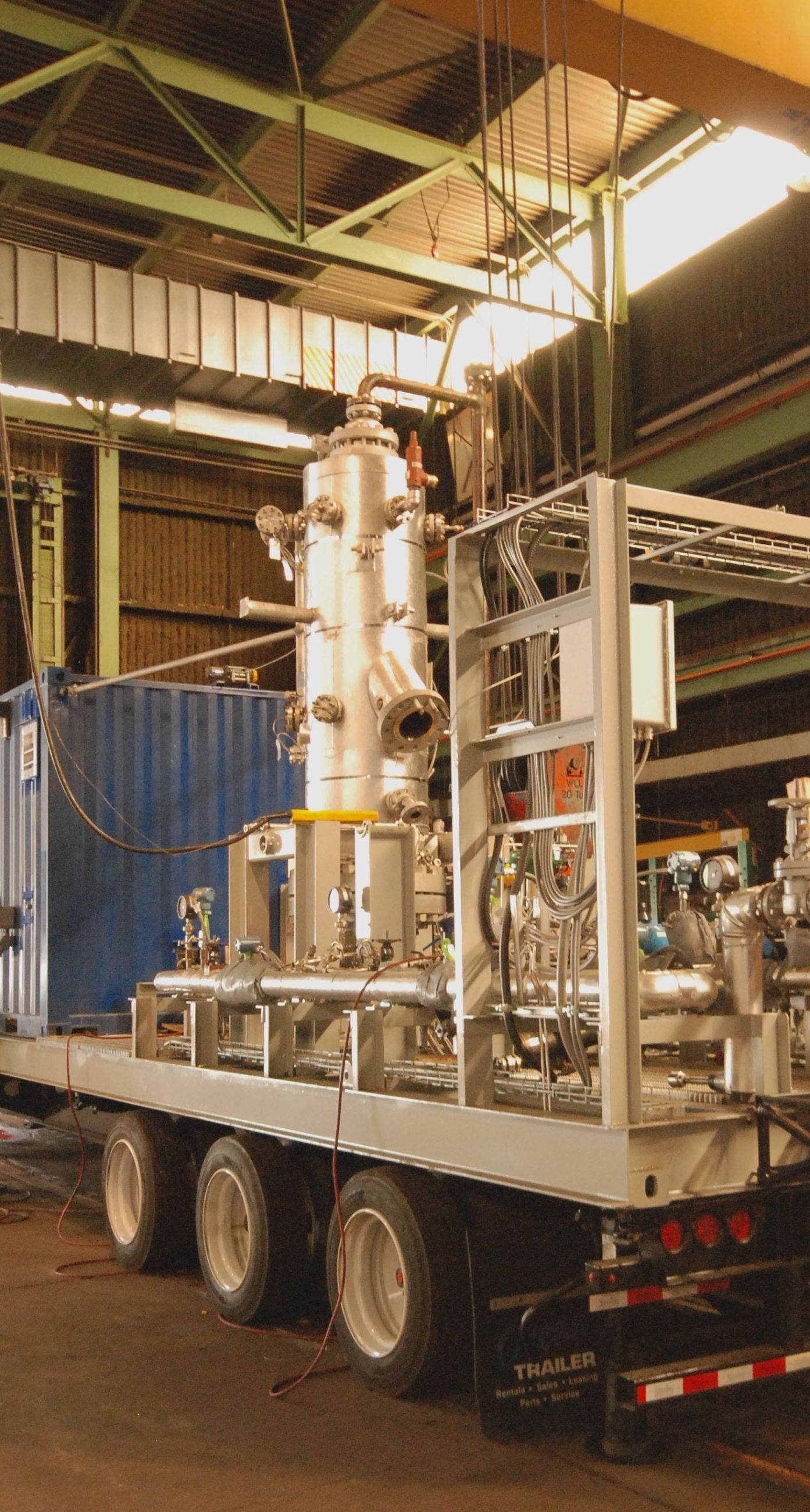
Text version
Submerged Combustion Vaporizer vessel as installed on 53’ step deck trailer
A beta prototype was constructed reusing the alpha prototype burner combined with the corrosion resistant submerged combustion vaporizer (SCV) vessel. The pressure retaining fittings and vessels used for the final beta prototype were designed to meet the requirements of the ASME VIII-1 code and were registered with the authority having jurisdiction in the province of Saskatchewan (TSASK) where the anticipated field trials were to be conducted.
Unfortunately, installation of the beta prototype at a well site, and field testing of the prototype system was not completed due to a substantial downturn in the oil industry. Insight into the suitability of the SCV process in a post-CHOPS Enhanced Oil Recovery (“EOR”) application was gained through collaboration with Petroleum Technology Association Canada (PTAC) and the Saskatchewan Research Council (SRC). A study was conducted and numerical modelling of the SCV EOR process was performed to determine the incremental oil recovery potential. Moreover, as alternative to field testing, the beta prototype was subjected to simulated field tests at CSI’s shop located in Squamish, B.C. Operational tests with an NRCan representative on site were conducted to demonstrate the ability of the beta prototype to generate a mixture of high pressure steam and combustion gases.
Benefits to Canada
Successful demonstration and subsequent adoption of SCV technology in Canada is expected reduce the environmental footprint and cost of oil sands operations when compared with existing practices, which will provide a competitive advantage to the industry.
Next Steps
Further testing and improvement of the SCV technology and process. Pursue opportunities for field testing, collaboration and partnering.