Download PDF of 2012 edition [PDF - 318KB] Footnote 1
Changes to this version, effective July 1, 2012:
Version | Technical changes |
---|---|
2012 |
|
1. Purpose
1.1 The technical requirements
The R-2000 Standard presents the criteria that a new house must meet to be eligible for R-2000 certification. The technical requirements of the R-2000 Standard include measures for the efficient use of energy, improved indoor air quality and better environmental responsibility in the construction and operation of a house.
CommentaryFootnote 2
The goal of the R-2000 Standard is to improve the energy efficiency of new houses without compromising either the interior or exterior environments. These technical requirements include both the performance goals and prescriptive measures that a house must meet to become eligible for R-2000 certification. The requirements are intended to give the builder flexibility in the selection of construction techniques, building products, mechanical equipment, lighting and appliances. The R-2000 Standard is periodically updated to ensure that R-2000 houses represent the leading edge of cost-effective housing technology.
1.2 A voluntary national standard
The R-2000 Standard is a voluntary national standard intended to encourage builder and consumer participation.
Commentary
The technical requirements are applicable to all parts of Canada, although there is provision for the approval of additional, supplemental requirements at the regional level, provided they do not compromise the intent of the technical requirements or the health and safety features of the houses.
1.3 Other applicable documents
The following documents provide additional information on procedures and any revisions to the requirements of theR-2000 Standard since this document was published:
- R-2000 Plan Evaluation, Inspection and Airtightness Testing Procedures and Guidelines
- R-2000 Indoor Air Quality and Environmental Features Pick-List – Appendix A
- Energy Target Calculation Procedure – Appendix B
Commentary
Technical and administrative procedures are combined in the R-2000 Procedures Manual. To ensure that you are working with the most current version of the Standard please refer to Natural Resources Canada’s (NRCan’s) R-2000 web site at www.nrcan.gc.ca/energy/efficiency/homes/20575 or contact your R-2000 service organization.
2. Scope
2.1 Types of buildings to which these requirements apply
This Standard applies to residential buildings that are within the scope of Part 9 of the National Building Code of Canada and are one of the following types
- detached houses, including houses with secondary suites
- attached houses, which include semi-detached houses, row houses, and attached houses with secondary suites
- multi-unit residential buildings (MURBs), which include stacked townhouses, duplexes, triplexes and apartment buildings
Commentary
Please refer to NRCan’s R-2000 Web site at www.nrcan.gc.ca/energy/efficiency/homes/20575 or contact your R-2000 service organization for the current compliance procedures.
2.2 R-2000 technical requirements are in addition to building code requirements
These technical requirements are in addition to provincial building codes and local building requirements or, in the absence of such codes or requirements, to the requirements of the current edition of the National Building Code of Canada. Where an overlap exists, the more stringent requirement shall apply.
Commentary
The R-2000 Standard is not a substitute for local or provincial building codes. Rather, it is an additional set of requirements that are intentionally more stringent in areas of energy efficiency, indoor air quality and environmental responsibility.
3. Compliance
3.1 Only licensed R-2000 builders can construct R-2000 houses
To be eligible for R-2000 certification under the R-2000 Standard, the house must be constructed by a trained and licensed R-2000 Builder. R-2000 trained builders are required to register, build and certify an R-2000 Demonstration Home before they can become licensed.
Commentary
See the Glossary at the end of this standard for the definition of “Licensed R-2000 Builder” and other program terms.
3.2 R-2000 certification
To be eligible for R-2000 certification, the house shall comply with the rules and procedures established by Natural Resources Canada for plan evaluation, inspection, airtightness testing and issuance of an R-2000 certificate.
Commentary
Each R-2000 service organization is authorized to enforce NRCan’s certification procedures. Service organizations shall adhere to minimum requirements set by Natural Resources Canada that include
- R-2000 house application
- plan evaluation
- inspection
- airtightness testing
- issuance of an R-2000 certificate. The R-2000 Procedures Manual provides additional information
3.3 Equivalency
Natural Resources Canada, in consultation with the Canadian Home Builders' Association and/or other industry representatives and the R-2000 service organizationhas the sole authority to accept equivalent materials, products, techniques or qualifications.
Commentary
This clause provides the mechanism by which new products, systems or concepts may be accepted under the R-2000 Standard. It also allows for the resolution of differences of opinion as to whether a given feature meets the intent of the requirements.
4. Building envelope requirements
4.1 Minimum insulation levels
Thermal insulation levels must meet or exceed provincial or local requirements.
Commentary
Because the technical requirements are performance-based standards intended to allow the designer flexibility in how to meet the energy target, minimum insulation requirements are not specified, provided provincial and local requirements are met.
4.2 Basement wall insulation
Insulation shall be applied to a substantial portion of basement walls without any reduction in the RSI value.
Commentary
Although full-height insulation is preferred, the phrase “substantial portion” was added because builders in some areas feel they can avoid moisture problems or the impact of flooding by raising the insulation off the floor slab to a maximum of 300 mm, thus leaving a small gap in the wall insulation. This practice is acceptable, provided the soil gas barrier is maintained and the energy target is met.
4.3 Airtightness requirements
The building envelope shall be constructed sufficiently airtight such that either the air change rate at 50 Pascals is no greater than 1.5 air changes per hour, or the Normalized Leakage Area at 10 Pascals does not exceed 0.7 cm2/m2 (1.0 in2/100 ft22), when measured in accordance with CAN/CGSB-149.10-M86 (Determination of the Airtightness of Building Envelopes by the Fan Depressurization Method).
Commentary
Airtightness is critical to building performance, not only to save energy but also to help ensure durability by preventing moist interior air from leaking outward and condensing within the envelope. Every R-2000 house must have the airtightness of its building envelope tested by a trained and R-2000 licensed airtightness tester to confirm that this requirement has been met. A dwelling unit shall be tested individually without fan depressurization of any adjacent heated space. Envelope area will include that of building components separating a dwelling unit from other dwelling units, heated space and/or the outdoors.
4.4 Window Performance Requirements
Windows shall have the following minimum requirements: double-glazed window with a low-emissivity coating, inert gas fill, and an insulated spacer with a wood, vinyl or fiberglass frame.
Commentary
Decorative windows (side lights, windows in doors, half-circle windows, lead windows, transoms and other specialty glazing products) are allowed provided that the total glazing area of such decorative glazing does not exceed 15% of the total glazing surface area of the house. Canadian ENERGY STAR certified windows meet or exceed these requirements. A list of these products can be found at: http://oee.nrcan.gc.ca/residential/business/manufacturers/search/windows-search.cfm.
5. Mechanical systems
5.1 Space heating, space cooling and water heating systems
5.1.1 Fuel-fired space and water heating appliances
All natural gas-, propane- and oil-fired space and water heating appliances shall have either sealed direct-vent, induced-draft or forced-draft venting systems with electronic ignition and shall be independently vented. Induced-draft and forced-draft vented appliances shall be capable of positive shutdown in the case of venting system blockage.
Commentary
The intent of this requirement is to confirm that all appliances used for space and water heating are not susceptible to combustion spillage since this can pose a serious health and safety risk to the occupants. Naturally aspirated appliances, as well as appliances with standing pilot lights, which are susceptible to spillage, do not meet this requirement. Also, spillage-resistant appliances operate at higher efficiencies, thereby saving energy and reducing operating costs. The prohibition against combined venting systems avoids the problem of one appliance spilling into the other if the house is depressurized. Although the Canadian Gas Association considers B-vents spillage-susceptible, their use is permitted provided the appliance is individually vented. The requirement specifies "venting system blockage" since the available technology, such as pressure switches, is capable of detecting blockage but not other types of failures, such as vent separation.
5.1.2 Natural gas and propane fireplaces
Natural gas and propane fireplaces must be either direct-vent (sealed) and top- or rear-vented; or power-vented and shall also be capable of positive shutdown in the case of venting system blockage. Natural gas and propane fireplaces with doors that open shall not be installed. If the fireplace uses a standing pilot light, its energy consumption will be included in the energy consumption of the house when calculating whether the design meets the R-2000 space heating energy target.
Commentary
The requirement for fireplaces without doors that open reduces the possibility of the appliance becoming susceptible to combustion spillage. Standing pilot lights are discouraged as they could increase the energy consumption of an R-2000 house from 6 to 23 percent with no useful contribution to the space-heating load.
5.1.3 Domestic water heaters
Electric water heaters shall have standby losses not exceeding 65 Watts for a 175 L (40 imp. gal.) tank or 80 Watts for a 270 L (60 imp. gal.) tank, measured in accordance with CSA-C191-M90-04 Performance of Electric Storage Tank Water Heaters for Household Service, or an additional builder-installed insulation blanket with a minimum RSI of 1.8 (R-10). Natural gas and propane water heaters shall have an Energy Factor of 0.58 or greater. Oil-fired water heaters shall have an Energy Factor of 0.57 or greater.
Commentary
Another technique for reducing the water-heating load is to use a drain water heat recovery system as these systems can be accounted for in HOT2000.
5.2 Ventilation systems
5.2.1 Design, installation and balancing of ventilation systems
Mechanical ventilation systems shall be designed, installed and balanced in accordance with CAN/CSA-F326-M91 (R2010) Residential Mechanical Ventilation Systems by an HRAI-certified Residential Mechanical Ventilation Designer or Installer, or an R-2000-recognized equivalent.
Commentary
A properly designed and performing mechanical ventilation system is essential in all houses to maintain good indoor air quality. Compliance with CAN/CSA-F326-M91 (R2010) means that the house automatically meets the ventilation requirements (Section 9.32) of the 2010 National Building Code of Canada.
5.2.2 Ventilation equipment
All heat recovery ventilators (HRVs), energy recovery ventilators (ERVs), exhaust fans and kitchen range hoods shall be certified by the Home Ventilating Institute (HVI).
Commentary
This requirement was expanded in 2001 to include exhaust fans and kitchen hoods. A copy of the HVI Certified Home Ventilating Products Directory can be obtained from HVI’s web site. New types of integrated mechanical and ventilation equipment are rapidly entering the market. Please contact your R-2000 service organization or refer to NRCan’s R-2000 web site at http://www.nrcan.gc.ca/energy/efficiency/housing/new-homes/5085 to determine whether equivalency has been established for any specific new product.
5.3 Wood-burning appliances
5.3.1 Requirements
All wood-burning appliances – including fireplaces, wood stoves and pellet stoves – must be certified as meeting either B415.1-10 Performance Testing of Solid-Fuel-Burning Heating Appliances, or the U.S. Environmental Protection Agency (EPA) wood-burning appliance standards (1990), 40 CFR Part 60.
Commentary
The purpose of this requirement is to provide a minimum level of energy efficiency for wood-burning appliances. The CSA International and EPA standards are emissions-testing procedures that specify maximum levels of flue-gas emissions. Not surprisingly, appliances that produce low flue-gas emissions also burn more efficiently. Site-built fireplaces, with the exception of masonry heaters (discussed in clause 5.3.2 below), are not permitted in R-2000 houses.
5.3.2 Masonry heaters
Masonry heaters shall comply with the requirements specified in the R-2000 Procedures Manual.
Commentary
Masonry heaters are appliances designed to burn rapidly a load of solid fuel mixed with an adequate amount of air at high temperature, to store the heat in the mass of the appliance, and to then gradually release the stored heat. They should not be confused with conventional fireplaces. Builders should confirm that their local authority having jurisdiction accepts masonry heaters.
5.4 Verification of heating, cooling and ventilation systems
5.4.1 Verification of heating and cooling systems
Heating and cooling system nameplate information shall be verified by a licensed R-2000 inspector in accordance with R-2000-recognized inspection procedures.
Commentary
This requirement is intended to ensure that the specifications of the installed heating and cooling systems have been documented. This information will be reflected in the as-built HOT2000 run. Refer to the R-2000 Plan Evaluation, Inspection and Airtightness Testing Procedures and Guidelines section of the R-2000 Procedures Manual for information on these procedures.
5.4.2 Verification of ventilation systems
Ventilation systems shall be inspected by a licensed R-2000 inspector in accordance with R-2000-recognized inspection procedures.
Commentary
This requirement is intended to confirm that the specifications of the installed equipment are documented and the installation complies with clause 5.2 of this Standard. Refer to the R-2000 Plan Evaluation, Inspection and Air Tightness Testing Procedures and Guidelines section of the R-2000 Procedures Manual for information on these procedures. This information will be reflected in the as-built HOT2000 run.
5.5 Carbon monoxide detectors
Carbon monoxide detector(s) conforming to CAN/CSA-6.19-01 (2006) Residential Carbon Monoxide Alarming Devices shall be installed in houses/each suite of residential occupancy containing either fuel-fired appliances or attached garages.
Commentary
This requirement addresses concerns about potential combustion spillage from fuel-fired appliances and attached garages. The following describes the recommended best practices for complying with this requirement:
- The carbon monoxide detectors(s) shall be equipped with an integral alarm which satisfies the audibility requirements of CAN/CSA-6.19-01(2006) Residential Carbon Monoxide Alarming Devices.
- The carbon monoxide detector(s) shall be permanently connected to an electrical circuit and shall have no disconnect switch between the over current device and the carbon monoxide detector.
- The carbon monoxide detector(s) shall be installed either inside each bedroom, or if outside, within 5 m, measured following corridors and doorways, of each bedroom door.
- The carbon monoxide detector(s) shall be mechanically fixed at a height recommended by the manufacturer.
- Where a fuel-burning appliance is installed in a service room that is not in a suite of residential occupancy, a carbon monoxide detector shall be installed either inside each bedroom, or if outside, within 5 m, measured following corridors and doorways, of each bedroom door in every suite of residential occupancy that shares a wall or floor/ceiling assembly with the service room, and in the service room. (Note: Item 5) applies to Multi-Unit Buildings only).
5.6 Ducts carrying outdoor air
Ducts that carry outdoor air through a conditioned space shall be insulated with a minimum of RSI 0.5 (R-3) and have a sealed vapour barrier.
Commentary
The intention of this requirement is to help control heat loss and condensation problems on any ductwork that carries outdoor air through a conditioned space. The insulation requirements of this clause are consistent with those of CAN/CSA-F326-M91(R2010) Residential Mechanical Ventilation Systems.
5.7 Unvented combustion appliances
No unvented combustion appliances shall be installed unless specific provision is made to exhaust the products of combustion to the outdoors.
Commentary
This clause addresses the health, safety and indoor air quality concerns created by the operation of unvented combustion appliances. Unvented gas heaters are not permitted. Interlocking the range hood control to the gas range is suggested, provided it meets the manufacturer’s installation requirements. Gas-fired ranges are permitted, provided a provision is made to exhaust the products of combustion to the outdoors.
6. Energy performance targets
6.1 Space heating and domestic hot water energy target
The annual household energy consumption target for space heating and domestic hot water heating combined shall be that calculated using the current authorized version of HOT2000 and multiplied by 50 percent.
Commentary
One of the most important components of the R-2000 Standard is the energy target, based on the combined consumption of energy for space heating and domestic water heating. The energy target is calculated for each house based on its size, location and fuel type. The equations for calculating the energy target are embedded in the HOT2000 program but need to be multiplied by 50% by the R-2000 plan evaluator. The energy target equations are presented in Appendix B – Energy Target Calculation Procedure.
6.2 Determining compliance with the energy target
Compliance with the energy target shall be determined by a licensed R-2000 plan evaluator by using either the current authorized version of HOT2000 or the Pre-Approved Evaluation Method, as described in the R-2000 Plan Evaluation, Inspection and Airtightness Testing Procedures and Guidelines section of the R-2000 Procedures Manual.
Commentary
The Pre-Approved Evaluation Method has been developed so that a house, or a group of similar houses, can be designed and pre-approved as meeting the energy target regardless of their orientation or insignificant changes in their design. With either method the detailed procedures set out in the R-2000 Procedures Manual must be followed. Once compliance has been demonstrated with either method, the house is deemed to have met the energy target.
7. Indoor air quality
7.1 Indoor air quality
At least three of the indoor air quality features identified in the current version of the R-2000 Indoor Air Quality and Environmental Features Pick-List shall be used in the house.
Commentary
Superior indoor air quality is one of the features of an R-2000 house. While adequate ventilation is part of an effective control strategy, the most effective way to improve indoor air quality is to reduce or eliminate sources of pollutants. Proper materials selection is a key area where builders can make a difference in the air quality of the house. The R-2000 Indoor Air Quality and Environmental Features Pick-List is now produced as a separate document so that it can be more easily updated and any regional considerations added. The R-2000 Pick-List is included in Appendix A. Copies of the most recent pick-list are available from R-2000 service organizations and NRCan’s R-2000 web site at www.nrcan.gc.ca/energy/efficiency/homes/20575
8. Water conservation and environmental features
8.1 Water conservation
Plumbing fixtures shall meet the following criteria:
- Toilets: Water-saver or ultra-low flush units using 4.8 litres/flush (1.3 U.S. gallons/flush) or less.
- Showers: Low-flow showerheads using 7.6 litres/min. (2.0 U.S. gallons/min) or less when tested at 551 kPa (80 psi).
- Faucets: Lavatory faucets using 5.7 litres/min. (1.5 U.S. gallons/min) or less when tested at 413 kPa (60 psi).
Commentary
The R-2000 Standard recognizes the need to improve the environmental performance of housing both during construction and ongoing operation. This clause is intended to reduce the amount of water consumed on a daily basis in the house. The values chosen reflect both desired performance and market availability, and are based on WaterSense® specifications (http://www.epa.gov/watersense/).
8.2 Environmental features
At least two of the environmental features identified in the current version of the R-2000 Pick-List shall be used in the house.
Commentary
The R-2000 Indoor Air Quality and Environmental Features Pick-List is now produced as a separate document so that it can be more easily updated and any regional considerations added. The R-2000 Pick-List is included in Appendix A. Copies of the most recent pick-list are available from R-2000 service organizations and NRCan’s R-2000 web site at www.nrcan.gc.ca/energy/efficiency/homes/20575.
Glossary
Licensed R-2000 builder
A builder, who has successfully completed an R-2000 Builder Workshop, has built a certified R-2000 Demonstration Home, has taken periodic R-2000 technical updates as required, and holds a valid R-2000 Builder Licensing Agreement with Natural Resources Canada.
R-2000 trained builder
A builder who has been trained but has not yet successfully completed a certified R-2000 Demonstration House to prove that he/she has mastered the knowledge taught in the R-2000 Builder Workshop.
R-2000 service provider
An individual holding a valid R-2000 license in one or more of the following categories: R-2000 Plan Evaluator, R-2000 Inspector, R-2000 Airtightness Tester.
R-2000 demonstration home
The first home that an R-2000 trained builder builds to the R-2000 Standard. The house has been evaluated by a licensed R-2000 plan evaluator to determine compliance as designed. It has been registered with an R-2000 service organization and entered into the national R-2000 database. After construction, the house must be inspected and air tested to determine whether it meets the R-2000 Standard as built. If the house meets all R-2000 requirements, it is certified as an R-2000 demonstration home.
Certified R-2000 home
A home constructed by a licensed R-2000 builder that meets the R-2000 Standard as built, and as determined by a successful completion of the R-2000 quality assurance process, consisting of a plan evaluation, inspection (building envelope and mechanical systems), and airtightness test, and that has been issued a certificate by NRCan or its authorized designate.
R-2000 service organization
the R-2000 service organizations administer the R-2000 Standard on a regional basis.
Appendix A
R-2000 Indoor Air Quality and Environmental Features Pick-List
The R-2000 Pick-List
A. Indoor air quality features
The dwelling shall incorporate a minimum of three of the following indoor air quality features (from A-1 to A-9) inside the air barrier or air/vapour barrier:
- Carpeting - Except as noted, carpeting used in the house shall meet either of the following criteria:
- The carpet shall be labeled under the Canadian Carpet Institute’s Green Label Program; or
- A non-Green Label carpet shall cover no more than 50 percent of the interior floor area. In this case, the interior floor area does not include the basement floor area. The following floor coverings are exempt: wool or cotton area rugs, and carpeting that has latex-free backing. These exempt floor coverings shall not be glued to the floor and cannot have under pads.
- Air filtration - One of the following shall be installed:
- A medium-efficiency air filter with a minimum MERV rating of 13 or 10 percent ASHRAE average dust spot efficiency, installed where air-circulating heating, or cooling systems are used; or
- An electronic air cleaner permanently installed in the forced-air system ductwork; or
- An air filtration system (e.g., activated carbon, catalytic air cleaners, etc.) in the forced-air system ductwork that is capable of removing gaseous contaminants from the air.
- Paints and varnishes - All liquid coatings used indoors, including wood floors, shall have low-VOC content as determined by a third party certification programsFootnote 3. Pre-finished items are allowed.
- Flooring adhesives - All finish flooring adhesives shall be water dispersion, low-VOCFootnote 4 formulations or be pre-adhesive types.
- Kitchen cabinets and bathroom vanities - Cabinets and vanities shall be solid wood or, if made from manufactured wood products, shall be made from formaldehyde-free fibre board or particleboard meeting the E-1 European standard or the HUD Standard, 24 CFR Part 3280.308; or have all exposed surfaces sealed with an Environmental Choice-approved sealer or a low-VOCFootnote 5 sealer.
- Vinyl flooring - All vinyl flooring shall be either linoleum or synthetic vinyl tile. Sheet vinyl flooring shall not be used.
- Particleboard underlayment - All particleboard-flooring underlayment shall meet the E-1 European standard or the ANSI A208.1-1993 Table B standard; or have all surfaces sealed with an Environmental Choice-approved sealer or a low-VOCFootnote 6 sealer; or be pre-finished.
- Sub-slab depressurization system - Install an active sub-slab depressurization system to control the entry of radon and soil gases into the house.
- Indoor moisture control - Choose one of the following options:
- Provide control measures to isolate a crawl space or space underneath a basement floor so as to minimize the transmission of moisture and soil gases into the occupied space; or
- Provide insulation with an RSI of 0.9 (R-5) or greater under the entire floor slab area; or
- Include basement waterproofing, as opposed to damp-proofing, or a free-draining layer, as a measure to keep the foundation drier and therefore less prone to mould development.
B. Environmental features
The dwelling shall incorporate a minimum of two of the following environmental features (from B-1 to B-14).
Insulation – As a minimum, use entirely in the attic, the main walls or the basement walls.
- Glass Fibre Insulation - Meets or exceeds the requirements of the EcoLogoCM Program for raw material from recycled glass.
- Cellulose Insulation - Meets or exceeds the requirements of the EcoLogoCM Program for raw material from recycled paper.
- Mineral Fibre Insulation - Meets or exceeds the requirements of the EcoLogoCM Program for recycled raw material.
- Insulation Made from Plastic - Meets or exceeds the requirements of the EcoLogoCM Program for recycled content.
Sheathing/Drywall - Product must replace equivalent conventional product throughout the house.
- Fibreboard - Product is made from recycled newsprint and/or wood fibres.
- Siding - Product is manufactured from factory and sawmill waste.
- Drywall - Product contains recycled gypsum and/or newsprint.
Interior framing and trim - Product must replace equivalent conventional product for entire floor.
- Steel Studs - A minimum of 23 percent of the raw material is recycled steel.
- Studs and trim - Product is manufactured from sawmill cut-offs and waste, and is urea-formaldehyde free.
- Foundation and/or under-slab drainage - Install a mixture of post-consumer glass and crushed rock or stone around the foundation wall and/or under the slab-on-grade. Product must replace equivalent conventional backfill in its entirety.
- Energy-efficient appliances - Builders who include major electrical household appliances with the sale of the home shall provide appliances that meet the Energy Starâ technical specifications, where applicable. For appliance categories that are not part of the ENERGY STAR Program, the energy performance of the appliances must be in the upper 33 percent of the EnerGuide rating for that appliance category.
Reduction in energy use
- Energy target - The house's predicted energy consumption is at least 15 percent less than its Energy Target (greenhouse gas reduction measure).
- Cooling systems - The cooling system shall be ENERGY STAR certified.
- Energy-Efficient Motors - The house air distribution system shall be equipped with an energy-efficient motor (known as brushless DC motors, DC variable speed motors and ECM™ motors). The furnace blower or the air handler can contain the energy-efficient motor.
Appendix B
Energy target calculation procedure
The annual energy consumption target for complying with the R-2000 Standard is determined from the following equation:
Annual Energy Target = [QS + QW] * 0.5
where:
Qs = space heating energy consumption target
QW = domestic hot water energy consumption target
The annual space heating energy consumption target is calculated using the following equation:
QS = S*(49*DD/6000)*(40 + V/2.5)
where:
S = 4.5 megajoules (MJ) for fuel-fired space heating systems, or
S = 1.0 kilowatt hours (kWh) or 3.6 megajoules (MJ) for electric space heating systems
DD = Celsius heating degree-days for the locality
V = Interior heated volume, including basement, in cubic meters
The annual domestic hot water heating energy consumption target is calculated using the following equation:
QW = 4745*W * (55-Tw) / (55-9.5)
where:
Tw = local water mains temperature
W = 1.72 kilowatt hours (kWh) or 6.19 megajoules (MJ) for fuel-fired DHW systems
W = 1.075 kilowatt hours (kWh) or 3.87 megajoules (MJ) for electric DHW systems.
Main floor heating set point | 21.0°C |
Basement heated | Yes |
Basement cooled | No |
Basement set point | 19.0°C |
Basement separate thermostat | No |
Allowable daily temperature rise | 3.5°C |
Interior loads, lighting | 3.0 kWh/day |
Interior loads, appliances | 14.0 kWh/day |
Interior loads, other | 3.0 kWh/day |
Average exterior use | 4.0 kWh/day |
Hot water load | 225.0 L/day |
Hot water temperature | 55.0°C |
Fraction of internal gains in basement | 0.15 |
Adult occupants | 2, at home 50% of time |
Child occupants | 2, at home 50% of time |
Terrain, building site | Suburban, Forest |
Local shielding, walls | Very Heavy |
Local shielding, flue | Light local shielding |
Ventilation sizing, including HRV | as per CSA Standard F326 |
Mechanical ventilation rates for evaluating the energy target
To comply with the R-2000 Standard, the ventilation energy use calculation assumes that a house is ventilated at a monthly average rate of 0.30 normal air changes per hour, with a minimum of 25 L/s and a maximum of 100 L/s, of combined natural and mechanical ventilation. The ventilation rates are provided mainly for the purpose of modelling and NOT for the purpose of sizing the ventilation equipment or systems. Ventilations systems must be designed and installed in accordance with CAN/CSA-F326-M91(R2010) Residential Mechanical Ventilation Systems. The following graph shows the HOT2000 modelling of monthly average ventilation rates:
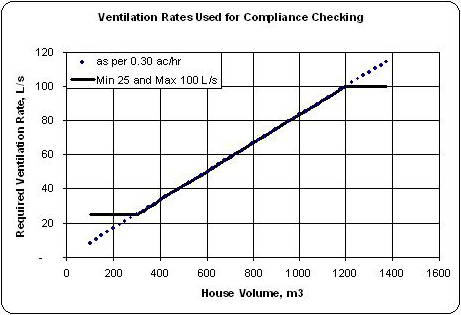
Ventilation Rates Used for Compliance Checking
Text version of chart: Ventilation rates used for compliance checking
This is a line graph depicting the ventilation rates used for checking compliance checking. The x-axis, labelled “House Volume (m3)” increases from 0 to 1600 at increments of 200. The y-axis, labelled “Required Ventilation Rate, (L/s)” increases from 0 to 120 at increments of 20.
There are two data sets represented by a dotted line and a solid line. A legend in the top left corner identifies these group labels as: dotted line, As per 0.30 ac/hr and solid line, Min 25 and Max 100 L/s.
The dotted line begins at 100, 10 and terminates at 1400, 120. The solid line begins at 100, 25 and plateaus until 300, 25 where it overlaps the dotted line until 1200, 100 where it plateaus until 1400, 100.
Between 300, 25 and 1200, 100 both data sets intersect at each point on the graph and follow the same growth rate.
*This standard is subject to revision. Please refer to the NRCan R-2000 web site, or contact your R-2000 service organization (formerly referred to as R-2000 delivery agents) for the current version of this standard.
R-2000 is an official mark of Natural Resources Canada.