Air leakage control is the single most important retrofit activity, and it should be considered first in any upgrade strategy for your house. Air leakage control is essential. Every time you insulate, install or upgrade the air barrier system, ensure that moisture does not enter the insulation or building envelope. Comprehensive air leakage control is the systematic identification and sealing of as many air leakage paths as possible with weatherstripping and caulking and by applying gaskets and tapes. Did you know that your windows, doors, cracks in the walls, interior trim and even light fixtures in the ceiling are potential leakages areas?
Contracting the work
Homeowners can usually do a relatively effective air sealing job if they have the time and patience and are conscientious about air sealing in areas that can be difficult and uncomfortable to work in (for example, the attic). However, professional air sealers can usually do a much better job because of their experience in locating and sealing leaks.
Contractors may use a depressurizing fan door (sometimes called a blower door) with smoke pencils to locate air leaks and use specialty caulking and sealants. The infrared scanner, used in conjunction with a blower door test, is also a powerful tool to locate air leaks and missing insulation.
Many air sealing companies also offer testing and assessment of ventilation and combustion air requirements, including testing for backdrafting of combustion gases.
Effect on a house as a whole
As the envelope is tightened, household humidity levels rise and can create condensation and moisture problems. Additionally, as less fresh air is circulated through the house, less air becomes available for combustion appliances. Therefore, an important part of comprehensive air leakage control is attention to controllable whole-house ventilation and combustion-air supply. Refer to Part 9.4, Ventilation and combustion air, for ways to control the ventilation in your home.
Proper ventilation ensures healthier indoor air quality which includes controlling the humidity in the home. For more information on indoor relative humidity, refer to Part 2.4.2, How much humidity?, and Figure 2-11, Sterling Chart.
Each house will respond to comprehensive air sealing in its own unique way, so monitoring is important. Older houses may require remedial measures before air sealing.
For example, moisture can accumulate in the walls over time, resulting in mould buildup. This situation may require cleanup and replacement of the affected materials and installation of an improved air and vapour barrier. The best way to avoid problems is to understand how they occur and to take steps to control humidity and ventilation.
Furnaces, water heaters, fireplaces, woodstoves and any other fuel-burning appliances require air for combustion and for exhausting the products of combustion out of the house. If there is not enough air, the chimney or flue could spill dangerous gases into the house.
Humidity, ventilation and combustion air are discussed in more detail in Section 9, “Operating your house.”
4.1 Finding leakage areas
Air leaks occur where there is a hole in the building envelope and a pressure difference. In winter, the house tends to operate like a chimney due to the stack effect, where air enters the house at lower levels and exits at the upper levels and ceiling.
4.1.1 How to locate air leaks
Identifying the specific leakage areas requires a little detective work. For optimal results, hire an air sealing contractor or professional energy advisor. However, you can also do it yourself, as described below.

Figure 4-1 Do-it-yourself leak detector
Text version
Illustration of a hand holding two burning incense sticks next to an electrical outlet with smoke drifting away from the outlet.
Make yourself a leak detector (see Figure 4-1) – all you need are burning incense sticks. Hold two or three together for more smoke and easier detection. Powerful leaks will cause the smoke to dissipate and the tips of the incense to glow. Slower leaks will cause the smoke to trail away or move toward the leak.
On a cold day, check for drafts in all suspected areas. It is easier to locate air leaks on a windy day. Check for possible leaks on the interior walls and features, such as electrical outlets and switches, because there may be a direct route through partition walls or along floor joists to the outside that should be sealed.
You can perform a rudimentary fan test by closing all windows and doors and turning on all the exhaust appliances in the house, such as bathroom and kitchen fans, clothes dryers (on cool cycle) and any portable fan placed in a window (if you can seal around it). However, before starting, turn off any fuel-fired space and water heaters to prevent backdrafting of combustion gases. You can now go around the house with your leak detector and identify and mark the air leakage locations that should be sealed.
4.1.2 Checklist of air leakage areas
A few areas deserve special attention (illustrated in Figure 4-2) but do not limit your detective work to just these places.
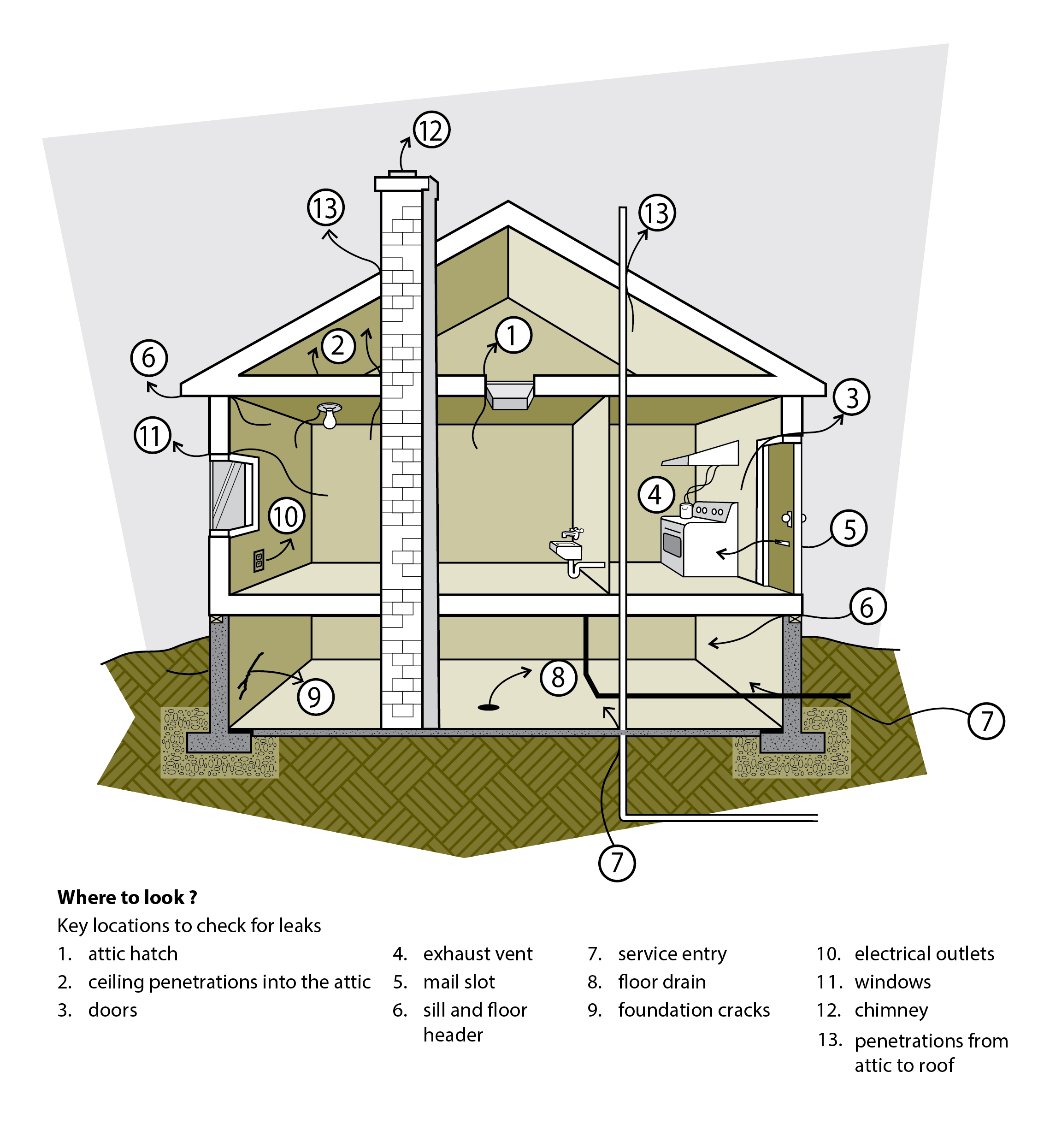
Figure 4-2 Typical leakage areas
Text version
Cutaway of one-storey house with sloped roof and basement showing 13 numbered key locations to check for leaks, including an attic hatch, ceiling penetrations into the attic, doors, exhaust vent, mail slot, sill and header, service entry, floor drain, foundation cracks, electrical outlets, windows, chimney, and penetrations from attic to roof.
Inside the main living areas, check the following:
- window glazings for tightness and around the window sash and casing
- around the door, including the threshold and around the door frame
- electrical outlets and switches, including ones on interior walls
- exhaust fans and vents (these should vent to the outside and close properly when not in use)
- corners where two walls meet with an imperfect seal
- light fixtures in the ceiling
- interior trim and baseboards
- cracks in the wall finish or ceiling
- the joint where a wood frame wall joins a masonry wall or chimney
- doors and hatches into unheated attics
- fireplace dampers and fireplace bricks
- behind bathtubs and under sinks
- above sliding pocket doors
- around plumbing pipes and ductwork
Inside the attic, check the following (you may have to move aside existing insulation):
- around the plumbing stack and any other pipes entering the attic
- around wires or ceiling light fixtures that penetrate the attic floor
- around ducting that enters the attic from inside the house
- at the junction of the ceiling with interior wall partitions
- around attic access doors
- around chimneys
- along any shared walls
- the ceiling area in bathrooms and above stairwells
Inside the basement, check the following:
- where the wood-frame wall (sill plate) meets the masonry (concrete or stone) foundation or where joists penetrate the masonry wall
- holes or gaps where the electrical service, gas service or oil fill pipes go through the wall; be careful around electrical wires and gas pipes; do not disturb connections
- holes for wiring, cabling, plumbing, and air conditioning pipes going into internal and external walls
- leaky ducting or poorly fitted hot air registers or cold air intakes
- around window and door framing
- cracks in the foundation wall and slab
- floor drains
- the base of the chimney or flue
Safety warning:
See Part 1.4, Health and safety considerations, for a warning about asbestos and vermiculite insulation.
4.2 Caulking and other air sealing materials
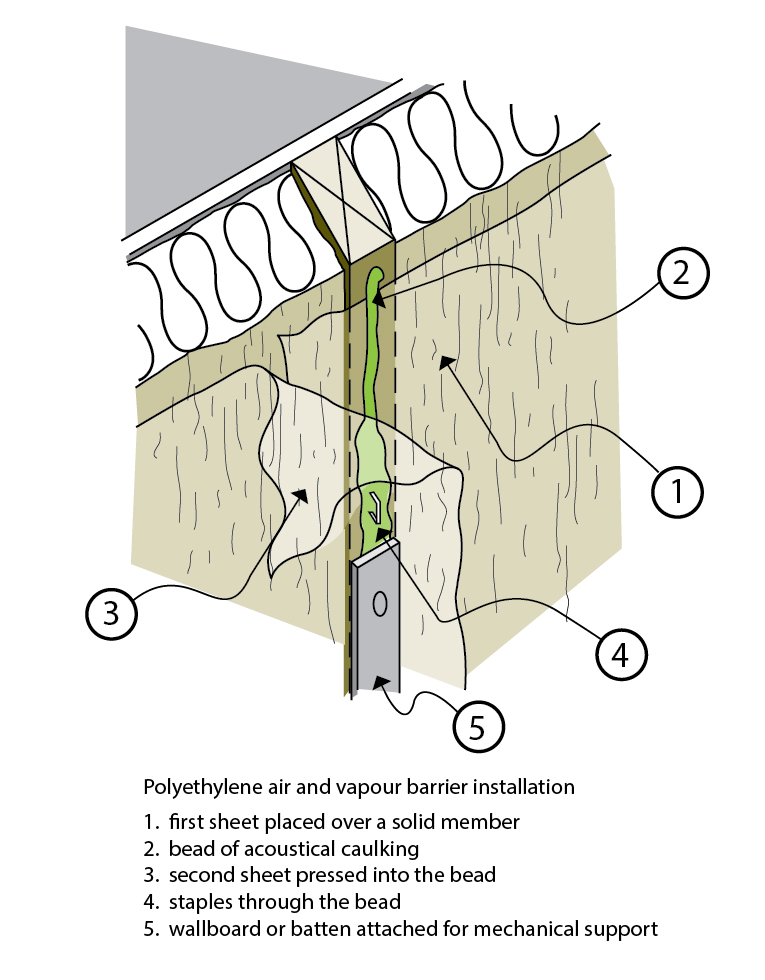
Figure 4-3 Sealing air and vapour barrier seams
Text version
Cutaway of a wall showing the five steps to installing polyethylene and vapour barriers: 1) First sheet placed over a solid member. 2) Bead of acoustical caulking. 3) Second sheet pressed into the head. 4) Staples through the bead. 5) Wallboard or batten attached for mechanical support.
Air seal cracks and penetrations on the inside surface of exterior walls, ceilings or floors to prevent air from escaping into the walls and roof.
On the exterior, caulk cracks that will allow water and insect entry. If you are painting the house, try not to plug the joints in the siding and use a permeable paint or stain. The outside of the walls must be able to dispel moisture. For these same reasons, do not paint stucco; special sealers are available for stucco.
4.2.1 Caulking basics
Buy a good quality caulking gun that easily fits your hand to avoid strain. The gun should have a pressure release lever. A thumb release is convenient since it permits one-hand operation, as are a nozzle cutter and tube piercer.
Choose the right sealant for the job. People often have a bad experience when they first try caulking because they purchase a low quality or inappropriate caulk and/or caulking gun. Choose premium caulks for durability. Practice running and smoothing beads before starting on the actual See Figures 4-3 and 4-4 for guidelines for applying caulking.
See Part 3.3, Air barrier materials, for a guide to the different types of caulking.
- Use wide sheets to minimize seams.
- Overlap all seams and edges over a solid backing such as a stud.
- Run a bead of non-hardening acoustical sealant between the overlapped sheets over the support.
- Staple through the sheets and the bead of sealant. Avoid or minimize the use of all other staples.
- The finish (for example, drywall) acts as an anchor, securing the seam. If the polyethylene is recessed in the wall, a batten nailed over the seam can provide mechanical support.
- Seal all penetrations. Where possible, penetrate at a solid backing such as plywood or drill through a single or double stud.
Safety warning:
Use non-combustible caulking around heat sources (chimney, light fixtures, fan motors, etc.). Silicone or polysulphide sealants usually work well. Special high-temperature silicones are available for flue pipes. Check the product labels.

Figure 4-4 How to lay a bead of caulking
Text version
Illustration of a tube of caulking, with caulking being applied to a small gap where a vertical and a horizontal surface meet. An arrow indicates the direction of application. Hold the caulking gun approximately perpendicular to the line of travel. Cut the nozzle squarely. Force the caulk into the crack.
4.2.2 Other sealing materials and applications
Other materials are used to provide an air barrier at different locations in the house, including specialty gaskets and tapes, as well as sheet materials such as polyethylene, spun-bonded olefin, rigid insulation, drywall, plywood, Oriented Strand Board (OSB) and sheet metal. Installation techniques are critical when using sheet materials as an air barrier. Seal all edges, seams and penetrations in the sheets.
4.2.3 Air and vapour barriers
It is often possible to install a new air and vapour barrier by using sealed drywall as the air barrier and layers of paint or sheet polyethylene as the vapour barrier. Alternatively, sealed sheet polyethylene installed on the warm side of the insulation can provide both an air barrier and a vapour barrier. Proper installation is critical (see Figure 4-3).
4.2.4 Refinishing the interior
If an attic retrofit is part of interior renovations, consider removing the ceiling and installing a new sheet-polyethylene or sealed drywall air barrier on the underside of the ceiling joists. Although sealing the air barrier on the ceiling to the one on the wall should pose no difficulties, maintaining continuity at interior partitions will require some ingenuity and detailed work.
Where partition walls run perpendicular to the ceiling joists, maintain continuity by working from above, using connecting strips of polyethylene or extruded polystyrene.
Where partition walls run parallel to the ceiling joists, install blocking and nailing strips to provide support for the new ceiling materials.
4.2.5 Tips on sealing some of the leakiest areas
Electrical outlets
If you notice a draft through any wall electrical outlet, seal it. Inside wall outlets can also be leaky and need to be sealed. Turn off the power to the outlet by turning off the circuit breaker or removing the fuse. Check to make sure the power is disconnected by turning on a lamp.
You will obtain a better seal if you caulk the gasket before installation. Additionally, there are special approved foam pads that fit between the cover plate and receptacles. As well, you can place child safety plugs in seldom-used outlets. Look for the foam pads that come with a gasket that fits on the safety plug (see Figure 3-3 in Section 3).
If you are installing an electrical outlet during a renovation, place it in a special plastic box available from building supply stores, for an optimal seal. Caulk the penetration for the wire, and seal the new air and vapour barrier to the edge of the box.
Trim areas
Seal areas of air leakage around all baseboards, mouldings and window and door casings. In some cases, this can be done easily by sealing all the joints with a flexible caulk that is clear, paintable or of a matching colour. A more effective solution is to carefully remove the trim and seal behind it. Insulate wide cracks with a foam backer rod and seal them with caulking, the appropriate type of polyurethane foam or other suitable material (see Figure 4-5). If you remove baseboards, you might also be able to caulk between the wall finish and the bottom wall plates, and between the plates and the floor.
Glass panes (glazings)
The seal between glass and its wood frame should be tight. Check the glazing carefully and be certain that all the seals are intact, with no cracks or missing sections. If not, repair them with glazing compound that lasts longer and stays semi-soft and usable longer than putty. Remove the old putty and apply the new materials with a putty knife. Press it firmly into the space for a good seal and then paint, allowing the paint to just touch the glass.
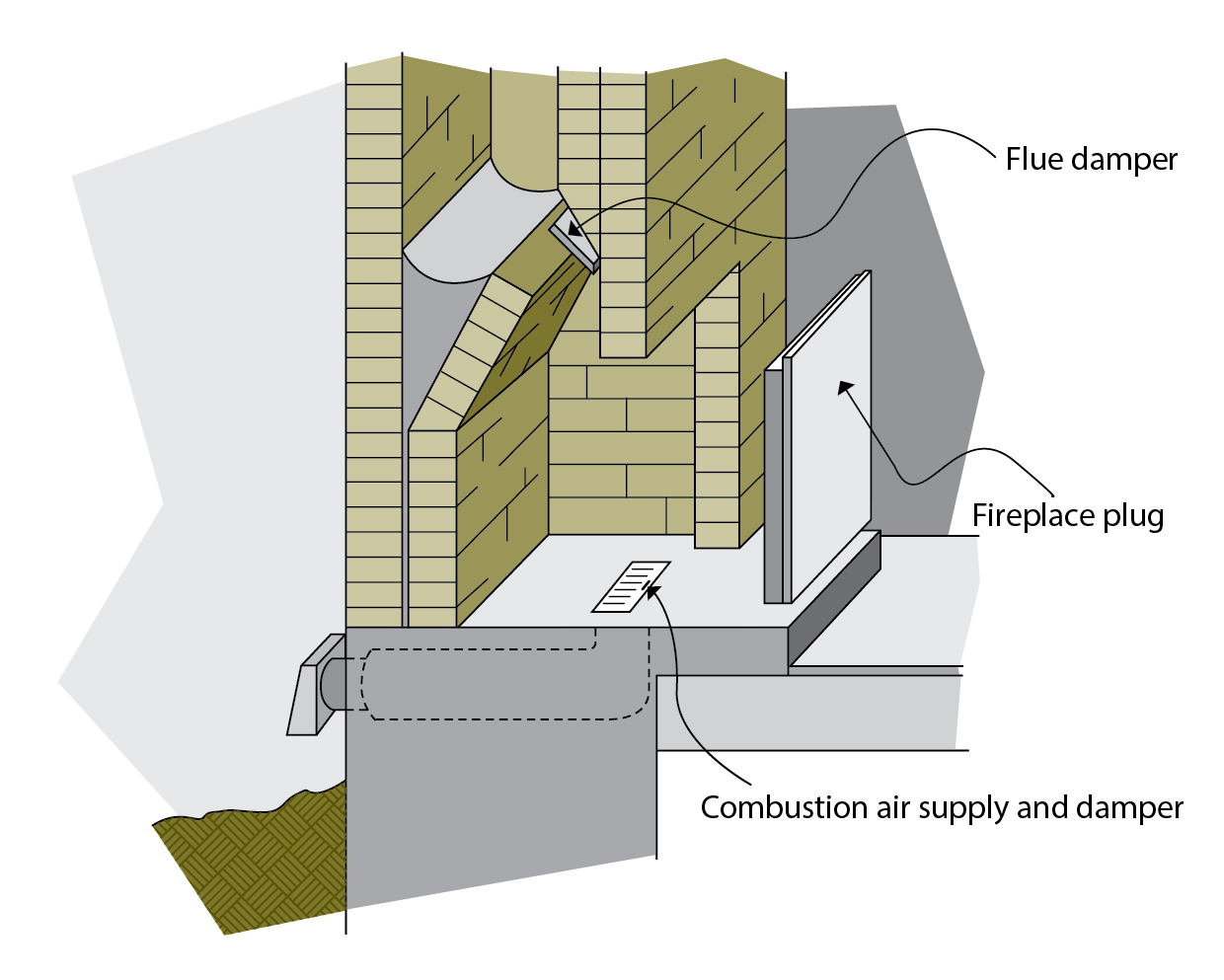
Figure 4-6 Sealing an unused open fire place
Text version
Cutaway of a fireplace indicating the damper at the base of the chimney, the combustion air supply and damper connected by a vent in the floor of the fireplace to the exterior, and an insulated board in front of the fireplace opening that can serve as a plug.
Fireplaces
Close the chimney damper when a fireplace is not in use. Take a flashlight and make sure the damper fully closes. If it does not, have it repaired by a certified chimney specialist. However, even with the damper closed, a great deal of heat may still escape up the chimney. You can install tight fitting glass doors but be aware that most are not very tight or effective. The door frame should be tightly sealed to the fireplace with non-combustible caulk, and the frame should include a combustion air gate or damper. The air gate permits entry of combustion air from the outside to supply the fire, but when not being used, the air gate should be closed. Ask for door kits at your wood-burning appliance dealer or local building-supply outlet.
Seal an unused or seasonally used fireplace by putting an airtight plug of some sort in the chimney or across the fireplace opening. This can be made from board material that is cloth-covered and provides a good seal at the edges (see Figure 4-6).
Check for air leaks where the chimney meets the wall (remove the trim if necessary). Caulk this joint with a high-temperature caulking.
Chimney
Chimneys pose particular challenges for air-sealing and insulating.
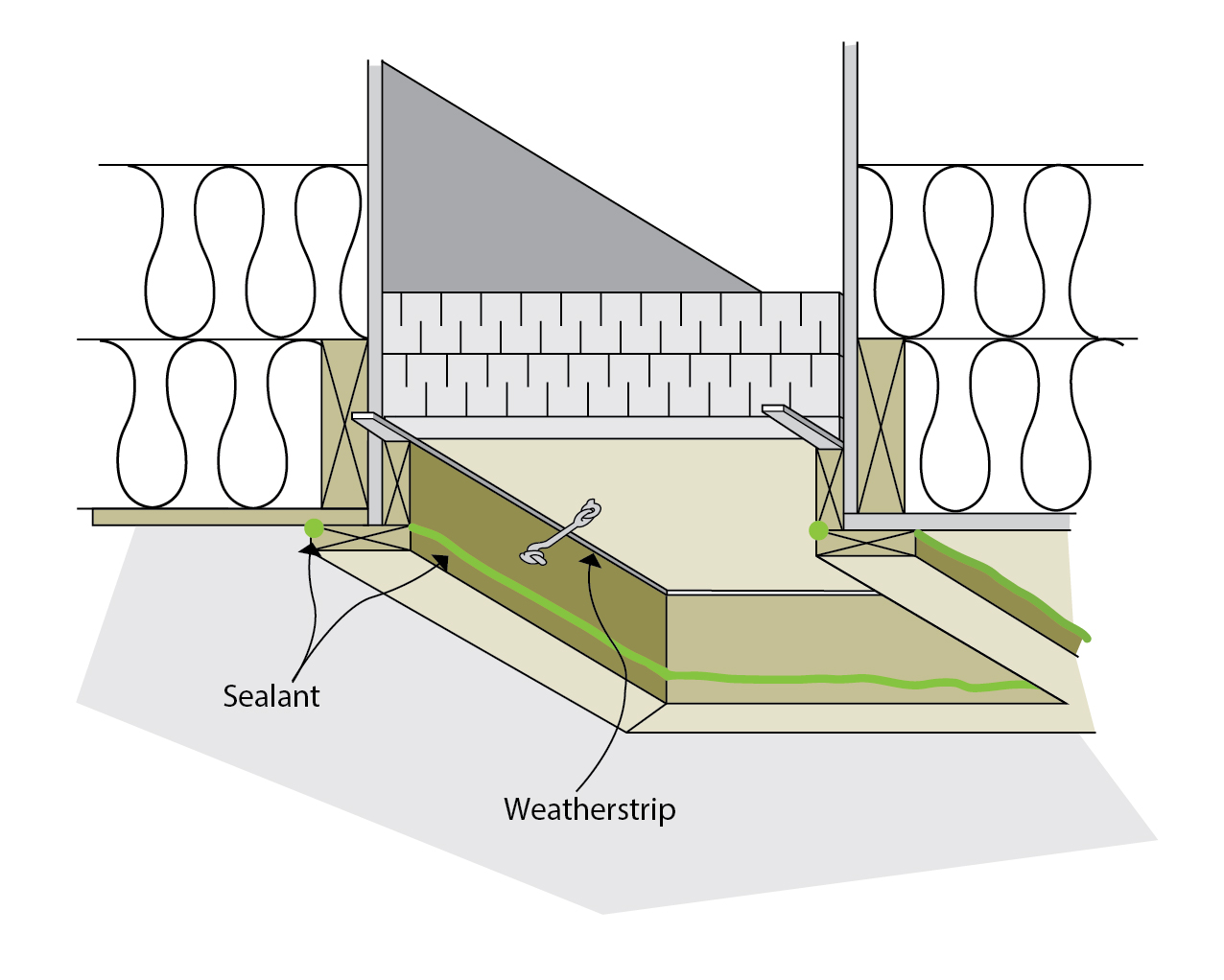
Figure 4-7 Cutaway view of a well-sealed attic hatch
Text version
There is sealant between the casing and the ceiling drywall. A hook with an eyebolt ensures that the hatch is held firmly against the weatherstripping.
Attic hatch
Seal the attic hatch exactly as you would seal an exterior door. Caulk around the frame and between the casing and the ceiling drywall. Weatherstrip along the edges of the casing or the access panel itself. Finally, install hooks with eyebolts or some sort of latch mechanism to hold the hatch firmly against the weatherstripping (see Figure 4-7). The hatch itself should be insulated.
Safety warning:
Fire safety is a real concern when air-sealing and insulating. Refer to Part 5.1.2, Fire and other hazards in attics, for methods of dealing with this area.
Windows that are never opened
Seal windows that are not needed for ventilation or as a possible emergency escape route with caulking rather than weatherstripping. Use special strippable caulk that can be removed when you want to operate the window again.
Relevant topics: Section 8 : Upgrading windows and exterior doors