January 24, 2019
In a modest laboratory tucked away in Ottawa’s forested suburbs, a team of researchers from Natural Resources Canada (NRCan) is testing new technology that could have a big environmental impact more than 3,000 kilometres away in the Alberta oil sands — direct contact steam generation.
“Canada has the third-largest reserves of crude oil in the world, consisting mostly of heavy crude called bitumen, glued up inside the oil sands,” says research scientist Bruce Clements. “What we’re trying to do is improve the extraction methods and maximize the cleanliness of resource extraction in an economical fashion.”
Transcript
Extraction of heavy oil called bitumen is an important component of Canada’s economy. Alberta provides over 15 percent of Canada’s gross domestic product and almost a third of that is from resource extraction. Unfortunately, Canadian oil resources are more difficult and expensive to extract with higher environmental consequences than many other crude oil resources making it les desirable to world markets.
What is there was a method of extracting bitumen that could be economical and have very little environmental impact including using minimal freshwater and producing almost no emissions. Working with industry Natural Resources Canada through its CanmetENERGY has developed methods that create far less negative environmental impact and lower greenhouse gas emissions while also being cost competitive. CanmetENERGY’s technology builds upon one of the most advanced of these techniques: steam assisted gravity drainage (SAGD). SAGD uses paired horizontally drilled wells that extend through the bitumen deposit buried underground. This process requires some freshwater makeup and the production of this steam results in making this process energy intensive and increases its negative environmental impact.
CanmetENERGY has developed steam generation technology that is far less energy intensive and has much less environmental impact. It’s called direct contact steam generation or DCSG, where the SAGD process requires expensive treatment of recycled water and normally has no GHG control. DCSG produces steam by putting recycled water from bitumen extraction directly through an oxygen flame with no need for treatment. This creates mostly steam mixed with produced carbon dioxide and residues, all going back to the underground injection well. In fact, the system is virtually a closed loop; here’s how it works:
We burn natural gas with oxygen at high pressure and inject recycled water from bitumen extraction through the flame to produce steam mixed with CO2. The pressurized steam product flows into the steam injection well, the upper of the paired horizontal wells dug underground at a depth of approximately 4 to 6 meters apart. This warms the bitumen in the reservoir, causing the bitumen to soften and eventually flow by gravity down to the lower well called the production well. The liquid in the lower well is then pumped back up to the surface where the bitumen is separated; the recycled water that is left over without treatment is then used within the DCSG to make steam again. A significant amount of the carbon dioxide produced in the process of heating the water stays underground and that helps to reduce greenhouse gases.
CanmetENERGY has developed the DCSG over the past 10 years as part of our R&D activities. We have built a pilot scale facility at our Ottawa labs that allows us to test every facet of the DCSG process with great care. In parallel with the DCSG pilot plant in Ottawa, a larger demonstration unit is being considered by Sun Corps for use in northern Alberta.
Here are the advantages of direct contact steam generation: it provides greater control of GHG emissions, it minimizes fresh water use by consuming recycled water, produced water and tailings water without treatment. DCSG produces a dry solid waste product, it can utilize waste fuels such as petroleum coke, costs are competitive with existing technology and it allows Canada to produce petroleum product with an environmental impact that is on par with the lowest in the world, making our oil much more attractive on the global market. For more information about direct contact steam generation and CanmetENERGY, please visit this site.
A unique pilot plant project
The NRCan direct contact steam generation (DCSG) team is part of a broad group of experts from the private and public sectors on an urgent quest: to find cleaner, more efficient ways to extract oil and gas products from the oil sands. In Ottawa, the team runs tests using the only pilot plant of its kind in the world, one that uses contaminated water from Alberta to mimic the processes used in the oil sands there.
While the oil in oil sand is bitumen — a viscous substance with a consistency similar to gritty dirt — the sand component consists of various deposits: sand, clay, sandstone and other sedimentary rocks. Before bitumen can be transported to global markets, it must first be isolated from these other deposits and then liquefied. Typically, producers extract bitumen using one of two methods: an in-situ process known as steam-assisted gravity drainage (SAGD) and an above-ground mining process.
Typical oil sand production can be energy-intensive
In the in-situ process, producers drill a well and inject steam into the ground to heat the bitumen until it becomes warm enough to flow. The mining process also uses steam but extracts the bitumen above ground, producing dirty waste water in the form of pools of wet tailings.
Both approaches have two fundamental problems. First, they rely upon steam that is produced by commercial boilers burning fuel, which creates greenhouse gas emissions. Secondly, the steam production requires large supplies of clean water, most of which can be recycled requiring intensive treatment systems, particularly for the in-situ process.
Shortcutting the process to reduce greenhouse gases
The solution? “We want to contract all those water treatment steps and shortcut the water treatment system,” says Lijun Wu, NRCan research scientist.
The NRCan team does this through DCSG, which produces steam by injecting dirty water directly into a 1300°C flame in a combustion chamber. This produces a high-pressure steam and CO2-rich flue gas mixture that can be injected into production wells using the in-situ process without requiring the energy-intensive use of commercial boilers and water treatment systems.
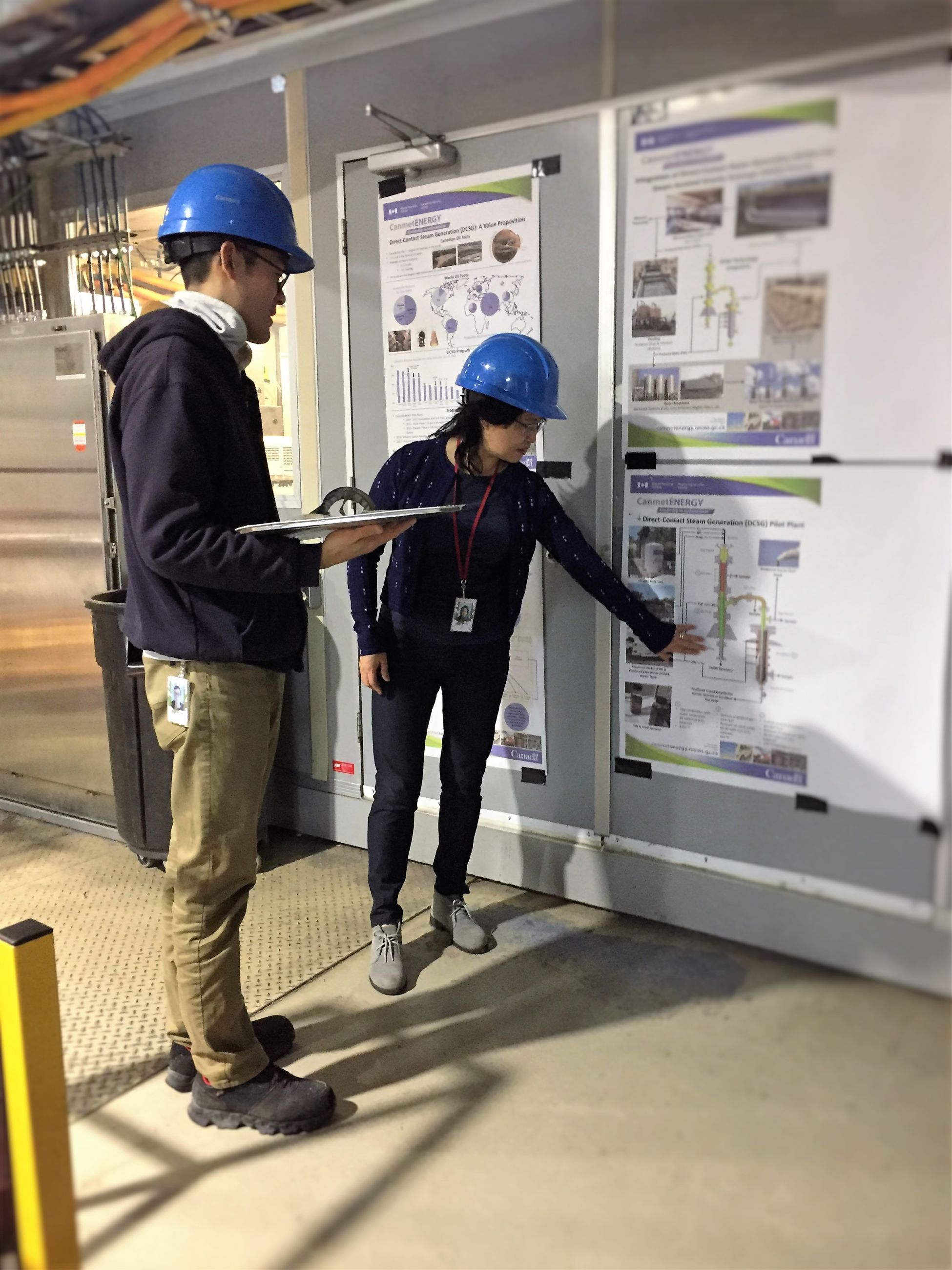
Larger image
Researchers at CanmetENERGY
DCSG has many potential environmental advantages:
- It uses far less clean water because boiler tubes are no longer needed
- It reduces the environmental footprint, since nearly all greenhouse gas emissions can be sequestered underground
- Instead of wet waste water tailings it produces dry tailings, which are easier to manage and dispose of.
Experiments and test phases are underway
Since July 2017, the NRCan team has completed eight successful tests at different levels of pressurization for the steam, starting from 80 bar down to 30 bar, depending upon the well requirements.
“At the beginning we asked ourselves if it was even possible to fire natural gas using high pressure and keep the flame stable with water injection,” says Lijun. The first test was a proof of concept, giving the team confidence to move forward.
After this round of testing, they will experiment with using different contaminated water sources to see what effects, if any, these might have. Eventually, they will test this technology under real commercial-scale oil sand extraction conditions.
While direct contact steam generation is still a few years away from full commercial use, the team is focusing on one experiment at a time to advance the commercialization of this technology.