Industrial Energy Systems
Improving the efficiency and performance of industrial systems can yield large energy and cost savings, particularly for energy-intensive industries such as iron and steel. This results in significant economic benefits to industry and helps Canada to realize its goals for a sustainable energy future that results in far less impact on our environment.
CanmetENERGY’s Industrial Innovation Group works closely with Canadian industry to identify priority technologies that can reduce and/or recover energy loss in the following areas:
Industrial Energy Systems, including combustion, process heating, combined heat and power, compressed air, motors, pumps and fans, account for approximately 80% of all energy used by industry. On average, 30% to 40% of that energy is lost. We help Canadian companies reduce and recover this lost energy thereby lowering their productions costs as well as their need for fossil fuels. This aids in mitigating the threat of global warming by reducing the GHGs emitted by these industries.
Our experts perform research and development that further lowers the use of carbon-intensive fossil fuels within Canadian industry by reducing the technical barriers to replacement fuels such as renewables/biomass. We also promote the adoption of economically sound industrial technologies and processes that reduce energy use and emissions.
To view some of our success stories with Canadian Industry, visit our partners page.
Metallurgical fuels
Metallurgical fuels have the required physical and chemical characteristics for economic metals production. These fuels include metallurgical or coking coals, metallurgical coke, and fuels for injection to blast furnaces to produce iron for steelmaking. Approximately 70% of the world's steel production (1.34 billion metric tonnes in 2007) is dependent on metallurgical coal.
CanmetENERGY researches ways to increase the efficiency of metallurgical fuels, which are primarily used by iron and steel industries. The research includes increasing the efficiency of the iron and steel making processes and reducing greenhouse gas (GHG) emissions associated with this work. We focus on:
- GHG mitigation
- Biofuels for steelmaking
- Coking and dry quenching processes
- CO2 capture and storage
- Coal and coke standards for Canada
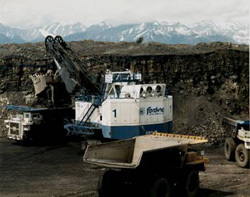
Metallurgical coal mine in Fording
River Mine, British Columbia, Canada
As coke is the most important raw material fed into a blast furnace, we work to improve the behaviour of coals during carbonization in order to provide high quality coke while ensuring efficient industrial operations. Introduction of high quality coke to a blast furnace results in lower coke rates, higher productivity, lower hot metal costs and reduced greenhouse gas emissions. A good quality metallurgical coke is generally made from the carbonization of several good quality coking coals so we also develop methods to enhance coal blend properties for carbonization.
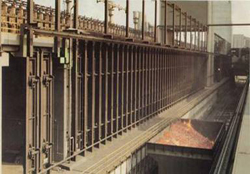
Metallurgical Fuels:
By-product coke oven battery
We also focus on the development of technologies to use coke and alternative fuels in blast furnaces and other metallurgical processes, and to demonstrate the advantages of Canadian coals to world markets.
Find out more:
Coal and coke technologies
Current research on coal and coke technologies focuses on improving the energy efficiency of Canada’s metallurgical industries, including cokemaking, ironmaking, and steelmaking. The goal of this research is to reduce the sector’s carbon footprint, while at the same time enhancing its sustainability.
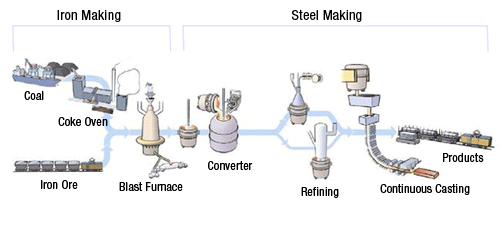
Long description
This diagram illustrates the process of iron making and steel making.
Iron making:
- coal and iron ore extraction
- coal to oven
- blast furnace
Steel making:
- converter
- refining
- continuous casting
- products
On behalf of Canadian coal, steel, and metal producers, CanmetENERGY conducts research and development on metallurgical coal and coke technologies including energy recovery from coke production, metallurgical coke, bio-coke, and research into Canadian coal. As a partner with the Canadian Carbonization Research Association, our scientists perform cost-shared metallurgical fuels research that enhances fuel utilization efficiency, productivity, and the economic viability of these industries, while also protecting our environment.
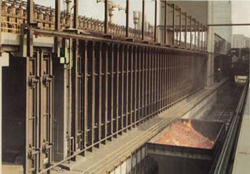
18-in (460 mm) wide Research Movable Wall Coke Oven
Our coal evaluation, preparation, agglomeration and carbonization facilities are unique in Canada. They are available to industry on a "fee-for-service" basis to assist with mine planning, marketing and economic investigations; ensure safety during coking; and evaluate the quality of coke, carbon, coal and other alternate fuels including biofuels for metallurgical purposes.
As part of our search for green energy solutions for iron and steelmaking, we are working on a bio-steel breakthrough project to evaluate renewable energy sources (biofuels). This project examines fuel injection and coke manufacturing and the technical and economical feasibility of substituting fossil carbon with bio carbon for these technologies.
We are also strengthening our ties to international research organizations to perform co-operative research projects in the fields of metallurgical coal/coke science, biofuels for steelmaking and applications.
By engaging with our partners in these and other innovative research projects, we aim to increase the market penetration of Canadian coal with superior quality and better energy characteristics, and to develop standards for enhancing the knowledge and utilization of Canadian coal and coke, according to ISO/TC 27.
Find out more:
- Blast furnace optimization
- Research publications on innovation in the commercial and industrial sectors
Licensed technologies
CanmetENERGY offers Canadian and international companies and organizations opportunities to invest in the development and deployment of clean energy technologies.
Below you will find a list of opportunities to license our technologies and to join other private sector companies in consortia research.
When used oils such as motor oil and lubricants are thermally cracked for reprocessing they produce unstable, foul-smelling gas oil with limited potential for further use. The ROBYSTM process purifies and stabilizes reprocessed used oils that would otherwise go to waste, producing gas oil that:
- meets regulatory and consumer colour criteria
- is not odorous
- minimizes the formation of gums and tars during storage, and
- has reduced sulphur, nitrogen, and chlorine contents.
The ROBYSTM process
The ROBYSTM process was developed in collaboration with Aldwich Canada and the first commercial ROBYSTM plant was successfully installed in Malaysia in 2005. For a fee, we will test used oils submitted by clients for their suitability for the ROBYSTM process.
CanmetENERGY SUPERCETANETM
CanmetENERGY SUPERCETANETM technology converts a wide variety of triglyceride-containing feedstocks including vegetable oils, yellow greases, animal fats, and tall oil, into a stable, high-cetane (~100) diesel fuel blending stock with low sulphur content (less than 10 ppm). High free fatty acid feedstocks are easily processed with the SUPERCETANETM Technology. The hydrotreating process generates water, burner gas, and a hydrocarbon liquid that is further distilled into naphtha, waxy residues, and a middle distillate (SUPERCETANETM). Yields of SUPERCETANETM from this efficient process are 70–80% by weight and 85–93% by volume.
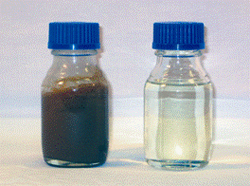
Feed grease (left) is converted into clean,
high-quality SUPERCETANETM (right).
SUPERCETANETM has multiple environmental advantages: lower diesel exhaust emissions of hydrocarbons, NOX, particulates, and carbon monoxide; reduced greenhouse gas emissions over its complete life cycle; and improvement in fuel economy by up to 8%. SUPERCETANETM is very stable, fully compatible with petroleum-derived diesel fuels at all concentrations, and has a better ignition quality (higher cetane number) than transesterification products (biodiesel).
Potential commercial applications of SUPERCETANETM centre on its ability to increase the ignition quality of low-cetane middle distillates, to reduce the NOX emissions of biodiesel blends, to increase the responsiveness of diesel fuels, and to produce renewable normal paraffins for petrochemical applications. CanmetENERGY has available a 0.2 barrel/day process development unit for process optimization and further research.
The AVRO DieselTM process
The AVRO DieselTM process converts recovered cooking greases, animal fats, cooking oils, and restaurant residues into a clean, high-cetane diesel fuel. In North America, these wastes amount to 6 – 8 kg/person/year and are currently sent to landfills at a cost of $30–$60/tonne. Recovery of these wastes in Canada alone could produce 200 million L/year of clean diesel fuel worth an estimated $150 million Canadian.
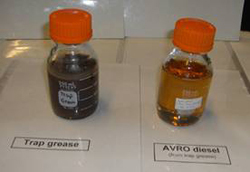
Soap, bacteria and cooking fat (left)
collected from commercial kitchens can
converted into AVRO DieselTM (right)
Existing conventional bio-diesel processes require clean and often expensive ($650–$800/tonne) feedstocks and have poor cold flow properties. The AVRO DieselTM process combines mild thermal cracking with esterification to yield a 50%-50% mixture of hydrocarbons and methyl-esters suitable for diesel-fuel blending and with improved cold flow properties.
CanmetENERGY is continuously developing new clean energy technologies, many of which are available for licensing and commercialization.
Page details
- Date modified: