Keeping The Heat In - Section 3: Materials: insulation, house wrap barriers and weatherstripping
Whether for your attic or your basement, choosing the right materials and installing them properly ensures the finished job lives up to your expectations. This section describes the types of insulations, house wrap materials (air barriers and vapour barriers) as well as details about weatherstripping windows and doors.
Embodied carbon
Embodied carbon, sometimes referred to as embodied energy, are the green house gas (GHG) emissions associated with building materials during their entire life cycle. This life cycle includes resource extraction, manufacturing, transportation, installation and construction process, maintenance, and eventual demolition and end of life recycling or disposal of the material. Just as improving the energy performance and efficiency of a home can reduce emissions from heating, cooling and ventilation systems, selecting materials with low embodied carbon emission factors is an important step in reducing the overall carbon footprint of a home. You can consider embodied carbon when selecting building materials and practices in planning energy efficient retrofits. For example, plant based materials (e.g. wood, straw, hemp, cellulose) typically have lower embodied carbon factors than synthetic and mineral-based products, which may require considerable energy to manufacture. You can ask your contractor, an energy advisor or check the web about embodied carbon when planning a renovation.
3.1 Insulation
To be effective, insulation must resist heat flow, fill the space completely and evenly, be durable, and for some locations, withstand exposure to heat or moisture. Different materials may be used at different locations in the house envelope depending on the space available, ease of access and other installation requirements.
In addition, consider the following:
- Is the material available locally?
- Is it relatively easy to install, especially for do-it-yourselfers?
- Is it the best buy for the space available (either high insulating value per dollar if you have a lot of open space, or high insulating value per thickness if space is restricted)?
- Can it conform to surface irregularities?
- Is it rigid enough to provide support for finished materials or resist pressures against its surfaces?
- Does any single type of insulation require more accessory products than another (e.g. fire protection, air and vapour barrier or framing)?
For proper application, material handling, safety equipment and protective clothing requirements, follow the manufacturer’s instructions (see Part 1.4, Health and safety considerations). Figure 3-1 shows various Insulating materials and safety equipment.
3.1.1 Do your research
Once you have selected a product, get the facts about it and find out about proper installation techniques. Compare the advantages, limitations and intended use of different products.
Materials (or their packaging) may be marked indicating that they comply with Canadian product standards. If they do not, they may have an evaluation number issued by the Canadian Construction Materials Centre. Your local municipal office can tell you if certain products are acceptable for use in your municipality.
Manufacturers and suppliers are responsible for making sure that the products they sell comply with Canadian legislation. If you are concerned about the safety of a particular product, find out if it is prohibited or regulated under the Canada Consumer Product Safety Act and Canadian Environmental Protection Act (the Acts), and other relevant federal, provincial or territorial legislation, or municipal bylaws.
Ask for a Safety Data Sheet (SDS) that lists the hazardous ingredients, safety information and emergency measures related to specific products (SDS replaces the previous Material Safety Data Sheet [MSDS]). An SDS is required for certain industrial and chemical products used in the workplace like paint, caulking, spray foam insulation and cleaners. An SDS is not required for manufactured items (e.g. insulation) or consumer products, but it may be available from the manufacturer or supplier.
For example, as of the date of publication, two types of insulation products are prohibited and one other is regulated under the Acts as follows:
Prohibited
- Urea formaldehyde-based foam insulation (UFFI) foamed in place (prohibited in Canada in 1980): This includes insulation products that are available in the United States that are urea-formaldehyde based and are installed via a foaming process.
- Asbestos: A product containing or composed entirely of asbestos cannot be sold as a consumer product (prohibited in Canada as of 2018).
Regulated
- Cellulose fibre insulation (first regulated in Canada in 1979): This commonly used and effective insulation material must meet certain performance standards with respect to flammability, among other things.
For more information about the Acts and for clarification on these requirements, visit Meeting Canada Consumer Product Safety Act requirements and Understanding the Canadian Environmental Protection Act. Visit Renovating for energy efficiency for information on Health and safety considerations for energy-efficient renovations.
3.1.2 Cost of materials
Generally, the cost per RSI value is lower for loose fill or batt type materials than for rigid board or foam type insulations. However, the price of the basic material is just one aspect. High material costs may be offset by lower installation costs or the installer’s preference for a particular insulation technique.
3.1.3 Thermal performance: How effective is that material?
Thermal resistance values (RSI and R) are listed in Table 3-1. This table also provides average design specifications because values for different manufacturer’s products of the same class may vary.
3.1.4 If it sounds too good to be true . . .
Some manufacturers may claim that an insulation product offers remarkable insulating value. Any product that is promoted as offering a long-term thermal resistance exceeding RSI 1.14/25 mm (R-6.5/in.) may be making a claim that is not substantiated by industry-recognized tests to specific accepted standards. Also, be alert to any manufacturer’s thermal performance claims that are based on building envelope systems (e.g. whole wall or ceiling configurations) that are not identical to those configurations or conditions in which the product is being considered for use.
3.1.5 Summary of insulation types
This section explains the following insulation types:
- batt or blanket
- loose fill
- cellulose fibre
- glass fibre
- mineral fibre (mineral wool or rock wool)
- rigid board
- expanded polystyrene
- extruded polystyrene
- mineral fibre rigid board
- polyurethane and polyisocyanurate boards
- spray foam
- closed-cell polyurethane foam
- open-cell polyurethane foam
- cementitious foam
- reflective bubble foil insulations and radiant barriers
Batt or blanket insulation
Glass fibre and mineral fibre (slag or rock wool) batt or blanket insulation is relatively easy to install in accessible spaces such as exposed wall cavities and some attics. This type of insulation does not settle, it conforms to slight surface irregularities, and it can be cut to fit. To gain the maximum insulating benefit, batts and blankets should completely fill the space they are fitted into and neither be compressed nor have gaps (especially avoid compressing the edges).
Some products are available in non-combustible form. Check with the manufacturer to verify that the products are non-combustible. Safety equipment and protective clothing are required during installation.
Technical note:
Glass and mineral fibre insulations are typically poor air sealing products. Sometimes these products are stuffed into cracks and gaps (at the header in the basement or around a window) in an attempt to block air leakage. This practice is not effective. Always air seal by using appropriate materials and techniques.
Loose-fill insulation
Loose-fill insulation is suitable for walls and floors and excellent in attics and enclosed spaces, such as roofs, where the space between the joists may be irregular or cluttered with obstacles. You can use it to top up existing insulation in attics and accessible enclosed wall cavities and to fill in cracks and small or uneven spaces. It is not appropriate for below-grade application. Use safety equipment and wear protective clothing during installation. Consider hiring a trained and manufacturer-licensed technician to perform the installation.
Safety warning:
Never allow insulation materials to come into contact with a chimney or a combustion vent, an exposed recessed lighting fixture or an old knob and tube wiring because these can pose a fire hazard. See Part 1.4, Health and safety considerations.
Loose-fill insulation may be poured or blown into cavities. Pouring will generally require more material than blowing to achieve a specified RSI value. Check the manufacturer’s information on the quantity of material required to provide a specified RSI value.
Most loose-fill materials installed in walls will settle after installation, creating gaps at the top of the cavities. There are different installation approaches for each type of material to lessen this effect.
Loose-fill insulation options include cellulose fibre, glass fibre and mineral fibre described as follows.
i) Cellulose fibre
Cellulose fibre is made from shredded newsprint treated with chemicals that resist fire and fungal growth and inhibit corrosion. Because of its small particle size, it can fill any gaps around obstructions such as nails or electrical wires that are within cavities. However, blowing cellulose fibre can create a lot of dust. Be sure to make allowance for settling.
Cellulose fibre offers limited additional air sealing when blown into cavities that already have insulation. However, it will provide increased air sealing when blown into empty and restricted cavities at dense-pack levels, typically around 56 kilograms per cubic metre (kg/m³) (3.5 pounds per cubic foot [lb./cu. ft.]).
To reduce settling, some companies offer a wet-spray installation technique for their products for open wall cavities that may require a fabric net. Drying time varies for the different types and brands of product.
ii) Glass fibre
Loose-fill glass fibre is a similar material to glass fibre batts, but chopped up for blowing or pouring applications. Hand-poured glass fibre works best in open horizontal surfaces such as attics. Blown glass fibre can be used in both horizontal and vertical applications.
At conventional application pressure, it may be difficult to install in cavities that are partially blocked by nails, framing, electrical wiring, etc. At dense-pack levels (i.e. around 40 kg/m3 [2.5 lb./cu. ft.]), higher RSI (R) values are achieved and can better fill cavities that have restrictions. For walls, application density is usually two to two-and-a-half times the manufacturer’s recommended rate of application for horizontal surfaces. This higher density ensures better overall application and performance.
Some products are classified as non-combustible. Check the manufacturer’s specifications for verification.
iii) Mineral fibre (mineral wool or rock wool)
Loose-fill mineral fibre is treated with oil and binders to suppress dust, maintain shape and ease the blowing process. It is similar to glass fibre in appearance and texture. Mineral fibre is suitable for accessible attics and inaccessible areas such as wood-frame walls, roofs or floors. For walls, the density of application is usually two to two-and-a-half times the manufacturer’s recommended rate of application for horizontal surfaces.
Mineral fibre may be acceptable for insulating around masonry chimneys as it will not support combustion. However, check with your local building inspector to learn what is accepted.
Rigid board insulation
Rigid board insulation (insulating boards) is currently manufactured from mineral fibre or foam plastic materials. These materials have a high insulating value per unit thickness although the cost per RSI value is greater than that for loose-fill or batt or blanket insulations.
Insulating boards are lightweight and easy to cut and handle. Fitting them into irregular spaces, however, can be a tedious process. Some boards are available with special coverings (e.g. a fire-resistant material) and their own system of attachment. Some board materials can be ordered pre-cut to specific sizes for an additional cost.
When installed on interior surfaces, all plastic-based rigid board insulation must be covered with a fire-resistant material – typically 13 mm (1/2 in.) drywall – that is mechanically fastened to the building structure. Plastic boards must be protected from prolonged exposure to sunlight, solvents and some sealants. Be sure to ask your supplier for a compatible sealant.
Rigid board insulation options include expanded polystyrene, extruded polystyrene, mineral fibre rigid board and polyurethane and polyisocyanurate plastic boards described as follows.
i) Expanded polystyrene
Expanded polystyrene (EPS), often called bead board, is made by using pressurized steam to expand and form polystyrene beads into rigid foam plastic boards. High and low-density products are manufactured using steam as the blowing agent. High-density board is more moisture resistant and can be used on the exterior of foundation walls in dry, sandy soils.
ii) Extruded polystyrene
Extruded polystyrene (XPS) is a foam plastic board with fine, closed cells containing a mixture of air and non-ozone depleting refrigerant gases. If joints are sealed properly, it can perform as an air barrier and, at certain thicknesses, may perform as a vapour barrier. Low permeability means that it does not absorb or pass on moisture, making it suitable for below-grade applications.
iii) Mineral fibre rigid board
Mineral fibre insulation, when compressed and held together with a combustible binder, forms semi-rigid board stock. The fibres are aligned vertically so that any water that penetrates the surface will run down, making it suitable as a drainage layer. High-density, semi-rigid mineral fibre board for residential use is designed for below-grade exterior applications.
iv) Polyurethane and polyisocyanurate boards
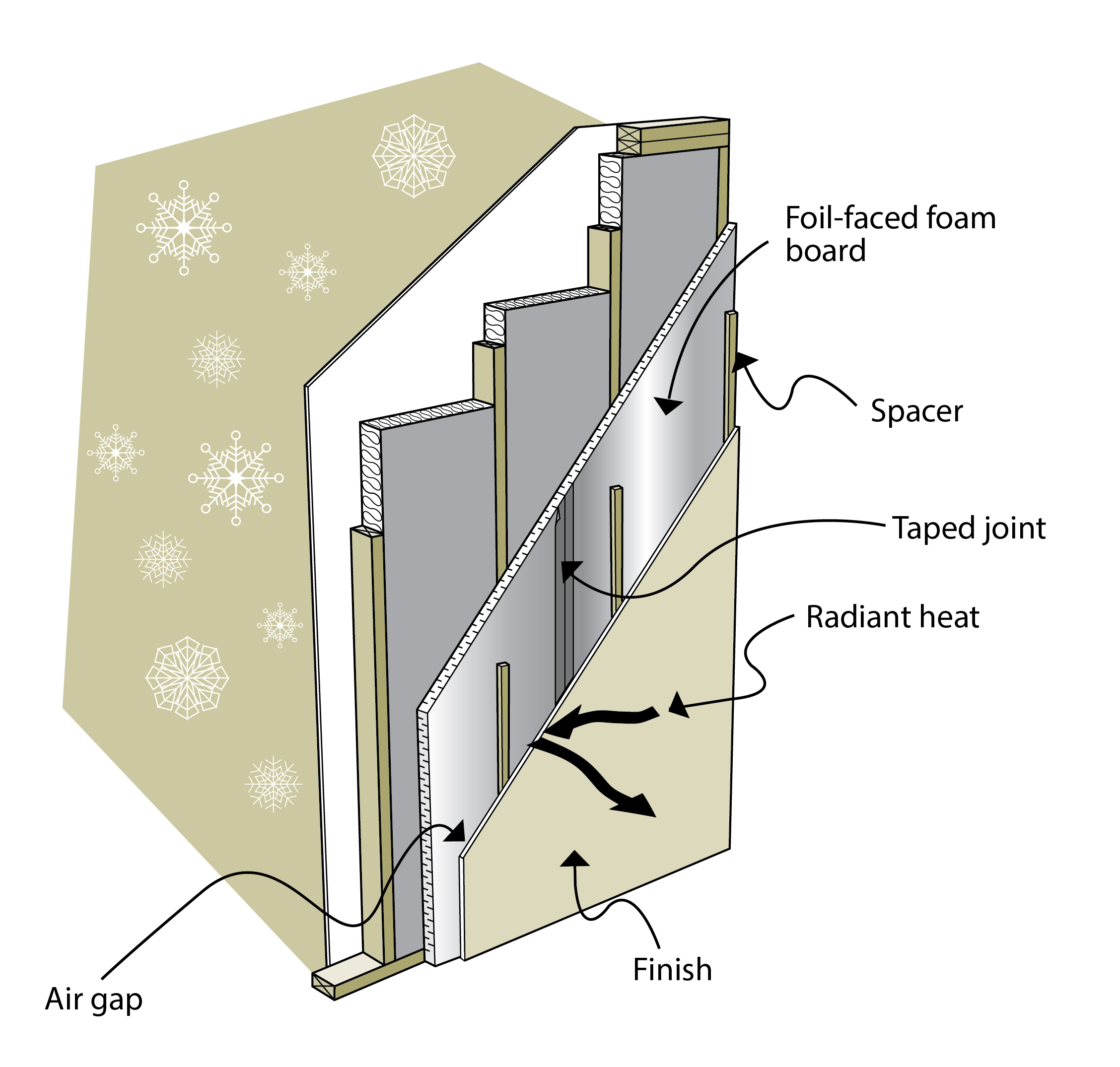
Figure 3-2 Foil-faced foam board acts as an air vapour barrier
Text version
Cutaway of a wall showing the multiple layers of an exterior-facing wall with snowflakes indicating the outdoors. The cutaway section has four wall studs with batts of insulation filling the three cavities. The batts form the layer closest to the exterior. The next layer is a foil-faced foam board, foil facing the interior, and with spacers creating an air gap between it and the interior wall finish.
Polyurethane and polyisocyanurate plastic boards are made of closed cells containing non-ozone depleting refrigerant gases instead of air. They usually come double-faced with foil (as shown in Figure 3-2) or are sometimes bonded with an interior or exterior finishing material. These products must be protected from prolonged exposure to sunlight and water. If the seams are well sealed, they can act as an air and vapour barrier. Use is generally limited to areas where a high RSI is desired and space is limited. The RSI value of some polyisocyanurate products tends to drop in cold temperatures so it should be used as an interior insulation layer unless a cold temperature rating is given.
Spray-foam insulation
Spray-foam insulation is a mixture of plastic resin (e.g. soy-based resins or resins made from recycled plastic) and a catalyst, that are prepared and applied on the job site. Spray kits for this type of insulation are available to the consumer, but employing a certified installer who is trained in the application of the specific product will ensure the best results. The liquid foam is sprayed directly onto the building surface or poured into enclosed cavities with a pump-driven applicator. The foam expands in place and sets in seconds.
There are two types of foam: low density and high density. When installed on interior surfaces, all plastic-based foam insulation must be covered with a fire-resistant material – typically 13 mm (1/2 in.) drywall – that is mechanically fastened to the building. All foam plastics must be protected from prolonged exposure to sunlight.
Options for spray-foam insulation include closed-cell polyurethane foam and open-cell polyurethane foam described as follows.
i) Closed-cell polyurethane foam
Closed-cell polyurethane foam (also called high-density or two-pound foam) is sprayed onto surfaces in layers not more than 50 mm (2 in.) thick at each pass (if greater thicknesses are desired), where it hardens in seconds. A 24 hour curing and off-gassing period is required before occupancy can resume. The foam can expand 28 to 35 times its initial volume and should not be used in enclosed cavities.
This product can be used as an air barrier. When applied to a thickness of 50 mm (2 in.), it can sometimes act as a vapour barrier. It can be used below grade and it bonds well to clean cement and masonry where it also makes a good moisture barrier. Though high-density foam is a premium, hard textured, multi-task product, it is not generally used to completely fill cavities due to its high cost.
Technical note:
Freshly applied closed-cell spray polyurethane foam can have an RSI value as high as 2.0. However, due to the loss of the foam’s blowing gases over the immediate and long term, its RSI value should be limited to only 0.90 as shown in Table 3-1. This is because the design RSI value is based on a long-term thermal resistance (LTTR) test that accounts for the deterioration of the insulation over time. The LTTR value is determined by measuring the thermal resistance of a closed-cell foam insulation over 5 years under laboratory conditions. It is best practice to use the LTTR as the design value when calculating the amount of insulation required.
ii) Open-cell polyurethane foam
Open-cell polyurethane foam (also known as low-density or half-pound foam) is made from a combination of isocyanurate resins and catalysts, resulting in an open-celled, spongy semiflexible material. With a very high expansion rate – up to 100 times its initial volume – and its lower comparative cost, this product is more effective than closed-cell foam for filling larger cavities. It can be used as an air barrier but not a vapour barrier.
Cementitious foam insulation
Recently introduced into Canada, cementitious foam insulation is a non-plastic based non-combustible material with a soft chalky texture. When poured or injected into cavities by a trained installer, it has the consistency of shaving cream and may require some drying out time. This insulation can be used as an air barrier but not a vapour barrier.
Reflective bubble foil insulations and radiant barriers
Reflective bubble foil insulation is essentially a plastic bubble wrap sheet with a reflective foil layer and belongs to a class of insulation products known as radiant foils. Reflective bubble foil insulations – and other radiant barrier products like paints and sheeting – are noted for their ability to reflect unwanted solar radiation in hot climates, when applied properly.
However, all of Canada is considered a cold climate, so these products do not perform as promoted. Though they are often marketed as offering very high insulating values, there is no specific standard for radiant insulation products, so be wary of posted testimonials and manufacturers’ thermal performance claims.
Research has shown that the insulation value of reflective bubble foil insulations and radiant barriers can vary from RSI 0 (R-0) to RSI 0.62 (R-3.5) per thickness of material. The effective insulating value depends on the number of adjacent dead air spaces, layers of foil and where they are installed.
If the foil is laminated to rigid foam insulation, the total insulating value is obtained by adding the RSI of the foam insulation to the RSI of the dead air space and the foil. If there is no air space or clear bubble layer, the RSI value of the film is zero.
3.2 Insulation values table
Table 3-1 lists the thermal resistance ranges and the accepted design specification values or averages of insulation materials, including older and less common materials that you may find in a house.
Material | Ranges RSI/25.4 mm (R/in.) | Design spec or average RSI/25.4 mm (R/in.) |
---|---|---|
Polyurethane closed-cell spray foam | 0.92 to 1.14 (R-5.2 to 6.5) | 1.06 (R-6) |
Polyurethane board | 0.97 to 1.2 (R-5.5 to 6.8) | 1.06 (R-6) |
Extruded polystyrene board (XPS) | 0.88 (R-5) | 0.88 (R-5) |
Polyisocyanurate spray foam | 0.85 to 1.46 (R-4.8 to 8.3) | 0.88 (R-5) |
High-density glass fibre board | 0.63 to 0.88 (R-3.6 to 5) | 0.7 (R-4) |
Expanded polystyrene board – Type I (EPS) | 0.67 (R-3.8) | 0.67 (R-3.8) |
Expanded polystyrene board – Type Il (EPS) | 0.7 to 0.77 (R-4 to 4.4) | 0.7 (R-4) |
Glass fibre roof board | 0.67 (R-3.8) | 0.67 (R-3.8) |
Cementitious foam | 0.69 (R-3.9) | 0.69 (R-3.9) |
Cotton fibre batt | 0.67 (R-3.8) | 0.67 (R-3.8) |
Cork | 0.65 to 0.67 (R-3.7 to 3.8) | 0.65 (R-3.7) |
Polyurethane open-cell spray foam | 0.63 to 0.67 (R-3.6 to 3.8) | 0.63 (R-3.6) |
Polyurethane open-cell foam, poured | 0.7 (R-4) | 0.7 (R-4) |
Cellulose fibre, wet sprayed | 0.53 to 0.67 (R-3 to 3.8) | 0.63 (R-3.6) |
Cellulose fibre, blown, settled thickness | 0.53 to 0.67 (R-3 to 3.8) | 0.63 (R-3.6) |
Mineral fibre batt | 0.53 to 0.7 (R-3 to 4) | 0.6 (R-3.4) |
Wood fibre | 0.58 (R-3.3) | 0.58 (R-3.3) |
Mineral fibre, loose fill, poured | 0.44 to 0.65 (R-2.5 to 3.7) | 0.58 (R-3.3) |
Glass fibre batt | 0.55 to 0.76 (R-3.1 to 4.3) | 0.56 (R-3.2) |
Glass fibre, loose fill, poured | 0.39 to 0.65 (R-2.2 to 3.7) | 0.53 (R-3) |
Mineral fibre, loose fill, blown | 0.51 to 0.56 (R-3 to 3.8) | 0.53 (R-3) |
Glass fibre, loose fill, blown | 0.48 to 0.63 (R-2.7 to 3.6) | 0.51 (R-2.9) |
Fibreboard (beaverboard) | 0.41 (R-2.3) | 0.41 (R-2.3) |
Mineral aggregate board (Insulbrick) | 0.41 to 0.7 (R-2.3 to 4) | 0.46 (R-2.6) |
Wood shavings | 0.18 to 0.53 (R-1 to 3) | 0.42 (R-2.4) |
Vermiculite* | 0.37 to 0.41 (R-2.1 to 2.3) | 0.38 (R-2.2) |
Compressed straw board | 0.35 (R-2.0) | 0.35 (R-2.0) |
Eel grass (seaweed) batt | 0.53 (R-3) | 0.53 (R-3) |
Cedar logs | 0.18 (R-1) | 0.18 (R-1) |
Softwood logs (other than cedar) | 0.18 to 0.25 (R-1 to 1.4) | 0.22 (R-1.25) |
Hardwood logs | 0.12 (R-0.7) | 0.22 (R-1.25) |
Straw bale | 0.23 to 0.28 (R-1.3 to 1.6) | 0.26 (R-1.45) |
Radiant foil insulation | See Reflective bubble foil insulations and radiant barriers in Part 3.1 |
* See the vermiculite health and safety warning in Part 1.4, Health and safety considerations.
3.3 Air barrier materials
The main purpose of an air barrier system is to protect the building structure and the insulation from moisture damage. It must resist air movement; be continuous, completely surrounding the envelope of the house; be properly supported by rigid surfaces on both the interior and exterior (to prevent movement in high winds); and be strong and durable. Attention to detail during installation is critical for good performance.
Various materials throughout the envelope act as an air barrier. Large-surface building materials such as drywall, baseboards or structural members and windows and doorframes are incorporated into the air barrier by sealing them to the adjoining materials. Caulking, tapes and gaskets are used for joints between materials that do not move, and weatherstripping, for joints that do move.
3.3.1 Choosing an air barrier material
If the material that you are considering using offers resistance to airflow and is strong and durable, consider the following installation factors:
- Is it easy to install without help?
- If installed in a concealed location, will it last the life of the building or will it be accessible and easily repairable?
- Is it compatible with other materials in the system?
- Can it be successfully sealed to adjacent materials?
- Is the choice of material appropriate for any other work being done?
- Does it serve other functions such as acting as insulation, a vapour barrier or part of a drainage plane?
Sheet materials
i) House wrap (typically made from a spun polyolefin plastic)
- is generally used to wrap the exterior of a house
- acts as a wind barrier when installed on the exterior; prevents wind from reducing the nominal RSI value of insulation
- acts solely as an air barrier does not function as a vapour barrier
- can function as a drainage plane surface when the upper sheet overlaps the lower sheet and the flashings and all edges and penetrations are sealed with acoustical sealant or sheathing tape
- can be applied in wide sheets to minimize; the number of seams required
- should be protected from extended exposure to sunlight
- when installed with stucco or embedded in stone veneers, requires a minimum of 6 mm (1/4 in.) gap for a drainage plane (use a drainage mat) to prevent the stucco from bonding to the house wrap
- should not come in direct contact with cedar because the oils in the wood can cause deterioration in the product
ii) Polyethylene sheeting
- is commonly installed as a vapour barrier in the thickness of 0.15 mm (6 mil) because it is more durable on the construction site
- should be labelled showing that it conforms to the Canadian General Standards Board (CGSB) standard for polyethylene
- can be applied in wide sheets to minimize the number of seams required
- should have the seams and edges supported on both sides to maintain the seal
- requires an appropriate sealant and overlapped joints
- functions as a vapour barrier
- should always be used on the interior or follow the 1/3 – 2/3 rule (see Part 1.4, Health and safety considerations)
- follow local building codes for placement of a polyethylene vapour barrier
Technical note:
If the sheeting will be exposed to sunlight over an extended period during renovations, use a UV-stabilized polyethylene.
iii) Polyamide sheeting
- is also known as Nylon-6 vapour retarder film or smart barrier
- adapts its permeability to the conditions: in cold temperatures, it offers high resistance to vapour pressure; in warmer conditions, it becomes more permeable, allowing the structure to dry out
- can be installed as a vapour barrier or an air barrier
- should not be used in indoor areas that have high humidity such as an indoor spa or pool or a bathroom
iv) Rigid materials
Most solid building components including drywall, plaster, plywood, glass, wood, rigid foam insulation and poured concrete (not concrete blocks) will act as air barriers. Seal all seams between these materials with the appropriate caulking, weatherstripping, tape or gasket. For example, caulking can be used between the baseboard and a wall as well as between the baseboard and the floor, linking the air sealing qualities of three building components.
3.3.2 Sealants
Caulking seals joints between building components. Most joints move because of changes in moisture and temperature in the building. Some materials can seal a larger joint and accommodate more joint movement than others. Choose carefully because there is wide variation among the same type of products produced under different brands. If possible, always select the premium product for long-term durability. Choosing the proper product and paying attention to the quality of application are crucial.
All sealants will require extra ventilation of the house after application to let the material cure. Typical curing time will be two or three days for interior applications. For application directions, see Part 4.2, Caulking and other air sealing materials.
Materials labelled “for exterior use only” may not be suitable for indoor applications because they may contain volatiles that may be hazardous in a confined space if inhaled over an extended period. Read the manufacturer’s literature carefully.
The following factors limit the effectiveness of caulking:
- the flexibility and elasticity of the product
- some products can span a larger gap than others
- use a backer rod or foam rope in joints of 6 mm (1/4 in.) and larger before applying caulking to ensure an effective seal
- its compatibility with the materials being joined
- its durability, paintability and curing time
- if the product will be exposed to sunlight, make sure it is appropriate for this condition
- its ease of removal and reapplication
- some products can be used over previous applications while others cannot; some clean up easily with water, some require solvents, and some are very difficult to remove once cured
Table 3-2 lists caulks and sealants available at most building supply stores. It is designed to help you select the best product for each application. If possible, always select a premium product for long-term durability.
Technical note:
Be mindful when using caulks and sealants. Urethane foams are impossible to remove once cured, other products are flammable. Read manufacturers’ literature and take proper precautions during installations (see Part 1.4, Health and safety considerations).
Type | Bonds to | Application | Maximum joint | Comments |
---|---|---|---|---|
Acoustical sealant |
|
|
|
|
Butyl rubber caulk (synthetic rubber sealant) |
|
|
|
|
Silicone sealant caulk |
|
|
|
|
Polysulphide caulk (synthetic rubber sealant) |
|
|
|
|
Polyurethane caulk (urethane) |
|
|
|
|
Acrylic latex caulk |
|
|
|
|
Acrylic latex with silicone caulk |
|
|
|
|
Elastomeric latex sealant |
|
|
|
|
Urethane foam sealant (low, medium and high expansion types) |
|
|
|
|
Latex foam sealant |
|
|
|
|
High-temperature stove or muffler cements and non-combustible sealants |
|
|
|
|
3.3.3 Gaskets
Gaskets are used to seal joints where caulking may not be appropriate. Figure 3-3 shows a gasket used to seal electrical outlets and Figure 3-4 shows a typical foam backer rod. Table 3-3 describes the most common types of gasket materials and where each type works best.
Type | Application | Installation | Comments |
---|---|---|---|
Sill plate gasket (polyethylene foam strips) |
|
|
|
Foam backer rod (closed-cell compressible foam rope) |
|
|
|
Electrical outlet and lighting fixture gaskets (pre-cut) |
|
|
|
Neoprene and elastomeric gaskets |
|
|
|
3.3.4 Weatherstripping
Weatherstripping is used to block air leakage around doors and the operable parts of windows. Weatherstripping comes in a variety of shapes: flat strip, tube or V (i.e. V-strips), and can be designed to work under compression or by sliding along the joint. To be effective, the product must close the gap and not allow air to pass. Some products get hard – and less effective – in cold weather when you need them the most.
When choosing weatherstripping, consider the size of the gap to be sealed and the durability, ease of installation and finished appearance of the product. Look for products that are flexible and that spring back to their original shape quickly and easily. Avoid products that make it difficult to operate the window or door. When replacing weatherstripping, bring a sample of the old material to the store with you to ensure that you purchase the correct product.
A wide range of products is available in most building supply stores, including complete sealing kits. For the best quality weatherstripping, contact window and door manufacturers or installers.
Table 3-4 lists the major types of products and Figure 3-5 illustrates them.
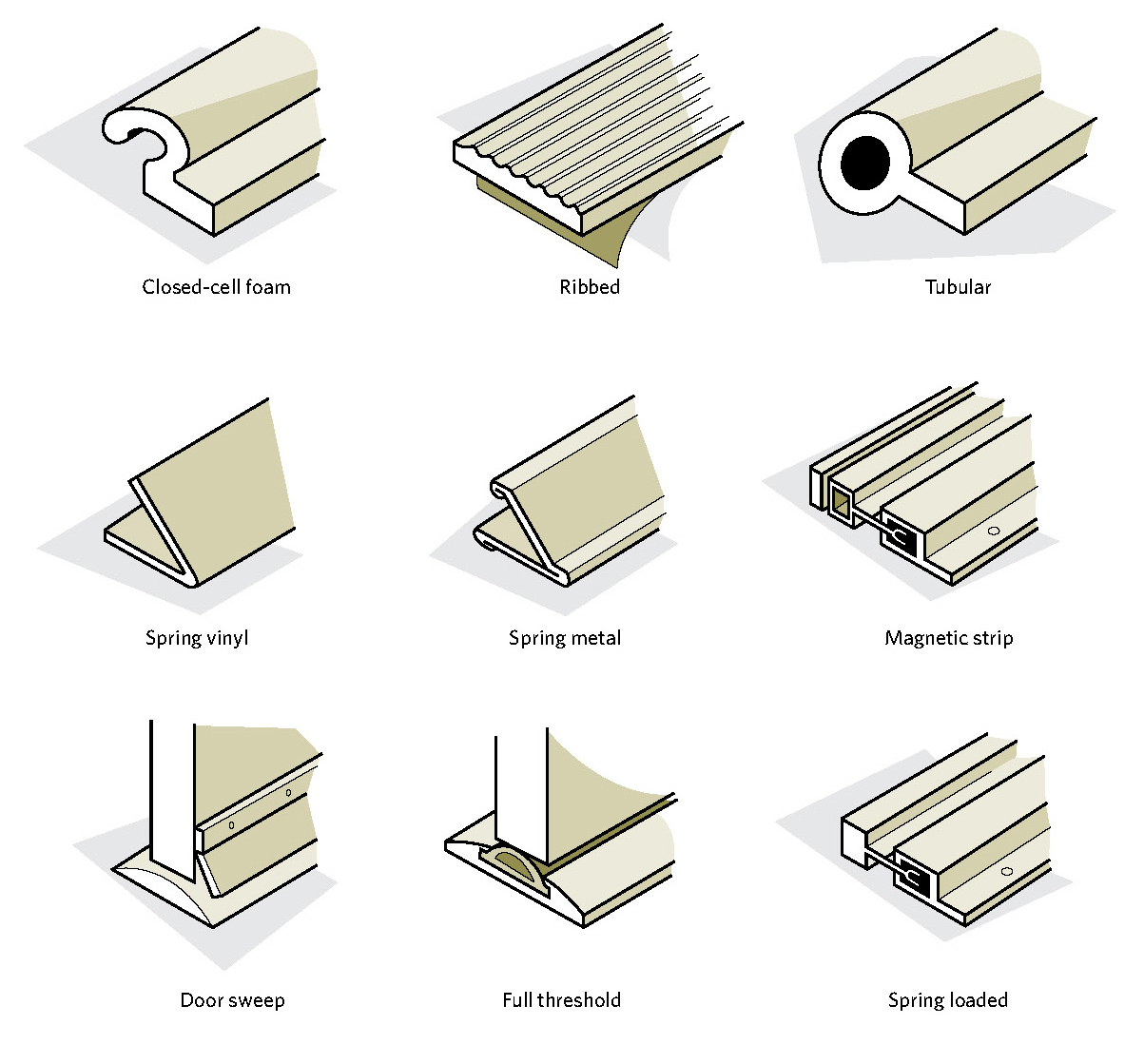
Figure 3-5 Types of weatherstripping
Text version
Nine illustrations of weatherstripping options including the following types: closed-cell foam, ribbed, tubular, spring vinyl, spring metal, magnetic strip, door sweep, full threshold, and spring loaded.
Table 3-4 Weatherstripping
Category | Application | Installation | Comments |
---|---|---|---|
Closed-cell foam (with or without vinyl covering) |
|
|
|
Ribbed closed-cell rubber | as above |
|
|
Tubular stripping material | as above |
|
|
Category | Application | Installation | Comments |
---|---|---|---|
Spring vinyl |
|
|
|
Spring metal |
|
|
|
Category | Application | Installation | Comments |
---|---|---|---|
Spring-loaded, self adjusting |
|
|
|
Magnetic-strip systems |
|
|
|
Category | Application | Installation | Comments |
---|---|---|---|
Door sweeps (attach to the door) |
|
|
|
Door bottoms |
|
|
|
Thresholds (attach to the floor or door frame beneath the door) |
|
|
|
Category | Application | Installation | Comments |
---|---|---|---|
Duct tape |
|
|
|
Sheathing tape (i.e. red technical tape) |
|
|
|
Electrical box air barriers |
|
|
|
Mastic putty |
|
|
|
Mastic latex sealant |
|
|
|
Pot light covers (recessed light covers) |
|
|
|
3.4 Vapour barrier materials
The vapour barrier is an important component of the house envelope because it protects the structure and insulation from moisture damage. The vapour barrier must resist the flow of water vapour from the interior, be durable and be located on the warm side of the insulation. In some cases it may be part of the insulation or air barrier. It should be easy to install and appropriate for other work being done on the home.
Install the vapour barrier to protect the entire surface areas of insulated walls, ceilings and floors. Give special attention to all penetrations, joints and junctions (e.g. light fixtures, wall plugs, switches and window frames) and areas that receive high humidity such as bathrooms and kitchens. Figure 3-6 illustrates an open electrical box, placed in a poly-pan vapour barrier box, encircled by a caulking to be attached to a vapour barrier.
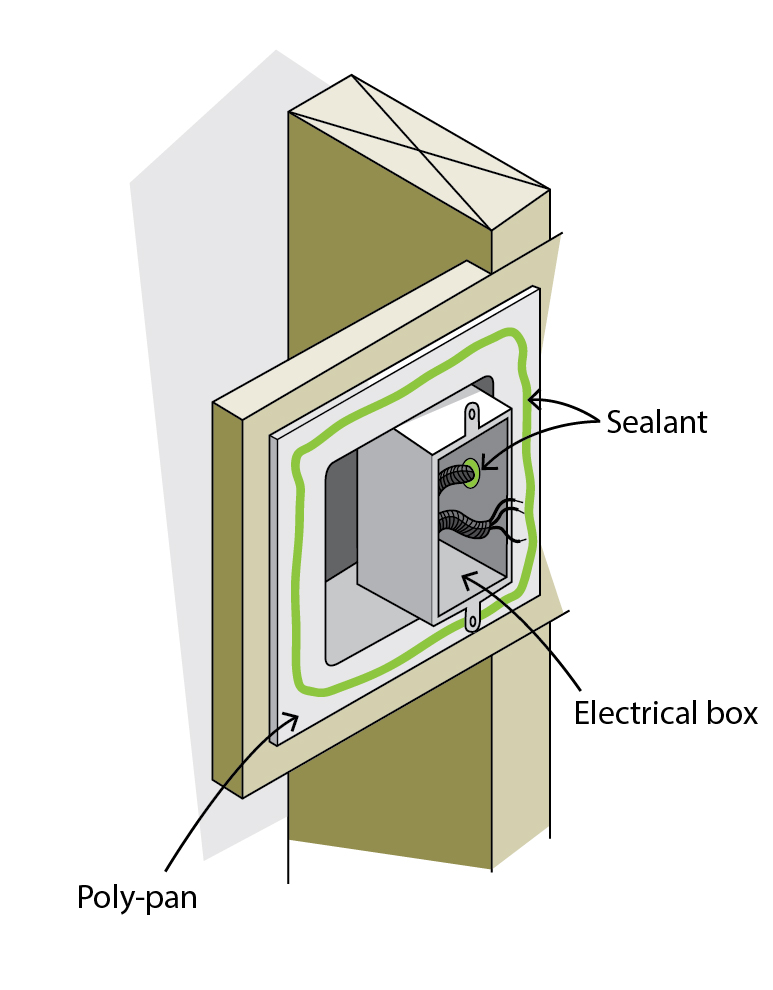
Figure 3-6 Sealing an electrical box
Text version
Illustration of an open electrical box, placed in a poly-pan vapour barrier box, encircled by a caulking to be attached to a vapour barrier.
Usually located on the warm side of the insulation, the vapour barrier can also be installed part way into the wall, provided that no more than one third of the insulating value of the wall is on the warm side of the vapour barrier. For information about the 1/3 – 2/3 rule, see Part 2.4, Control of moisture flow.
This amount of insulating value should be reduced to one quarter or less in very cold climates or in buildings with high moisture sources such as swimming pools. Like an air barrier, the vapour barrier can be made of various materials, including existing building components such as plywood, OSB, paint or vinyl wallpaper. In most older homes, the layers of oil-based primer and paint can function as an adequate vapour barrier for walls and ceilings.
Vapour barrier performance
The effectiveness of a vapour barrier (also known as a vapour diffusion retarder) is measured in terms of its permeability (perm) rating. The lower the perm rating, the more effective the moisture barrier will be. Materials considered to be effective vapour barriers include polyethylene, aluminum foil, polamide film (smart barrier), oil-based and latex vapour barrier paints (varying by type and thickness, some types and thickness of insulation and even some vinyl wallpapers).
Relevant topics: Section 1: Introduction
Page details
- Date modified: