Low Cost Wheel Motors for Electric and Hybrid Electric Vehicles
Lead Proponent: TM4 Inc.
Location: Boucherville, Québec
ecoEII Contribution: $ 3,719,000
Project Total: $ 5,681,000
Project Background:
Electric vehicle development represents a strategic option for Canada. For many years, several Canadian small and medium-sized businesses (SMBs) have been front-runners in their respective fields, helping Canada earn a strong reputation for innovation in certain key areas. After demonstrating the relevance and feasibility of several technical scenarios, the global electric vehicle industry is now focusing on developing solutions that are more integrated, more effective and more specialized. In order to meet growing market demand for electric or hybrid vehicles, auto companies are seeking out high-performance, reliable components at low cost.
Wheel motors are an ideal solution since they eliminate the need for transmissions, allowing for increased efficiency. They also free up room in the vehicle where the drive system and differential would normally be located, which is significant in compact vehicle development. Finally, wheel motors provide better vehicle performance in terms of road adherence. That being said, a number of technical issues, as well as high system costs have hindered wheel motor technology commercialization. Moreover, the weight of the motor itself poses problems for the suspension system.”
Recognizing the need to advance wheel motor technology, TM4 (a company with expertise in electric motor technologies) proposed the project “Low Cost Wheel Motors for Electric and Hybrid Electric Vehicles” for ecoEII funding. The project was awarded $3,719K to design an in-wheel motor electric drive system for electric vehicles, with one of the highest power densities in the world, and at the lowest possible cost
Results
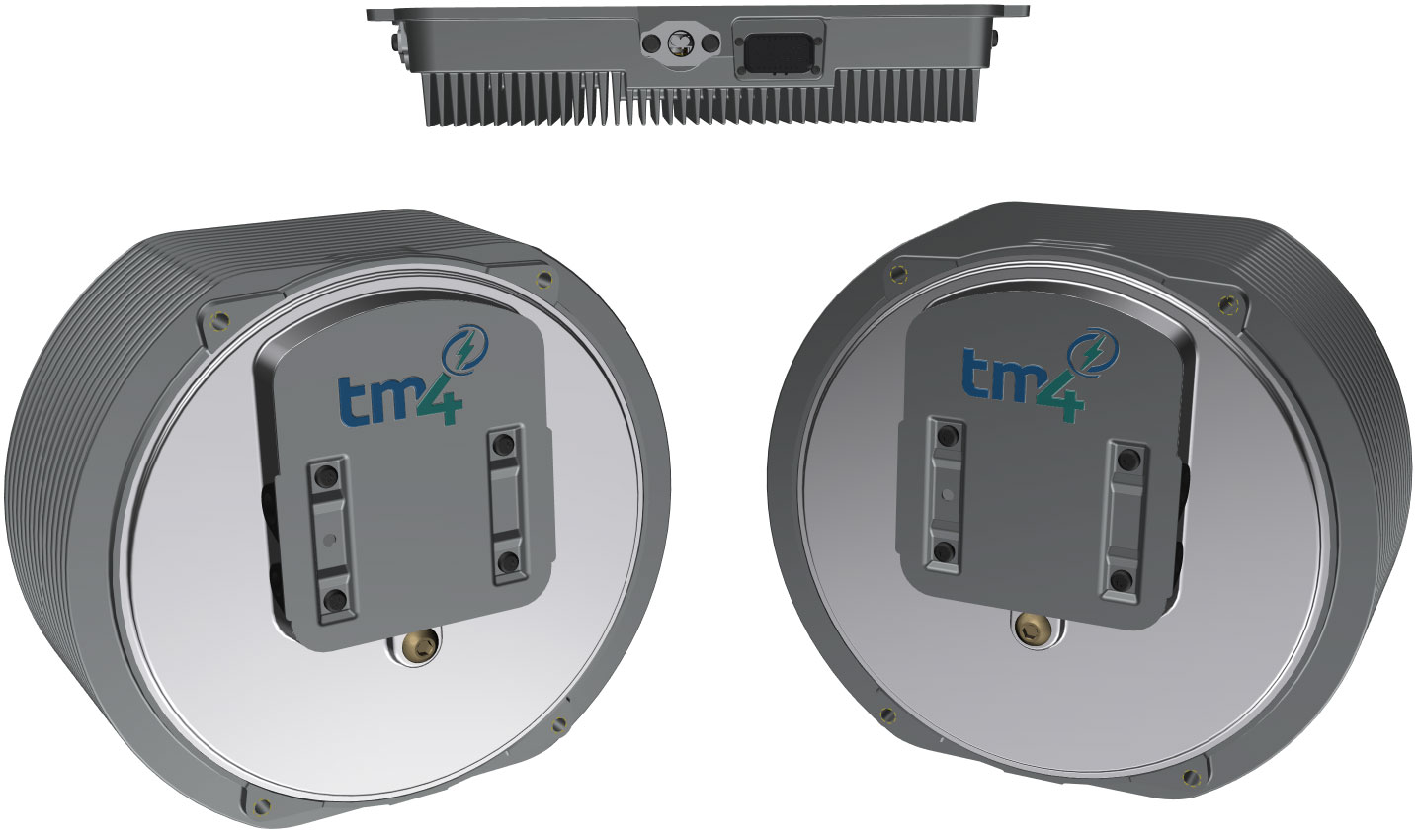
CNTA’s electric propulsion system
Text version
The photo contains three 3D engineering drawings. The drawing at the top is a grey rectangular inverter. The top of the inverter is flat and the bottom is serrated. The serrated metal represents fins for air cooling. There is a small black rectangular connector at the centre of the inverter. The two left and right drawings at the bottom are symmetrical and represent the grey circular electric motors. The surface of the outer radius of the motors consists entirely of fins. There are four black connector points as well as the blue TM4 logo on the front of the motors.
During the first year (Phase I) of the project, a feasibility study was conducted to identify innovative technologies with potential to increase the power density of TM4’s original wheel motor system. Results of the study contributed to the mechanical and electrical design and development of the first prototype wheel motor system, in the following year. The prototype was developed in accordance with the requirements of the project partner CNTA (Centre national du transport avancé). Requirements included: a nominal voltage of 350 V, a rated capacity of 20 kW per motor, a torque of 400 Nm and a maximum diameter of 30.48 cm. The prototype system consisted of an inverter controlling two motors.
The maximum power density of the prototype was measured to be nearly four times the power density of the original TM4 wheel motor. The torque density of the prototype wheel motor doubled in relation to the original TM4 wheel motor, i.e., 4 Nm/kg for the initial motor and 9.3 Nm/kg for the prototype motor. Moreover, the cost per kW of the prototype was 89% less than that of the original wheel motor.
CNTA’s electric motor on test bench
Text version
The photo shows a cylindrical silver aluminium motor installed on a test bench. The motor is fastened to an aluminium support on the left side. A green load motor is connected on the right side and the drive shaft is hidden behind an orange protector. Behind the motor is a large grey ventilator that supplies air via a blue rectangular conduit.
After the second year, CNTA was unable to secure the funding needed to pursue integration activities that were scheduled for the third phase. TM4 searched for potential integrators interested in the wheel motor for passenger vehicle application. Centre de technologies avancées - BRP - UdeS (CTA) showed interest in the technology for integration into one of its recreational on-road vehicles. The vehicle selected was equipped with a gas engine, and transforming it to an electric vehicle required TM4 to reduce the size and cost even further than that of the first prototype. Other requirements included: a maximum torque of 125 Nm and continuous torque of 50 Nm, a maximum speed of 6,500 rpm, continuous power of 20 kW, and a maximum length of 210 mm and diameter of 240 mm. A new P1 prototype was designed and assembled in order to meet CTA’s requirements. The P1 integrated new technologies, including an innovative cooling system and soft-magnetic composite powder wedges (for permanent magnet variable reluctance) in magnetic components of the motor. TM4 bench tested the P1 system and provided CTA with the results. The P1 system exceeded continuous power output requirement by 13 kW.
Benefits to Canada
Technological advancements in electric vehicle reliability and durability will increase buyer and consumer confidence and enable Canadian stakeholders to strengthen their position in the industry. More zero-emission vehicles on the roads will reduce Canada’s greenhouse gas emissions from the transportation sector.
Next Steps
TM4 intends to pursue system integration of P1 prototype and road testing of the completed system. The proponent also intends to conduct tests and explore new motor designs that can utilize soft-magnetic composite powder wedges.
Please contact the ecoENERGY program to obtain a copy of the TM4 Final Public Report. (Available in French only)
Page details
- Date modified: