Bioenergy Optimization Program Demonstration
Lead proponent: Manitoba Hydro
Location: Multiple locations in Manitoba
CEF contribution: $ 2.77 M
Project total: $ 6 M
Project Background:
Utilization of biomass as an energy source has been practiced for many thousands of years. Due to the sustainable nature of the source fuel, conversion of biomass to electricity generation has gained renewed interest in recent decades. Worldwide, there is more than 65,000 MW of installed capacity.
In Manitoba, the province’s utility (Manitoba Hydro) set out to obtain load reductions savings for both electricity and natural gas, as well as to help lower overall costs for its customers. Since biomass-to-energy conversion systems are believed to have future potential to compete with current generation technologies in the province, Manitoba Hydro launched the “Power Smart™ Bioenergy Optimization Program”. The program offered customers technical support and financial incentives to help offset project evaluation and capital costs associated with incorporating a biomass-to-energy conversion system into their operations. Manitoba Hydro proposed a series of demonstration projects across the province to showcase various technologies to potential program participants. Collectively, five demonstration projects plus an add-on component formed the “Bioenergy Optimization Program Demonstration Project” which received $2,772K from the Clean Energy Fund.
The 6 components of this project are featured below
1. Results - Pyrolysis Oil Demonstration Component:

Combustion of pyrolysis oil in the steam power boiler
Pyrolysis oil is a renewable liquid fuel derived from woody biomass via the fast pyrolysis process. The fuel is viscous, somewhat acidic, and contains a large fraction of water; the energy content of the fuel is approximately half that of diesel fuel on a volumetric basis. Ensyn Technologies supplied pyrolysis oil for the demonstration. Use of the oil (in place of fossil fuels) was tested in two different types of heat and power generation systems: in a large-scale multi-fuel power boiler and a community district heating system boiler, as well as, in a reciprocating diesel engine-generator.
Tolko Kraft Papers, located near The Pas, Manitoba, was the host site for the large scale boiler trial. Pyrolysis oil displaced heavy fuel and waste oil in a large power boiler and provided high pressure steam for a 22.3 MWe steam turbine generator CHP system. Approximately 68,880 L of pyrolysis oil were combusted in the steam power boiler over three combustion trial periods. Emission testing was performed by RWDI AIR Inc.
Then, at the Rock Lake Hutterite Colony near Grosse Isle, Manitoba, a 390 kWth hot water boiler fitted with a pyrolysis oil burner showcased the oil as an alternative fuel for community district heating system. Approximately 1,200 L of pyrolysis oil was combusted in the Boilersmith boiler fitted with an Oilon burner to deliver hot water to the Colony’s district heating network. Results from the demonstrations at Tolko and Rock Lake indicate that there exists a good potential for replacing fossil fuels with pyrolysis oil in both small and large scale commercial and industrial boilers.
Finally, testing and evaluation of the effects of pyrolysis oil on diesel engine fuel injector system was performed by Celtic Power & Machinery, in partnership with Assiniboine Community College. It was determined that more in-depth research and development will be required before a reciprocating engine fuelled by pyrolysis oil can be properly demonstrated.
Benefits to Canada:
The use of pyrolysis oil as an alternative to fossil fuels in conventional industrial and commercial boilers has the potential to provide significant environmental benefits including reduced emissions. Reduction of greenhouse gas emissions will benefit all of Canada, and the world.
Next Steps:
Pyrolysis oil for this demonstration was shipped from Ensyn Technologies in Ontario. A local supply of pyrolysis oil would be required to reduce transportation costs, and ensure that the fuel is a viable alternative. Through this demonstration, local interest in pyrolysis oil as a renewable fuel was generated, setting the stage for a pyrolysis oil fuel market in Manitoba.
2. Results - Syngas Demonstration Component:

BioMax100 gasification system installed at Pineland Forest Nursery
Biomass gasification is a thermochemical process by which solid biomass is converted to a synthesis gas (syngas) primarily composed of carbon monoxide, hydrogen, methane, and non-combustibles (carbon dioxide, nitrogen, and water vapour). The gasification system (BioMax100) featured in this component consisted of a fixed-bed downdraft gasifier operating between 800 and 900°C. The BioMax 100, developed by Community Power Corporation (CPC), was installed at Pineland Forest Nursery in Hadashville, Manitoba. Pineland produces high quality seedlings for silvicultural plantings in central Canada and the northern United States. Dry wood chips were fed from the top of the gasifier, and as they slowly moved down the gasifier, they passed through a drying zone, a pyrolysis zone, a gasification zone, and a char oxidation zone. The volatile gases in the pyrolysis zone and water vapour released in the drying zone moved downward under suction and reacted with the biomass charcoal and injected air according to gasification and water-shift reactions. The air was injected via hundreds of injection points throughout the gasification bed, and was tuned to finely control the temperature profile within the gasifier for maximum conversion of tars into gaseous products. The syngas generated in the gasifier was then cooled, filtered, and blown into twin reciprocating engine-generators to generate combined heat and power. Heat was delivered to a 200,000 L hot water storage tank, which had been integrated into the system and acted as a buffer tank between the BioMax100 CHP system and Pineland’s hot water distribution network.
The BioMax100 was online and generating electricity for 488 hours between April, 2013 and March, 2014. The system was capable of generating a net 100 kW of electricity and 120 kW of thermal energy. The longest period of continuous generation achieved was 22 hours. 18,155 kWh of electricity was generated to offset Pineland’s demand.
A variety of operational issues prevented the BioMax 100 demonstration from operating on a continuous basis. Some issues were overcome through troubleshooting and improving operational, maintenance and control processes. Other issues, such as the blockages in the feedstock handling system, are still ongoing and will require a reduction in the variability in the biomass feedstocks, and design or setup changes. Further development of the BioMax100 would be necessary before the technology could be relied upon for consistent generation of heat and power from wood chips.
Benefits to Canada:
Lessons learned from this project could be applied to future projects in order to substantially decrease the commissioning period, learning curve and down time. Once a system is proven to reliably and efficiently convert solid biomass to combined heat and power, it could replace other forms of generation and contribute to the reduction of greenhouse gases emissions in Canada.
Next Steps:
The system at Pineland Forest Nursery will be removed once the Remote Community Demonstration and Standarized Fuel Testing is completed. Electrical generation will be monitored throughout the remaining operation.
3. Results - Waste Heat Component:

GE Heat Recovery Solutions Clean Cycle 125 installed at Spruce Products Ltd.
Organic Rankine cycles (ORCs) can be used to generate electricity from low-grade heat sources. The ORC is a vapour power cycle similar to a steam power cycle, with the working fluid being a refrigerant or organic fluid with a lower saturation curve than steam. For this demonstration component, a GE Heat Recovery Solutions Clean Cycle 125 was installed at Spruce Products Ltd. (SPL), in the Swan Valley region of Manitoba. SPL is a manufacturer of premium lumber and wood products for the construction industry and the integrated wood products industry. This was GE’s first installation of the Clean Cycle 125 in Canada.
In the Clean Cycle 125, the working fluid (R245-FA) is circulated to an evaporator where heat from the low-temperature steam is used to boil and superheat the refrigerant. The refrigerant then passes through an expander – in this case, an integrated power module (IPM) with a high-speed micro-turbine that spins at angular velocities of up to 27,000 RPM. The low-pressure vapour that exits the IPM passes first through an economizer, then an air-cooled condenser, and is finally pumped back to the evaporator. Electrically, the high-frequency power produced by the IPM is converted to 60 Hz AC at 480 V via a power electronics module. The R245-FA working fluid allows the system to use heat sources as low as 105°C for power generation.
The Clean Cycle 125 system supplied by Waste Gas Power achieved a maximum net electrical output of 92 kW from low grade thermal energy (such as low pressure steam < 15 psi). The system suffered from poor performance and lower than expected productivity due to variability in thermal energy supply and the parasitic load from the air cooled condenser, as well as several significant component failures. That being said, the demonstration system generated electricity for 5,143 hours between Oct. 2011 and Dec, 2013. 206,046 kWh of electricity was produced to offset SPL’s electrical demand.
Benefits to Canada :
The best applications of ORC technology are industrial sites with medium to high grade waste heat streams such as refineries, cement plants, and steel mills. Once a system is proven to reliably and efficiently harness low-grade heat sources for electrical production using ORC technology, it could replace other forms of generation and contribute to the reduction of greenhouse gases emissions in Canada.
Next Steps:
The Clean Cycle 125 system at SPL will continue to operate for five years beyond the end of the project, conditional upon reaching a suitable operating agreement with the host site. Electrical generation will be monitored throughout the five year period.
4. Results - Biogas Component:

A continuously mixed concrete tank reactor where manure digestion takes place
Anaerobic digestion is a microbiological process by which high moisture content organic material is transformed in the absence of oxygen to produce biogas – a mixture of methane, carbon dioxide, and trace amounts of hydrogen sulphide (H2S) – and liquid digestate. On-farm anaerobic digesters use livestock manure as the base feedstock, and may add other organic feedstocks or co-substrates – such as vegetable waste, grease trap waste, or glycerin – to increase biogas production.
For this demonstration component, a PlanET Biogas Solutions complete mix anaerobic digester and biogas CHP system was installed at Sweetridge Farms near Winkler, Manitoba. Sweetridge Farms are the owners of a 200 head dairy farm who are seeking better manure management practices.
In the PlanET system, manure digestion takes place in the mesophilic temperature regime (35°C to 40°C) in a continuously mixed concrete tank reactor. H2S is removed from the biogas using a microbial process that resides on a wood structure within the digester. The lower H2S content biogas is then consumed in either a biogas engine – in this case, a 75 kW Caterpillar natural gas engine – or a boiler – in this case a 200 kW dual-fuel propane/biogas Boilersmith boiler. Digested manure (digestate) is treated using a FAN solid-liquid separator system, and the solid fraction of the digestate (or fiber) is recycled to the dairy barn as a substitute for straw bedding.
Construction and commissioning of the PlanET system at Sweetridge Farms faced significant regulatory barriers. Strict application of the CSA B149.6 Code for Digester and Landfill Gas, requirements for biogas flares, modifications to accommodate manure and mortalities regulations along with a lack of capacity of equipment suppliers to provide engineering support in order to address regulatory issues increased the cost and complexity of the project. Major changes to the design of the system were therefore required, which lead a delay in the construction and commissioning of the system. The PlanET system was partially commissioned in March 31, 2014.
Benefits to Canada:
Manitoba’s provincial government has shown interest in deployment of anaerobic digestion technology to address manure management issues in the province. However, changes to policy and legislation at the provincial level are required. On-farm anaerobic digestion and biogas CHP technology has been commercially deployed in other jurisdictions in Canada such as Ontario. On-farm biogas production could contribute to the reduction of greenhouse gases emissions in Canada.
Next Steps:
The PlanET biogas plant at Sweetridge Farms is expected to be put into operation and continue to operate for the next five years, conditional upon reaching a suitable operating agreement with the host site. Electrical generation will be monitored throughout the five year period.
5. Results - Biocarbon Component:
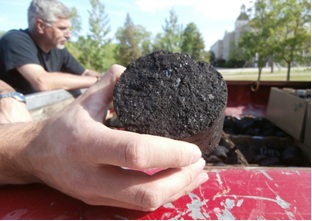
3-inch biocarbon briquette made at Biovalco’s biomass densification facility
Biocarbon is a renewable solid fuel product derived from solid biomass through the thermochemical process known as slow pyrolysis. Cellulosic biomass (wood, agricultural residues, or wetland biomass) is heated to between 400°C and 500°C in the absence of oxygen to break down the cellulose and hemicellulose components into vapours, leaving the fixed char in solid form. The char is the biocarbon product, while the hot vapours may be directed towards a burner to provide heat for the reaction, or may be condensed to form pyrolysis oil and wood vinegar. When the volatile gas fraction is combusted, the process is heat self-sufficient, with excess high-grade heat available for use in heating or power generation applications.
For this demonstration component, Preseco Oy (Canada)’s pilot carbonization system was installed at Rock Lake Hutterite Colony near Grosse Isle, Manitoba, for the trial production of biocarbon from woody biomass. The biocarbon was then briquetted at Biovalco’s biomass densification facility in La Broquerie, Manitoba. The 3-inch biocarbon briquettes were sent to Providence University College near Otterburne, Manitoba where they were test-fired in the 1.2 MWth Blue Flame Stoker boiler system on campus. The system at Rock Lake operated from October 2012 to February 2013, producing enough biocarbon for 660 kg of briquettes at Biovalco’s facility.
The production of biocarbon from cattail biomass was also validated. Approximately 1,800 kg of cattails were harvested at Pelly’s Lake, Manitoba in the fall of 2012. The bales of cattails were transported to Titan’s slow pyrolysis plant near Craik, Saskatchewan where they were carbonized to produce 400 kg of biocarbon. Similarly, the cattail biocarbon was made into briquettes at Biovalco’s facility in 2014.
Benefits to Canada:
The production, densification, and combustion of biocarbon from wood chips and cattails have technical potential; however carbonization equipment and supporting processes are not yet sufficiently developed to be viable in Manitoba. Should carbonization equipment reach productive, reliable and safe operation, use of biocarbon as an alternative fuel provides opportunities for Manitoba and all of Canada to displace fossils fuels in heat and power production, reduce greenhouse gases through carbon sequestration, and improve nutrient management and soil productivity.
Next Steps:
Based on the experiences and knowledge gained in this project component, Economic Development Winnipeg Inc., the lead economic development agency for Winnipeg, plans to proceed with validating a business case for biocarbon by looking at systems, technology and market opportunities for the renewable fuel. The International Institute for Sustainable Developement (IISD) based in Winnipeg is also continuing research on the production of biocarbon from cattail biomass.
6. Results - Remote Community Add-on Component:
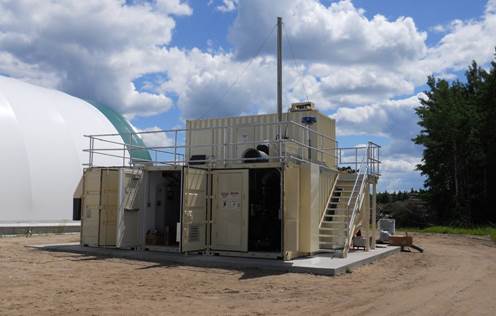
Building that houses the BioMax100 gasification system at Pineland Forest Nursery
Remote communities that are reliant on diesel fuel for electricity and heat are a current focus for the application of renewable and clean energy technologies, primarily based on the high cost of energy in these communities. However, significant challenges exist when deploying power generation projects in remote northern Canadian communities. In Manitoba for instance, communications and approvals are required from several different organizations such as the local Band Chief and Council, Aboriginal Affairs and Northern Development Canada, and Manitoba Hydro. In addition, capital projects must be included in a five year capital plan for the communities. Furthermore, remote communities have limitations on availability of skilled labour, construction equipment & materials and times of access. These factors significantly increase costs and timelines. These challenges were, in part, the primary reasons why Manitoba Hydro elected to add-on a sixth component to the demonstration project.
For this add-on component, Manitoba Hydro set out to demonstrate and evaluate a technology alternative to diesel power generation suitable for deployment in remote northern Canadian communities. Three alternative technologies for renewable combined heat and power generation technologies were evaluated for deployment: pyrolysis oil, ORC with waste heat, and biomass gasification for the production of syngas. These technologies all have potential to interface with diesel engine powered systems. However, reciprocating engines fired on pyrolysis oil are still in an R&D stage. ORC technologies would be suitable for deployment in remote communities, but have more limited diesel fuel displacement potential in comparison to pyrolysis oil and syngas. The BioMax100 gasification system is complex and its limited commercial installations to date may prohibit application at the present time, however its modular, portable design and ongoing equipment refinement offers good potential for future application.
The BioMax100 system (like the one installed at Pineland Forest Nursery as part of the Syngas Demonstration Component) was therefore chosen to simulate operation in a remote northern community. A new char-ash handling system was designed and installed to provide enough capacity for the char-ash produced by the gasifier, over a 48-hour period. This was done to increase unsupervised continuous run times and eliminate the need for an overnight operator. Small-diameter black spruce trees, similar to those found in Northern Manitoba, were harvested, chipped, and delivered to Pineland for testing in the BioMax100 system. An operator with skills and background similar to someone from a remote northern community was also hired to operate the system. It was determined that the BioMax 100 system is not sufficiently reliable for deployment in a remote community setting at present.
Benefits for Canada:
The impact of the high cost of energy in remote communities in Canada is significant. Alternative renewable sources of electricity and heat for these communities will go a long ways towards improving the social and economic status of these communities, as well as reducing their carbon footprint.
Next Steps:
This component will continue for 12 months beyond project end. The system will be put into operation and data on the operational activities, fuel costs, and electrical and heat production will be collected throughout the 12 month period.
Page details
- Date modified: