ARCHIVED - Council of Energy Ministers
Information Archived on the Web
Information identified as archived on the Web is for reference, research or recordkeeping purposes. It has not been altered or updated after the date of archiving. Web pages that are archived on the Web are not subject to the Government of Canada Web Standards. As per the Communications Policy of the Government of Canada, you can request alternate formats. Please "contact us" to request a format other than those available.
Moving Forward on Energy Efficiency in Canada: A Foundation for Action
Industry
Scope
The industrial sector can be divided into two groups: the energy consumers (mining, manufacturing23, and construction); and the energy producers (upstream oil and gas, heavy oil upgrading and electricity generation).
Context24
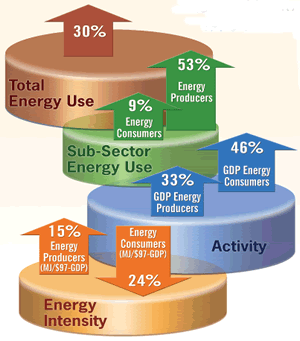
Industry is currently the dominant energy user in Canada, accounting for 48% of primary energy demand in 2004 and generating 29% of economic output ($303 billion in GDP). Overall energy intensity improvements of 9% since 1990 resulted in annual fuel savings of $3.1 billion and avoided greenhouse gas emissions of almost 30 Mt per year. Energy efficiency in industry can substantially reduce costs and provide enormous productivity, environmental and other non-energy benefits.
Energy Consumers
Between 1990 and 2004, the energy-consuming industries had an extremely positive record of energy intensity during a period of strong growth in output (45%). In 2004, Canada’s mining, manufacturing and construction sectors used 24% less energy to produce a unit of product than they did in 1990. This can be explained by investments in energy efficiency, fuel switching and shifts in production from more energy-intensive industries, such as iron and steel, to less energy-intensive industries, such as computer and electronic products. Analysis shows that efficiency investments accounted for over 70% of overall energy intensity improvements25. Improvements came from sect ors as diverse as textiles and food and beverage (where energy represents less than 10% of overall manufacturing costs), to pulp and paper, cement and lime (where energy represents between 25% and 50% of overall costs)26.
Rock Solid Savings
CVRD INCO (Ontario) reduced its energy consumption by 10% since 1990, while increasing production by 20%. In total, the company has recorded a $60 million reduction in energy consumption since 2000.Energy Producers
In contrast, the energy-producing industries became 15% more energy intensive between 1990 and 2004. As production rose by 33%, energy use increased by 53%. This increase in energy intensity occurred in both the upstream oil and gas and electricity generation sectors.
In the upstream oil and gas sector, it takes more energy to produce oil and gas today than it did in the past. Conventional oil and gas reserves are increasingly more difficult to access, thus requiring more energy. The more intensive extraction process in the oil sands uses more energy compared to conventional reserves.
In the electricity generation sector, the increased energy intensity results from a decrease in electricity generated from non energy-intensive hydroelectric sources relative to the more energy-intensive coal and natural gas-fired generation.
Proactive Corporate Culture Leads to Remarkable Results
BP Canada’s proactive corporate environmental culture and positive view of energy efficiency have led the company to achieve remarkable results. In recent years, the company has completed more than 400 energy efficiency projects, resulting in emissions reductions of more than 300,000 tonnes of carbon dioxide equivalent per year.
Looking forward, the environment for industrial energy use will be subject to change:
- The 2007 federal Regulatory Framework for Industrial Air Emissions sets out short-term emission intensity reduction targets for greenhouse gas emissions that will require an 18% emission intensity reduction over 2006 levels by 2010, and a 2% annual improvement thereafter. Under the framework, when interpreted in regulation, firms would be able to choose the most cost-effective way to meet their targets from a range of compliance options including in-house investments in energy efficiency and fuel switching as well as contributions to a technology fund, inter-firm trading, domestic offset, and access to the Clean Development Mechanism. Air pollutants will also be regulated.
- In terms of productivity and innovation, Canadian manufacturers perform on average about half as well as the best of the G7. Our excellence gap is, therefore, 50% of G7 best practice. Canada, in fact, turns in one of the lowest performance ratings of any of the world's major industrial economies when all benchmarks are taken into account27.
- More energy will be required to extract non-renewable natural resources, like copper, iron ore and oil and gas. As existing reserves are depleted, resources are less accessible and will require more energy to exploit.
Energy efficiency can play a strong role to help industry address these issues, with the additional benefit of providing significant environmental improvements such as reduced greenhouse gas emissions and cleaner air.
Key Tools, Technologies and Practices
A wide array of tools can be used to improve industrial energy efficiency. These tools can aid industry in the implementation of energy efficient actions through equipment replacement, minimization of process waste, new plant design and construction, the adoption of emerging technologies and management best practices. The following are key tools for use in this sector:
Policy/Regulation |
Develop mandatory minimum performance standards for industrial equipment (e.g. large air conditioners, heat pumps, condensing units, commercial boilers). Develop codes and standards for energy efficiency in new industrial plants that integrate equipment and building envelope requirements. Develop an energy management best practices rating system. |
---|---|
Research, Development and Deployment | Support the development of new industrial cutting edge technologies (e.g. combustion, insulation, production and plant control). |
Capacity Building |
Provide energy efficiency training to industrial employees at all levels to improve technical knowledge and shape corporate culture. Provide training to industrial energy efficiency service providers to ensure that clients receive current energy efficiency information (eg. consultants, product manufacturers/distributors). |
Leadership | Encourage regional/local networks of industry leaders and government officials to examine energy efficiency needs on a regular basis. |
Information |
Undertake employee awareness campaigns to help employees use energy more efficiently at work, at home and on the road. Develop and distribute publications and tools to educate industry about technical, operational and organizational good energy management. |
Market Stimulation |
Ensure that prices reflect the real cost of energy (e.g. two-tiered pricing, time of use pricing). Develop and encourage the use of creative financing mechanisms to improve project economics (e.g. revolving funds, energy performance contracts). Place levies and/or taxes on the use of energy. Provide financial incentives for projects with long payback periods. Provide financial incentives for emerging and cutting-edge technologies. |
Pointing the Way to Savings
Some 6000 participants from industrial organizations have used energy-saving tips from a modest workshop program to collectively save $100 million or 10 PJ since 1997. This is enough energy to heat half the homes in New Brunswick. Natural Resources Canada's Office of Energy Efficiency offers the Dollars to $ense workshop series to help organizations find, plan and implement energy efficiency opportunities. For example, a Proctor & Gamble plant started tracking their energy use and created an in-house team which led to the implementation of 80 projects proposed by P&G employees from the shop floor; eliminating pre-filter fans alone saved $158,000 a year.
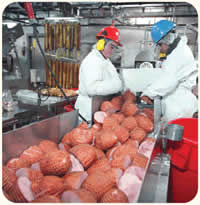
These tools can be used to support energy efficiency improvements in a number of areas. Studies from two provinces suggest that the largest areas of opportunity for equipment retrofit and replacement are28:
- Motors and Motor Driven Systems - The potential exists to save 30% to 60% of the energy consumed by motors by optimizing motor and compressor size, using variable frequency drives and managing air compressor leaks. Motors represent about 20% to 30% of industrial energy use.
- Direct Process Heat - Potential energy savings are estimated at 10% to 35% of energy consumed by direct process heat equipment. Improvements that can be made include heat recovery, boiler upgrades and replacement as well as other process-specific opportunities such as oxy-fuel combustion in the steel industry. This area represents about 20% to 40% of industrial energy use in Canada.
Waste Not, Want Not
Following a process integration study supported by Natural Resources Canada, Maple Leaf Consumer Foods installed a heat exchanger system to capture heat from ammonia gas before the rooftop condensers cool it. The new installation diverts the captured energy to the plant’s water supply, where it helps heat a 15,000-litre hot water tank. A monitoring system calculates and records actual energy savings in real time, enabling operators to verify that the heat recovery system is operating correctly. The system has lowered natural gas consumption in the plant’s boiler system by 22% and reduced the need for boiler chemicals.
Opportunities for system-wide improvements also exist such as improved monitoring and tracking of energy use and advanced modeling and analysis methods to improve productivity and throughput.
These technologies can be used by energy consumers and producers alike. There are, however, some improvements that are specific to the energy producers sector:
- Supercritical electricity generation units, which are made of super alloys that can withstand high temperature and pressure, can be used to increase efficiencies of new fossil-fueled generating stations from current levels of 32-34% to 36-40%.
- Gasification technologies can provide the upstream oil and gas sector with hydrogen, heat and electricity by using fuels such as biomass, municipal solid waste and residues from oil refineries instead of natural gas, while achieving efficiencies greater than with the use of natural gas.
You can’t manage what you can’t measure – Lord Kelvin, 1891
Lord Kelvin who invented the Kelvin temperature scale knew that measurement is key to good management - and this applies equally to profit, spending or energy use. Pratt & Whitney Canada Corp. profited from this concept by monitoring and, tracking energy-demand fluctuations with a novel energy tool. Installed at three company plants, the new tool predicts long-term energy consumption and tracks key operational parameters. Since its installation, the tool has led the company to implement 70 energy projects and save over $1 million from the installation of energy-efficient boiler systems; better lighting controls; improvements to Heating Ventilating and Air Conditioning (HVAC) systems; compressed air and other systems; and a high-profile employee awareness campaign.
The use of a combination of the tools presented here can help industry to make some of the changes illustrated above. Increased action can set the stage for building sustainable energy efficiency improvements and help position energy efficiency as a core business value in the same way that health and safety is a core business value today. Through these changes, energy efficiency can be at the forefront of business decisions for equipment replacement and retrofit of industrial processes, to minimize waste in existing facilities. New industrial plants built to stringent energy efficiency standards, could be energy self-sufficient where possible. Capacity can be built for the development of new energy efficiency technologies. Barriers to energy management can also be minimized.
23 Including petroleum refining.
24 Unless otherwise stated, data in this section are based on Natural Resources Canada’s Energy Use Data Handbook, 1990 and 1998 to 2004. August 2006.
25 Based on methodology and data used in Natural Resources Canada’s Canada’s Energy Efficiency Trends in Canada, 1990 to 2004. August 2006.
26 Statistics Canada, Annual Survey of Manufactures and Logging. 2006.
27 Canadian Manufacturers and Exporters, 2020, Building our Vision for the Future, 2004, page 19.
28 Marbek Resource Consultants, Neill and Gunter, Energy Performance Benchmarking & Best Practices in New Brunswick Industrial and Manufacturing Sector, 2006. Ontario Power Authority, Market Profile and Conservation Opportunity Assessment for Small and Medium-Sized Industry in Ontario, 2006. Ontario Power Authority, Market Profile and Conservation Opportunity Assessment for Large Industrial Operations in Ontario, 2006.
Page details
- Date modified: