Metal Forming
Metal forming research involves primarily the development of novel alloys and processes in the study of lightweight metals, such as advanced high-strength steel, aluminum, titanium and magnesium alloys. These materials are being considered in the transportation sector to reduce weight and fuel consumption. Other metal forming activities involve the study of materials for the nuclear, pipeline and defence sectors.
CanmetMATERIALS’ pilot-scale metal forming facility is used to study technologies such as stamping, extrusion and forging. The facility includes an 1800-ton triple-acting press, a 1200-ton single-acting forging press and a 500-ton hydro/gas bulge forming press. The triple-acting press can be used for sheet stamping trials, but also as an extrusion facility with a capability of about 600 tons. In this last set-up, a billet can be extruded vertically into a pit beneath the press. The single-acting press has an advanced control system and is used for forging and squeeze casting. The hydro/gas bulge forming press is used mainly to conduct formability studies of sheet and tubular metal.
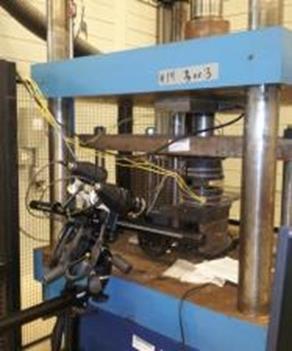
Double-acting forming press with Digital Image Correlation for strain measurement.
Photo by CanmetMATERIALS.
The Metal Forming lab also boasts other key technical capabilities:
- Forming Limit Diagrams up to 350°C using Marciniak method
- Multi-axial testing: hydro/gas sheet and tube forming
- Advanced strain measurement using Digital Image Correlation (ARAMIS/ARGUS)
- Simulation of metal forming processes using ABAQUS
- Warm/hot die design for stamping, extrusion and forging
These capabilities can be used in the following applications:
- Deformation and forming limits of advanced high-strength steel, aluminum, magnesium and titanium alloys
- Anisotropic characterization of hexagonal closed-packed metal (e.g. magnesium, titanium and zirconium alloys)
- Controlled forging and extrusion for improved materials properties
- Experimental validation of advanced computational materials models
Page details
- Date modified: