Biofuels for Steelmaking
Steelmaking is an energy-intensive process. According to a 2002 survey, the energy consumption of Canadian iron and steel manufacturing was 247 petajoules (NAICS Energy Consumption Report). The major energy sources for this sector are coke, coke oven gas and natural gas, which account for over 80% of the energy consumed. This heavy dependence on non-renewable energy sources makes the iron and steel industry a major greenhouse gas (GHG) emitter.
In 2005, the GHG emission associated with iron and steel production in Canada was 13 Mt CO2eq, ranking this industry as the second highest emission source among various industrial sub-sectors. This sector also accounted for 18% of the GHG emissions by the entire manufacturing sector.
Integrated steel mills use the blast furnace (BF)-basic oxygen furnace (BOF) route to produce steel. During this process, iron ore and coke (prepared by pyrolysis of coal) are charged into the blast furnace where iron ore is chemically reduced and physically melted into molten metallic iron. To lower the coke consumption in this process most modern blast furnaces are also equipped with auxiliary fuel injection for direct usage of carbon base fuels.
The molten iron produced is tapped from the BF regularly and transferred to the BOF for lowering its carbon content and converting it into steel. Recycled steel can be re-melted by either charging into the BOF or using the electric arc furnace (EAF) to increase the steel throughput of the mill. The produced molten steel is further refined in the ladle where it is subject to fine adjustments to its temperature and chemistry prior to casting. (Figure)
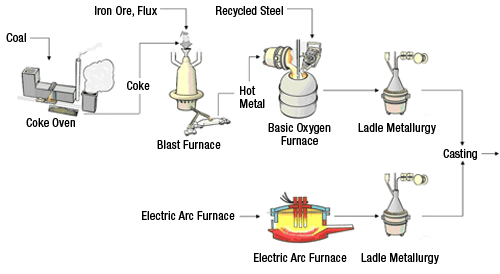
Typical Integrated Steelmaking Process
Carbon supplied to the blast furnace serves to both reduce the ore into metallic iron and provide a source of energy for melting. Because of this duel role, most non-carbon based renewable energy sources are not suitable for blast furnace ironmaking. Understanding the importance of mitigating the CO2 emission of the cokemaking-blast furnace system, substitution of fossil fuel with biofuel is proposed. As fossil fuel, biofuel is also carbon-based but the CO2 released in its combustion does not increase GHG concentration in the atmosphere. Hence, biofuel is capable of mitigating the environmental impact of ironmaking and supplying carbon to maintain the productivity of the furnace.
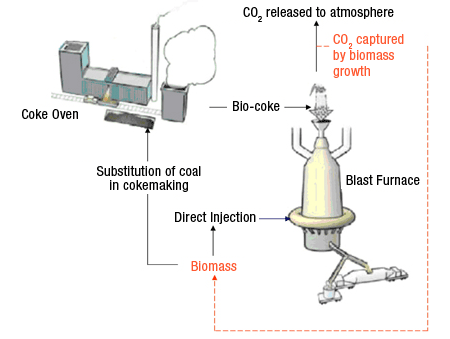
Illustration of Biofuel Application in Blast Furnace Ironmaking
Biofuel can be used in two ways in the cokemaking-blast furnace system. As coke prepared by substituting a portion of the coal blend by biofuel - termed ‘bio-coke’ (figure 1) and as an auxiliary fuel injected directly into the furnace (figure 2).
CanmetENERGY’s experimental research is being performed to investigate both the hot and cold strengths of bio-coke. The goal of this study is to prepare bio-coke suitable for modern blast furnace application. Numerical simulations have also been done to examine the effect of direct biofuel injection on blast furnace behaviour and its ironmaking ability. Charcoal was found to be the most effective biofuel for direct injection in terms of GHG mitigation potential. Furthermore, furnace conditions were not significantly affected by charcoal injection and the ironmaking ability of the furnace could be preserved. Complete substitution of fossil fuel injection by biofuel could reduce the GHG emission of steelmaking by as much as 25%, from about 13 Mt/yr to 9.8 Mt/yr.
Page details
- Date modified: