Lignin-to-Drop-In BioJetfuels and Chemicals
Lead Proponent: CRB Innovations Inc.
Location: Sherbrooke, Quebec
ecoEII Contribution: $ 1,000,000
Project Total: $ 1,505,000
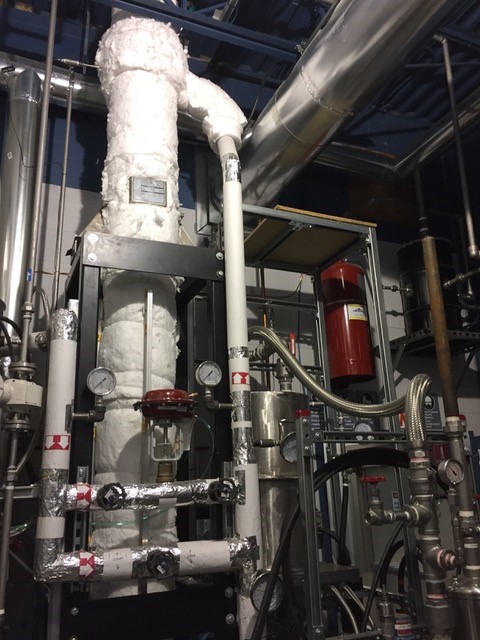
Base-Catalyzed Depolymerisation (BCD) depolymerization reactor assembly
Project Background:
Lignin is a complex organic chemical compound found in wood, in the cell walls of most plants and in some algae. It is a by-product of the kraft pulping process and can also be produced in fractionation facilities using residual biomass (forest and wood processing residues, wood debris from construction, and agricultural residues such as straw) as feedstock. CRB Innovations, a technology company headquartered in Sherbrooke, Québec owns and operates a pilot unit and a demonstration plant (150 kg/h, dry basis) that produces lignin for use in process heat generation via combustion.
However, a disruptive alternative to combustion had emerged from ongoing research being performed the University of Sherbrooke, NREL, CanmetENERGY, as well as in CRB’s own lab. It was discovered that through a Base-Catalyzed Depolymerisation (BCD), lignin could be converted into functional monomers (having significant value as specialty chemicals) and oligomers (upgradable to hydrocarbons molecularly compatible with biojet fuels). Since initial results had proved encouraging, CRB proposed the project “Lignin-to-Drop-In BioJetfuels and Chemicals” for ecoEII funding. The project was awarded $906K to demonstrate that lignin can be isolated from advanced fractionation processes and can be subsequently catalytically depolymerized to produce useful and marketable co-products such as drop-in biofuels and specialty chemicals.
Results:
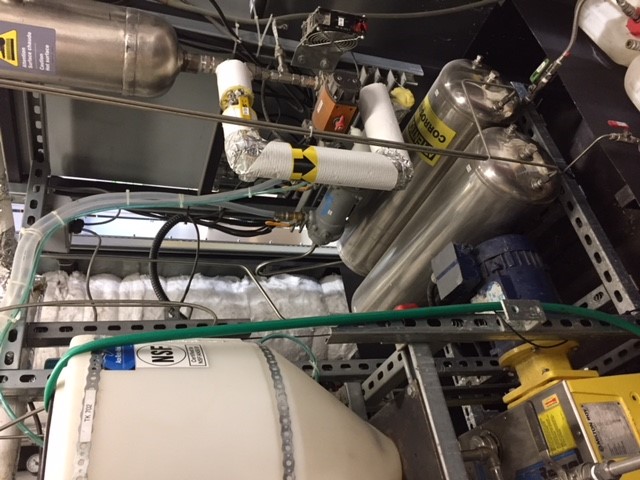
Base-Catalyzed Depolymerisation (BCD) pumping and preheating system
CRB Innovations adopted a modular approach to the design of a BCD pilot plant. Module 1 BCD reactor: uses a plug flow tubular reactor model that allows reaction parameters to be adjusted in order to achieve the optimum conditions necessary for lignin depolymerisation. Module 2 Acidification and Solid/Liquid Separation (ASLS) process: solidifies and separates organic products that are dissolved in the BCD reactor effluent (an alkaline aqueous solution) through acidification and filtration. Module 3 Solvent-Extractions and Solid-Adsorbent (SESA) process: efficiently extracts Monomers Rich Fraction (MRF) from the aqueous solution using a Kühni liquid–liquid extraction column. Module 4 Recovery of monomers: uses various solvents for extraction of MRF and Oligomers Rich Fraction (ORF). Module 5 Recovery of cations and anions used in the BCD process: uses electro-technologies to recycle ions.
A BCD pilot plant capable of processing 5 kg/h of lignin was designed, fabricated and put into operation. The plant yielded high value monomers (7-9 wt% of the recovered Lignin), oligomers (65-70 wt%), low value (residual) monomers (5-8 wt%), biocarbon-rich residue (char) and some gases (rich in biobased CO2). High value monomers are specialty oxy-aromatic chemicals (all carbon is biogenic) with identified markets. The oligomers were catalytically upgraded to drop-in hydrocarbon biofuels by a third party. Such biofuels are, to a large extent, within the kerosene-naphtha range of hydrocarbons and can therefore be considered for use as biojet fuels in the aviation sector. The biofuels yield represents 42.5 wt% of the oligomers treated, for a total of 27.6-29.75 wt% of the treated lignin.
A techno economic analysis was performed, and the results led to the development of a “hub & spoke” business model for lignin production and processing where by satellite plants deconstruct and fractionate local (regional) residual biomass (40-60 thousand metric tonnes, dry basis) into intermediates (including lignin). Intermediates from several satellite plants are then converted to marketable products and valorized at finishing hubs. Productivity gains through economies of scale would be achievable in this hub & spoke model. For the production of oligomers, petroleum refineries could serve as finishing hubs whereas for monomers it could be chemical companies.
Key learnings include: lignin from steam fractionation is better suited than Kraft lignin for depolymerisation; monomers and oligomers can be readily separated; oligomers can be valorized via direct use as feedstock for biofuel or via derivatives for the aromatics polymer; and high value monomers can be separated, isolated and purified.
Benefits to Canada:
Successful recovery of lignin from the deconstruction and fractionation of residual wood, and subsequent depolymerisation to marketable products such as biojet fuel would benefit Canada economically as well as environmentally through avoided greenhouse gas emissions (resulting from fuel switching).
Next Steps:
To install and commission a pre-commercial demonstration system, potentially at CRB’s Westbury facilities where a deconstruction and fractionation process is already functional. Lignin-derived biofuels and specialty chemicals could therefore be produced, evaluated and homologated, then introduced to the appropriate markets.
Page details
- Date modified: