BOILER AND HEATER OPERATIONAL CONTROL
Previously, this guidebook explained why it is necessary to operate a boiler with more air than is theoretically needed to burn all the fuel. Burner controls are therefore always set to provide some amount of excess air in all operating scenarios, typically from two to five percent O2 in the flue gas. This guidebook has also pointed out that excess air incurs a heat loss; it enters the combustion system at ambient temperature and leaves at stack temperature. Therefore, reducing the oxygen level in the flue gas will reduce the heat loss.
A general rule is that a 1 percent reduction in excess oxygen will reduce fuel usage by 1 percent.
Controlling excess air is the most important tool for managing the energy efficiency and atmospheric emissions of a boiler system.
It is important to keep in mind that the air-to-fuel ratio is based on mass, not volume. The mass of air supplied to the mass of fuel being used (e.g. on a kilogram-to-kilogram basis) must be controlled. The density of air and gaseous fuels changes with temperature and pressure, a fact that must be taken into account in controlling the air-to-fuel ratio. For example, if pressure is fixed, the mass of air flowing in a duct will decrease when the temperature increases. The controls should therefore compensate for seasonal temperature variations and, optimally, for day and night variations too (especially during the spring and fall, when daily temperature variations are substantial). As Figure 1 shows, the effect of air temperature on excess air in the flue gas can be dramatic.
Similarly, the mass of natural gas flowing through a pipe will fall if the pressure in the supply pipe drops. (This may happen when the fuel flow to a second boiler increases.) Constant flow of liquid fuels, although less influenced by temperature, still depends on steady supply pressure to a valve maintaining a constant position. If pressure increases (e.g. when a second pump is started), the oil flow for a given valve position will also increase.
Variations in pressure and temperature can be corrected by sophisticated air and fuel control systems. Such systems can be expensive, so simpler systems are often used to avoid the expense. They are less precise and are set up with larger margins of excess air to avoid insufficient air conditions. They cannot ensure optimum continuous operation. Due to the higher heat losses (i.e. lower energy efficiencies) associated with the cruder control systems, it pays to evaluate the economics of investing in a high-quality control system.
Figure 1. Effects of Air Temperature on Excess Air Level
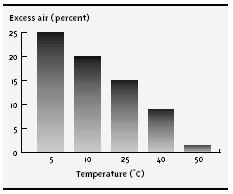
For existing combustion equipment, measuring and minimizing excess air is the primary way to optimize boiler and heater efficiency. Optimizing excess air (also referred to as O2 control) means adjusting burner airflow to match fuel flow. Burner settings, initially calibrated during burner commissioning, should be reviewed regularly. Carbon monoxide (CO) is a sensitive indicator of incomplete combustion; its levels should range from zero to, perhaps, 50 parts per million (ppm) by volume, rather than the usual environmental limit of 400 ppm. Each boiler house should have accurately calibrated analysers for measuring O2, CO and nitrogen oxides (NOx).
For ideas about upgrades, a brief description of the types of air and fuel controls follows, in order of sophistication and costs.
On-off and high-low controls
The use of on-off and high-low controls is limited to processes that can tolerate cycles of temperature and pressure, such as heating applications.
Mechanical jackshaft controls
The simplest type of modulating burner control is used in small burners, where the cost of more complex systems cannot be justified. These controls cannot measure airflow or fuel flow; the play in the jackshaft and linkages needs settings with higherthan- necessary excess air to ensure safe operation under all conditions. The range of oxygen control (oxygen trim) is limited. The control response must be very slow to ensure that the burner reaches a steady state before the oxygen trim acts.
Parallel controls
Separate drives in parallel controls adjust fuel flow and airflow, taking their signal from a master controller. The operator can adjust the flows individually and override the automatic control settings. These controls are usually applied to older, medium-sized boilers equipped with pneumatic controls. Their performance and operational safety can be improved by adding alarms that indicate if an actuator has slipped or calibration has been lost. Also, an additional controller can be added to provide oxygen trim. Parallel controls have similar disadvantages to mechanical jackshaft controls.
Cross-limiting control
Usually applied to larger boilers, cross-limiting control can sense and compensate for some of the factors that affect optimum air-to-fuel ratio. This control measures the flow of air and fuel and adjusts airflow to maintain the optimum value determined during calibration tests. Flue gas composition can be monitored and used in air control. Operations are safer when airflow cannot drop below the minimum needed for the existing fuel. They are also safer when fuel flow cannot be increased more than the existing airflow can burn. Oxygen trim is possible but, again, it has a limited range of adjustment. It must also respond slowly enough to allow the primary controls to reach equilibrium.
Automatic control of excess air (oxygen trim)
The high cost of purchasing and installing an oxygen analyser limits the use of oxygen trim controls to large boilers that use between $100,000 and $1 million worth of fuel annually. It increases energy efficiency by one to two percent. For very large boilers, where efficiency gains of 0.1 percent mean significant annual savings, these controls usually measure CO as well.
Page details
- Date modified: