Comparative Study of Refrigerations Systems for Ice Rinks - HTML Version
Download Full Document (PDF. 6.6 MB)
CanmetENERGY in Varennes
1615, Boulevard Lionel-Boulet, P.O. Box 4800
Varennes, Québec, J3X 1S6
Canada
Cat. : No.: M154-72/2013E-PDF
ISBN: 978-1-100-22499-2
Website: http://www.nrcan.gc.ca
This Publication is distributed for informational purposes only and does not necessarily reflect the views of the Government of Canada. Neither Canada, nor its ministers, officers, employees and agents make any warranty in respect to this publication nor assume any liability arising out of this publication.
©Her Majesty the Queen in Right of Canada, 2013
Preface
This techno-commercial study was conducted by Natural Resources Canada’s CanmetENERGY Research Centre with the technical and financial participation of the following organizations and companies:
- Ville de Montréal
- Ville de Québec
- Ministère de l’Éducation, du Loisir et du Sport du Québec (MELS)
- Ministère des Finances et de l’Économie du Québec (MFÉ)
- Hydro-Québec
- Association québécoise des arénas et des installations récréatives et sportives (AQAIRS)
- Fixair Inc.
- Cimco Refrigeration
- Carnot Refrigeration
- Kube Solutions
- Mayekawa Canada Inc.
- Smart Ref
- Trane
CanmetENERGY… AT A GLANCE
Mission
Natural Resources Canada’s CanmetENERGY is the Canadian leader in clean energy research and technology development. Three centres offer world-class expertise in energy research and are based in Devon (Alberta), Ottawa (Ontario) and Varennes (Quebec).
CanmetENERGY in Varennes, near Montreal, provides scientific and technical expertise in the following areas:
- Clean Energy Project Analysis: RETScreen International
- Smart Grid: to Enable the Integration of Renewable Energy
- Solar Photovoltaic Energy in Buildings
- Solar Photovoltaic Energy
- Industrial Systems Optimization
- Refrigeration
- Heat Pumps
- Recommissioning (RCx)
- Commissioning (Cx)
- Ongoing Commissioning (Cx)
Approximately 110 scientists, engineers, technologists, managers and support staff employees manage programs and provide science and technology (S&T) services. These resources work closely with members of the energy sector, academic and environmental protection partners through the use of cost-sharing agreements to carry out work done by experts at the Centre. In addition to acting as a window to federal financing, the Centre also obtains a large part of its financial support from the private sector and other public and institutional organizations.
Additional information about CanmetENERGY-Varennes is available at the following website:
http://www.nrcan.gc.ca/energy/offices-labs/canmet/14487
Expertise in Refrigeration
The field of refrigeration is managed by the Centre’s Buildings Department, which is comprised of about 30 researchers, technology experts, project leaders and managers as well as support staff. Their work in refrigeration is mainly focused on:
- Developing and promoting an integrated refrigeration approach to reduce energy consumption and GHG emissions
- Design and implementation support
- Developing and optimizing emerging refrigeration technologies
All the Centre resources who contributed to this study are part of the Buildings Department. Further information, reports and scientific tools can be accessed through the following link:
http://www.nrcan.gc.ca/energy/efficiency/buildings/research/refrigeration/3841 Source: CanmetENERGY Website
- BACKGROUND
- REFRIGERATION SYSTEMS
- INTRODUCTION
- METHODOLOGY
- REFERENCE BUILDING
- CHOICE OF SYSTEMS STUDIED
- PERFORMANCE ASSESSMENT
- FIRST COST ASSESSMENT
- ENERGY COST ASSESSMENT
- MAINTENANCE AND REPAIR COST ASSESSMENT
- TRAINING OF OPERATING PERSONNEL
- ASSESSMENT OF RESIDUAL VALUE AFTER 20 YEARS
- LIFE CYCLE
- INCENTIVES AND FINANCIAL CONTRIBUTIONS
- ASSESSMENT OF OWNING AND OPERATING COST OVER 20 YEARS
- EXCLUDED COST ITEMS
- SUMMARY TABLES OF RESULTS
- RISK ANALYSIS BASED ON REFRIGERANT TYPE
- ANALYSIS OF STUDY RESULTS
- POTENTIAL SUPPLIERS
- CONCLUSIONS
- STUDY CONTRIBUTORS
- APPENDICES
- APPENDIX 1: SCHEMATIC, DESCRIPTION AND OPERATION OF THE 12 SYSTEMS STUDIED
- APPENDIX 2: SUMMARY OF SYSTEM WARRANTIES
- APPENDIX 3: ENERGY CONSUMPTION RESULTS FOR AN ICE RINK OPERATING FOR 12 MONTHS
- APPENDIX 4: SUMMARY REPORT ON RISKS ASSOCIATED WITH THE USE OF AMMONIA IN ARENAS
- APPENDIX 5: TECHNICAL STUDY OF CO2 ARENA REFRIGERATION
- APPENDIX 6: RISK MANAGEMENT GUIDE FOR HALOCARBON ARENA REFRIGERATION SYSTEMS
LIST OF TABLES
- Table 1: Systems Identified as the 12 Options
- Table 2: Technical Features and Performance of the Refrigeration Systems under Study
- Table 3: Financial Data of Systems under Study
- Table 4: Main Refrigerants and Their Environmental Impacts
- Table 5: Laws and Regulations Pertaining to Refrigeration Systems for Ice Rinks
- Table 6: Main Features of the 12 Refrigeration Systems Studied
- Table 7: Maintenance Frequency and Equipment Replacement
- Table 8: Factors Used in Financial Calculations
- Table 9: Main Physical Characteristics of Equipment
- Table 10: Cooling and Heating Capacities
- Table 11: Installed Electrical Power
- Table 12: Energy Consumption of Refrigeration Systems
- Table 13: Energy Consumption of Heating Systems
- Table 14: Energy Balance and Power Demand
- Table 15: Average COP (Coefficients of Performance) in Cooling, Heating and Combined.
- Table 16: Initial Investments (Without Subsidies)
- Table 17: Energy Costs per Year
- Table 18: Maintenance and Repair Costs
- Table 19: Other Costs (Training, Refrigerant)
- Table 20: Subsidies and Incentives
- Table 21: Summary of Purchase and Maintenance Costs
- Table 22: Net Present Value and Annuity of Purchase and Operating Costs Over 20 Years.
- Table 23 : Summary of Financial Scenarios for Systems Under Study
- Table 24: Summary – PV of Residual Values
- Table 25: Main Suppliers of Refrigeration Systems for Ice Rinks
- Table 26: Organizations and Companies Offering Refrigeration Training
LIST OF FIGURES
EXECUTIVE SUMMARY
CanmetENERGY in Varennes conducted a study to respond to questions and concerns from ice rink owners and several public organisations regarding the deterioration and obsolete technology used in the majority of refrigeration systems currently operated in Quebec ice rinks. The study is also targeted towards equipment suppliers seeking insight on objective assessments of various options offered in the refrigeration field.
These assessments take into account a large number of technical, financial, environmental and security criteria. In addition to being funded almost entirely by the refrigeration sector, the study has given way to a vast sharing of information – in some cases confidential – with a significant number of participants.
More specifically, the study encompasses the following:
- Twelve typical refrigeration systems currently offered on the market.
- A performance evaluation of each system assuming it meets the performance requirements of a selected reference ice rink the reference ice rink is the Camillien-Houde Arena located in Montreal. This methodology permitted a precise comparison of energy costs and consumptions for a 9 month ice rink operation period.
- Financial analyses were performed over a period of twenty years and considering the following cost elements:
- System acquisition, taking into account the grants and incentives currently available
- Work costs related to the dismantling, upgrading of the mechanical room, if required, as well as, in certain cases, the safety equipment required by the laws and regulations in this regard
- Energy costs taking into account power demand, consumptions and current electricity rates
- Preventive and regular maintenance costs, including periodic supervision by stationary enginemen, when required
- Costs for equipment replacement, repairs or upgrades occurring over the 20-year period
- Specific initial and continuous refrigeration training for ice rink staff (i.e., manager, maintenance worker and refrigeration technician or stationary engineman)
Financial comparisons are made by calculating the present value (PV) of all costs and the corresponding annuity. Escalation rates and discount factors as well as interest rates were taken into account. A sensitivity analysis on the most uncertain escalation rates such as the price of energy has also been conducted.
A risk management analysis has also been conducted, which was outsourced to an expert, JP Lacoursière Inc., for each of the three refrigerant categories - ammonia, CO2reventative measures as well as mitigation measures in the event of an accident.
To assist ice rink owners in choosing the best refrigeration system possible, the study concludes with observations and comments made from CanmetENERGY experts based on the study results.
The summary tables of results are found below. Table 1 summarizes the choice of the 12 options identified, while Table 2 focuses on the performance of the 12 systems and Table 3 shows the financial results. The main findings and comments from experts are also included. More information on the technical characteristics of the refrigeration systems can be obtained in the body of the report.
# | Refrigerant | Rink Slab Fluid | Features | Example of realization with this concept |
---|---|---|---|---|
A1 | Ammonia R717 |
Brine | Open packaged system with stratified thermal storage | St-Ambroise Arena by Cimco (Eco Chill) |
A2 | Ammonia R717 |
Brine | Open system assembled with heat pump, Concept: City of Montreal |
Camilien-Houde Arena, City of Montreal |
A3 | Ammonia R717 |
Brine | Open system with integrated heat pump, Concept: Quebec City |
Bardy Arena, Quebec City |
A4 | Ammonia R717 |
Ethylene glycol | Open packaged system with economiser port on the compressors | Louiseville Arena by Fixair inc. |
A5 | Ammonia R717 |
Ethylene glycol | Open packaged system with efficient reciprocating compressors | Unidentified Arena with Mayekawa Compressors. |
C1 | CO2 R744 |
CO2 | Semi-hermetic split packaged system with direct evaporation in the rink slab | St-Gédéon-de-Beauce Arena by CSC/CIMCO |
C2 | CO2 R744 |
Brine | Semi-hermetic split-package with CO2 space heating | Dollard-des-Ormeaux Civic Centre by Carnot Refrigeration |
H1 | HFC – R22 | Brine | Traditional open system assembled with electric heating | Camillien-Houde Arena before being replaced by an ammonia system |
H2 | HFC – R507A | Brine | Packaged semi-hermetic system with economiser port on compressors | Olympia Arena in Longueuil by Fixair Inc. |
H3 | HFC– R410A | Methanol | Hermetic packaged heat pump system | Val-des-Monts Arena by The Kube Solutions (without ground source heat pumps) |
H4 | HFC – R507A | Ethylene glycol | Modular semi-hermetic system with stratified thermal buffer system | Lunenburg County lifestyle Complex by Cimco (Eco Chill) |
H5 | HFC – R134A | Brine | Packaged semi-hermetic system with heat pumps for water heating | Centre Meredith Arena in Chelsea by Trane |
System # | Identification | Main Technical features | Performance | |||||||||||||
---|---|---|---|---|---|---|---|---|---|---|---|---|---|---|---|---|
Assembly type | Refrigerant | Load (kg) | Compressors (Type1) | Evaporator (Type2) | Ext. Waste Heat Type3 |
COP | Energy Consumption (kWh/year) |
Variation | Maximum power (kW) |
GHG emissions4 (kg) |
||||||
Cooling annual |
Heating Annual |
Combined | Cooling | Heating | Total | %5 | ||||||||||
A1 | Packaged | R717 | 45 | OR | TPS-F | OCT | 2.4 | 7.6 | 3.2 | 407,000 | 77,100 | 484,100 | -11 | 180 | 1,000 | |
A2 | On site | R717 | 114 | OS | TP-F | CCCT | 2.5 | 3.7 | 2.9 | 383,400 | 159,000 | 542,400 | 0 | 198 | 1,100 | |
A3 | On site | R717 | 273 | OS | SSP-RF | CCCT | 2.2 | 3.2 | 2.5 | 453,600 | 183,600 | 637,200 | 17 | 210 | 1,300 | |
A4 | Packaged | R717 | 320 | OR | SSP-RF | OCT | 2.3 | 7.8 | 3.2 | 412,200 | 75,600 | 487,800 | -10 | 179 | 1,000 | |
A5 | Packaged | R717 | 230 | OS | SSP-RF | OCT | 2.1 | 21.5 | 3.3 | 446,400 | 27,400 | 473,800 | -13 | 171 | 900 | |
C1 | Split-packaged | R744 | 1591 | SHR | ST-RF | GC | 3.1 | 6.5 | 3.9 | 291,100 | 90,500 | 381,600 | -30 | 181 | 800 | |
C2 | Split-packaged | R744 | 500 | SHR | PS-DE | GC | 2.6 | 19.8 | 3.8 | 374,500 | 29,700 | 404,200 | -25 | 188 | 800 | |
H1 | On site | R22 | 409 | OS | TC-DE | AC | 1.8 | 1.3 | 1.6 | 550,200 | 469,300 | 1,019,500 | 88 | 381 | 76,100 | |
H2 | Packaged | R507A | 114 | SHS | TP-DE | DFC | 2.0 | 5.8 | 2.7 | 468,400 | 101,300 | 569,700 | 5 | 197 | 10,300 | |
H3 | Modular | R410A | 45 | HS | SSP-DE | DFC | 1.7 | 5.9 | 2.3 | 554,600 | 100,400 | 655,000 | 21 | 225 | 2,900 | |
H4 | Modular | R507a | 100 | SHS | SSP-DE | DFC | 2.0 | 3.8 | 2.5 | 485,500 | 153,000 | 638,500 | 18 | 192 | 9,300 | |
H5 | Packaged | R134A | 166 | VCSHS | ST-FF | DFC | 1.8 | 9.5 | 2.7 | 518,600 | 61,800 | 580,400 | 7 | 208 | 5,900 |
1 Compressor types | 2 Evaporator and evaporation types | 3 Waste heat equipment types | ||||
---|---|---|---|---|---|---|
OR | Open reciprocating | TPS-F | Titanium plate/shell | Flooded | OCT | Open cooling tower |
OS | Open screw | TP-F | Titanium plate | Flooded | CCCT | Closed circuit cooling tower |
SHR | Semi-hermetic reciprocating | SSP-RF | Stainless steel plate | Recirculating flooded | GC | Gas cooler |
SHS | Semi-hermetic screw | ST-RF | Slab tubing | Recirculating flooded | AC | Air condenser |
HS | Hermetic scroll | PS-DE | Plate/shell | Direct expansion | DFC | Dry fluid cooler |
VCSHS | Variable capacity semi-hermetic screw | TP-DE | Titanium plate | Direct expansion | ||
SSP-DE | Stainless steel plate | Direct expansion | ||||
ST-DE | Shell/tube | Direct expansion | ||||
ST-FF | Shell/tube | Falling film |
System # | Identification | Investments | Operating Costs3 | Overall Costs | |||||||||
---|---|---|---|---|---|---|---|---|---|---|---|---|---|
Assembly Type | Refrigerant | Purchasing Costs1 | Minus Funding2 |
Initial Net Investment | Energy | Yearly Maintenance | Periodic Maintenance + Repairs | Initial and Continuous Training | Current Value3 | Error with 95% Certainty5 | Annuity | Variations4 | |
($) | ($) | ($) | ($) | ($) | ($) | ($) | ($) | ($) | ($/year) | % | |||
A1 | Packaged | R717 | 912,000 | 596,300 | 315,700 | 930,400 | 307,400 | 45,800 | 32,100 | 1, 631,400 | ±170,000 | 109,700 | -44 |
A2 | On site | R717 | 2, 347,500 | 831,600 | 1, 515,900 | 1, 044,200 | 282,100 | 54,900 | 32,100 | 2, 929,600 | ±184,000 | 196,900 | 0 |
A3 | On site | R717 | 2, 177,000 | 817,400 | 1, 359,600 | 1, 160,200 | 267,600 | 63,500 | 32,100 | 2, 884,000 | ±199,000 | 193,800 | -2 |
A4 | Packaged | R717 | 909,800 | 594,700 | 315,100 | 933,800 | 265,800 | 63,200 | 32,100 | 1, 611,100 | ±168,000 | 108,300 | -45 |
A5 | Packaged | R717 | 949,400 | 616,600 | 332,800 | 888,300 | 278,800 | 52,600 | 32,100 | 1, 585,400 | ±162,000 | 106,600 | -46 |
C1 | Split-packaged | R744 | 1, 286,000 | 600,700 | 685,300 | 825,600 | 267,600 | 35,500 | 32,100 | 1, 850,500 | ±149,000 | 124,400 | -37 |
C2 | Split-packaged | R744 | 719,500 | 512,100 | 207,400 | 857,600 | 253,100 | 41,900 | 32,100 | 1, 392,800 | ±152,000 | 93,600 | -52 |
H1 | On site | R22 | 82,000 | 0 | 82,000 | 1,843,300 | 289,300 | 106,000 | 18,100 | 2,373,800 | ±305,000 | 159,600 | -19 |
H2 | Packaged | R507A | 751,900 | 102,600 | 649,300 | 1, 054,900 | 214,600 | 42,500 | 18,100 | 1, 980,100 | ±177,000 | 133,100 | -32 |
H3 | Modular | R410A | 399,300 | 98,000 | 301,300 | 1, 205,900 | 179,000 | 51,800 | 18,100 | 1, 756,400 | ±196,000 | 118,100 | -40 |
H4 | Modular | R507A | 682,000 | 88,300 | 593,700 | 1, 119,100 | 291,100 | 40,500 | 18,100 | 2, 063,200 | ±193,000 | 138,700 | -30 |
H5 | Packaged | R134A | 649,000 | 108,200 | 540,800 | 1, 111,200 | 90,400 | 40,400 | 18,100 | 1, 801,300 | ±174,000 | 121,100 | -38 |
Basis for Comparison:
- Purchasing costs including Class-T mechanical room for ammonia and the professional fees for 11 systems (no major work needed for # H1 (R22))
- Includes the total of contributions from MELS, Hydro-Québec and the BEIE (OPTER Program)
- PV: Present value calculated over 20 years
- Variation with respect to the basis for comparison – A2 (R717)
- The inflation rates used in calculating the Total Present Values are listed in table 8 with corresponding uncertainties. The possible errors on the Total Present Values have been calculated by applying at random the uncertainty values on the inflation rates. The calculation incorporates 500 random combinations of these uncertainties. The errors indicated incorporate 95% of these combinations
Main Findings of CanmetENERGY Refrigeration Experts
In reviewing the data presented in Tables 1 to 3, several system types offer similar cost and performance characteristics. The CO2 system identified as C1 emerges as being the most effective and the one identified C2, the least expensive. However, CO2 systems are still relatively unknown to ice rink owners due to their novelty in Quebec. These systems have been in operation for less than 10 years which makes it difficult to evaluate the life expectancy of the CO2 equipment. Furthermore, the large CO2 load when the piping circulates CO2 under the ice, could represent a risk for the occupants. This last aspect raises precautionary issues for the risk management expert involved in this study. Nonetheless, innovative owners and eager buyers are interested in these systems for the intrinsic qualities they offer in regards to their low environmental impact and refrigerant toxicity.
On the other hand, ammonia systems offer value in regards to long-term performance and reliability. In addition, the expertise of equipment manufacturers is a well-known and trusted source. Ammonia remains however a dangerous product and so to minimize the risk of accidents, strict security measures must be put in place, which can sometimes be costly. Considerable initial and recurring costs can be incurred due to the required supervision of permanent maintenance personnel and for the exhaust and containment equipment in case of ammonia leakage in the mechanical room.
HFCs are used in the majority of new air conditioning systems for residential, commercial and institutional buildings. They are also present in our everyday life such as in cars, refrigerators and heat pumps. However, HFCs are the subject of a debate on propositions wanting to reduce their production in the medium term, due to their negative impact on greenhouse effect. Refrigerant leakage into the atmosphere represents only 2% of all GHG emissions in comparison to 84% fromCO2, 9% from CH4 and 5% from N2O (Source : U.S. EPA. 2009. Inventory of U.S. Greenhouse Gas Emissions and Sinks: 1990-2007. EPA Report #430-R-09-004, U.S. Environmental Protection Agency).
Nevertheless, systems with HFCs are more favored compared to the innovative CO2 systems and the danger posed by the toxic products of ammonia systems. They offer low-cost solutions attractive when an owner’s investment capability is limited.
The last option to consider is maintaining the status quo (continue using R22). With many systems reaching the end of their life however, this option is not truly viable. Repair and replacement costs for obsolete equipment, energy costs as well as costs associated with refrigerants that will become increasingly rare as of 2015 are all factors making this the least favorable option available in addition to being a significant source of pollution and reliability concern for ice rink owners.
Ultimately, the final choice could depend on the following factors:
- The owner’s financial capacity.
- The emphasis placed on reducing environmental impacts.
- The willingness and ability to rigorously manage the risks that some options may present.
- The openness to technological innovation and confidence in respect to certain technological risks.
Once the main criteria are chosen, it will be possible to consider many options and select the one(s) which would be used to define tendering guidelines. Regardless of which options are chosen, the fact remains that caution should be used in all cases, including the status quo, to ensure the health and safety of occupants is met and ensured by conducting thorough risk analyses and implementing preventive measures and mitigation solutions to minimize hazards.
In the case of synthetic refrigerants, still associated with harmful greenhouse gas emissions, the goal of minimizing the refrigerant load in the systems and also minimizing the risk of leaks through reliable assembly is of great importance.
The current market offers enough options for ice rink owners to justify conducting analyses similar to the ones presented in this report. While these analyses may include fewer options, they will nonetheless identify a variety of solutions for making a performing, efficient and safe renovation while providing quality service for the next 20 to 30 years.
Study Objectives
The goal of this study is to better inform ice rink owners and managers on the choices available to them when planning to renovate or to replace a refrigeration system.
For this purpose, the study compares the performance as well as first costs and operating costs of a conventional refrigeration system using R22, to 11 other refrigeration systems currently offered on the market place which use ammonia, CO2 and HFCs without ODS (ozone-depleting substances).
Health and safety risks associated with each of these three refrigerant types are also analyzed and recommendations are presented to minimize and mitigate these hazards.
The proposed methodology in this study may also be used by professionals having to advise their clients on the type of refrigeration system that best meets their needs.
BACKGROUND
Current Condition of Refrigeration Systems
In the province of Quebec, there are approximately 425Footnote 1 ice rinks and 75 curling facilities. Of these, 71% are over 30 years old and 62% use the HCFC (hydrochlorofluorocarbon) type R22 refrigerant, an ozone-depleting substance. Ammonia, a natural refrigerant, is found in 30% of the facilities.
Ice rink refrigeration systems are currently evolving due to a large number of contextual factors:
- R22 refrigerant is being phased out due to the Montreal Protocol on Substances that Deplete the Ozone Layer.
- Most refrigeration systems are nearing the end of their useful life and require major renovations or replacement.
- New systems are much more efficient and incorporate energy efficiency measures that reduce energy costs and consumption by at least 40%.
- Innovative concepts are appearing on the market and are generating great interest from ice rink owners and managers.
- In March of 2012, Quebec’s Ministère de l’Éducation, du Loisir et du Sport implemented a $160 million financial aid program to help improve the state of refrigeration systems in ice rinks and curling facilities.
These combined factors stimulate the market while raising several questions from ice rink owners and managers:
- How do the various types of systems compare in terms of performance and cost?
- Are the new systems reliable?
- What about the safety aspect and the regulatory requirements?
In the fall of 2012, this study was therefore undertaken to address these questions.
ADDITIONAL INFORMATION ON ENERGY EFFICIENCY
Two major changes regarding heat recovery occurred during the last decade. The first one was the almost unanimous adoption and integration of heat recovery from the hot gas at the outlet of the compressors for preheating domestic hot water. The second change was the use of condensation heat to meet other ice rink heating loads using a secondary loop. The use of secondary loops has the added benefit of confining the refrigerant in mechanical rooms, thereby reducing the total refrigerant load in the system and, in the process, also reducing environmental impacts and risks associated with leaks.
In 1995, in Quebec, single and double ice rink arenas without heat recovery measures were still being built. At that time, innovative energy saving measures focused on installing low emissivity ceilings, using efficient lighting throughout the arena and installing a load shedding controller to optimize electrical peak demands. Few projects actually focused on the refrigeration system itself.
Here are some energy consumption data for old ice rinks:
- 1,525,000 kWh-equivalent of energy consumed on average per year and per ice rink (500 kWh/m2), twice as much as the average of other municipal buildings which amounts to 236 kWh/m2/year.
- 50% of the annual electricity consumption was for refrigeration.
- 30% was for space and water heating.
- Only 10% of the refrigeration system waste energy was being recovered.
- GHG emissions of the reference ice rink amounted to more than 145 tonnes of CO2 equivalent per year.
- The refrigeration system rejected three times the amount of energy required for heating needs.
The scope of engineering projects began expanding due to research findings, the dissemination of information and the introduction of various incentive programs, the first one being the PIRAQ (Refrigeration Action Plan for Quebec Arenas), managed by the AAQ (Association des arénas du Québec) now known as the AQAIRS (Association québécoise des arénas et des installations récréatives et sportives), together with other partners such as the Agence de l’efficacité énergétique, now known as the BEIE (Bureau de l’efficacité et de l’innovation énergétiques), and CEDRL (CANMET Energy Diversification Research Laboratory) now known as CanmetENERGY.
Other programs followed the PIRAQ:
- PARB, Programme d’action en réfrigération pour les bâtiments, CTEC Varennes (now the CanmetENERGY Research Centre in Varennes).
- OPTER Refrigeration Optimization Program – Arenas and Curling Rinks, Bureau de l’efficacité et de l'innovation énergétiques (BEIE).
- Incentive program – Energy Optimization for Buildings by Hydro-Québec, for the Commercial and Institutional Markets. The latter is now called the Buildings Program.
- Support Program for the Replacement or Modification of Refrigeration Systems using R-12 or R-22 in Quebec Ice Rinks and Curling Facilities, offered by the Ministère de l’Éducation, du Loisirs et du Sport du Québec (MELS).
The last three programs are still offered at the time of publication of this document.
Globally, these programs were acting on several fronts: technology transfer to engineering consultants and equipment manufacturers, innovative technology demonstration projects, training and financial incentives.
Since 2008, 68 financial assistance applications were filed and over 60 feasibility studies were conducted under the BEIE’s OPTER Program – Arenas and Curling Rinks Component. These projects represent the greater part of all major renovations that were carried out. The following figures show how the market for ice rink refrigeration equipment has evolved:
- 75% of these new projects selected ammonia as the refrigerant.
- 80% of ice rinks implemented an energy recovery system capable of recovering the equivalent of the total refrigeration system capacity (100 MBH of heat recovered for every 100 MBH of refrigeration?).
- 35% of ammonia systems use less than 1 kg of ammonia per tonne of refrigeration.
- 80% of facilities using synthetic refrigerants use less than 3 kg of refrigerant per tonne of refrigeration.
- 76% of all facilities use less than 3 kg of refrigerant per tonne of refrigeration.
This gradual market transformation has contributed to arenas consuming much less energy and being less costly to operate while drastically reducing their environmental footprint.
SUMMARY OF KEY ENVIRONMENTAL GUIDELINES
Several countries including Canada have set targets, established regulations and developed programs aimed at reducing the environmental impacts caused by the emissions of synthetic refrigerants into the atmosphere. Two negative effects are particularly targeted:
- The depletion of the ozone layer.
- The greenhouse effect.
The impacts of the main refrigerants are presented in Table 4 . Please note that due to the Montreal Protocol, the most harmful ozone-depleting refrigerants (i.e., CFC R11 and CFC R12) have been eliminated while the HCFC R22 and R123 are currently undergoing the elimination process. While a large number of synthetic refrigerants have little or no effect on the ozone layer they still contribute to global warming in a significant way, however. In fact, the GWP (global-warming potential), which measures the importance of the greenhouse effect, shows that synthetic refrigerants have indicators ranging from 1430 to 4000 compared to the CO2 index, which is 1. This emphasizes the considerable impact synthetic refrigerants have on the environment.
New international agreement projects are therefore in the process of being signed in order to achieve the medium-term goal of removing all synthetic refrigerants for the precise purpose of restricting greenhouse gas (GHG) emissions. In this respect, the agreements are aimed at gradually reducing the use of synthetic refrigerants as of 2016 until 2033, when production will be capped at 15% of the 2005-2008 average.
Refrigerant | Components | GWP(1) | ODP(2) |
---|---|---|---|
R-717 | Ammonia | 0 | 0 |
R-744 | Carbon dioxide (CO2) | 1 | 0 |
CFC-R11 | Pure | 3800 | 1.0 |
CFC-R12 | Pure | 8100 | 1.0 |
HCFC-R22 | Pure | 1810 | 0.055 |
HCFC-R123 | Pure | 76 | 0.012 |
HFC-R134A | Pure | 1430 | 0 |
HFC-R404A | R -125 /143A/134A | 3900 | 0 |
HFC-R407A | R-32/125/134A | 2100 | 0 |
HFC-R407c | R-32/125/134A | 1800 | 0 |
HFC-R410A | R-32/125 | 1725 | 0 |
HFC-R417A | R-125/134A/600 | 2300 | 0 |
HFC-R422A | R-125/134A/600A | 3100 | 0 |
HFC-R422d | R-125/134A/600A | 2700 | 0 |
HFC-R427A | R-32/125/143A/134A | 2100 | 0 |
HFC-R507a | R-125 /143A | 4000 | 0 |
Legend:
Bold font = frequently used in ice rinks
(1) GWP: Global-warming potential
(2) ODP: Ozone depletion potential
Source: ASHRAE Handbook Fundamentals 2009, Refrigerants
Under the influence of current government environmental guidelines, ice rink refrigeration system designers have embarked on a significant process aimed at transforming these systems in order to:
- Minimize the amount of system refrigerants, which in turn would reduce the negative impacts in case of leakage. Systems traditionally contained an average of 700 kg of refrigerant (9 kg/tonne) while more recent concepts use less than 3 kg/tonne of refrigerant.
- Improve system assembly methods to reduce leakage risks.
- Develop transition synthetic refrigerants with no significant impact on the environment Refrigerant manufacturers have developed HFOs with a GWP of 4. While the environmental impacts of these synthetic refrigerants are well known, their availability is limited and HFOs are still unused in ice rinks.
- Promote ammonia as a “green” permanent solution.
- Innovate by introducing CO2–based systems as an alternate permanent “green” solution.
SUMMARY OF ICE RINK REFRIGERATION REGULATIONS
Several national and international organizations have gotten involved with providing guidance on minimizing the environmental impacts of refrigerant leaks. Other organizations have also focused on the risks associated with these leaks with regards to human safety. Through the involvement of these organizations codes and regulations have been established. In Canada, the latter comes from various levels of government – federal, provincial as well municipal administrations. Table 5 shows the main regulations relating to ice rink refrigeration systems in Quebec. In the section on risk management associated with various refrigerants, these laws and regulations were taken into account in the recommendations made.
Identification | Authority | Targeted Refrigerants | Regulation Purpose | Notes |
---|---|---|---|---|
Regulation for Halocarbons |
Government of Quebec | All synthetic refrigerants | Recovery of refrigerants during equipment maintenance Workers qualification |
Decree 384-2007 |
B52-05 Code for Mechanical Refrigeration | CSA - ACNOR | All refrigerants including ammonia and CO2 | Minimum requirements for the design, construction, installation, inspection and maintenance of mechanical refrigeration systems | Minimizes the risks of injury to workers and the general public. Published in 2005. |
Canadian Environmental Protection Act, 1999 | Government of Canada | All refrigerants including ammonia and CO2 | Legislative framework for pollution prevention | |
Environmental Emergency Regulations of the Canadian Environmental Protection Act, 1999 | Government of Canada | All refrigerants considered to be hazardous substances | Requirements concerning the declaration of hazardous substances and the description of the relative contingency plan | |
Ozone-Depleting Substances Regulations, 1998 | Government of Canada | All ozone-depleting substances | Requirements for the manufacture, distribution and use of ODS for the purpose of phasing them out | Ban on the import and use of ODS as of 2030 |
CSST Refrigeration Systems Operating on Ammonia: Prevention Measures |
Government of Quebec | Ammonia | Prevention Guide for the handling and storing as well as protective and preventive measures for risks associated with the use of refrigeration systems | |
Civil Protection Act | Government of Quebec | All refrigerants | Protecting people and property against disasters | |
Pressure Vessels Regulations | Government of Quebec | All refrigerants | Manufacture, installation, repair and use of pressurized systems | |
Stationary Enginemen Regulations | Government of Quebec | All refrigerants | Determining how refrigeration systems are supervised | |
Workplace Health and Safety Regulations | Government of Quebec | All refrigerants | Preventive measures |
ENERGY EFFICIENCY AND HEAT RECOVERY
For several years, ice rink refrigeration units have undergone significant energy improvements both in terms of equipment performance and waste heat recovery, which was previously being rejected into the atmosphere.
Recovering and using the heat rejected alone can reduce energy consumption and costs by over 40 % and GHG emissions by 80% assuming the waste heat recovery replaces the fuels used for space heating and domestic hot water. The latter came from the use of fuels for heating water and the premises.
Figure 1 shows a conventional refrigeration system without heat recovery. The waste heat is rejected into the atmosphere.
while Figure 2 shows a newly developed system using waste heat to meet several heating needs in the ice rink. In this case, only the excess waste heat is rejected into the atmosphere.
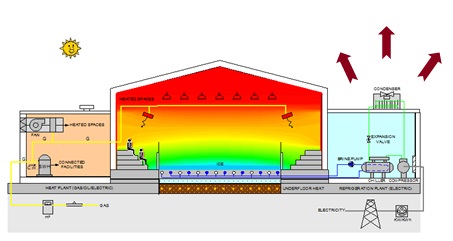
Figure 1: Traditional Ice Rink (Exterior Waste Heat Evacuation)
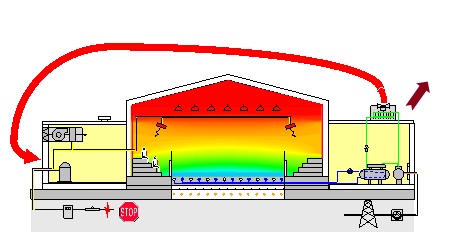
Figure 2: Contemporary Ice Rink (Waste Heat Reused and Remainder Released into the Atmosphere)
The most common uses for recovered heat are the following:
- Heating of the stands area, the players locker rooms and other spaces.
- Water heating for showers and ice surfacing.
- Snow melting (i.e. from the thin layer of ice removed during surfacing.
- Heating the slab under the ice to prevent soil from freezing.
Some concepts also offer heat storage in the form of hot water tanks or phase change materials to store the excess heat recovered which can be used as supplemental heat at a later period when the heat demand exceeds the amount of heat recovered from the refrigeration system.
Given the impact they have on operating costs and GHG emissions, energy efficiency and heat recovery are essential in new facilities or when renovating or replacing existing systems.
ADDITIONAL INFORMATION ON ENERGY EFFICIENCY
Two major changes regarding heat recovery occurred during the last decade. The first one was the almost unanimous adoption and integration of heat recovery from the hot gas at the outlet of the compressors for preheating domestic hot water. The second change was the use of condensation heat to meet other ice rink heating loads using a secondary loop. The use of secondary loops has the added benefit of confining the refrigerant in mechanical rooms, thereby reducing the total refrigerant load in the system and, in the process, also reducing environmental impacts and risks associated with leaks.
In 1995, in Quebec, single and double ice rink arenas without heat recovery measures were still being built. At that time, innovative energy saving measures focused on installing low emissivity ceilings, using efficient lighting throughout the arena and installing a load shedding controller to optimize electrical peak demands. Few projects actually focused on the refrigeration system itself.
Here are some energy consumption data for old ice rinks:
- 1,525,000 kWh-equivalent of energy consumed on average per year and per ice rink (500 kWh/m2), twice as much as the average of other municipal buildings which amounts to 236 kWh/m2/year.
- 50% of the annual electricity consumption was for refrigeration.
- 30% was for space and water heating.
- Only 10% of the refrigeration system waste energy was being recovered.
- GHG emissions of the reference ice rink amounted to more than 145 tonnes of CO2 equivalent per year.
- The refrigeration system rejected three times the amount of energy required for heating needs.
The scope of engineering projects began expanding due to research findings, the dissemination of information and the introduction of various incentive programs, the first one being the PIRAQ (Refrigeration Action Plan for Quebec Arenas), managed by the AAQ (Association des arénas du Québec) now known as the AQAIRS (Association québécoise des arénas et des installations récréatives et sportives), together with other partners such as the Agence de l’efficacité énergétique, now known as the BEIE (Bureau de l’efficacité et de l’innovation énergétiques), and CEDRL (CANMET Energy Diversification Research Laboratory) now known as CanmetENERGY.
Other programs followed the PIRAQ:
- PARB, Programme d’action en réfrigération pour les bâtiments, CTEC Varennes (now the CanmetENERGY Research Centre in Varennes).
- OPTER Refrigeration Optimization Program – Arenas and Curling Rinks, Bureau de l’efficacité et de l'innovation énergétiques (BEIE).
- Incentive program – Energy Optimization for Buildings by Hydro-Québec, for the Commercial and Institutional Markets. The latter is now called the Buildings Program.
- Support Program for the Replacement or Modification of Refrigeration Systems using R-12 or R-22 in Quebec Ice Rinks and Curling Facilities, offered by the Ministère de l’Éducation, du Loisirs et du Sport du Québec (MELS).
The last three programs are still offered at the time of publication of this document.
Globally, these programs were acting on several fronts: technology transfer to engineering consultants and equipment manufacturers, innovative technology demonstration projects, training and financial incentives.
Since 2008, 68 financial assistance applications were filed and over 60 feasibility studies were conducted under the BEIE’s OPTER Program – Arenas and Curling Rinks Component. These projects represent the greater part of all major renovations that were carried out. The following figures show how the market for ice rink refrigeration equipment has evolved:
- 75% of these new projects selected ammonia as the refrigerant.
- 80% of ice rinks implemented an energy recovery system capable of recovering the equivalent of the total refrigeration system capacity (100 MBH of heat recovered for every 100 MBH of refrigeration?).
- 35% of ammonia systems use less than 1 kg of ammonia per tonne of refrigeration.
- 80% of facilities using synthetic refrigerants use less than 3 kg of refrigerant per tonne of refrigeration.
- 76% of all facilities use less than 3 kg of refrigerant per tonne of refrigeration.
This gradual market transformation has contributed to arenas consuming much less energy and being less costly to operate while drastically reducing their environmental footprint.
TECHNOLOGICAL PROGRESS AND INVENTORY OF CURRENT OPTIONS
In addition to the energy improvements previously described, ice rink refrigeration systems are not immune to technological innovations. Always under the influence of environmental guidelines and the almost constant increase in energy prices, equipment manufacturers have never ceased innovating and offering ice rink owners and managers the findings of their research.
The most significant innovations of recent years are:
- The advent of CO2 refrigeration systems operating in transcritical mode (compressed gas refrigerant cooled at high pressure – over 7 MPa (± 1,000 lbs/inch²)).
- CO2 refrigerant circulation and vaporization directly in the slab piping network.
- Completely pre-assembled refrigeration systems operating with ammonia or HFC and ready to be placed in a mechanical room; some even include thermal storage.
- The forthcoming arrival of HFO type refrigerants that will minimize the greenhouse effect. Designed primarily for automobile air conditioners, these refrigerants could be mixed with HFCs to work with ice rink refrigeration systems. Their GWP index would then be set at a maximum level of 150.
REFRIGERATION SYSTEMS
INTRODUCTION
A large number of technical and financial data were used to produce the results provided in this report. In order to simplify the analysis of these results, they have been compiled herein with the use of summary tables. For a more in-depth understanding of specific results or to obtain further details, corresponding appendices listed at the bottom of the tables serve as references.
In addition to calling on an experienced team of experts at CanmetENERGY, a large number of stakeholders, equipment manufacturers, ice rink owners, refrigeration specialists and trainers were consulted throughout the development of this project in order to ensure the greatest objectivity possible. Also contributing to the results were data collected on actual buildings, simulations and validations with real data.
METHODOLOGY
The methodology used to obtain or to determine the components of this study can be summarized as follows:
REFERENCE BUILDING
All systems studied were analyzed as though they were installed and operated in the same building. The arena selected was the Camillien-Houde Arena, owned by the city of Montreal. This ice rink was chosen as the reference building because it is considered a typical hockey ice rinks found in Quebec as well as the arenas proximity to the surrounding residential buildings made it an ideal candidate for risk analyses.
The main characteristics of the ice rink are the following:
- Only one ice rink
- In use 9 months per year (including start-up and shutdown periods)
- Total building area: 3,733.4 m² (40,171 ft²)
- Number of seats in the stands: 300 – 500
- Operating hours: 6:00 a.m. to 12:00 midnight
- Ceiling emissivity index: 0.85
- Relative humidity over ice: 50%
- Lighting power above ice rink: 18 W/m²
- Temperature in the stands area: 15°C (60°F)
- Ice rink temperature: -6°C (21°F)
- Refrigeration systems: R22 – six 30 HP compressors
- Secondary loop: Brine with 25 HP circulating pump. Two pass network
- Heat recovery: Desuperheater for heating water for showers and ice surfacing
- Slab is in good condition
CHOICE OF SYSTEMS STUDIED
The choice was made by CanmetENERGY experts based on their knowledge of the market and their continuous observations of the evolving refrigeration technologies in Canada and abroad. Each system was subsequently discussed and validated with the organizations and businesses participating in the study. The system schematics reflect those currently offered by equipment manufacturers in the Canadian market. Table 6 summarizes the choice of the 12 options selected. Please note that #A2 using ammonia-based refrigerant will serve as a basis of comparison for the other 11 systems studied.
# | Refrigerant | Rink Slab Fluid | Features | Example of realization with this concept |
---|---|---|---|---|
A1 | Ammonia` R717 |
Brine | Open packaged system with stratified thermal storage | St-Ambroise Arena by Cimco (Eco Chill) |
A2 | Ammonia R717 |
Brine | Open system assembled with heat pump, Concept: City of Montreal |
Camilien-Houde Arena, City of Montreal |
A3 | Ammonia R717 |
Brine | Open system with integrated heat pump, Concept: Quebec City |
Bardy Arena, Quebec City |
A4 | Ammonia R717 |
Ethylene glycol | Open packaged system with economiser port on the compressors | Louiseville Arena by Fixair inc. |
A5 | Ammonia R717 |
Ethylene glycol | Open packaged system with efficient reciprocating compressors | Unidentified Arena with Mayekawa Compressors. |
C1 | CO2 R744 |
CO2 | Semi-hermetic split packaged system with direct evaporation in the rink slab | St-Gédéon-de-Beauce Arena by CSC/CIMCO |
C2 | CO2 R744 |
Brine | Semi-hermetic split-package with CO2 space heating | Dollard-des-Ormeaux Civic Centre by Carnot Refrigeration |
H1 | HCFC – R22 | Brine | Traditional open system assembled with electric heating | Camillien-Houde Arena before being replaced by an ammonia system |
H2 | HFC – R507A | Brine | Packaged semi-hermetic system with economiser port on compressors | Olympia Arena in Longueuil by Fixair Inc. |
H3 | HFC– R410A | Methanol | Hermetic packaged heat pump system | Val-des-Monts Arena by The Kube Solutions (without ground source heat pumps) |
H4 | HFC – R507A | Ethylene glycol | Modular semi-hermetic system with stratified thermal buffer system | Lunenburg County lifestyle Complex by Cimco (Eco Chill) |
H5 | HFC – R134A | Brine | Packaged semi-hermetic system with heat pumps for water heating | Centre Meredith Arena in Chelsea by Trane |
Legend:
A2 = Basis for comparison
PERFORMANCE ASSESSMENT
All systems studied were subject to an energy simulation based on actual equipment performance. This simulation took into account hour-by-hour equipment power, operating hours, outdoor temperature and heat recovery requirements.
Recognized calculation software was used for this purpose.
These technical characteristics were then imported into an Excel VBA spreadsheet to establish monthly and annual energy consumption.
The COP (coefficient of performance) was also calculated for each system type.
Coefficients of Performance
The coefficient of performance (COP) is an indicator derived from the useful energy ratio obtained (or the service rendered), divided by the energy consumed. For example, the COP of a refrigeration compressor is defined as the cooling capacity produced divided by the electrical power required by the compressor. If a compressor consumes 100 kWh of electricity to produce 300 kWh of cooling capacity then its COP will be 300/100 = 3.0. A compressor’s refrigeration COP is typically greater than 1.
The refrigeration systems analyzed in this study include many components that consume energy, such as pumps, cooling towers, heat pumps, etc. To facilitate the analysis and the performance comparison of energy systems studied in this report, three new system COPs have been defined. A COP for the refrigeration, a COP for heating as well as a combined COP. All are defined below.
Average COP of a Refrigeration System
The average COP of a refrigeration system is defined by the cooling energy produced during the operating season divided by the amounts of energy spent to operate the refrigeration system, namely the:
- Energy consumed by the compressor
- Energy consumed by the cooling towers, condensers, cooling gas or fluid
- Energy consumed by secondary fluid pumps (brine, glycol or other)
- Energy consumed by the auxiliary cooling system for CO2 systems

Text Version
Equation 1
COP refrigeration equals E cooling divided by (E compressor plus E water tower divided by condenser plus E pumps plus E aux cooling)
The higher the value, the more the refrigeration system is economical (i.e., able to produce cooling power at a lower cost).
Average COP for Heating
The COP for heating is defined as the heating energy produced during an operating season (air heating plus water heating) divided by the amounts of energy spent for heating:
- Heat pumps for air heating
- Heat pumps for water heating
- Secondary fluid pumps
- Auxiliary air heating
- Auxiliary water heating

Text Version
Equation 2
COP heating equals E water heating plus E air heating divided by (E heat pumps plus E pumps plus E aux heating)
The higher this value, the more the heating and energy recovery system is economical. The COP of an electrical heating system is equal to 1, while the heating COPs calculated with the proposed formula are greatly larger than 1 when the energy comes from the heat recovery of the refrigeration systems. Some systems show heating COP values greater than 4, meaning that these systems consume four times less energy than an electrical heating system.
Combined COP
In the case of the overall COP, useful energy is defined as the cooling energy produced + the heating energy produced. A refrigeration system might have a very high refrigeration COP and a very low heating COP if heat recovery is not present. Taking into account a system that must provide both cooling and heating, the two services rendered must be considered. The overall COP is thus defined as follows:

Text Version
Equation 3
COP combined equals E cooling plus E water heating plus E air heating divided by (E compressor plus E water tower / condenser plus E pumps plus E aux cooling plus E heat pumps plus E pumps plus E aux heating)
In a refrigeration system with energy recovery, this is the value that must be maximized. This COP takes into account both cooling and heating performance. The overall COP represents an easy method of comparing the energy performance of complex systems.
FIRST COST ASSESSMENT
The investments required to replace a refrigeration system were obtained from equipment manufacturers considering the technical features identified and the presented system schematics. All systems are considered as being implemented in the reference building. The submitted costs were subsequently validated with the help of ice rink managers and of available data from the Refrigeration Optimization Program (OPTER). Cost elements include the:
- Refrigeration system with all its components in original and unused condition.
- Components of the heat recovery system considering heating of the arena and of domestic hot water for showers and ice surfacing.
- Safety components recommended in the risk management reports conducted by JP Lacoursière Inc.
- Dismantling and removal of old equipment.
- Adjustment or expansion of the mechanical room (when applicable) as required by codes and regulations, in particular code B52. Class-T mechanical rooms are planned for ammonia systems (see the insert detailing the main characteristics of a Class-T room).
- Installation and commissioning: control system, on-site monitoring and coordination, equipment electrical power connections to the breakers and control panel in the technical room. Transportation, tool rental, structures and supports for the equipment, piping, valves and insulation, identification, refrigeration refilling and hydronic balancing.
- Professional fees for the study, design and supervision of the work, assumed at 10% of the acquisition costs before funding.
- Costs of risk analysis for systems using ammonia or CO2.
- Applicable taxes are not included.
Important Notice: In the case of the reference system H1 using HFCF-R22, the replacement of obsolete equipment parts (i.e., two of the six compressors, air condensers, circulation pump motor and evaporator re-tubing) was considered as the initial investment for system restoration.
MAIN CHARACTERISTICS OF A CLASS-T ROOM
As required by Code B52 of the CSA (Canadian Standards Association), a mechanical room with an ammonia refrigeration system must comply with Class-T requirements which include:
- A room sealed off from indoor air and constantly ventilated with outside air.
- Ventilation control outside of the room.
- Controlled access to the room.
- A door giving direct access to the exterior of the building.
- A vestibule with a fireproof door giving access to the room.
- Masks and/or personal respirators available in case of major leaks.
- Written emergency procedures.
- Staff exercises and training.
- An ammonia detector coupled with an alarm system that sets off the emergency ventilation system to exhaust accumulated ammonia vapours to the outside.
- An alarm to alert maintenance staff and firefighters.
- No combustion equipment in the room.
ENERGY COST ASSESSMENT
Energy costs are calculated for the refrigeration systems and the heat recovery units used for heating the arena and the hot water used for showers and ice surfacing. Lighting and other energy needs are not considered in this study.
Costs were established considering electricity was the only energy source for all cooling and heating energy demands (for space and water) even when additional heating is required for certain uses such as heating of surfacing water.
Electricity cost calculations were made using Hydro-Québec’s rate M (2013); the latter takes into account the monthly power rate of $13.71/kW and the consumption rate of 0.0449$/kWh. The rule establishing the minimum billing demand was taken into account, meaning that it cannot be less than 65% of the maximum power demand during the winter months (December 1 to March 31). The power factor is considered to be greater than 90% at all times.
MAINTENANCE AND REPAIR COST ASSESSMENT
Maintenance and repair costs were subdivided as follows:
External Preventive Maintenance
This includes all maintenance work that must be performed every year on the refrigeration system. Usually, this involves 3 to 4 visits per year to get the system ready for operation and for routine inspection of the operating data and performing oil changes and system shutdown at the end of the season. The cost was determined using service contracts of specialized companies and confirmed by the municipalities.
Routine Maintenance and Inspections
Regular inspection tours, when required, the chemical treatment of evaporative condensers/exchangers or cooling towers, valves and other equipment needing to be replaced every year are considered as regular maintenance. The associated costs were obtained by consulting individuals with knowledge in the field.
Average annual expenditures equal to 2% of the capital cost were planned for this purpose. This expense includes the salaries of internal staff and minor variable costs throughout the years such as staff intervention (i.e., settings, review, controls, checking operation and equipment condition, addition of refrigerants, etc.) and parts replacement and minor costs necessary to maintaining the system in good operating condition. Service calls are also included in this annual budget.
Periodic supervision
For ammonia systems, as required by the Stationary Enginemen Regulation, periodic supervision (defined as one-hour per day minimum) is included in the costs, with several options:
- Costs for Stationary Enginemen when they are municipal employees, dependant on the time devoted to this task and the usual salary, plus fringe benefits.
- When entrusted to an outsourcing company, the average value of contracts for supervision services provided by stationary enginemen or specialized technicians.
Some variants are proposed in this study to reflect the practices put in place by the municipalities. In certain municipalities, even if regulations require only periodic supervision (minimum of a one-hour inspection daily), these visits can take up to 3 hours per day depending on the inspection program implemented by the municipality.
A normalized cost of $16,000/year was established following numerous consultations. The financial impact of this cost item over the 20 year period of the financial analysis is presented in Tables 23 and 24.
Maintenance and Regular Repairs
Routine maintenance and repairs include compressors rebuilding at the frequency indicated in the detailed maintenance cost tables. This maintenance takes into account the type of equipment used. The cleaning of exchangers and the replacement of seals, when applicable, are also discussed. The replacement of circulating pump motors is also included. When the equipment has a useful life of less than 20 years, replacement costs are provided and a residual value is taken into account, if appropriate. Costs were calculated as above for regular maintenance in consultation with ice rink equipment suppliers and managers.
TRAINING OF OPERATING PERSONNEL
To be operated properly and in a safe manner, ammonia and CO2 systems require specialized training. Systems using HFCs are already well known and require little retraining.
While teaching institutions offer training for ammonia systems, no institution yet offers training for CO2 systems. For this case, equipment manufacturers provide training to operating personnel. The following training costs are considered in the study:
For ammonia systems:
- One-day training for ice rink managers, two-day training for maintenance workers and five-day training for stationary enginemen or refrigeration specialists.
- Training is considered to be delivered on site.
- Training costs include only registration fees .
- When training is held in educational institutions, the trainee’s salary must be added as well as a budget for expenses.
- Continuous training every 2 years is taken into account (registration fees only).
For CO2 systems:
- Same training approach for CO2 systems as for ammonia
- Cost for initial training offered by equipment manufacturers was established at the same amount as the one for ammonia systems
- Continuous training every 2 years is also taken into account
ASSESSMENT OF RESIDUAL VALUE AFTER 20 YEARS
The study considers the fact that some components will need to be replaced before the 20-year time frame while others have a life expectation greater than 20 years. When equipment requires replacement within a 20-year term, the replacement costs are taken into account in the year in which the replacement is needed. If applicable, a residual value for this equipment is taken into account at the 20th year. Equipment with a life expectancy greater than 20 years are also assigned a residual value at the 20th year. In all cases, residual values are calculated based on the acquisition cost and in proportion to the number of years of life expectancy beyond the 20-year term. Residual values are then discounted and subtracted from the total cost balance sheet.
THE RESIDUAL VALUE
The residual value refers to «the value of an asset at the end of the economic term (or period of analysis)». This value is determined with regards to the initial cost of the asset and the amortization method chosen.
Amortization can be linear, increasing or decreasing with time. Without justification for a better option, a linear amortization is generally chosen. This is the option retained in this study. Linear amortization is calculated in the following way.
Value of a linear amortization ($/year) = Initial cost in $
Life expectancy in years
Residual value in $ = Value of amortization ($/year) x number of years of life remaining beyond the term of the analysis
The more costly was the equipment initially or the longer its life expectancy, the higher will be its residual value at the end of the term of the economic analysis.
Example calculation: a new refrigeration system requires an initial investment of $600,000 and offers a life expectancy of 30 years. What is the residual value of this investment at the end of a 20 year term life cycle study?
Linear amortization = $600,000/30 years = $20,000/year
At the end of the 20 year term of the life cycle study, the system will still have 10 years of life expectancy
Residual value at the 20th year = 10 years x $20,000/year = $200,000
Important note: Amortization values are applied to investments for refrigeration equipment and systems. On the other hand, they are not applied to investments for buildings such as a Class T mechanical room. These investments remain stable in value or even increase in time. In this study, the value of the initial cost remains constant i.e. there is no amortization.
Residual values are discounted to convert them into present values (PV). This takes into account the time delay between today and the year of disbursement: the longer the period, the lower the present value, the latter depending on the discount rate.
The residual value of refrigeration equipment is also discounted. On the other hand, it is zero if the life expectancy of the asset is equal to the period of the life cycle study.
Example calculation: considering the residual value calculated in the previous example i.e. $200,000, what would be the present value (PV) of this asset. The discount rate is 3%/year. (No Answer Provided?).
LIFE CYCLE
In this study, the definition of equipment life cycle is the same as the one found in the ASHRAE Handbook – HVAC Applications 2011, Owning and Operating Costs, Chapter 37. The median life cycle is defined as the longest period of time where 50% or more of the equipment or systems have survived. For example, if 50% or more of refrigeration equipment put in service 25 years ago are still in operation today, their life cycle will be considered at least 25 years.
Consequently, replacing a compressor on a refrigeration system does not determine the system’s life cycle, but rather only that of the compressor. The complete replacement of a refrigeration system is what determines its life cycle. There could be various reasons for replacing a system:
- Faulty and non-operational equipment.
- Spare parts no longer being available.
- Obsolete technology.
- Unacceptable reliability.
- Excessive maintenance costs.
- Significant changes in the facility (major expansion, addition of an ice rink, etc.).
Equipment life cycle is a determining factor in calculating the overall cost. The life cycle affects routine maintenance costs and the residual value of the equipment after 20 years of operation.
Routine maintenance costs can include, for instance:
- Maintenance of open type compressors after a few thousand hours of operation.
- Replacing semi-hermetic type compressors after several years of operation.
- Cleaning and replacing seals on plate heat exchangers.
- Replacing circulating pump motors.
- Replacing fluid cooler fan motors.
- Re-tubing of shell and tube exchangers.
The overall cost is calculated while taking into account the depreciation of the equipment on a 20-year period. The residual value is calculated in proportion to the number of years remaining after the 20-year life cycle period (i.e. an open type compressor with an estimated 30-year life cycle would have a residual value equal to 10/30 of its original purchase cost).
For the purpose of this study, life cycles were estimated at:
- Ammonia refrigeration systems, 30 years.
- CO2 refrigeration systems, 25 years.
- HFC refrigeration systems, 20 years.
At least 50% of HFC refrigeration systems are still in use after 20 years of operation, even if these devices use semi-hermetic compressors that must be replaced instead of services as well as copper piping with brazed joints. All HFC systems included in this study were factory assembled. Statistical data exist and can be consulted on the ASHRAE Web site.
Ammonia refrigeration systems are often referred to as being “industrial” since they have been used in industry for over a century. They contain open type compressors that can be maintained to prolong their life cycle for several decades. Their highly efficient compressor motors are specifically chosen for this purpose and offer better performance and flexibility considering that they can be replaced without impacting the compressor. Ammonia system components are connected by welded steel piping. The 30-year life cycle used in this study is inferior to what most equipment manufacturers consider it to be; this restriction is mostly due to the technology being considered obsolete at the end of the life cycle period. After a term of 30 years, an overall cost assessment would show it beneficial to replace existing equipment by more efficient options that are less expensive to maintain and that comply with requirements that are most likely to be different than those of today.
CO2 refrigeration systems have been widely used in more than a thousand facilities in Europe for over ten years. In Quebec, during the past four or five years, local equipment manufacturers have installed a few dozen CO2-based systems in supermarkets, ice rinks and refrigerated warehouses. At this time, Quebec remains the North American leader in transcritical CO2 refrigeration systems.
CO2 refrigeration systems use:
- Semi-hermetic type compressors.
- Brazed plate heat exchangers.
- Welded shell and plate exchangers.
- Air coils with stainless steel pipes for heat recovery.
- Welded stainless steel piping.
Semi-hermetic compressors cannot be maintained on site such as open type compressors and so they must therefore be replaced when defective. Exchangers do not have joints with seals that need replacing. The quality of the solder joints in the piping linking the CO2 refrigeration system components is comparable to that of ammonia-based refrigeration systems. In this respect, CO2 refrigeration systems offer a quality of assembly comparable to that of ammonia systems, and one that is also highly superior to HFC systems with copper piping and solder joints. That is why this system was assigned an intermediate life cycle of 25 years.
Table 7summarizes the frequency of equipment maintenance, repair and/or maintenance and replacement that was used to calculate operating costs for routine repairs. In the following table, the replacement frequency cannot exceed the life cycle of the overall equipment. For example, the titanium shell and plate evaporator of Item #13 displays a replacement frequency of 30 years, even if the equipment life cycle could be much higher. This explains why the evaporator’s residual value after 20 years is equivalent to 10/30 of its original cost.
# | Equipment | Type | R | Frequency of Restoration and/or Maintenance | Replacement Frequency | Comments |
---|---|---|---|---|---|---|
1 | Compressors | Open screw | 717 | 12 years | 30 years | Maintenance for compressor head |
2 | Compressors | Open reciprocating | 717 | 5 years | 30 years | Maintenance for compressor head |
3 | Compressors | Semi-hermetic reciprocating | 744 | 7 years | Replacement of faulty compressor | |
4 | Compressors | Open reciprocating | 22 | 7 years | Replacement of faulty compressor (if no maintenance) | |
5 | Compressors | Semi-hermetic screw | 507A | 10 years | Replacement of faulty compressor | |
6 | Compressors | Hermetic scroll | 410A | 3 years | Replacement of faulty compressor | |
7 | Compressors | Variable capacity semi-hermetic screw | 134A | 10 years | Replacement of faulty compressor | |
8 | Interior Condenser | Plate exchanger | 717 | 5 years | 30 years | Dismantling, cleaning, inspection, replacement of sealing joints, etc. |
9 | Exterior Condenser | Induced draft, counter-flow open cooling tower | 717 | Annually | 20 years | Maintenance and chemical products |
10 | Exterior Condenser | Forced draft, counter-flow closed circuit cooling tower | 717 | Annually | 20 years | Maintenance and chemical products |
11 | Exterior Condenser | Air gas cooler (similar to dry condenser) |
744 | Annually | 20 years | Replacement of faulty fan motors |
12 | Exterior Condenser | Dry fluid cooler | 507A, 410A | Annually | 20 years | Replacement of faulty fan motors |
13 | Evaporator | Titanium shell and plate, flooded | 717 | 30 years | Light brine maintenance (included in annuity) | |
14 | Evaporator | Titanium plate, flooded | 717 | 5 years | 30 years | Dismantling, cleaning, inspection, replacement of sealing joints, etc. |
15 | Evaporator | Stainless steel plate, flooded | 717 | 5 years | 30 years | Dismantling, cleaning, inspection, replacement of sealing joints, etc. |
16 | Evaporator | Stainless steel shell and plate, direct expansion | 744 | Not required | 25 years | Light brine maintenance (included in annuity) |
17 | Evaporator | Steel shell and tube, direct expansion | 22 | 12 years | 20 years | Complete re-tubing |
18 | Evaporator | Titanium or stainless steel plate, direct expansion | 507A | 5 years | 20 years | Dismantling, cleaning, inspection, replacement of sealing joints, etc. |
19 | Evaporator | Steel shell and tube, falling film | 134A | 12 years | 20 years | Complete re-tubing |
20 | Pump | Circulating pump for cooling or heating fluid | - | 5 years | Replacement of motor and inspection of mechanical seal |
INCENTIVES AND FINANCIAL CONTRIBUTIONS
The financial support
Incentives and financial contributions have been calculated considering the various Programs available in spring 2013.
Hydro-Québec
Hydro-Québec’s Building program offers financial incentives for the implementation of energy efficiency measures in the commercial and institutional sectors. Incentives are for electrical energy savings. The amount of the incentive varies according to the complexity of the project submitted. In the present case, the incentive has been calculated using the difference of energy consumption between the system with R22 and every other replacement systems. The assumption is based on $0.15 per kWh saved. This number was set after consultation with Hydro-Québec. The incentive program is under review and the numbers shown are indicative only.
Financial support by MELS
The program developed by Québec’s Ministère de l’éducation, du loisir et du Sport (MELS) has the objective of fighting climate change. It offers financial support for the replacement or the modification of refrigeration systems using specifically R12 or R22 in ice rinks and curlingrinks. The maximum amount of support offered under option 1 of the program for the acquisition of a refrigeration system is 50% of permissible costs with a maximum incentive of $700,000 (this being for a single rink). Only refrigerants ammonia and CO2 are allowed under this program. No financial support is offered for HFC’s. The cost for building a Class T mechanical room for ammonia systems is an permissible cost item in option 1. The cost for rebuilding a rink slab or installing an over-slab is not allowed if the original slab is in good order and does not need necessary work to insure the health and safety of the users or the integrity of the building.
Financial support by BEIE
The Program for the optimization of refrigeration systems (OPTER) section for ice rinks and curling clubs of the Bureau de l’efficacité et de l’innovation énergétique du Québec offers financial support to owners of facilities whowish to improve their refrigeration system. The financial support is proportional to the amount of reduction of GHG emissions that the new system can provide. The contribution is 50% of the permissible costs with a maximum incentive of $60,000 (this being for a single rink). The amount of contribution indicated in this study has been calculated using an estimation tool available on the BEIE Web site.
The potential incentive for each rink in this study was calculated using the financial estimation tool available on the BEIE web site. It should be noted that this program is currently under review and the numbers shown are indicative only.
ASSESSMENT OF OWNING AND OPERATING COST OVER 20 YEARS
The initial investment cost for a new system is assumed to be entirely spent at year 0. All other costs arising in subsequent years are discounted to present values (PV) to provide an aggregated purchase and operating cost over a 20 years term. The factors listed in Table 8 are used for the purpose of this calculation.
Inflation rates | Uncertainty | |
---|---|---|
Loan Interest Rate | 3%/year | ± 1% |
Discount Rate | 3%/year | ± 1% |
Inflation Rate – Replacement Equipment | 1%/year | ± 0.5% |
Inflation Rate – Energy | 3%/year | ± 1% |
Inflation Rate – Maintenance | 2%/year | ± 1% |
Inflation Rate – Cost of Refrigerants (other than R22) | 2%/year | ± 1% |
Inflation Rate – R22 Refrigerant | 10%/year | ± 5% |
The sum of all costs obtained in this study have been submitted to a statistical analysis in accordance with the Monte-Carlo methodology where the level of uncertainty or error was set equal to two times the standard deviation.
Calculating Annuity Equal to Present Value
The calculation of annuity takes into account the present value of the total owning and operating costs over 20 years. The interest rate used for calculating the annuity is shown in Table 8.
Excluded cost items
The following cost items have been excluded from the initial investment for a refrigeration system:
- The safety equipment recommended in the risk analysis. These vary considerably depending on the type of refrigerant, the type of installation and the location of the facility within the municipality. There are two exceptions: System A2 (City of Montréal) and A3 (City of Québec): Included in their costs are those for an air washer installed on the emergency exhaust system of the mechanical room to absorb ammonia vapors plus a water tank to absorb the ammonia that could be exhausted from the safety valve in case of over pressure in the system. The cost for these items can reach up to $150,000.
- The cost of periodic supervision of a refrigeration system with ammonia by a stationary enginemen. This cost varies between $13,000 and $21,000 per year depending on the number of hours of supervision per day and the number of months of operation of the ice rink. The minimum requirement is one hour per day. A sensitivity analysis has been made on these costs the results which are reported in Tables 23 and 24.
- The cost for training municipal firemen in their capacity of handling emergency health and safety dangers. This involves creating an emergency squad called HAZMAT (Hazourdous Materials). Training costs can reach up to $100,000 initially and $20,000/year for updates and specialized equipment renewal. Less costly options could involve sharing the cost of a HAZMAT squad with neighbouring municipalities. Also, in certain regions, the private sector offers such services.
- The costs for extended warranties. These vary according to the type of refrigeration system, the manufacturer and the type of equipment.
SUMMARY TABLES OF RESULTS
The tables presented hereafter provide a summary of the items listed below for the 12 systems studied.
List of summary tables:
- Table 9: Main Physical Characteristics of Equipment
- Table 10: Cooling and Heating Capacities
- Table 11: Installed Electrical Power
- Table 12: Energy Consumption of Refrigeration Systems
- Table 13: Energy Consumption of Heating Systems
- Table 14: Energy Balance and Power Demand
- Table 15: Average COP (Coefficients of Performance) in Cooling, Heating and Combined
- Table 16: Initial Investments (Without Subsidies)
- Table 17: Energy Costs per Year
- Table 18: Maintenance and Repair Costs
- Table 19: Other Costs (Training, Refrigerant)
- Table 20: Subsidies and Incentives
- Table 21: Summary of Purchase and Maintenance Costs
- Table 22: Net Present Value and Annuity of Purchase and Operating Costs Over 20 Years
- Table 23: Summary of Financial Scenarios for Systems Under Study
- Table 24: Summary – PV of Residual Values
Case | Assembly Type | Refrigerant | Compressor Type | Number | Evaporation | Evaporator | Interior Condenser | Exterior Waste Heat Equipment | Rink Slab Fluid | Life Cycle (years) |
---|---|---|---|---|---|---|---|---|---|---|
A1 | Packaged | R717 | Open screw | 2 | Flooded | Titanium shell and plate | Plate | Open cooling tower | CaCl2 | 30 |
A2 | On site | R717 | Open reciprocating | 3 | Flooded | Titanium plate | Plate | Closed circuit cooling tower | CaCl2 | 30 |
A3 | On site | R717 | Open reciprocating | 3 | Flooded | 254 Stainless steel plate | Plate | Closed circuit cooling tower | CaCl2 | 30 |
A4 | Packaged | R717 | Open screw | 2 | Flooded | Stainless steel plate | Plate | Open cooling tower | Ethylene glycol | 30 |
A5 | Packaged | R717 | Open reciprocating | 3 | Flooded | Stainless steel plate | Plate | Open cooling tower | Ethylene glycol | 30 |
C1 | Split-packaged | R744 | Semi-hermetic reciprocating | 8 | Recirculating flooded | Slab tubing | None | Gas cooler | CO2 | 25 |
C2 | Split-packaged | R744 | Semi-hermetic reciprocating | 6 | Direct expansion | Shell and plate | None | Gas cooler | CaCl2 | 25 |
H1 | On site | HCFC R22 | Open reciprocating | 6 | Direct expansion | Shell and tube | None | Air condenser | CaCl2 | 20 |
H2 | Packaged | HFC R507A | Semi-hermetic screw | 3 | Direct expansion | Titanium plate | Plate | Fluid cooler | CaCl2 | 20 |
H3 | Modular | HFC R410A | Hermetic scroll | 5 | Direct expansion | Stainless steel plate | Plate | Fluid cooler | Methanol | 20 |
H4 | Modular | HFC R507a | Semi-hermetic screw | 2 | Direct expansion | Stainless steel plate | Plate | Fluid cooler | Ethylene glycol | 20 |
H5 | Packaged | HFC R134A | Semi-hermetic screw (variable capacity) | 2 | Falling film | Shell and tube, two independent circuits | Shell and tube | Fluid cooler | CaCl2 | 20 |
- This table shows the main physical characteristics of the twelve options. Data were provided by the equipment manufacturers and designers of these systems.
Case | Assembly Type | Refrigerant | Total Amount of Refrigerant | Amount of Refrigerant | Cooling Capacity |
Auxiliary Heating Capacity | Hot Water Desuperheater | Air Heating Recovery | Heat Pump Heating | PAC COP |
---|---|---|---|---|---|---|---|---|---|---|
Unités | kg | kg/tr | kW | kW | kW | kW | kW | kW/kW | ||
A1 | Packaged | R717 | 45 | 0.6 | 262 | 75 | 42 | 200 | 0 | 0 |
A2 | On site | R717 | 114 | 1.6 | 247 | 75 | 42 | 200 | 191 | 4.5 |
A3 | On site | R717 | 273 | 3.8 | 254 | 75 | 36 | 200 | 206 | 3.01 |
A4 | Packaged | R717 | 320 | 4.1 | 273 | 75 | 88 | 200 | 0 | 0 |
A5 | Packaged | R717 | 230 | 3.3 | 247 | 75 | 88 | 200 | 0 | 0 |
C1 | Split-packaged | R744 | 1,591 | 20.7 | 270 | 110 | 100 | 200 | 0 | 0 |
C2 | Split-packaged | R744 | 500 | 6.5 | 271 | 75 | 90 | 200 | 0 | 0 |
H1 | On site | HCFC R22 | 409 | 4.6 | 310 | 275 | 42 | 0 | 0 | 0 |
H2 | Packaged | HFC R507A | 114 | 1.4 | 287 | 75 | 88 | 200 | 0 | 0 |
H3 | Modular | HFC R410A | 45 | 0.6 | 267 | 75 | 0 | 200 | 0 | 0 |
H4 | Modular | HFC R507a | 100 | 1.4 | 254 | 75 | 0 | 200 | 0 | 0 |
H5 | Packaged | HFC R134A | 166 | 2.0 | 289 | 75 | 0 | 200 | 79 | 3.69 |
- Amount of refrigerant used in refrigeration systems.
- Cooling capacity in kW.
- Capacity of the auxiliary heating system for air and water - all cases use an auxiliary 75 kW electric boiler for domestic hot water and ice surfacing.
- Rated heating capacity of the desuperheater.
- Capacity of the space heating coil; system H1 does not recover heat from the refrigeration system.
- Heating capacity of heat pumps for arena make-up air, domestic hot water and ice surfacing.
- COP of heat pumps in heating mode.
Case | Assembly Type | Refrigerant | Auxiliary Heating Power | Compressor Horsepower | Heat Pump Heating | Slab Pump | Waste Heat Pump | Waste Heat Ventilator | Heat Recovery Pumps | Total | Variation |
---|---|---|---|---|---|---|---|---|---|---|---|
Unit | kW | kW | kW | kW | kW | kW | kW | kW | % | ||
A1 | Packaged | R717 | 75 | 81 | 0 | 11.2 | 9.7 | 3.7 | 3.7 | 184 | -29 |
A2 | On site | R717 | 75 | 81 | 42.5 | 11.2 | 5.6 | 37.3 | 6.3 | 259 | 0 |
A3 | On site | R717 | 75 | 113 | 68.3 | 18.6 | 8.6 | 37.3 | 7.8 | 329 | 27 |
A4 | Packaged | R717 | 75 | 84 | 0 | 11.2 | 16.8 | 14.9 | 5.6 | 208 | -20 |
A5 | Packaged | R717 | 75 | 81 | 0 | 11.2 | 16.8 | 14.9 | 5.6 | 205 | -21 |
C1 | Split-packaged | R744 | 110 | 100 | 0 | 2.2 | 0.0 | 16.0 | 3.7 | 232 | -10 |
C2 | Split-packaged | R744 | 75 | 129 | 0 | 11.2 | 0.0 | 23.5 | 0.0 | 239 | -8 |
H1 | On site | HCFC R22 | 275 | 126 | 0 | 18.6 | 0.0 | 22.3 | 0.0 | 442 | 71 |
H2 | Packaged | HFC R507A | 75 | 128 | 0 | 11.2 | 5.6 | 11.9 | 3.7 | 235 | -9 |
H3 | Modular | HFC R410A | 75 | 130 | 0 | 11.2 | 11.2 | 11.9 | 2.2 | 242 | -7 |
H4 | Modular | HFC R507a | 75 | 106 | 0 | 14.9 | 7.5 | 23.9 | 3.7 | 231 | -11 |
H5 | Packaged | HFC R134A | 75 | 100 | 21.5 | 11.2 | 14.9 | 13.4 | 0.0 | 236 | -9 |
- The installed electrical power of the cooling and heating systems represents most of the ice rink’s electrical demand. The actual billed electricity demand must be inferior or equal to this value. The compressor horsepower is estimated based on design conditions.
- The power of systems A2 and A3 is the highest among the new systems mainly because of the waste heat recovery pumps and the indirect cooling tower ventilators. The power of CO2 systemsis 25% higher than the best case mainly due to the compressors. System A1 has the lowest power demand of all systems.
Case | Assembly Type | Refrigerant | Compressors | Slab Pump | Heat rejection EQUIPMENT |
Total | Variation |
---|---|---|---|---|---|---|---|
Unit | kWh/year | kWh/ year | kWh/year | kWh/year | % | ||
A1 | Packaged | R717 | 279,200 | 73,300 | 54,500 | 407,000 | 6 |
A2 | On site | R717 | 245,000 | 73,300 | 65,000 | 383,400 | 0 |
A3 | On site | R717 | 267,800 | 122,200 | 63,600 | 453,600 | 18 |
A4 | Packaged | R717 | 264,000 | 73,300 | 74,900 | 412,200 | 8 |
A5 | Packaged | R717 | 298,500 | 73,300 | 74,600 | 446,400 | 16 |
C1 | Split-packaged | R744 | 263,400 | 14,700 | 13,000 | 291,100 | -24 |
C2 | Split-packaged | R744 | 281,200 | 73,300 | 19,900 | 374,500 | -2 |
H1 | On site | HCFC R22 | 411,900 | 122,200 | 16,100 | 550,200 | 44 |
H2 | Packaged | HFC R507A | 368,800 | 73,300 | 26,200 | 468,400 | 22 |
H3 | Modular | HFC R410A | 465,300 | 36,200 | 53,100 | 554,600 | 45 |
H4 | Modular | HFC R507a | 323,900 | 97,800 | 63,900 | 485,500 | 27 |
H5 | Packaged | HFC R134A | 339,300 | 73,300 | 106,000 | 518,600 | 35 |
- The C1 refrigeration system using CO2 consumes less energy, 18% less than Unit A2. This is mostly due to the CO2 directly recirculating in the rink slab.
- Unit C2 that is CO2–based uses a secondary fluid in the rink slab and is a more realistic comparison to ammonia systems.
Case | Assembly Type | Refrigerant | Heat Pumps, Air Heating |
Heat Recovery Pumps, Air Heating |
Auxiliary Heating, Air Heating |
Auxiliary Heating Water |
Total | Variation |
---|---|---|---|---|---|---|---|---|
Unit | kWh/ year | kWh/ year | kWh/ year | kWh/ year | kWh/ year | % | ||
A1 | Packaged | R717 | 0 | 12,000 | 0 | 65,100 | 77,100 | -52 |
A2 | On site | R717 | 93,800 | 29,300 | 0 | 35,800 | 159,000 | 0 |
A3 | On site | R717 | 98,800 | 39,100 | 0 | 45,700 | 183,600 | 15 |
A4 | Packaged | R717 | 0 | 19,000 | 0 | 56,600 | 75,600 | -52 |
A5 | Packaged | R717 | 0 | 19,000 | 0 | 8,400 | 27,400 | -83 |
C1 | Split-packaged | R744 | 0 | 19,000 | 29,400 | 42,100 | 90,500 | -43 |
C2 | Split-packaged | R744 | 0 | 0 | 0 | 29,700 | 29,700 | -81 |
H1 | On site | HCFC R22 | 0 | 0 | 441,900 | 27,500 | 469,300 | 195 |
H2 | Packaged | HFC R507A | 0 | 28,500 | 0 | 72,900 | 101,300 | -36 |
H3 | Modular | HFC R410A | 0 | 7,600 | 0 | 92,800 | 100,400 | -37 |
H4 | Modular | HFC R507a | 0 | 12,000 | 0 | 141,000 | 153,000 | -4 |
H5 | Packaged | HFC R134A | 0 | 0 | 0 | 61,800 | 61,800 | -61 |
- In this table, options C2 and A5 stand out above the rest. In C2, the CO2 flows directly into the heat recovery, making it a simple system that consumes very little energy to recover heat from the refrigeration system. The A5 ammonia system shows the best performance in terms of water heating due to reciprocating compressors having a higher hot gas discharge temperature than screw compressors.
Case | Assembly Type | Refrigerant | Cooling | Heating | Total | Variation | Total Installed Power | Power Demand | Variation |
---|---|---|---|---|---|---|---|---|---|
Unit | kWh | kWh | kWh | % | kW | kW | % | ||
A1 | Packaged | R717 | 407,000 | 77,100 | 484,100 | -11 | 184 | 180 | -9 |
A2 | On site | R717 | 383,400 | 159,000 | 542,300 | 0 | 259 | 198 | 0 |
A3 | On site | R717 | 453,600 | 183,600 | 637,100 | 17 | 329 | 210 | 6 |
A4 | Packaged | R717 | 412,200 | 75,600 | 487,800 | -10 | 208 | 179 | -10 |
A5 | Packaged | R717 | 446,400 | 27,400 | 473,800 | -13 | 205 | 171 | -14 |
C1 | Split-packaged | R744 | 291,100 | 90,500 | 381,600 | -30 | 232 | 181 | -9 |
C2 | Split-packaged | R744 | 374,500 | 29,700 | 404,100 | -25 | 239 | 188 | -5 |
H1 | On site | HCFC R22 | 550,200 | 469,300 | 1, 019,600 | 88 | 442 | 381 | 92 |
H2 | Packaged | HFC R507A | 468,400 | 101,300 | 569,700 | 5 | 235 | 197 | -1 |
H3 | Modular | HFC R410A | 554,600 | 100,400 | 655,000 | 21 | 242 | 225 | 14 |
H4 | Modular | HFC R507a | 485,500 | 153,000 | 638,500 | 18 | 231 | 192 | -3 |
H5 | Packaged | HFC R134A | 518,600 | 61,800 | 580,400 | 7 | 236 | 208 | 5 |
- Considering the total energy consumption for cooling and heating, the CO2 units C1 and C2 consume 29 and 27% less energy than A2, and the power demand is comparable to the best cases.
Case | Assembly Type | Refrigerant | Compressor COP | Refrigeration COP | Heating COP | Combined COP | Variation |
---|---|---|---|---|---|---|---|
Unit | kWh/kWh | kWh/kWh | kWh/kWh | kWh/kWh | % | ||
A1 | Packaged | R717 | 3.4 | 2.4 | 7.6 | 3.2 | 10 |
A2 | On site | R717 | 3.9 | 2.5 | 3.7 | 2.9 | 0 |
A3 | On site | R717 | 3.8 | 2.2 | 3.2 | 2.5 | -14 |
A4 | Packaged | R717 | 3.6 | 2.3 | 7.8 | 3.2 | 10 |
A5 | Packaged | R717 | 3.2 | 2.1 | 21.5 | 3.3 | 14 |
C1 | Split-packaged | R744 | 3.4 | 3.1 | 6.5 | 3.9 | 34 |
C2 | Split-packaged | R744 | 3.4 | 2.6 | 19.8 | 3.8 | 31 |
H1 | On site | HCFC R22 | 2.4 | 1.8 | 1.3 | 1.6 | -45 |
H2 | Packaged | HFC R507A | 2.6 | 2.0 | 5.8 | 2.7 | -7 |
H3 | Modular | HFC R410A | 2.0 | 1.7 | 5.9 | 2.3 | -21 |
H4 | Modular | HFC R507a | 3.0 | 2.0 | 3.8 | 2.5 | -14 |
H5 | Packaged | HFC R134A | 2.8 | 1.8 | 9.5 | 2.7 | -7 |
- Option A5 shows a high heating COP at 21.5. Reciprocating compressors offer the potential of more heat recovery for hot water heating due to a high gas discharge temperature.
- Option C2 shows a high heating COP of 19.8. This system does not use circulating pumps for heat recovery and the only other expense is for auxiliary water heating.
- The COP table confirms the data from energy consumption tables (i.e., cases C1 and C2 are well ahead with a combined COP that is 34 and 31% superior to that of case A2).
Case | Assembly Type | Refrigerant | System Refrigeration | Class-T Mechanical Room Expansion | Top Slab | Engineering Architecture |
Risk Analysis | Total | Variation |
---|---|---|---|---|---|---|---|---|---|
$ | $ | $ | $ | $ | $ | % | |||
A1 | Packaged | R717 | 770,000 | 50,000 | 0 | 82,000 | 10,000 | 912,000 | -61 |
A2 | On site | R717 | 1, 525,000 | 600,000 | 0 | 212,500 | 10,000 | 2, 347,500 | 0 |
A3 | On site | R717 | 1, 370,000 | 600,000 | 0 | 197,000 | 10,000 | 2, 177,000 | -7 |
A4 | Packaged | R717 | 768,000 | 50,000 | 0 | 81,800 | 10,000 | 909,800 | -61 |
A5 | Packaged | R717 | 804,000 | 50,000 | 0 | 85,400 | 10,000 | 949,400 | -60 |
C1 | Split-packaged | R744 | 800,000 | 0 | 360,000 | 116,000 | 10,000 | 1,286,000 | -45 |
C2 | Split-packaged | R744 | 645,000 | 0 | 0 | 64,500 | 10,000 | 719,500 | -69 |
H1 | On site | HCFC R22 | 82,000 | 0 | 0 | 0 | 0 | 82,000 | -97 |
H2 | Packaged | HFC R507A | 683,500 | 0 | 0 | 68,400 | 0 | 751,900 | -68 |
H3 | Modular | HFC R410A | 363,000 | 0 | 0 | 36,300 | 0 | 399,300 | -83 |
H4 | Modular | HFC R507a | 620,000 | 0 | 0 | 62,000 | 0 | 682,000 | -71 |
H5 | Packaged | HFC R134A | 590,000 | 0 | 0 | 59,000 | 0 | 649,000 | -72 |
- Engineering and architecture costs are estimated at 10% of the refrigeration system acquisition cost.
- Apart from Case H1, investment costs are lower for systems using synthetic refrigerants. Cases A2 and A3, assembled on site, are particularly expensive.
- The risk analysis cost considers it is made by a consultant supervised by a risk analysis expert. Such a study is not eligible for MELS funding.
- Slab restoration is eligible for MELS funding only if it requires work essential to its operation. Such funding is not considered in this project, because the slab is considered in good condition.
- The cost related to the top slab includes copper piping, chairs, concrete frame and pouring (2 or 3 inches). A cost of $50,000 for removing and re-installing the boards has been included (this is a minimum). The cost of $360,000 assumes that the existing slab has the capacity of carrying the weight of the over-slab. This must be confirmed by a structural engineer since certain refrigerated slabs are sitting on a pile foundation.
- The costs associated with a Class T mechanical room for options A2 and A3 take into account that these constructions conform to the local city planning regulation. Costs for option A1, A4, and A5 are adequate in municipalities that have regulations not as strict for this type of construction.
Case | Assembly Type | Refrigerant | Refrigeration Systems | Space Heating | Water Heating | Energy Total | Power Demand | Total Energy Costs | Variation |
---|---|---|---|---|---|---|---|---|---|
$/year | $/ year | $/ year | $/ year | $/ year | $/ year | % | |||
A1 | Packaged | R717 | 18,300 | 500 | 2,900 | 21,700 | 24,800 | 46,500 | -11 |
A2 | On site | R717 | 17,200 | 5,500 | 1,600 | 24,300 | 27,900 | 52,200 | 0 |
A3 | On site | R717 | 20,400 | 6,200 | 2,100 | 28,600 | 29,400 | 58,000 | 11 |
A4 | Packaged | R717 | 18,500 | 900 | 2,500 | 21,900 | 24,800 | 46,700 | -11 |
A5 | Packaged | R717 | 20,000 | 900 | 400 | 21,300 | 23,100 | 44,400 | -15 |
C1 | Split-packaged | R744 | 13,100 | 2,200 | 1,900 | 17,100 | 24,100 | 41,300 | -21 |
C2 | Split-packaged | R744 | 16,800 | 0 | 1,300 | 18,100 | 24,700 | 42,900 | -18 |
H1 | On site | HCFC R22 | 24,700 | 19,800 | 1,200 | 45,800 | 46,400 | 92,200 | 77 |
H2 | Packaged | HFC R507A | 21,000 | 1,300 | 3,300 | 25,600 | 27,200 | 52,700 | 1 |
H3 | Modular | HFC R410A | 24,900 | 300 | 4,200 | 29,400 | 30,900 | 60,300 | 16 |
H4 | Modular | HFC R507a | 21,800 | 500 | 6,300 | 28,700 | 27,300 | 56,000 | 7 |
H5 | Packaged | HFC R134A | 23,300 | 0 | 2,800 | 26,100 | 29,500 | 55,600 | 7 |
- The total costs of electricity (power demand plus consumption) in cases C1 and C2 are the lowest, i.e. respectively -21 % and -18 % compared to A2
Case | Assembly Type | Refrigerant | Regular Equipment Maintenance | Regular Cooling Tower Maintenance | Preventive Maintenance Contract (Manufacturer) | Total Maintenance Expenses | Variation |
---|---|---|---|---|---|---|---|
$/ year | $/ year | $/ year | $/ year | % | |||
A1 | Packaged | R717 | 9,000 | 3,000 | 5,000 | 17,000 | 9 |
A2 | On site | R717 | 12,600 | 3,000 | 0 | 15,600 | 0 |
A3 | On site | R717 | 11,800 | 3,000 | 0 | 14,800 | -5 |
A4 | Packaged | R717 | 8,700 | 3,000 | 3,000 | 14,700 | -6 |
A5 | Packaged | R717 | 9,400 | 3,000 | 3,000 | 15,400 | -1 |
C1 | Split-packaged | R744 | 9,800 | 0 | 5,000 | 14,800 | -5 |
C2 | Split-packaged | R744 | 9,000 | 0 | 5,000 | 14,000 | -10 |
H1 | On site | HCFC R22 | 16,000 | 0 | 0 | 16,000 | 3 |
H2 | Packaged | HFC R507A | 7,900 | 0 | 4,000 | 11,900 | -24 |
H3 | Modular | HFC R410A | 4,900 | 0 | 5,000 | 9,900 | -37 |
H4 | Modular | HFC R507a | 7,100 | 0 | 9,000 | 16,100 | 3 |
H5 | Packaged | HFC R134A | 2,000 | 0 | 3,000 | 5,000 | -68 |
- Case H5 using HFC R134A is the least expensive option in terms of maintenance. This manufacturer offers an extended warranty for the compressors for 10 years from the date of purchase at a cost of $30,000 payable at the time of acquisition of the system. The warranty covers labour and parts for any form of compressor failure during the period of guaranty. This cost item is not included in the study and is not considered in the maintenance costs reported here.
- For the other systems, the maintenance costs are quite similar varying from $10,000 to $17,000 per year.
- The regular equipment maintenance is calculated at 2% of the acquisition cost of the refrigeration system except for option H5. This percentage can be more than 2% in some municipalities.
Ident. | Assembly Type | Refrigerant | Initial Training | Specialized Training | Refrigerant Cost | Leakage Rate | Total Annual Leakage | Refrigerant Expenses |
---|---|---|---|---|---|---|---|---|
$/year | $/kg | %/year | kg/year | $/year | ||||
A1 | Packaged | R717 | 3200.00 | 1600.00 | 3.50 | 2.0 | 1 | 3 |
A2 | On site | R717 | 3200.00 | 1600.00 | 3.50 | 5.0 | 6 | 21 |
A3 | On site | R717 | 3200.00 | 1600.00 | 3.50 | 5.0 | 14 | 48 |
A4 | Packaged | R717 | 3200.00 | 1600.00 | 3.50 | 5.0 | 16 | 57 |
A5 | Packaged | R717 | 3200.00 | 1600.00 | 3.50 | 5.0 | 12 | 39 |
C1 | Split-packaged | R744 | 3200.00 | 1600.00 | 3.00 | 5.0 | 80 | 240 |
C2 | Split-packaged | R744 | 3200.00 | 1600.00 | 3.00 | 2.0 | 10 | 30 |
H1 | On site | HCFC R22 | 0.00 | 1000.00 | 47.50 | 10.0 | 41 | 1,944 |
H2 | Packaged | HFC R507A | 0.00 | 1000.00 | 18.00 | 2.0 | 2 | 42 |
H3 | Modular | HFC R410A | 0.00 | 1000.00 | 22.00 | 2.0 | 1 | 21 |
H4 | Modular | HFC R507a | 0.00 | 1000.00 | 18.00 | 2.0 | 2 | 36 |
H5 | Packaged | HFC R134A | 0.00 | 1000.00 | 6.60 | 2.0 | 3 | 21 |
- In smaller municipalities, ammonia options will require further training for firefighters in addition to ice rink personnel. These costs are not included in the budget shown above.
Case | Assembly Type | Refrigerant | Hydro-Québec | OPTER | MELS Component 1 |
Subsidies Total |
---|---|---|---|---|---|---|
A1 | Packaged | R717 | 80,300 | 60,000 | 456,000 | 596,300 |
A2 | On site | R717 | 71,600 | 60,000 | 700,000 | 831,600 |
A3 | On site | R717 | 57,400 | 60,000 | 700,000 | 817,400 |
A4 | Packaged | R717 | 79,800 | 60,000 | 454,900 | 594,700 |
A5 | Packaged | R717 | 81,900 | 60,000 | 474,700 | 616,600 |
C1 | Split-packaged | R744 | 95,700 | 60,000 | 445,000 | 600,700 |
C2 | Split-packaged | R744 | 92,300 | 60,000 | 359,800 | 512,100 |
H1 | On site | HCFC R22 | 0 | 0 | 0 | 0 |
H2 | Packaged | HFC R507A | 67,500 | 35,100 | 0 | 102,600 |
H3 | Modular | HFC R410A | 54,700 | 43,300 | 0 | 98,000 |
H4 | Modular | HFC R507A | 57,200 | 31,100 | 0 | 88,300 |
H5 | Packaged | HFC R134A | 65,900 | 42,300 | 0 | 108,200 |
- Potential support from the Hydro-Québec program – 0.15$/kWh saved.
- The MELS subsidy awarded to the refrigeration system also includes the costs associated with the mechanical room whether or not the latter is prefabricated or architectural. The subsidy amounts to 50% of costs inherent to refrigeration systems with ammonia or CO2. HFC systems like the ones considered in this study are not subsidised by MELS.
Case | Assembly type | Refrigerant | Acquisition Cost Total | Subsidies total | Energy | Routine Maintenance | Regular & Preventive Maintenance | Réfrigérant | Training |
---|---|---|---|---|---|---|---|---|---|
$ | $ | $/20 years | $/20 years | $/20 years | $/20 years | $/20 years | |||
A1 | Packaged | R717 | 912,000 | 596,300 | 930,400 | 45,800 | 307,400 | 60 | 32,100 |
A2 | On site | R717 | 2, 347,500 | 831,600 | 1, 044,200 | 54,900 | 282,100 | 360 | 32,100 |
A3 | On site | R717 | 2, 177,000 | 817,400 | 1, 160,200 | 63,500 | 267,600 | 860 | 32,100 |
A4 | Packaged | R717 | 909,800 | 594,700 | 933,800 | 63,200 | 265,800 | 1,010 | 32,100 |
A5 | Packaged | R717 | 949,400 | 616,600 | 888,300 | 52,600 | 278,800 | 730 | 32,100 |
C1 | Split-packaged | R744 | 1, 286,000 | 600,700 | 825,600 | 35,500 | 267,600 | 4,310 | 32,100 |
C2 | Split-packaged | R744 | 719,500 | 512,100 | 857,600 | 41,900 | 253,100 | 540 | 32,100 |
H1 | On site | HCFC R22 | 82,000 | 0 | 1, 843,300 | 106,000 | 289,300 | 35,140 | 18,100 |
H2 | Packaged | HFC R507A | 751,900 | 102,600 | 1, 054,900 | 42,500 | 214,600 | 740 | 18,100 |
H3 | Modular | HFC R410A | 399,300 | 98,000 | 1, 205,900 | 51,800 | 179,000 | 360 | 18,100 |
H4 | Modular | HFC R507A | 682,000 | 88,300 | 1, 119,100 | 40,500 | 291,100 | 650 | 18,100 |
H5 | Packaged | HFC R134A | 649,000 | 108,200 | 1, 111,200 | 40,400 | 90,400 | 400 | 18,100 |
- Routine maintenance costs that include equipment replacement vary between $45,000 and $63,000.
Case | Assembly Type | Refrigerant | Present Value | Error Rate on 95% Certainty | Variation | Annuity |
---|---|---|---|---|---|---|
$ | $ | % | $/20 year | |||
A1 | Monobloc | R717 | 1, 631,400 | ±170,000 | -44 | 109,700 |
A2 | Sur place | R717 | 2, 929,600 | ±184,000 | 0 | 196,900 |
A3 | Sur place | R717 | 2,884,000 | ±199,000 | -2 | 193,800 |
A4 | Monobloc | R717 | 1, 611,100 | ±168,000 | -45 | 108,300 |
A5 | Monobloc | R717 | 1, 585,400 | ±162,000 | -46 | 106,600 |
C1 | Bibloc | R744 | 1,850, 500 | ±149,000 | -37 | 124,400 |
C2 | Bibloc | R744 | 1, 392,800 | ±152,000 | -52 | 93,600 |
H1 | Sur place | HCFC-R22 | 2,373, 800 | ±305,000 | -19 | 159,600 |
H2 | Monobloc | HFC-R507A | 1, 980,100 | ±177,000 | -32 | 133,100 |
H3 | Modulaire | HFC-R410A | 1, 756,400 | ±196,000 | -40 | 118,100 |
H4 | Modulaire | HFC-R507A | 2, 063,200 | ±193,000 | -30 | 138,700 |
H5 | Monobloc | HFC-R134A | 1, 801,300 | ±174,000 | -39 | 121,100 |
- Case C2 remains the most efficient of all cases. As soon as the mechanical room cost is included, ammonia systems are disadvantaged and HFC systems become greater competition.
- The annuity calculated in this table represents the annual loan repayment over 20 years, covering all costs for acquisition, operation, maintenance and training.
- In options A2 and A3, the following cost items are included: a Class T mechanical room and a minimum amount of prevention and mitigation measures against risks. These measures can be modulated according to the geographical location of the ice rink, the refrigerant type and charge, etc.
- The column indicating error rate on 95% show the variation on the total present value resulting from a plus or minus variation of the inflation rates as indicated in Table 8
Case | Identification | Global costs on 20 years without residual values | |||||||
---|---|---|---|---|---|---|---|---|---|
Assembly type | Refrigerant | Scenario 1 | Scenario 2 | Scenario 3 | Scenario 4 | Scenario 5 | Scenario 6 | Scenario 7 | |
$ | $ | $ | $ | $ | $ | $ | |||
A1 | Packaged | R717 | 1,631,000 | 2,228,000 | 2,158,000 | 1,992,000 | 2,833,000 | 2,519,000 | 2,809,000 |
A2 | On site | R717 | 2,930,000 | 3,761,000 | 3,456,000 | 2,930,000 | 3,761,000 | 3,456,000 | 3,746,000 |
A3 | On site | R717 | 2,884,000 | 3,701,000 | 3,411,000 | 2,884,000 | 3,701,000 | 3,411,000 | 3,700,000 |
A4 | Packaged | R717 | 1,611,000 | 2,206,000 | 2,138,000 | 1,971,000 | 2,811,000 | 2,498,000 | 2,787,000 |
A5 | Packaged | R717 | 1,585,000 | 2,202,000 | 2,112,000 | 1,965,000 | 2,807,000 | 2,492,000 | 2,781,000 |
C1 | Split-packaged | R744 | 1,850,000 | 2,451,000 | 2,025,000 | 1,850,000 | 2,451,000 | 2,025,000 | 2,421,000 |
C2 | Split-packaged | R744 | 1,393,000 | 1,905,000 | 1,920,000 | 1,393,000 | 1,905,000 | 1,920,000 | 1,920,000 |
H1 | On site | HCFC-R22 | 2,374,000 | 2,374,000 | 2,901,000 | 2,374,000 | 2,374,000 | 2,901,000 | 2,901,000 |
H2 | Packaged | HFC-R507A | 1,980,000 | 2,083,000 | 2,507,000 | 1,980,000 | 2,083,000 | 2,507,000 | 2,507,000 |
H3 | Modular | HFC-R410A | 1,756,000 | 1,854,000 | 2,283,000 | 1,756,000 | 1,854,000 | 2,283,000 | 2,283,000 |
H4 | Modular | HFC-R507A | 2,063,000 | 2,151,000 | 2,590,000 | 2,063,000 | 2,151,000 | 2,590,000 | 2,590,000 |
H5 | Packaged | HFC-R134A | 1,801,000 | 1,909,000 | 2,328,000 | 1,801,000 | 1,909,000 | 2,328,000 | 2,328,000 |
- Scenario 1 is the reference scenario and it includes subsidies.
- Scenario 2 = reference scenario without subsidies.
- Scenario 3 = reference scenario with a renovation of the concrete slab for all options.
- Scenario 4 = reference scenario with a Class T mechanical room for all ammonia systems.
- Scenario 5 = scenario 2 with a Class T mechanical room for all ammonia systems.
- Scenario 6 = reference scenario with a Class T mechanical room for all ammonia systems plus the renovation of the concrete slab for all options.
- Scenario 7 = scenario 6 plus supervision costs by a stationary engineman.
Case | Identification | Residual values for the total cost of 20 years | |||||||
---|---|---|---|---|---|---|---|---|---|
Assembly type | Refrigerant | Scenario 1 | Scenario 2 | Scenario 3 | Scenario 4 | Scenario 5 | Scenario 6 | Scenario 7 | |
$ | $ | $ | $ | $ | $ | $ | |||
A1 | Packaged | R717 | 84,000 | 84,000 | 563,000 | 684,000 | 684,000 | 1,163,000 | 1,163,000 |
A2 | On site | R717 | 718,000 | 718,000 | 1,197,000 | 718,000 | 718,000 | 1,197,000 | 1,197,000 |
A3 | On site | R717 | 710,000 | 710,000 | 1,189,000 | 710,000 | 710,000 | 1,189,000 | 1,189,000 |
A4 | Packaged | R717 | 81,000 | 81,000 | 560,000 | 681,000 | 681,000 | 1,160,000 | 1,160,000 |
A5 | Packaged | R717 | 87,000 | 87,000 | 566,000 | 687,000 | 687,000 | 1,166,000 | 1,166,000 |
C1 | Split-packaged | R744 | 452,000 | 452,000 | 575,000 | 56,000 | 56,000 | 575,000 | 575,000 |
C2 | Split-packaged | R744 | 51,000 | 51,000 | 530,000 | 51,000 | 51,000 | 530,000 | 530,000 |
H1 | On site | HCFC-R22 | 4,000 | 4,000 | 483,000 | 4,000 | 4,000 | 483,000 | 483,000 |
H2 | Packaged | HFC-R507A | 3,000 | 3,000 | 482,000 | 3,000 | 3,000 | 482,000 | 482,000 |
H3 | Modular | HFC-R410A | 6,000 | 6,000 | 485,000 | 6,000 | 6,000 | 485,000 | 485,000 |
H4 | Modular | HFC-R507A | 2,000 | 2,000 | 481,000 | 2,000 | 2,000 | 481,000 | 481,000 |
H5 | Packaged | HFC-R134A | 2,000 | 2,000 | 481,000 | 2,000 | 2,000 | 481,000 | 481,000 |
- Scenario 1 is the reference scenario and it includes subsidies.
- Scenario 2 = reference scenario without subsidies.
- Scenario 3 = reference scenario with a renovation of the concrete slab for all options.
- Scenario 4 = reference scenario with a Class T mechanical room for all ammonia systems.
- Scenario 5 = scenario 2 with a Class T mechanical room for all ammonia systems.
- Scenario 6 = reference scenario with a Class T mechanical room for all ammonia systems plus the renovation of the concrete slab for all options.
- Scenario 7 = scenario 6 plus supervision costs by a stationary engineman.
RISK ANALYSIS BASED ON REFRIGERANT TYPE
All refrigerant types used in ice rinks pose risks to human health and/or safety. Whether it is the pressure of systems operation or the product toxicity or flammability, it is essential that risk analyses be conducted in all cases in order to determine prevention and mitigation measures in case of accident. These measures are often foreseen by laws and regulations, but they can also be recommended by experts in the field.
JP Lacoursière inc., an expert company in the refrigeration prevention and mitigation assessment field, conducted the analysis and made specific risk recommendations for each of the three refrigerant categories (i.e. ammonia, CO2 and HFCs) identified in this report.
A summary of the results is presented in this section; the complete reports can also be viewed in the appendices at the end of this document.
AMMONIA (R717)
Used as a refrigerant for over 30 years, ammonia was gradually being replaced by chlorofluorocarbons (CFCs), but has begun regaining some ground since the adoption of the Montreal Protocol and the Kyoto Protocol, aimed at completely banishing HCFCs over the course of the next 10 years. Ammonia systems are reclaiming their place due to their efficiency and to the fact that they represent a long-term solution to the sustainable development of ice rinks. Specific precautionary measures must be taken however to ensure a safe use of this refrigerant.
Facilities equipped with ammonia refrigeration systems are safe when properly designed and when their safety is assured by an operational security program. The operational security program includes elements such as equipment information, appropriate hazard assessments, mechanical integrity, management of changes, management of subcontractors, training of operation and maintenance staff, post-incident investigations, records of accidents and incidents, emergency plans and compliance audits.
Ammonia refrigeration systems for ice rinks must at least comply with all relevant clauses of the Mechanical Refrigeration Code B52-05 and other applicable laws and regulations, in particular the Occupational Health and Safety Regulations (OHSR). The goal of this study was to identify methods of designing and operating facilities that are inherently safer than what the ammonia refrigeration code calls for, considering that ice rinks are not isolated from their surroundings and frequented by vulnerable groups of the population, often including children.
The study identified the following 18 recommendations:
1 | It is recommended that the client (i.e. the municipality) require the refrigeration system designer to perform an ammonia system risk analysis and to report the findings to the client and competent authority. |
2 | It is recommended to do a modeling of the effects of ammonia release in the following cases:
|
3 | Using a mechanical ventilator (exhaust) with an upward-flow vertical outlet, with internal dilution and high outlet velocity (26 m/s) as a minimum standard for emergency ventilation for a Class T mechanical room. Note that the presence of high-rise buildings overlooking the Class T mechanical room within a short distance (< 300 m) could require additional intervention measures including a scrubber. |
4 | Using a suction fan purifier when there are tall buildings located within a short distance (< 300 m) of the mechanical room. It is recommended to confirm the relevance of implementing the recommendation through the use of plume modeling. The goal of the modeling will be to identify appropriate preventive and intervention measures. The modeling software should allow for vertical plane modeling, at least the PHAST v 6.7 software and later versions of Det Noska Veritas (DNV). The methodology is described in MIARC 2007 (Major Industrial Accidents Reduction Council). Wake effects should be taken into account for the modeling. |
5 | Setting up the ammonia condenser inside the Class T mechanical room when there are residents (people permanently or sporadically present in homes, buildings, schools, hospitals, shopping malls, parks, bridges, walkways, etc.) at a distance of less than 300 m, and also to use a coolant for cooling the condenser with a fluid cooler outside the mechanical room. It is recommended to confirm the relevance of implementing the recommendation through the use of plume modeling. The goal of the modeling will be to identify appropriate preventive and intervention measures. The modeling software should allow for vertical plane modeling, at least the PHAST v 6.7 software and later versions of Det Noska Veritas (DNV). The methodology is described in MIARC 2007 (Major Industrial Accidents Reduction Council). Wake effects should be taken into account for the modeling. |
6 | Installing at least two ammonia detectors on the Class T mechanical room ceiling, The location selected should be close to areas posing a high risk of ammonia leakage (i.e. near compressors, plate cooler). |
7 | Making sure that equipment controls cannot be automatically reset following a stoppage resulting from ammonia detection because of improper computer programming. |
8 | Considering redundancy by installing electrochemical cell and infrared ammonia sensors to increase the reliability of detection system in case of high ammonia concentrations. |
9 | Installing a titanium or brine-resistant alloy plate heat exchanger, unwelded or semi-welded, for the application of the brine cooler. Semi-welded plate coolers are safer and should thus be the preferred choice. |
10 | Installing (as needed) an ammonia detector near the ice rink’s ventilation system return to avoid having this system prevent ammonia detection. |
11 | Installing a closed circuit for oil drainage of the ammonia refrigeration circuit. |
12 | Putting devices in place to stop the compressors and to isolate the refrigeration system by the use of solenoid valves in case of detected ammonia concentrations exceeding 250 ppm in the Class T mechanical room. |
13 | Installing a neutralization reservoir to collect the relief valve discharge preventing the dispersion of ammonia from this source. |
14 | Ensure the Class T mechanical room setup complies with Article 6.1.3 of the Mechanical Refrigeration Code and provides secure access to equipment and valves for troubleshooting and emergency response. |
15 | Making sure that the control room and the motor control station are located in an airtight room separate from the Class T mechanical room to allow remote operation of the equipment without exposure to ammonia. |
16 | Ensure that the equipment, fittings and controls are identified in accordance with Article 5.11.3 of the Mechanical Refrigeration Code to facilitate troubleshooting and response to an emergency. In addition, the identification should be consistent with the flow diagrams and P&IDs for refrigeration facilities. |
17 | Making sure that a holistic operational safety program is put in place including components on process information, hazard analysis, change management, mechanical integrity, contractor management, operating and maintenance staff training, emergency plans, incident investigation and records and verification of accidents and incidents. Although equipment manufacturers provide a maintenance service for refrigeration system components, their service mainly targets equipment life cycle and not civil security. Thus, conducting a risk analysis would lead to the creation of a more comprehensive maintenance plan that would result in not only managing the life cycle of equipment, but also in improving the safety of the refrigeration system. |
18 | Developing a training program on refrigeration systems sanctioned by the Order des ingénieurs du Québec to be shared with refrigeration system designers. This program could be developed and shared through a university. |
CO2 (R744)
These recommendations are taken from our report entitled “Technical Study on CO2 Refrigeration Systems for Ice Rinks as Part of the Techno-Commercial Study on CO2 Refrigeration for Ice Rinks”.
CO2 systems are mainly used in supermarkets where they replace CFC and HCFC systems. They are now good options for air conditioning systems in cars. A natural extension for the use of this refrigerant is in ice rinks. Some specialists consider CO2 as a long term solution for ice rink refrigeration in view of the need for sustainable development.
CO2 is not more or less safe than the other refrigerants. Like all other refrigerants, the key to a safe installation is to design, install and operate the system after having thoroughly identified and evaluated the risks and dangers and minimized them by having well trained resources to design and operate such system.
The main danger with CO2 is reaching a lethal concentration (30,000 ppm) in a confined space. To evaluate the impact and demonstrate the effect of CO2 leaks in arena, simulations have been conducted following the rupture of tubes supplying the refrigerant to the under floor network if the ice pad as well as ruptures in piping supplying CO2 to unit heaters for space heating in the arena.
The rupture of a ½ inch liquid CO2 filled tube sitting inside a trench and connected to the supply or return distribution manifold can result in the accumulation of gas in excess of 30,000 ppm in some interior zones of the arena such as the players’ benches, inside the ice rink and at the lower rows of spectator benches. At the point of release, the gas is heavy i.e. 2.3 times the weight of air, becoming lighter (1.5 times the weight of air) after warming up. The gas will thus have a tendency to stratify in the lower parts of areas before being dissipated.
The rupture of a CO2 hot gas line coming from the compressors and supplying unit heaters could also result in a concentration of CO2 in excess of 30,000 ppm in the lower parts of the arena although this problem is less severe than with a liquid line.
Other risks of a CO2 system include the opening of a safety valve protecting the equipment. Opening this valve produces a high velocity jetstream at -76°C that could wound and produce serious frostbites on nearby people.
In conclusion, scenarios that have been simulated showing that CO2 concentrations can reach lethal concentration in areas close to the ice rink (players’ benches and lower rows of spectator seats). This observation justifies the implementation of prevention and mitigation measures to ensure a safe operation of such refrigeration system. Gaining a better understanding of the behaviour pattern of the CO2 after a leak either liquid or gas through the simulations, it is recommended to confine the CO2 within the mechanical room and using secondary fluids to refrigerate the skating pad and to meet the space heating demands of the arena and adjoining spaces.
The following recommendations are made in the event where confining the CO2 in the mechanical room is not the selection option:
The study identified the following 14recommendations:
1 | It is recommended to use tubing smaller than ½ inch in the ice pad in order to limit the quantity and the flow of CO2 in the event of a tubing rupture. |
2 | Use a more robust and resilient material than copper. |
3 | Reduce the number of joints in the piping. |
4 | Use a welding method that ensures a constant level of quality. |
5 | It is recommended to take into account the potential effects of an earthquake when designing the refrigeration system. |
6 | It is recommended to confine liquid CO2 in trenches with solid and airtight covers capable of resisting the high pressures that could be reached. It is also recommended to use CO2 sensors, alarm and exhaust fans of adequate capacity and exhausting in a safe area. |
7 | It is recommended to ventilate the arena with exhaust grills located in the lower parts of the spaces. Establishing a holistic program of operational security management for facilities operating at very high pressures and very low temperatures. |
8 | It is recommended to install the safety valve in a safe location and fence the immediate area to prevent a person from being in a dangerous area. |
9 | It is recommended that the safety valve be located at a safe distance from the exits of the ice rink as well as in the mechanical room. |
10 | It is recommended to anchor the piping strongly enough to resist the reactive force that occurs when the CO2 is expelled at high speed. |
11 | It is recommended, in areas where CO2 is used or can potentially reach, that CO2 sensors with alarms are present to monitor the levels of CO2 and O2 in order to alert persons in the vicinity and ventilate the area. |
12 | Conduct a risk analysis of facilities designed with CO2 refrigeration systems to identify risks and design an operational safety management program. |
13 | It is recommended to implement an operational safety program that comprises the following elements:
|
14 | Develop a training program on the safety aspect of refrigeration systems, approved by the Ordre des ingénieurs du Québec and offered to designers of refrigeration systems. This program could be developed and provided by universities. |
Halocarbons (HCFC-R22, HFC-R507a, hfc-r410a, hfc-r134a
These recommendations are abstracts from our report titled «Guide sur la gestion des risques à l’intention des concepteurs des systèmes frigorifiques d’arénas utilisant les halocarbures comme frigorigènes»
Chlorofluorocarbons (CFCs) have been used as refrigerants since 1930. Hydrochlorofluorocarbons (HCFCs) and hydrofluorocarbons (HFCs) have been introduced later as refrigerants. CFCs and HCFCs are partly responsible for depleting the ozone layer. The Montréal Protocol is aiming at totally banishing CFCs and HCFCs which includes R22. HFCs have been developed in order to replace CFCs and HCFCs. While they do not deplete the ozone layer, they are known to be significant greenhouse gas contributors.
Refrigeration systems using HFCs are an excellent option for ice rinks especially when ammonia [NH3 (R717)]or carbon dioxide [CO2 (R744)] are considered too risky for the neighbourhood or the users of the ice rink and/or that the cost of preventive and mitigation measures are found too costly.
The same safety principles that apply to the other types of refrigerants also apply to HFCs.
The study identified the following 11 recommendations:
1 | Avoid hydraulic shocks. |
2 | Prevent liquid refrigerant from reaching the compressor. |
3 | Provide safety valves to exhaust the refrigerant in case of over pressurization. |
4 | Prevent excessive vibrations. |
5 | Support equipment and piping separately. |
6 | Take into account the lowest temperature and the highest pressure in the selection of construction materials. |
7 | Size the length and diameter of the piping in a way that induces the smallest pressure loss when circulating lubrication oil thus minimizing inefficiencies in the refrigeration system. |
8 | Implement a maintenance program including preventive maintenance for critical components. |
9 | Implement an emergency plan with trained personnel and ensure the plan is operational and can be followed through at any time |
10 | Conduct a risk analysis at the design phase of an HFC refrigeration system to clearly identify risks and implement an operational safety management for the system |
11 | It is recommended to implement an operational safety program that comprises the following elements:
|
ANALYSIS OF STUDY RESULTS
WINNING CONDITIONS FOR SUCCESSFUL MAJOR RENOVATIONS TO A REFRIGERATION SYSTEM
The research and expertise that led to the realization of this study have allowed identifying a set of recommendations designed to better ensure the success of major renovations.
These recommendations were structured based on the milestones of a major renovation:
Planning
- Having detailed risk management analyses carried out that are specific to refrigeration and heat recovery concepts. The present report shows that several types of refrigeration systems may be suitable for a specific ice rink while the best solution is not necessarily obvious from the outset. Given the life cycle of a refrigeration system (generally 20 to 30 years), a rigorous approach from the start can generate benefits for many years. For this purpose, the terms of reference for these studies must include an accurate and precise scope of the work. CanmetENERGY developed such documents under the BEIE’s OPTER program (Refrigeration Optimization). The documents can be obtained from that organization.
- Planning a risk management analysis to be carried out by an expert and that is tailored to each concept. The analysis should detail the capital costs required to ensure that the facility does not only comply with laws and regulations, but that it also provides the greatest reliability possible through the implementation of best practices.
Feasibility Study
- Commissioning complete financial studies while adopting the approach of the overall purchasing and operating cost over a period of at least 15 year or of 20 years, as was the choice for the current report.
- Using, as needed, the topics covered in the following appendices as a checklist to ensure a comprehensive cost assessment.
- Taking into account the equipment and work required for the implementation of recommendations made in the risk management analysis.
Design
- The design stage is crucial to ensuring the performance, reliability and security of a refrigeration system. To this end, it is strongly recommended to use known and specialized refrigeration designers, as well as experts in mechanical HVAC design and risk management.
- Integrated heating and cooling solutions have become essential to ensuring lower long-term energy costs as well as minimizing greenhouse gas emissions.
- Preference will be given to systems containing the smallest amounts of refrigerant to minimize hazards in case of leakage and to reduce environmental impacts.
- Other preventive measures intended to minimize risks and to mitigate hazards in the event of an accident will be required at the design stage in accordance with the risk management analyses carried out during the planning stage.
Execution
- Supervision of the work is crucial to ensuring a quality facility, a quick start-up and efficient long-term operation. The managers of several ice rinks, after having invested considerable sums of money, were disappointed with the performance and reliability of their refrigeration systems due to inadequate supervision during the installation process.
Commissioning
- In terms of refrigeration, the importance of commissioning work is well established. This work should be entrusted to certified specialists.
- Training for ice rink managers and maintenance personnel should be given to ensure a better understanding and to require minimal supervision of facilities. This aspect of training is particularly important when ammonia or CO2 is the chosen refrigerant.
Ongoing Operations
- The importance of establishing preventive maintenance programs upon system start-up is the best guarantee against failures and risks associated with pressurized systems.
- The continuous training of operating personnel encourages them to refresh their knowledge and skills on a periodic basis while ensuring that they stay up to date with technological developments regarding refrigeration systems.
POTENTIAL SUPPLIERS
REFRIGERATION SYSTEMS
Table 25 contains the names of the companies that participated in the financing of the current study and that were identified with the help of ice rink managers.
Manufacturing, Assembly, Installation and Services | Ammonia | CO2 | HFC | |
---|---|---|---|---|
Carnot Réfrigération | Trois-Rivières (QC) http://www.carnotrefrigeration.com |
♦ | ♦ | |
Cimco Réfrigération | 18 Service Centres in Canada http://www.cimcorefrigeration.com | ♦ | ♦ | ♦ |
Fixair Inc | Laval (QC), Darmouth (NS) http://www.fixair.qc.ca |
♦ | ♦ | |
Kube Solutions | Darmouth (NS) http://thekubesolutions.com |
♦ | ||
Mayekawa | Vancouver, Toronto, Ottawa http://www.mycomcanada.com |
♦ | ♦ | ♦ |
Trane | Montreal, Quebec City, Chicoutimi http://www.trane.com |
♦ |
REFRIGERATION TRAINING
Table 26 provides a preliminary list of companies offering training sessions intended for ice rink managers, maintenance workers, stationary enginemen and refrigeration specialists. Depending on the training facilities, courses are offered in teaching institutions, hotels or at the workplace. The training content, duration and fees must be obtained directly from the companies identified.
Organizations and Companies | Website | Refrigeration Training |
---|---|---|
AQLP (Association québécoise du loisir public) (uses AQAIRS Training Program) |
http://www.aqairs.ca | Training in regions |
Marguerite-Bourgeois School Board Dalbé-Viau School |
http://www2.csmb.qc.ca | Training in educational institutions |
Comenco Services aux immeubles inc. | www.comenco.ca | Training on site |
CFCPC (Centre de formation continue des professionnels de la construction) | www.cfcpc.ca | Training in hotel meeting rooms |
André Delisle Refrigeration Consultant |
andel53@videotron.ca | Training on site |
CONCLUSIONS
This study presents a significant number of data and information useful for ice rink owners who plan to renovate a refrigeration system. Twelve systems are compared from the point of view of their performance, acquisition and operating costs over 20 years. The risks for the health and safety of the occupants and the neighborhood are also considered for the three families of refrigerant under study: ammonia, CO2 and synthetic refrigerants such as HFC and HCFC.
The reference ice rink which serves to evaluate the 12 options aims to be the most representative of the 425 ice rinks in Québec. This facility comprises:
- Only one ice rink in use 9 months per year - Operating hours: 6:00 a.m. to 12:00 midnight.
- Number of seats in the stands: 300 – 500.
- Refrigeration systems: R22 – six 30 HP compressors.
- Secondary loop: brine with 25 HP circulating pump.
- Desuperheater for water heating for showers and ice surfacing by heat recovery.
- Energy consumptions for dehumidification and lighting are not considered in this study.
The results of the study have been divided in four categories:
- Technical results: The results present the performance of the refrigeration systems in terms of COP (coefficient of performance) for refrigeration, heating as well as for the combined refrigeration and heating performances. Furthermore, the annual energy consumptions of every system have been calculated with the use of energy simulation software.
MAIN CONCLUSIONS- The systems with CO2 offer the best combined COP (3.9) followed by the ammonia systems (3.0 on average), systems with HFC (2.6 on average) and finally the system with R22 (1.6).
- The lowest total energy consumption belongs to the CO2 systems with 393 MWh/year on average versus 525 MWh/year (+34%) on average for ammonia systems and 611 MWh/year (+55%) for HFC systems. The system with R22 consumes the most with 1,020 MWh/year (+160%).
- The maximum electric power demand varies by approximately 10% amongst all systems (194 kW on average) with the exception of the R22 system where the power demand reaches 381 kW (+96%).
- Financial results: The results present the total costs of acquisition and operation over 20 years. Financial incentives and other contributions are taken into account. Sensitivity analyses also demonstrate the dependency and variations in the results caused by changing some criteria such as the inflation rate on energy prices.
MAIN CONCLUSIONS- When considering first cost only, the system with R22 is the least expensive option ($82,000). Replacing it by an ammonia system will require a net investment, after subsidies, of approximately $321,000. With a CO2 system, the investment varies between $207,000 with an unchanged brine loop to $685,000 with a new CO2 loop under the ice installed in a concrete over-slab.
- For the municipalities of Québec and Montréal, capital costs are considerably higher i.e. by more than $1 million. This is attributable to the concept of assembling the refrigeration system on site, building an architectural Class T mechanical room and providing special equipment to implement additional safety measures.
- Operating costs include energy, annual preventive maintenance, periodic maintenance and repairs as well as training. They are accumulated over 20 years and discounted to present values (PV). On the basis of annual maintenance only, refrigeration systems with HFC’s are the least costly with an average PV of $194,000. Amongst these, the system with refrigerant R134a has the lowest cost at $90,000. Ammonia and CO2 systems show slightly more expensive annual maintenance with an average of $275,000. The CO2 system with a brine loop is the least costly at $253,000.
- The total acquisition and operating cost on a 20 year time frame for all systems except those of the two large cities show an average of $1,740,000 with variations less than $250,000. With the exception of the ammonia systems in the two large cities, maintaining the existing R22 system is the most expensive option at $2,374,000 concluding that replacing this system is a sound decision.
- Again with the exception in the two large cities, on the basis of the annuity derived from the present value, the total acquisition and operating costs will require an average disbursement of $117,000/year with a variation of ± $22,000/year depending on the option or the refrigerant selected. On the same basis, the R22 system will cost $160,000/year.
- Environmental impacts: The greenhouse gas emissions (GHG) are calculated in consideration of refrigerant leaks as well as emissions related to electricity consumption.
MAIN CONCLUSIONS- Synthetic refrigerants being powerful GHG’s, it is not surprising that they would have the largest impact in this matter. The two main recommendations in this regard are first to limit the refrigerant charge in a system and secondly to ensure that the method assembly involves strict controls to minimize the risk of leaks in the future. In this perspective, packaged units are favored.
- Ammonia and CO2 systems have the smallest GHG emissions i.e. an average of 1,000 kg for 20 years of operation.
- Risks on health and safety: The casualties that are most liable to occur while operating refrigeration systems are analysed. Preventive and mitigation measures are proposed to ensure health and safety of the occupants as well as for the neighbourhood.
MAIN CONCLUSIONS- Ammonia systems are the ones requiring the most attention because of the high toxicity of this substance. In order to manage risk adequately and be well informed on preventive and mitigation measures, a formal risk analysis conforming with best practices is recommended in all case.
- When adjacent buildings are higher than the arena and within 300 meters, equipment designed to absorb ammonia emissions are recommended.
- CO2 systems also carry important risks especially when the CO2 circulates inside the arena. In case of a leak and because the gas is at high pressure and low temperature, it remains at floor level and displaces the ambient air. Occupants are then in risk of being asphyxiated. For this reason, a formal risk analysis is also recommended when this refrigerant is selected.
- Synthetic refrigerants are those offering the least risk; however is still of equal importance. Even though their use is better known in Québec, preventive and mitigation measures still need to be enforced rigorously.
STUDY CONTRIBUTORS
CREDITS
CanmetENERGY-Varennes, Natural Ressources Canada
- André Chalifour, P.Eng., Project Manager
- Daniel Giguère, P.Eng., Expert in refrigeration and heat pumps
- Ethel Mayrena Zelaya, P.Eng., Chef of project
- Philippe Simard, M.Sc.A., Expert in simulation
- Sylvie Lavoie, Secretary
- Josée Ottavi, Graphic Art and Web Design
- Joanie Frigon, Page Layout
- Amy-Lou Lafontaine, Translation
- Guillaume Corbeil-Archambault, Correction and markup.
- Martin Kegel, M.Sc.A., Research Engineer
EXTERNAL CONTRIBUTORS
- Dave Bouchard, P.Eng., Technical Representative – HVAC systems, Trane Québec
- David Gauvin, P.Eng., Technical Representative – HVAC-R systems, Trane Québec
- Benoit Rodier, P.Eng., Director, Business Development, CIMCO Refrigeration, Québec
- Sebastien Castonguay, General Manager – Province of Québec, CIMCO Refrigeration, Québec
- Serge Dubé, Président, SMARTREF Technology Inc., Québec
- Marc-André Lesmerises, P.Eng., President, Carnot Refrigeration, Québec
- Jonathan Ayotte, B. Eng., Technical Representative, Carnot Refrigeration, Québec
- Len Puchaz, Sales Manager, Mayekawa Canada Inc, Ontario
- Quinn Vo, P.Eng., Corporate Engineer, Mayekawa Canada Inc, Ontario
- Jason Pillipow, P.Eng., Director, Kube Solutions, Winnipeg
- Marc Gosselin, P.Eng., President, Fixair Inc., Québec
- Fabrice Springhetti, Project Manager, Fixair Inc., Québec
- Ronald Beaulne, Bitzer Canada Inc., Québec
- Alain Gadbois, P.Eng., Project Management and Construction Division, City of Québec
- Jean Walsh, P.Eng., Interim Division Head, Real Estate Transactions and Strategies Directorate, City of Montréal
- Costas Labos, P.Eng., Real Estate Transactions and Strategies Directorate, City of Montréal
- Claude Dumas, P.Eng., Expert – Refrigeration Systems for Ice Rinks, Real Estate Transactions and Strategies Directorate, City of Montréal
- Bertrand Plante, P.Eng., Section Head, Technical Development and Support, City of Montréal
- Mario Piché, Director general, Sportium of Val-des-Monts, Québec
- Eric Lachance, Mayor, Municipality of St-Gédéon-de-Beauce, Québec
- Gilles Beaudouin, Division Head, Buildings, City of Laval, Québec
- Yvan Grégoire, P.Eng., Project Engineer, Building Services, City of Longueuil, Québec
- Alain Boutin, Section Head, Building Maintenance, City of Sherbrooke, Québec
- Doris-Gilles Lafleur, Councillor, Office of Public Safety, Québec
- Sany Maltais, Councillor in Risk Management, Ministry of Public Safety, Québec
- Stéphanie Lacoursière, P.Eng., Expert in Risk Management, JP Lacoursière Inc., Québec
- Jean-Paul Lacoursière, P.Eng., Expert in Risk Management, JP Lacoursière Inc., Québec
- Jérémie Couture, Analyste, Ministry of Education, Leisure and Sport, Québec
- Samira Hélène Sammoun, P.Eng., Hydro-Québec Distribution, Québec
- Luc Simard, P.Eng., Génivar, Québec
- Kateri Héon, P.Eng., EXP Services Inc, Montréal
- Marie-Ève Lacroix, Councillor in Industrial Development, Ministry of Finance and Economy, Québec.
- Gilles Auger, P.Eng. Counsellor, Energy Efficiency Programs, AQAIRS
- Michel Fournier. P. Eng. Project Engineer, Institutional et Municipal Sectors, BEIE
APPENDICES
Appendix 1:
Schematic, Description and operation of the 12 Systems Studied
Appendix 2:
Summary of system warranties
Appendix 3:
energy consumption Results for an ice rink operating for 12 months
Appendix 4:
Summary Report on Risks Associated with the Use of Ammonia in Arenas
Appendix 5:
Risk Management Guide for Halocarbon Arena Refrigeration Systems
Appendix 6:
Risk Management Guide for Halocarbon Arena Refrigeration Systems
APPENDIX 1: SCHEMATIC, DESCRIPTION AND OPERATION OF THE 12 SYSTEMS STUDIED
SYSTEM A1: OPEN PACKAGED SYSTEM WITH STRATIFIED THERMAL STORAGE
SYSTEM DESCRIPTION
- Packaged ammonia refrigeration system, open screw compressors, assembled in factory on a steel base.
- Operates without a refrigerant receiver (45 kg or 0.3 kg/tonne of refrigeration), refrigerant confined to the mechanical room.
- Evaporator: titanium plate heat exchanger.
- Increased efficiency of refrigeration system by reducing the condenser temperature down to 13.5oC, weather permitting.
- Stratified thermal storage permits optimization of the refrigeration system operating pressure to stabilize energy demands
(hot and cold) and prioritizes heating needs. - Complete heat recovery from the refrigeration system: desuperheat from the compressor discharge, compressor oil cooler
and the system condenser heat rejection. - Pumping system modulated according to the required heating needs.
- Automatic oil recovery and management.
- Direct, induced draft, counter-flow cooling tower sized to meet the entire heat rejection requirements of the system.
- Class T mechanical room, prefabricated and installed in an addition to the building.
Performance | Annual Energy Consumption (kWh) | Required Power* (kW) | ||
---|---|---|---|---|
Refrigeration COP | 2.36 | Refrigeration | 407,038 | 180 |
Heating COP | 7.63 | Heating | 77,088 | |
Combined COP | 2.67 | Total | 484,186 |
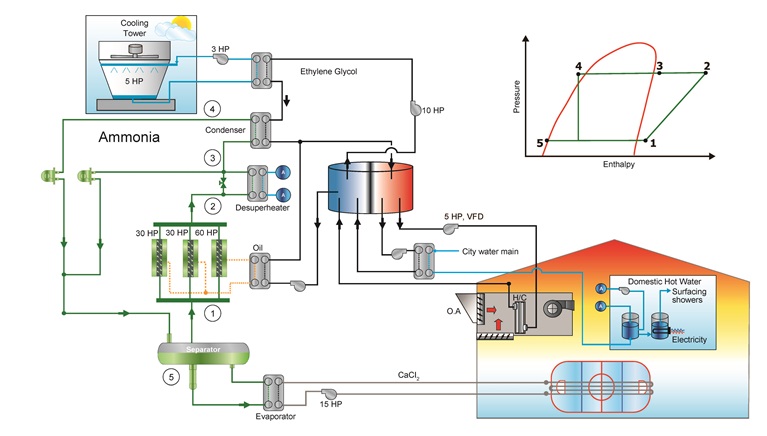
Diagram A1: Open packaged system with stratified thermal storage
Text Version
Diagram A1: Open packaged system with stratified thermal storage
The diagram shows the system A1, an open package system with stratified thermal storage. It is a packaged ammonia refrigeration system, with open screw compressors, installed on a steel base. It operates without a refrigerant receiver, and the refrigerant is confined to the mechanical room. The evaporator is a titanium plat heat exchanger. The pumping system is modulated according to the required heating needs. The oil is automatically managed. A direct, induced draft, counter-flow cooling tower is sized to meet the entire heat rejection requirements of the system. The class T mechanical room is installed in an addition to the building.
System A2: Open Assembled System With Heat Hump, Concept: City of Montréal
SYSTEM DESCRIPTION
- Ammonia refrigeration system, open reciprocating compressors, assembled on-site on a concrete base.
- Functions without a refrigerant reservoir (114 kg or 1.6 kg/tonne of refrigeration), confined to the mechanical room.
- Evaporator: titanium plate heat exchanger.
- Increase refrigeration system efficiency by using a condenser temperature of 26oC, during heat recovery period and weather permitting.
- Heat pump to upgrade the total heat rejected from the system to satisfy space heating needs.
- Complete heat recovery from the refrigeration system: desuperheat from the compressor discharge, compressor oil coolerand the system condenser heat rejection.
- Indirect, induced draft, counter flow cooling tower sized to meet the entire heat rejection requirements of the system.
- Class T mechanical room integrated into the building.
- Closed loop oil recovery and management.
Performance | Annual Energy Consumption (kWh) | Required Power* (kW) | ||
---|---|---|---|---|
Refrigeration COP | 2.50 | Refrigeration | 383,354 | 198 |
Heating COP | 3.70 | Heating | 158,953 | |
Combined COP | 2.85 | Total | 542,308 |
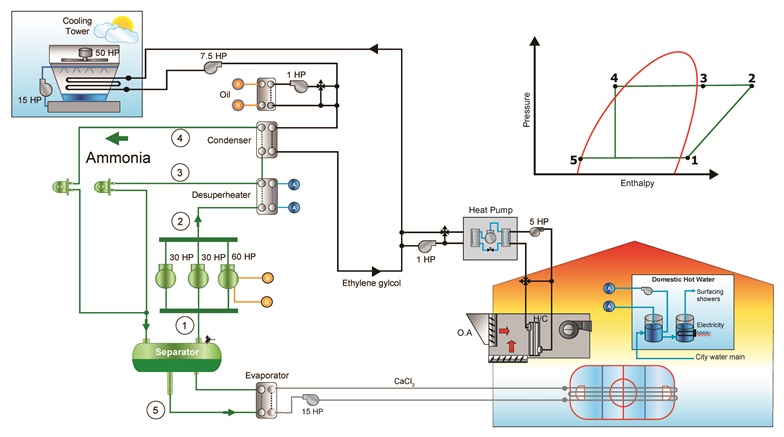
Diagram A2: Open assembled system with heat pump, concept of the City of Montréal
Text Version
Diagram A2: Open assembled system with heat pump, concept of the City of Montréal
The diagram shows the system A2, an open assembled system with heat pump. It is an ammonia refrigeration system, with open reciprocating compressors, installed on a concrete base. It operates without a refrigerant tank. The evaporator is a titanium plate heat exchanger. The system recovers entirely the heat. An indirect, induced draft, counter flow cooling tower is sized to meet the entire heat rejection requirements of the system. The class T mechanical room is integrated to the building. The oil is managed in a closed loop.
System A3: Open Assembled System With Heat Pump, Concept: Québec City
SYSTEM DESCRIPTION
- Ammonia refrigeration system, open reciprocating compressors, assembled on-site on a cement base.
- Functions with refrigerant (273 kg or 3.6 kg/tonne of refrigeration) confined to the mechanical room.
- Evaporator: Plate heat exchanger made from type 254 stainless steel, austenitic stainless steel alloy resistant to chloride corrosion (stress, pitting and corrosion at the joints).
- Increase refrigeration system efficiency by using a 29oC condenser temperature, weather permitting.
- Heat pump to upgrade energy recovered by the system to meet space heating needs
- Complete heat recovery from the refrigeration system: desuperheat from the compressor discharge, compressor oil coolerand the system condenser heat rejection.
- Indirect, induced draft, counter-flow cooling tower sized to meet the entire heat rejection requirements of the system.
Performance | Annual Energy Consumption (kWh) | Required power* (kW) | ||
---|---|---|---|---|
Refrigeration COP | 2.22 | Refrigeration | 453,590 | 210 |
Heating COP | 3.20 | Heating | 183,555 | |
Combined COP | 2.51 | Total | 637,145 |
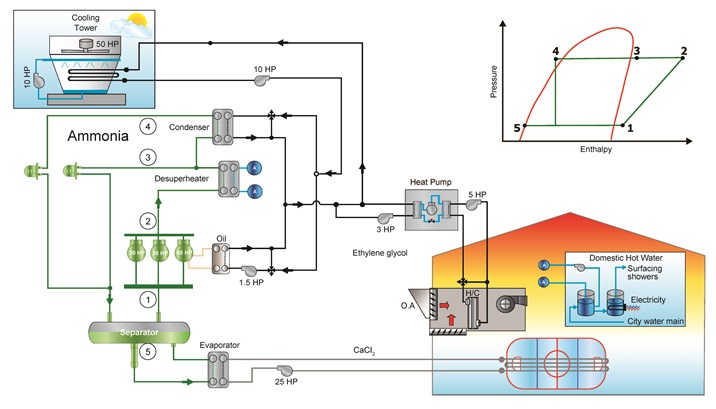
Diagram A3: Open assembled system with heat pump, concept of Québec City
Text Version
Diagram A3: Open assembled system with heat pump, concept of Québec City
The diagram shows the system A3, an open assembled system with heat pump. It is an ammonia refrigeration system with open reciprocating compressors, installed on a cement base. It operates without a refrigerant tank; the system is confined to the mechanical room. The evaporator is a plate heat exchanger. A heat pump upgrades the energy recovered by the system to meet space heating needs. The refrigeration system completely recovers the heat. An indirect, induced draft, counter-flow cooling tower is sized to meet the entire heat rejection requirements of the system. The class T mechanical room is integrated into the building.
System A4: Open Packaged System With Economiser Port on the Compressors
SYSTEM DESCRIPTION
- Packaged ammonia refrigeration system, open screw compressor, factory assembled on a steel base.
- Operates with a refrigerant charge (320 kg or 4 kg/tonne of refrigeration) that is confined to the mechanical room.
- Evaporator: Plate heat exchanger from stainless steel.
- Increase refrigeration system efficiency by using a 21°C condenser temperature, weather permitting.
- Increased refrigeration system efficiency due to operation using the economiser port on the screw compressors.
- Thermal energy storage permitting the optimisation floating head pressure control of the refrigeration system while capable of meeting the space heating demands
- Complete heat recovery from the refrigeration system: desuperheat from the compressor discharge, compressor oil coolerand the system condenser heat rejection.
- Secondary heat transfer fluid for the rink cement slab: 35% ethylene glycol solution.
- Direct, induced draft, counter-flow cooling tower sized to meet the entire heat rejection requirements of the system Class T mechanical room, prefabricated and installed in an addition to the building.
Performance | Annual Energy Consumption (kWh) | Required power* (kW) | ||
---|---|---|---|---|
Refrigeration COP | 2.33 | Refrigeration | 453,590 | 179 |
Heating COP | 7.78 | Heating | 183,555 | |
Combined COP | 3.17 | Total | 637,145 |
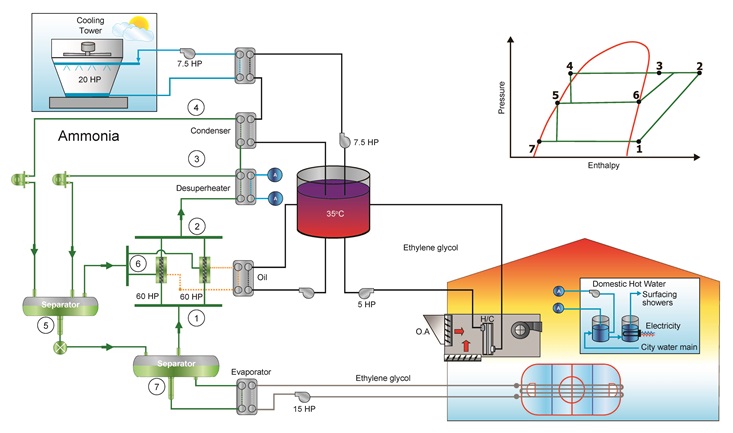
Diagram A4: Open packaged system with economiser port on the compressors
Text Version
Diagram A4: Open packaged system with economiser port on the compressors
The diagram shows the system A4, an open packaged system with economiser port on the compressors. It is a packaged ammonia refrigeration system, with open screw compressor, installed on a steel base. It operates with a refrigerant charge of 320 kg; the system is confined to the mechanical room. The evaporator is a plate exchanger from stainless steel. The system completely recovers the heat waste. A 35% ethylene glycol solution is used as a secondary heat transfer fluid for the rink cement slab. A direct, induced draft, counter-flow cooling tower is sized to meet the entire heat rejection requirements of the system. The class T mechanical room is installed in an addition to the building.
System A5: Open Packaged System With Efficient Reciprocating Compressors
SYSTEM DESCRIPTION
- Ammonia refrigeration system, open reciprocating compressors, factory built package system built on a steel base.
- Operates with refrigerant charge (230 kg or 3 kg/tonne of refrigeration) confined to the mechanical room.
- Evaporator: Plate heat exchanger in stainless steel.
- Increase refrigeration system efficiency by using a 21°C condenser temperature, weather permitting.
- Thermal energy storage permitting the optimisation of the system operating pressure while meeting the space heating demands.
- Complete heat recovery from the refrigeration system: desuperheat from the compressor discharge, compressor oil coolerand the system condenser heat rejection.
- Secondary thermal heat transfer fluid for the concrete slab: 35% solution of ethylene glycol.
- Direct, induced draft, counter-flow cooling tower sized to meet the entire heat rejection requirements of the system.
- Class T mechanical room, prefabricated and installed in an annex to the building.
Performance | Annual energy consumption (kWh) | Required power* (kW) | ||
---|---|---|---|---|
Refrigeration COP | 2.15 | Refrigeration | 446,417 | 171 |
Heating COP | 21.49 | Heating | 27,357 | |
Combined COP | 3.27 | Total | 473,774 |
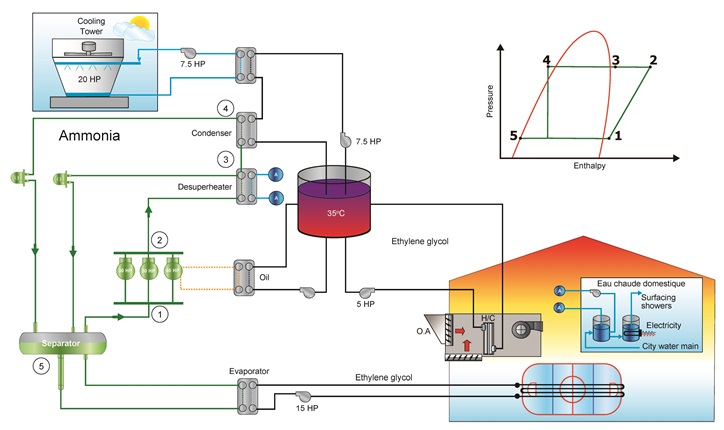
Diagram A5: Open packaged system with efficient reciprocating compressors
Text Version
Diagram A5: Open packaged system with efficient reciprocating compressors
The diagram shows the system A5, an open packaged system with efficient reciprocating compressors. It is an ammonia refrigeration system, with open reciprocating compressors, installed on a steel base. It operates with a refrigerant charge of 230 kg; the system is confined to the mechanical room. The evaporator is a plate heat exchanger in stainless steel. Thermal energy storage allows optimizing the system operating pressure while meeting the space heating demands. The system recovers completely recovers the heat waste. A 35% ethylene glycol solution is used as a secondary thermal heat transfer fluid for the rink concrete slab. A direct, induced draft, counter-flow cooling tower is sized to meet the entire heat rejection requirements of the system. The class T mechanical room is installed in an addition to the building.
System C1: Semi-hermetic Split Packaged System with Direct Evaporation in the Rink Slab.
SYSTEM DESCRIPTION
- Split-packaged R-744 (CO2) refrigeration system: semi-hermetic reciprocating compressor, factory assembled on a steel base.
- Operation at high pressure (transcritical cycle) with a refrigerant charge of 1,591 kg (20 kg/tonne of refrigeration) that circulates directly under the rink slab.
- Refrigerant (CO2) flows directly under the rink slab, which acts as the evaporator.
- Uniform ice temperature at a colder temperature due to the direct heat transfer between the CO2 and the rink slab.
- Minimal pumping power used to pump the CO2 under the rink slab.
- Normal operating pressure of 75 bars (1087 psi) controlled to prioritize heat recovery for heating requirements while minimizing the compressor energy consumption.
- Gas cooler sized to meet the entire heat rejection requirements of the system
- An auxiliary refrigeration system is added to ensure the critical system pressure is maintained in case of shut down.
Performance | Annual Energy Consumption (kWh) | Required Power* (kW) | ||
---|---|---|---|---|
Refrigeration COP | 3.09 | Refrigeration | 291,083 | 181 |
Heating COP | 6.50 | Heating | 90,479 | |
Combined COP | 3.90 | Total | 381,562 |
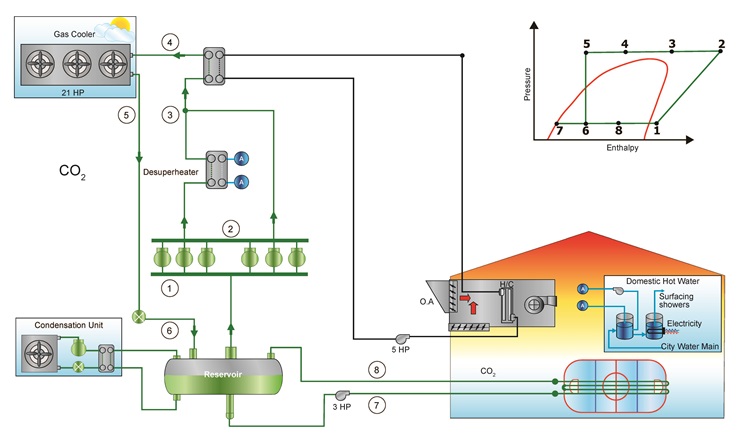
Diagram C1: Semi-hermetic split packaged system with direct evaporation in the rink slab
Text Version
Diagram C1: Semi-hermetic split packaged system with direct evaporation in the rink slab
The diagram shows the system C5, a semi-hermetic split packaged system with direct evaporation in the rink slab. It is a split-packaged R-744 refrigeration system, with semi-hermetic reciprocating compressor, installed on a steel base. It operates at high pressure (transcritical cycle) with a refrigerant charge of 1,591 kg that circulates directly under the rink slab. The CO2 refrigerant flows directly under the rink slab, which acts as the evaporator. Minimal pumping power is used to pump the CO2 under the rink slab. A gas cooler is sized to meet the entire heat rejection requirements of the system. An auxiliary refrigeration system is added to ensure the critical system pressure is maintained in case of shut down.
System C2: Semi-hermetic Split-package System with Direct CO2 Space Heating
SYSTEM DESCRIPTION
- Split-packaged R-744 (CO2) refrigeration system with semi-hermetic reciprocating compressors, factory assembled on a steel base.
- Operates at high pressure (transcritical cycle) with a refrigerant charge of 500 kg (6.5 kg/tonne of refrigeration). Hot gas is circulated directly to the space heating equipment in the arena
- Evaporator: stainless steel shell and plate heat exchanger.
- Operating pressure controlled as a function of the outdoor temperature to meet the heating needs and minimize compressor energy consumption.
- Space heating in perimeter spaces accomplished directly through a CO2 stainless steel coil heat exchanger installed in the air handling unit eliminating the need for a secondary pumping system.
- Gas cooler sized to meet the entire heat rejection requirements of the system.
- On-site laser welding reduces the risk of CO2 leakage into the arena.
- System may be shut down at any time without requiring an auxiliary cooling unit to maintain the system pressure.
Performance | Annual Energy Consumption (kWh) | Required Power* (kW) | ||
---|---|---|---|---|
Refrigeration COP | 2.56 | Refrigeration | 374,455 | 188 |
Heating COP | 19.80 | Heating | 29,692 | |
Combined COP | 3.83 | Total | 404,147 |
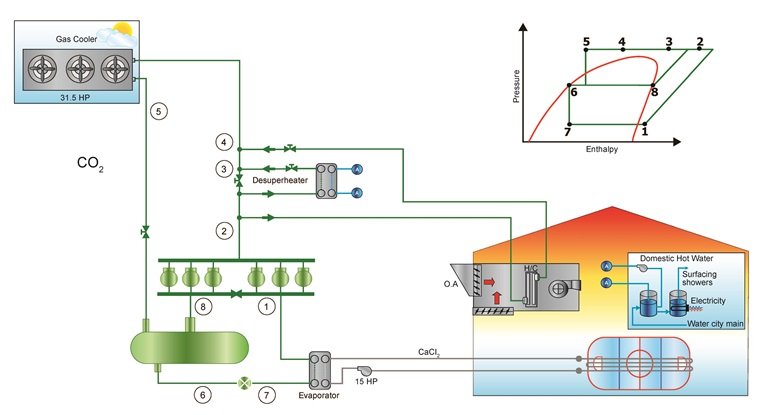
Diagram C2: Semi-hermetic split-packaged system with direct CO2 space heating
Text Version
Diagram C2: Semi-hermetic split-packaged system with direct CO2 space heating
The diagram shows the system C2, a semi-hermetic split-packaged system with direct CO2 space heating. It is a split-packaged R-744 refrigeration system with semi-hermetic reciprocating compressors, installed on a steel base. It operates at high pressure (transcritical cycle) with a refrigerant charge of 500 kg. Hot gas circulates directly in the space heating equipment in the arena. The evaporator has a stainless steel shell and a plate heat exchanger. Operating pressure is controlled as a function of the outdoor temperature to meet the heating needs and minimize the compressor energy consumption. Space heating in perimeter spaces is accomplished directly through a CO2 stainless steel coil heat exchanger installed in the air handling unit, thus eliminating the need for a secondary pumping system. A gas cooler is sized to meet the entire heat rejection requirements of the system. On-site laser welding reduces the risk of CO2 leakage into the arena.
H1 System: Traditional Open System with Electric Space and DHW Heating
SYSTEM DESCRIPTION
- R-22 refrigeration system, open reciprocating compressors, assembled on-site on a cement base.
- System operates with a refrigerant charge of 409 kg (5 kg/tonne of refrigeration) circulating between the arena, mechanical room and rooftop air condenser.
- Stainless steel shell and tube evaporator.
- No heat recovery on the condenser heat rejection.
- Recovery on the desuperheat for domestic hot water preheating.
- Liquid receiver at the condenser exit.
Performance | Annual energy consumption (kWh) | Required power* (kW) | ||
---|---|---|---|---|
Refrigeration COP | 1.83 | Refrigeration | 550,247 | 381 |
Heating COP | 1.25 | Heating | 469,330 | |
Combined COP | 1.57 | Total | 1,019,576 |
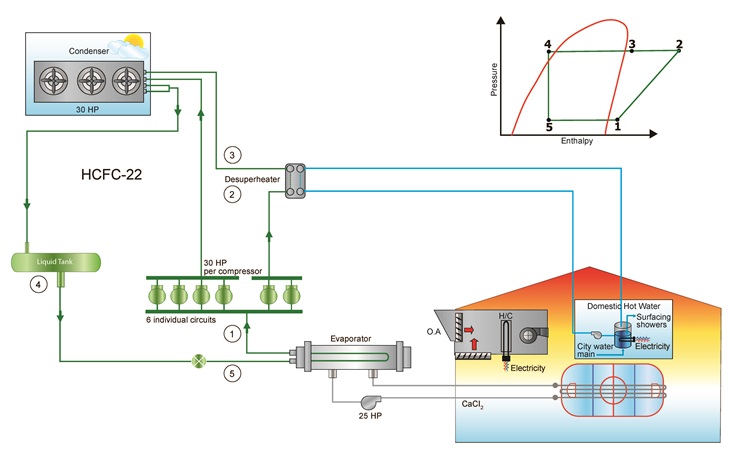
Diagram H1: Traditional open system with electric space and domestic hot water heating
Text Version
Diagram H1: Traditional open system with electric space and domestic hot water heating
The diagram shows the system H1, a traditional open system with electric space and domestic hot water heating. It is an R-22 refrigeration system, with open reciprocating compressors, installed on a cement base. It operates with a refrigerant charge of 409 kg, which circulates between the arena, the mechanical room and the rooftop air condenser. The evaporator is a stainless steel shell and tube. The system recovers heat waste with a desuperheater for domestic hot water preheating. A liquid receiver is located at the condenser exit.
H2 System: Packaged Semi-hermetic System with Economiser Port on Compressors
SYSTEM DESCRIPTION
- Packaged R507a refrigeration system, semi-hermetic screw compressors, factory assembled on a steel base.
- Operates with a reduced refrigeration charge (114 kg or 1.3 kg/tonne of refrigeration) confined to the mechanical room.
- Evaporator: titanium plate heat exchanger.
- Increased efficiency of semi-hermetic screw compressors due to use of the economiser port.
- Thermal energy storage permitting the optimisation of the system operating pressure and meeting the space heating demands.
- Complete heat recovery from the refrigeration system: desuperheat from the compressor discharge and the system condenser heat rejection.
- Dry fluid cooler sized to meet the entire heat rejection requirements of the system.
Performance | Annual Energy Consumption kWh) | Required Power* (kW) | ||
---|---|---|---|---|
Refrigeration COP | 2.05 | Refrigeration | 468,361 | 197 |
Heating COP | 5.80 | Heating | 101,326 | |
Combined COP | 2.72 | Total | 569,686 |
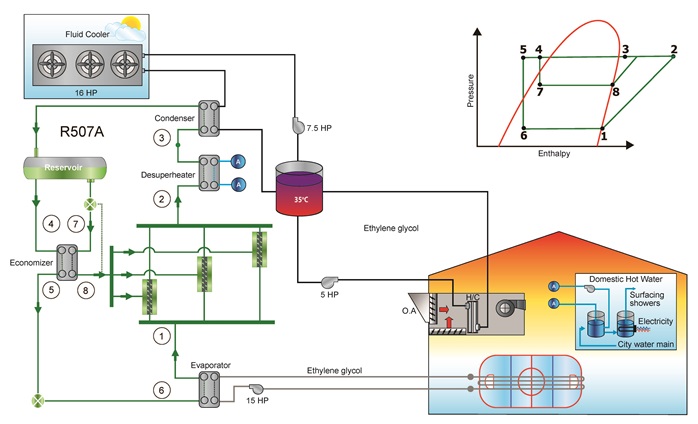
Diagram H2: Packaged semi-hermetic system with economiser port on compressors
Text Version
Diagram H2: Packaged semi-hermetic system with economiser port on compressors
The diagram shows the system H2, a packaged semi-hermetic system with economiser port on compressors. It is a packaged R507a refrigeration system, with semi-hermetic screw compressors, installed on a steel base. It operates with a reduced refrigeration charge, confined to the mechanical room. The evaporator is a titanium plate heat exchanger. Thermal energy storage allows optimizing the system operating pressure and meeting the space heating demands. The system completely recovers the heat waste. A dry fluid cooler is sized to meet the entire heat rejection requirements of the system.
H3 System: Hermetic Modular System with Heat Pumps
SYSTEM DESCRIPTION
- R-410A refrigeration system, hermetic scroll compressor, packaged and factory assembled on a steel base.
- Modular refrigeration system, factory assembled, verified, charged with refrigerant and tested.
- Evaporator: stainless steel plate heat exchangers integrated in the factory assembled system.
- Excellent sealing against refrigerant leaks requiring little maintenance.
- Runs with a small refrigerant charge (45 kg or 0.6 kg/tonne of refrigeration), confined within the factory assembled system installed in the mechanical room.
- Complete heat recovery from the refrigeration system accomplished through one heat exchanger: desuperheat from the compressor discharge and the system condenser heat rejection.
- Methanol is used as the secondary refrigeration fluid.
- Dry fluid cooler sized to meet the entire heat rejection requirements of the system.
- Can be linked to a geothermal system.
- Easy to operate.
Performance | Annual energy consumption (kWh) | Required power* (kW) | ||
---|---|---|---|---|
Refrigeration COP | 1.68 | Refrigeration | 554,608 | 225 |
Heating COP | 5.86 | Heating | 100,377 | |
Combined COP | 2.32 | Total | 654,985 |
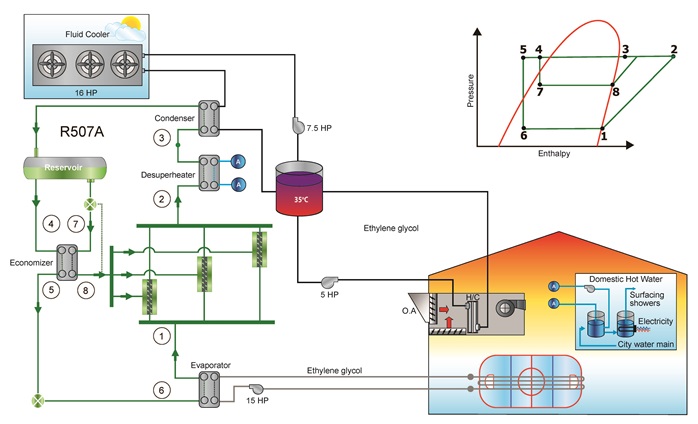
Diagram H3: Hermetic modular system with heat pumps
Text Version
Diagram H3: Hermetic modular system with heat pumps
The diagram shows the system H3, a hermetic modular system with heat pumps. It is a R-410A refrigeration system, with hermetic scroll compressor, installed on a steel base. The modular refrigeration system is charged with refrigerant. The evaporator is a stainless steel plate exchanger integrated into the system. It runs with a small refrigerant charge, which is confined to the mechanical room. The system recovers the heat waste. Methanol is used as the secondary refrigeration fluid. A dry fluid cooler is sized to meet the entire heat rejection requirements of the system.
H4 System: Modular Semi-hermetic System with Stratified Thermal Storage
SYSTEM DESCRIPTION
- Packaged R-507a refrigeration system, factory assembled on a steel base.
- Packaged modular units with semi-hermetic screw compressors.
- Operates with 100 kg of refrigerant (1.3 kg/tonne refrigeration) confined within the factory assembled system located in the mechanical room.
- Evaporator: stainless steel plate heat exchangers integrated into the modular units.
- Stratified thermal storage allowing for the optimisation of the refrigeration system operating pressure to balance the heating and cooling energy demand and prioritizing the heating demands.
- Pumping system modulates according to the heating demand.
- Complete heat recovery from the refrigeration system accomplished through one heat exchanger: desuperheat from the compressor discharge and the system condenser heat rejection.
- Secondary heat transfer fluid: 35% ethylene glycol.
- Efficient, dry fluid cooler sized to meet the heat rejection requirements of the system.
- Easy to operate.
Performance | Annual Energy Consumption(kWh) | Required Power (kW) | ||
---|---|---|---|---|
Refrigeration COP | 2.03 | Refrigeration | 485,485 | 192 |
Heating COP | 3.84 | Heating | 153,013 | |
Combined COP | 2.46 | Total | 638,498 |
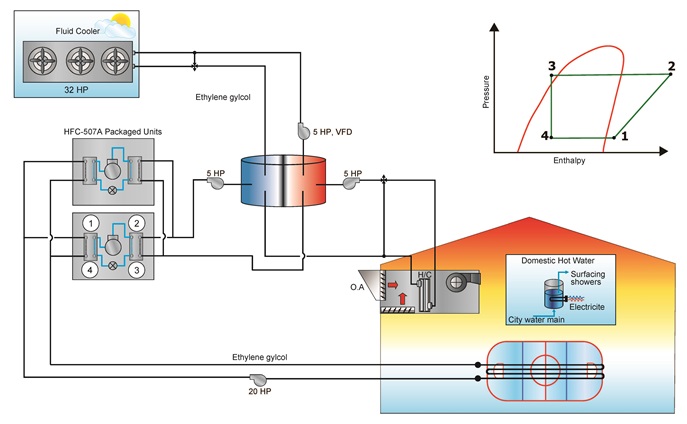
Diagram H4: Modular semi-hermetic system with stratified thermal storage
Text Version
Diagram H4: Modular semi-hermetic system with stratified thermal storage
The diagram shows the system H4, a modular semi-hermetic system with stratified thermal storage. It is a packaged R-507a refrigeration system, installed on a steel base. The packaged modular units have semi-hermetic screw compressors. It operates with 100 kg of refrigerant, confined to the mechanical room. The evaporator is a stainless steel plate heat exchanger integrated into the modular units. The system recovers the heat waste. It uses a 35% ethylene glycol as secondary heat transfer fluid. A dry fluid cooler is sized to meet the heat rejection requirements of the system.
H5 System: Packaged Semi-hermetic System with Heat Pumps for Water Heating
SYSTEM DESCRIPTION
- Mass produced, packaged R-134a refrigeration system: variable capacity, semi-hermetic screw compressors.
- Factory built, assembled, charged with refrigerant and tested.
- Very compact design reduces the refrigerant charge and has good sealing against refrigerant leaks.
- Operates with 166 kg of refrigerant (21 kg/tonne refrigeration) confined within the factory assembled system located in the mechanical room.
- Two completely independent refrigeration circuits are used thereby eliminating the risk of losing some of its charge and ensuring redundancy.
- This type of system requires no mechanical room modifications, except for perhaps installing a double door to get the system into the mechanical room.
- Any type of coolant is permitted.
- Heat pump is used for heating domestic hot water and for ice surfacing.
- Complete heat recovery from the refrigeration system accomplished through one heat exchanger: desuperheat from the compressor discharge and the system condenser heat rejection.
- The chilled secondary fluid can be stored in geothermal boreholes and/or ice storage tanks.
- Efficient dry fluid cooler sized to meet the heat rejection requirements of the system.
- Easy to operate.
Performance | Annual Energy Consumption (kWh) | Required Power* (kW) | ||
---|---|---|---|---|
Refrigeration COP | 1.85 | Refrigeration | 518,610 | 208 |
Heating COP | 9.52 | Heating | 61,771 | |
Combined COP | 2.67 | Total | 580,381 |
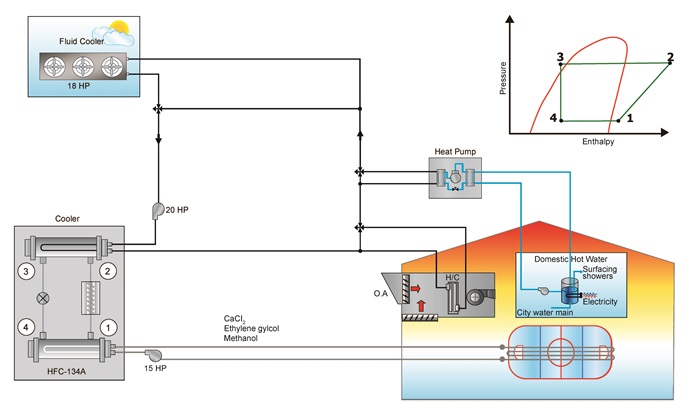
Diagram H5: Packaged semi-hermetic system with heat pumps for water heating
Text Version
Diagram H5: Packaged semi-hermetic system with heat pumps for water heating
The diagram shows the system H5, a packaged semi-hermetic system with heat pumps for water heating. It is a R-134a refrigeration system with variable capacity and semi-hermetic screw compressors and charged with refrigerant. It operates with 166 kg of refrigerant, which is confined to the mechanical room. The system uses two completely different refrigerant circuits. The system recovers heat waste. An efficient dry fluid cooler is sized to meet the heat rejection requirements of the system.
APPENDIX 2: SUMMARY OF SYSTEM WARRANTIES
IDENTIFICATION | GUARANTIES INCLUDED WITH THE SYSTEM | EXTENDED GUARANTIES | ||||||
---|---|---|---|---|---|---|---|---|
Case | Assembly Type |
Refrigerant | Parts | Labour | Compressors | Refrigerant | System | Compressors |
Duration | Duration | Duration | Duration | Duration/price | Duration/price | |||
A1 | Packaged | R717 | 1 an | 1 an | 1 an | 1 an | Not available | Not available |
A2 | On site | R717 | 1 an | 1 an | Not available | Not available | ||
A3 | On site | R717 | 1 an | 1 an | Not available | Not available | ||
A4 | Packaged | R717 | 1 an | 1 an | 1 an | 1 an | 2 years / $4,000 | 2 years / $4,000 |
A5 | Packaged | R717 | 1 an | 1 an | 1 an | 1 an | Not available | Not available |
C1 | Split-packaged | CO2 | 1 an | 1 an | 1 an | 1 an | Not available | Not available |
C2 | Split-packaged | CO2 | 1 an | 1 an | 1 an | 1 an | 1 years / $11,000 | 1 years / $6,000 |
H1 | On site | HCFC-R22 | 1 an | 1 an | Not available | Not available | ||
H2 | Packaged | HFC-R507A | 1 an | 1 an | 1 an | 1 an | 2 years / $1,500 | 2 years / $1,500 |
H3 | Modular | HFC-R410A | 1 an | 1 an | 1 an | 1 an | 5 years / $6,000 | Not available |
H4 | Modular | HFC-R507A | 1 an | 1 an | 1 an | 1 an | Not available | Not available |
H5 | Packaged | HFC-R134A | 1 an | 1 an | 1 an | 1 an | 10 years / $30,000 | Not available |
APPENDIX 3: ENERGY CONSUMPTION RESULTS FOR AN ICE RINK OPERATING FOR 12 MONTHS
Case | IDENTIFICATION | MAIN ENERGY CONSUMPTION FEATURES | |||||||
---|---|---|---|---|---|---|---|---|---|
Refrigerant | energy consumption for 9 months (kWh/an) |
Variations | energy consumption for 12 months (kWh/an) |
Variations | |||||
Refrigeration | Heating | Total | % | Refrigeration | Heating | Total | % | ||
A1 | R717 | 407,000 | 77,100 | 484,100 | -11% | 491,300 | 103,000 | 594,300 | -14 |
A2 | R717 | 383,400 | 159,000 | 542,300 | 0% | 511,200 | 176,100 | 687,400 | 0 |
A3 | R717 | 453,600 | 183,600 | 637,100 | 17% | 599,000 | 203,700 | 802,700 | 17 |
A4 | R717 | 412,200 | 75,600 | 487,800 | -10% | 505,600 | 100,300 | 605,900 | -12 |
A5 | R717 | 446,400 | 27,400 | 473,800 | -13% | 545,700 | 38,700 | 584,400 | -15 |
C1 | R744 | 291,100 | 90,500 | 381,600 | -30% | 365,200 | 107,400 | 472,600 | -31 |
C2 | R744 | 374,500 | 29,700 | 404,100 | -25% | 488,200 | 39,100 | 527,300 | -23 |
H1 | HCFC-R22 | 550,200 | 469,300 | 1,019,600 | 88% | 774,800 | 478,400 | 1,253,200 | 82 |
H2 | HFC-R507A | 468,400 | 101,300 | 569,700 | 5% | 583,200 | 117,100 | 700,300 | 2 |
H3 | HFC-R410A | 554,600 | 100,400 | 655,000 | 21% | 656,700 | 139,000 | 795,600 | 16 |
H4 | HFC-R507A | 485,500 | 153,000 | 638,500 | 18% | 616,300 | 200,700 | 817,100 | 19 |
H5 | HFC-R134A | 518,600 | 61,800 | 580,400 | 7% | 650,800 | 84,900 | 735,700 | 7 |
APPENDIX 4: SUMMARY REPORT ON RISKS ASSOCIATED WITH THE USE OF AMMONIA IN ARENAS
Summary Report on Preventive Measures and Mitigation Concerning Risks Associated with Use of Ammonia in Arenas
Jean-Paul Lacoursière, Eng., Stéphanie Lacoursière, Eng., M. Eng.
JP Lacoursière inc.
35, rue Lemoyne, Repentigny, (Québec) Canada J6A 3L4
T : (450)-581-2315; C : (514) 770-2315; F : (450) 581-4539
E-mail : jpla@sympatico.ca
Report No. P00459-1-AB-rev0
This summary report is an overview of the full report, of the same title, published on March 31, 2013 for the benefit of Natural Resources Canada – Buildings Group – CANMET Center for Energy Technology - 1615, boul. Lionel-Boulet, C.P. 4800, Varennes QC J3X 1S6 under contract 3000506842.
Executive Summary
Ammonia can be a safe refrigerant for arena refrigeration systems when facilities are well designed and operated. The study shows that during a leak in the class T machinery room, vapours from fans from this room can affect the population surrounding the arena. The use of fans with upwardly directed outlets, internal dilution and an exhaust velocity of 25 m/s can overcome this problem. It is however recommended to do a « What-if? » hazard study and in some cases an ammonia release simulation to properly identify problems and design facilities accordingly. In addition, a process safety management program which takes into account the maintenance and emergency plans must be put into place.
Used for over 130 years as a refrigerant, ammonia was gradually supplanted by chlorofluorocarbons (CFC), but is now regaining importance since the adoption of the Montreal and Kyoto protocols, which seek a total ban of CFCs over the next 10 years. Ammonia systems resume their place because they are effective and represent a long-term solution for sustainable development of the arena sector. However, special care and precautions must be taken in order to make safe use of these systems.
Ammonia refrigeration facilities for arenas must respect at least all relevant clauses of the B52-05 Mechanical Refrigeration Code and other relevant laws and regulations, like the Regulation on Health and Work Safety in Quebec. The objective of this study is to identify how to design and to operate inherently safer facilities than what the ammonia refrigeration code predicts, considering that arenas are integrated with their surroundings and are frequented by vulnerable populations, including children.
Figure 1 shows an ammonia-refrigerated flooded system (ammonia-filled vaporizer) with shell and tubes heat exchanger used to cool brine that runs under the slab supporting ice, a large high-pressure tank, 3 compressors and an evaporative condenser. The illustrated system contains 568 kg (1,250 lbs) of ammonia. In the event of a loss of containment, the high ammonia inventory could lead to toxic ammonia concentrations reaching significant distances and could affect residents near the arena.
The ammonia refrigeration industry envisioned to reduce these inventories by using critical load refrigeration systems. A critical load refrigeration system is characterized by the fact that the refrigerant load is limited so it is impossible for the liquid refrigerant to be drawn into the suction line of the compressor or compressors, when the entire load is in the evaporator.
Figure 2 shows a critical load system. A plate heat exchanger, which is much more compact than a shell and tube heat exchanger, is used to cool brine. The illustrated case has an ammonia inventory of 114 kg (250 lbs) vs. 568 kg (1250 lbs) for a conventional system. In case of loss of containment, the quantity of ammonia that would be liberated would be far smaller and the distances for the toxic concentrations should also be shorter.
Ammonia in liquid or gaseous form is colorless. The gas is toxic but has a strong odour that allows detection of its presence. Even though the gas is usually lighter than air, vapours from leaking liquid initially remain on the ground before they heat up. Contact with liquid may cause frostbite. It is assumed that the gas is not flammable. However, it can burn within a certain range of concentrations in the presence of a strong ignition source. Fire hazards increase in the presence of oil or other fuel. Exposure of an ammonia tank under pressure to a fire can cause its explosion by producing a BLEVE (tank explosion with fireball, flying debris, shock wave and toxic cloud). Long-term exposures to low concentrations of ammonia or short-term exposures to high concentrations of ammonia may have effects on health.
Reference Values of Concentrations in Air
Two reference values for concentration of ammonia in air can be used to determine the consequences for those exposed: The Acute Exposure Guideline Levels (AEGLs) of the US-EPA and the Emergency Response Planning Guidelines (ERPG) of the American Industrial Hygiene Association (AIHA). The AEGL2 and ERPG2 are usually used to identify areas that should have emergency planning.Footnote 2
Identified Accidents
Several accidental releases of ammonia occurred at refrigeration facilities including those used in arenas. These releases of ammonia resulted from several causes including processes upsets with opening of safety relief valve, leaks on pump mechanical seals, compressors, valves, etc.
Elements for the Design of a Fail-Safe System for Arenas
The objectives to pursue in order to achieve inherently safe ammonia refrigeration installations are:
- Identify and assess hazards (equipment, operation modes, etc.) associated with the accidental release of ammonia.
- Develop safe facilities to prevent such releases.
- Operate facilities and train staff to prevent the release of ammonia.
- Mitigate the consequences of releases of ammonia if they occur.
To reach these objectives, one must proceed systematically by preforming the following three steps:
- Perform a hazard analysis;
- Model leak scenarios as required in order to asses resulting consequences; and,
- Implement measures to reduce risks.
Hazards Study
A hazards study is a systematic evaluation to identify dangerous situations associated with a process in order to evaluate its importance. The What-if? / Check-list Technique is appropriate to identify hazards in order to correct them. The International Institute for Ammonia Refrigeration (IIAR) has developed check-lists specifically for ammonia hazard studies.Footnote 3
Nearby residents or tall buildings overlooking the machinery room within 300 m would require the deployment of more elaborate prevention and intervention measures. Leak scenarios simulation using models which take into consideration leakage parameters, ventilation of the building as well as the behaviour of the ammonia cloud as a function of height (side view) and on the grounds (footprint) will provide insight to the appropriate decision-making. The PHAST software by Det Noske Veritas (DNV) permits this type of simulation while the ALOHA software by the Environmental Protection Agency (EPA) of the United States does not. Table 1 presents a number of measures that can be applied to design inherently safer installations. The choice of measures to be put into place will be dictated by the Hazards Study.
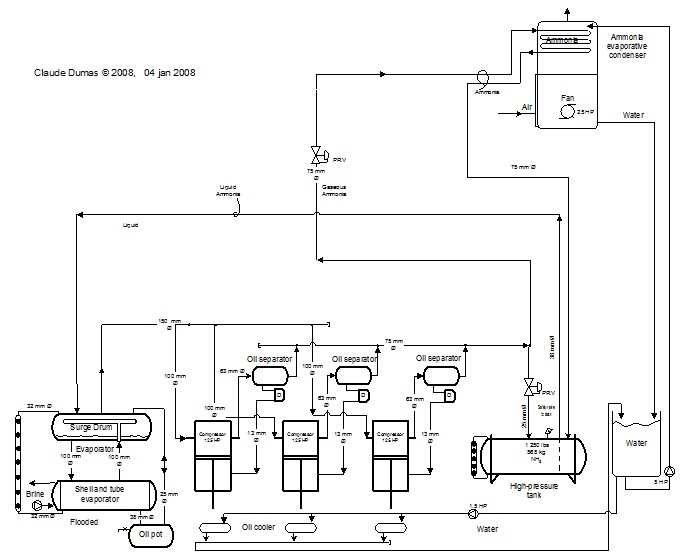
Appendix 4, Figure 1: Previous refrigeration system of the City of Montréal
Text Version
Appendix 4, Figure 1: Previous refrigeration system of the City of Montréal
The diagram shows an ammonia-refrigerated flooded system (ammonia-filled vaporizer) with shell and tubes heat exchanger used to cool brine that runs under the slab supporting ice, a large high-pressure tank, three compressors and an evaporative condenser. The system contains 568 kg of ammonia.
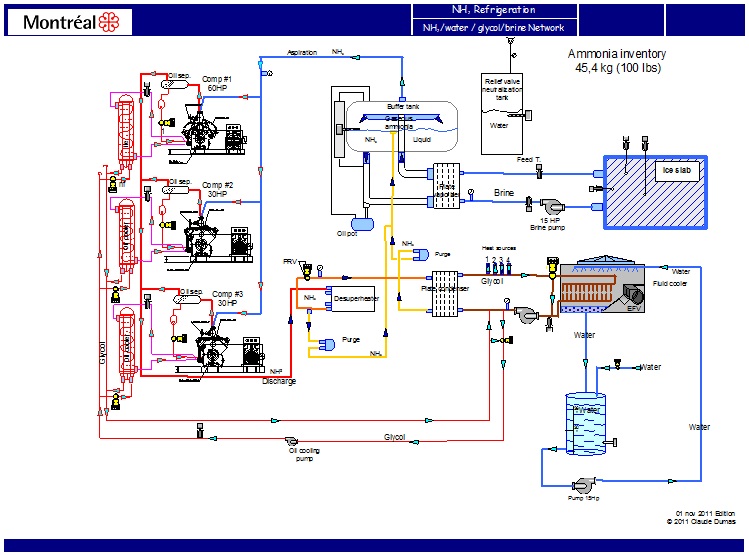
Appendix 4, Figure 2: Critical load ammonia refrigeration system of the City of Montréal
Text Version
Appendix 4, Figure 2: Critical load ammonia refrigeration system of the City of Montréal
The diagram shows a critical load system. A plate heat exchanger, which is much more compact than a shell and tube exchanger, is used to cool brine. The illustrated case has an ammonia inventory of 114 kg vs. 568 kg for a conventional system.
Typical Measures | Examples |
---|---|
|
|
|
|
|
|
|
|
|
|
|
|
|
|
|
|
|
|
|
|
|
|
|
|
|
|
An ammonia refrigeration system located inside a building must be installed in a class T machinery room. The air in the class T machinery room is to be discharged to the outside to control the temperature and also during ammonia leakage on equipment. Code B52-05 specifies the mathematical formulas for calculating the ventilation flow required for machinery rooms as well as other requirements.
The mechanical ventilation system must be properly designed to prevent re-entrainment of ammonia towards the ground or even the arena. Figure 3 taken from the ASHRAE HANBOOK 1999 illustrates the phenomena associated with the use of fans.

Appendix 4, Figure 3: Wake effects
Text Version
Appendix 4, Figure 3: Wake effects
The diagram shows the phenomena associated with the use of fans. The wind induces recirculation in two zones, firstly a roof recirculation zone and a secondly, the recirculation zone due to wake. These recirculation zones will trend the ammonia towards the ground.
The wind induces recirculation in two zones, firstly a roof recirculation zone and a secondly, the recirculation zone due to wake. These recirculation zones will tend to direct the ammonia towards the ground.
It is therefore necessary that the flow of ammonia from the fan detaches itself from the re-entrainment zones. This can be accomplished by pre-diluting it and providing sufficient upward gas velocity. The ANSI/IIAR 2-2008 specifies in article 13.3.7.1 « All exhaust fans shall discharge up vertically with a minimum discharge velocity of 12.7 m/s (2 500 FPM). »
This concept has unfortunately not been used in most refrigeration facilities that the author studied. It was noted in many instances that the fan exhaust is directed towards the ground or at the ground level which represents an exposure potential for people in the area. The following pictures show facilities that increase exposure potential in the case of an ammonia release.
Figure 4 shows a fan which directs the exhaust towards the roof. The presence of a nearby wall creates a recirculation zone due to the wake effect which accentuates the drawdown of the gas towards the ground. Simulations revealed that residents of the duplexes shown in the background of the photo are potentially exposed to concentrations of ammonia that could affect their health.
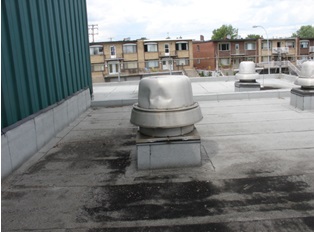
Appendix 4, Figure 4: Emergency exhaust vent towards the ground
Text Version
Appendix 4, Figure 4: Emergency exhaust vent towards the ground
The picture shows a fan which directs the exhaust towards the roof. The presence of a nearby wall creates a recirculation zone due to the wake effect which accentuates the drawdown of the gas towards the ground.
Figure 5 shows a side view of a simulation of an ammonia cloud with an emergency fan exhaust directed towards the ground.
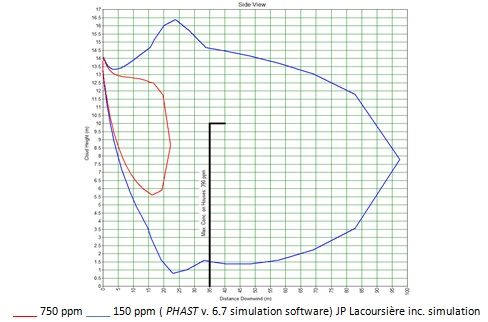
Appendix 4, Figure 5: Ammonia cloud with an emergency fan exhaust directed towards the ground
Text Version
Appendix 4, Figure 5: Ammonia cloud with an emergency fan exhaust directed towards the ground
The diagram shows a side view of a simulation of an ammonia cloud with an emergency fan exhaust directed towards the ground.
In this particular illustrated case, the ammonia cloud affects residents in the vicinity of the arena. The ammonia load of this refrigeration system is of 114 kg (250 lbs).
Figure 6 presents the same scenario as shown in Figure 5, except that the exhaust is directed vertically upwards with a discharge velocity of 26 m/s.
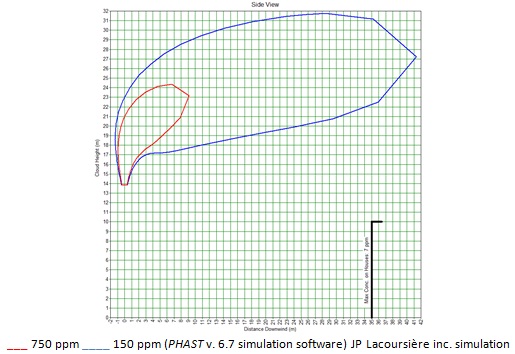
Appendix 4, Figure 6: Ammonia cloud with high velocity fan exhaust and internal dilution and a velocity of 26 m/s
Text Version
Appendix 4, Figure 6: Ammonia cloud with high velocity fan exhaust and internal dilution and a velocity of 26 m/s
The diagram shows a side view of a simulation of an ammonia cloud with an emergency fan exhaust directed vertically upwards with a discharge velocity of 26 m/s.
However, other arrangements should be made if there are tall buildings overlooking the class T machinery room nearby, including the use of a gas scrubber. There are several types of mechanical vents on the market with exhaust directed vertically upwards.
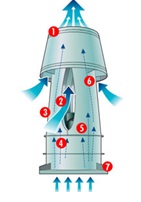
Appendix 4, Figure 7: Vertical mechanical fans with upwards directed outlet
Text Version
Appendix 4, Figure 7: Vertical mechanical fans with upwards directed outlet
The diagram shows the Strobic Tri-Stack fan, which facilitate the dilution of ammonia by sucking air into the fan and by their high discharge velocity.
Some fans like the Strobic Tri-Stack®Footnote 4or the Cook Model QMXVP/QMXHPVPFootnote 5 facilitate the dilution of ammonia by sucking air into the fan and by their high discharge velocity which meets the objective of the standard ANSI/IIAR 2-2008 and should reduce the impact on the ground.
We believe that these types of fan should be the norm for Quebec arenas with ammonia refrigeration system. Their incremental cost is justifiable and will allow more flexibility in the use of land near the arena.
Operational Safety Management
Safety of the ammonia refrigeration facilities requires a holistic management program. The elements of the program presented in the following paragraphs are based on recommended practices by IIAR. This program meets the objectives of the CSST FRIGO program. A summary of this program follows.
- Accountability: Appoint a person responsible for the prevention programs and emergency plans of the ammonia refrigeration facilities.
- Know the process: Keep the drawings and procedures up to date.
- Process hazards: Keep the list of process hazards up to date.
- Prestartup safety reviews: Make prestartup safety reviews of repairs or modifications to facilities before start up after prolonged shutdown.
- Management of changes: Establish a procedure for managing changes to facilities or procedures to ensure that compliant parts are used for maintenance.
- Management of contractors: Establish a procedure for managing contractors working in these facilities.
- Mechanical integrity: Establish a program to maintain the mechanical integrity of the equipment : preventive maintenance.
- Procedures: Develop critical operating and maintenance procedures.
- Training: Provide training for equipment operation, maintenance, emergency plan;
- Emergency plan: Develop an emergency plan that considers the population surrounding the facility, the personnel and the users of the arena. This plan covers communications provided to the population, alert, evacuation, sheltering, and response.
- Verifications: Make verifications of compliance of the program according to a set frequency.
Emergency Plan
- Develop an emergency plan that addresses the safety of the personnel, users of the arena and population surrounding the facility.
- In case of a major leak, the atmosphere inside the machinery room could become explosive. The presence of oil mist may reduce the lower explosive limit under ammonia’s lower explosive limit. Interrupt all power inside the class T machinery room with the exception of the ventilation system towards the outside because the power supply may cause the ignition of explosive gases. Ventilate before entering. It is better to liberate the atmosphere of ammonia present in the room than to maintain an explosive atmosphere.
- Plan on installing independent fan switches that are easily accessible inside and outside of the machinery room. The objective here is to keep the fans in operation when power is interrupted to the other equipment.
- Do not use the machinery room for the storage of equipment including combustible materials and chemicals.
- Control access to the machinery room.
- Establish an intervention procedure for ammonia leaks in the class T machinery room.
- Ensure that the emergency exists are identified.
- Ensure that a sign showing the information required by the code B052-05 is in place.
- Display diagrams showing the evacuation routes.
- Confine ammonia-contaminated water in case of leakage, or water used to spray the leak, and dispose in an approved facility.
- Display signs for no-smoking, no use of an open flame or no welding near the exits of the room.
Conclusions and Recommendations
This study identified the following eighteen recommendations:
- It is recommended that the work provider (e.g. the municipality) specify the requirement that the refrigeration system designer preforms a hazard study of the ammonia refrigeration system and report to the work provider and competent authorities.
- It is recommended to model the effects of ammonia release in the following cases :
Ammonia load ≥137 kg (300 lbs) Residents at a distance < 300 m or buildings overlooking the class T machinery room.Model ammonia release scenarios, with the objective to identify preventive measures and appropriate intervention. The modelling software should allow side view simulation of the cloud, with at least the software PHAST v 6.7 of Det Noske Veritas (DNV) and its later versions. The methodology is described in CRAIM 2007. - It is recommended to use a mechanical vent (extractor) with a vertical upwards exhaust, internal dilution and high exhaust velocity (26 m/s) as a minimum requirement for emergency ventilation of the class T machinery room. Note that the presence of tall buildings overlooking the class T machinery room at a short distance (<300 m) may require additional intervention measures including a scrubber.
- It is recommended to use a scrubber on the fan suction line when there are tall buildings overlooking the machinery room (< 300 m). It is recommended to confirm, by modelling plume behaviour, the appropriateness of applying the recommendation.Model ammonia release scenarios, with the objective to identify preventive measures and the appropriate response. The modelling software should allow side view simulation of the cloud, with at least the software PHAST v 6.7 of Det Noske Veritas (DNV) and its later versions. The methodology is described in CRAIM 2007. Ensure that the concentrations of NH3 of the ammonia solution to be disposed of not exceed the concentrations permitted by regulation.
- It is recommended to locate the ammonia condenser inside the class T machinery room when there is presence of surrounding residents (those present permanently or sporadically in homes, buildings, infrastructures e.g., schools, hospitals, shopping centres, bridges, footbridge, parks, etc.) located at a distance smaller than 300 m and to use a coolant to cool the condenser outside of the class T machinery room. It is recommended to confirm by modelling plume behavior the appropriateness of applying the recommendation. Model ammonia release scenarios, with the objective to identify preventive measures and the appropriate intervention. The modelling software should allow side view simulation of the cloud, with at least the software PHAST v 6.7 of Det Noske Veritas (DNV) and its later versions. The methodology is described in CRAIM 2007.
- Install at least two ammonia detectors per class T machinery room and position them on the ceiling, close to places with high probability of ammonia leak, e.g. compressors, plate coolers.
- Make sure that the equipment controls cannot automatically reset after a shutdown following ammonia detection, due to improper computer programming.
- Consider installing redundant chemical cell detectors for ammonia and infrared analyzers to increase reliability of the detection system in the event of high ammonia concentration.
- It is recommended to install plate exchangers made of titanium or another alloy capable of withstanding brine, semi or non-welded seam for the application of the brine cooler. A semi-welded plate cooler is safer and should be preferred.
- Consider installing, as required, an ammonia detector at the inlet of the ventilation system of the arena in order to shut down this system as soon as there is ammonia detection.
- Consider installing a closed circuit for oil drainage of the ammonia refrigeration circuit.
- Consider putting in place mechanisms to stop compressors and isolate by solenoid valves, the refrigeration system, upon detection of ammonia concentrations in excess of 250 ppm in the class T machinery room.
- Install a neutralization tank to receive the relief valves discharge to prevent the release of ammonia from this source.
- Ensure that the layout of the class T machinery room is consistent with Article 6.1.3 of the mechanical refrigeration code and offers a safe access to the equipment and fittings for troubleshooting and emergency response purposes.
- Separate the class T machinery room into two parts, an equipment room and a control/electricity room. Ensure that the control room and the engine control post be situated in a hermetic room separated from the class T machinery room to permit operation of remote equipment without exposure to ammonia.
- Ensure that equipment, valves and controls are identified in accordance with Article 5.11.3 of the Mechanical Refrigeration Code B52-05 to facilitate troubleshooting and response to an emergency. In addition, these identifications should be consistent with the flow diagrams and P&IDs of the refrigeration facilities.
- Ensure that a holistic program of process safety is in place including information on the process, hazard analysis, change management, mechanical integrity, management of contractors, training of operating and maintenance personnel, emergency plans, incident investigation, record of accidents and incidents and verification. Although equipment manufacturers provide a plan for the maintenance of the components of the refrigeration system, their plan targets mainly the life of equipment and non-civil security. Thus, conducting a risk analysis would lead to the creation of a more complete maintenance plan that would result not only on operating the lifetime of the equipment but also increasing the safety of the refrigeration system.
- Develop a training program on the safety of refrigeration systems sanctioned by the Order of Engineers of Quebec, to be distributed to designers of refrigeration systems. This program could be developed and distributed by an academic institution.
The following flowchart illustrates the process to follow for the selection of mitigation measures and modelling of accident scenarios that may be required.
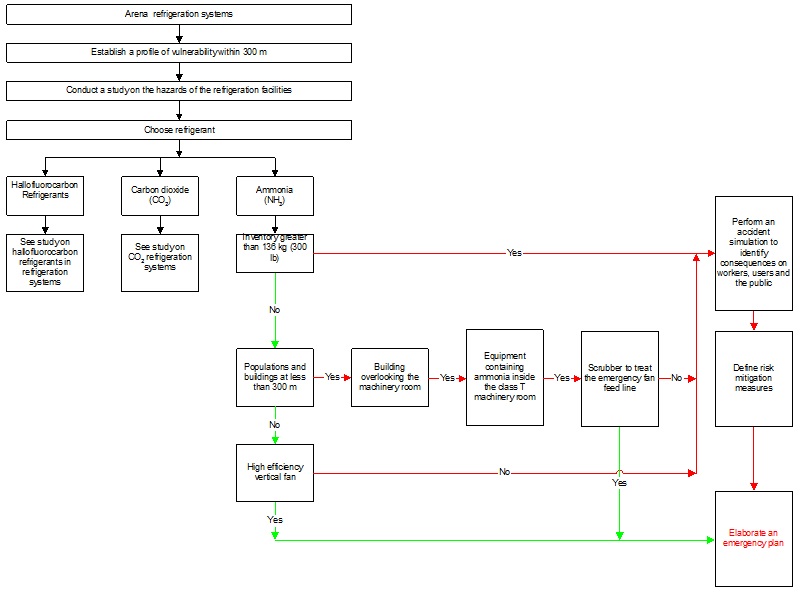
Appendix 4, Figure 8: The flowchart illustrates the process to follow for the selection of mitigation measures and modelling of accident scenarios that may be required.
Text Version
Appendix 4, Figure 8: The flowchart illustrates the process to follow for the selection of mitigation measures and modelling of accident scenarios that may be required.
The diagram shows the hazards study that must be done. It is a systematic evaluation to identify dangerous situations associated with a process in order to evaluate its importance.
Appendix 5: Technical Study of CO2 Arena Refrigeration
Technical Study of CO2 Arena Refrigeration for the Technical and Commercial Study Arena Refrigeration
Jean-Paul Lacoursière, Eng., Stéphanie Lacoursière, Eng., M. Eng.
JP Lacoursière inc.
35, rue Lemoyne, Repentigny, (Québec) Canada J6A 3L4
T : (450)-581-2315; C : (514) 770-2315; F : (450) 581-4539
E-mail : jpla@sympatico.ca
Report No. P00449-1-AB-rev0
This summary report is an overview of the full report of the same title published May 17, 2013 for the benefit of Natural Resources Canada – Buildings Group – CANMET Center for Energy Technology - 1615, boul. Lionel-Boulet, C.P. 4800, Varennes QC J3X 1S6 under contract 3000505435.
Executive Summary
CO2 refrigeration systems (R744) resume their place because they have a neutral impact on the addition of greenhouse gases and because new engineering concepts have made their operation more energy efficient. A natural extension of these applications is arena refrigeration. CO2 is neither more nor less secure than other refrigerants and it has its advantages and disadvantages. As for all other refrigerants, the key to a secure system is to design, install and operate the system having identified, evaluated and disposed of all hazards by relying on well-trained personnel to design and operate the refrigeration system. The main hazard with CO2 is the possibility of generating lethal concentrations within confined spaces.
Simulations of CO2 leakage inside an arena were performed following the rupture of pipes supplying the refrigerant to cool the slab supporting the ice and pipes feeding the heaters for heating the arena. The gas is very heavy near the emission point, relative to air 2.3 to 1.5 after warming up. The gas tends to stratify in lower zones before dispersing. The intrinsically safe solution is to move the CO2 in the machinery room and to use heat transfer fluids for cooling the slab supporting ice and heating the arena and players’ chambers. It is recommended to perform a risk assessment when designing a CO2 refrigeration system in order to target the issues and implement a program of porcess safety to manage the operation of facilities.
CO2 refrigeration systems (R744) are resuming their place because they have a neutral impact on the addition of greenhouse gases and because new engineering concepts have made their operations more energy efficient. A natural extension of these applications is arena refrigeration. Some consider that CO2 is a long-term solution to arena refrigeration in a concept of sustainable development of this sector.
The unique properties of CO2 bring differences with ammonia [NH3 (R717)] for selection of building materials, components of the system, its design, commissioning and operation, the safety of these facilities for workers, users and the public outside of the arena (population surrounding the facilities).
The mandate of this study is to develop recommendations for carbon dioxide (CO2) arena refrigeration systems with the primary goal to comment on the safety of the facilities for the workers and population surrounding the facilities.
CO2 and its Characteristics
CO2 is non-flammable and non-toxic in comparison with other natural refrigerants - hydrocarbons (flammable) and NH3 (flammable and toxic). It is inexpensive, readily available anywhere in the world and is not subject to restrictions for its release into the atmosphere. The most important challenge is to design an efficient and reliable system that takes into account the unique characteristics of CO2, in particular, a pressure five times that of a typical NH3 system and a low critical temperature requiring cooling of a supercritical fluid instead of condensing a two phase mixture.
Although the triple point and critical points will not normally influence the selection of common refrigerants, this is not the case with CO2. At atmospheric pressure, CO2 can only exist in solid or gaseous form and cannot form liquid; under -78,4oC, it is a « dry ice » solid; at higher temperature it sublimes directly to gas. At 5.2 bar (75.1 psi) and -56,6oC, CO2 reaches a triple point. At this point, the three phases, e.g. solid, liquid and vapour simultaneously exist in equilibrium. CO2 reaches its critical point at 31,1oC. At this temperature, the density of the liquid and vapour are equal. As a result, at temperatures above the critical point, the distinction between the two phases disappears and a new phase, the supercritical phase, exists.
The pressures of CO2 refrigeration systems are much higher than those normally encountered in the refrigeration industry. They are still within the possibilities of mechanical refrigeration systems used in other industries. CO2 is considerably denser than NH3. This particular feature has several potential benefits including allowing for equipment (compressors and piping) with dimensions much smaller than those of similar capacity systems using NH3.
In addition, if there is a need to release the CO2 in case of overpressure, special measures must be taken to prevent the solid CO2 from blocking the gas outlets and adequate support of the piping for these equipments is required.
Population Exposure Limit to CO2 during Emergency Situations
At high concentrations, CO2 can affect respiratory function with asphyxia and even death. It has advantages and disadvantages. CO2 has a time weighted average concentration- 8 hours (TWA) of 5 000 ppm while NH3 has a TWA (VEMP) of 25 ppm. This concentration represents the highest level at which a worker can be exposed safely for eight hours. Although CO2 seems safer than ammonia, it can also be lethal. The advantage of ammonia is its unpleasant odor to alert exposed people to the presence of this gas. CO2 is odorless and colorless so that concentrations can be high without anyone being aware of it unless you have a detection system.
Effects on Humans
CO2 is classified as an A1 refrigerant (classification of toxicity and lower flammability according to ASHRAE Standard 34). It has a TWA (VEMP) 5 times higher than a hydrochlorofluorocarbon. This does not mean that it is 5 times safer. CO2 is generally considered as non-toxic but it will not support life and is very dangerous at concentrations greater than 10%. The threshold of the Immediately Dangerous to Life or Health (IDLH) of CO2 is 40 000 ppm, while that of ammonia is 300 ppm. Exposure to concentrations of CO2 in excess of 30 000 ppm causes discomforts that increase with time which include difficulty breathing, increased heart rate, headaches, dizziness, sweating and disorientation which could prevent the exposed person from evacuating the site to protect themselves. Table 1 presents the CO2 exposure thresholds for workers and people which are recommended by the Public Health.
Refrigerant | Name | Workers Regulation (ppm) | Population Threshold Values (ppm) | Important Properties | |||
---|---|---|---|---|---|---|---|
R744 | Carbon dioxide (CO2) | 5 000 | 40 000 | 5 000 | 30 000 (TEEL-1) | 30 000 (TEEL-2) | Simple asphyxiate |

Text Version
Acronyms
"VEMP" means "Value-weighted average exposure (8 hours) of the "Règlement sur la santé et la sécurité du travail". "IDLH" means "Immediately Dangerous to Life or Health". "No effects" is related to the airbone concentration to which an individual may be exposed to for up to one hour without experiencing adverse effects. "Transitory effects" are related to concentrations higher than AEGL-1, ERPG-1 or TEEL-1. "Irreversible effects" are related to to concentrations higher than AEGL-2, ERPG-2 or TEEL-2. "TLV" means "Threshold Limit Values". "P" egals RSST threshold value not to be exceeded for any period of time whatsoever. "RSST" means "Règlement sur la santé et la sécurité du travail". "CFC" means "Chlorofluocarbons". "HCFC" means "Hydrochlorofluocarbons". "HFC" means "Hydrofluorocarbons". "ppm" means "parts per million". "LEL" means "Lower Explosion Limit". Lastly, "n.a." means "not available".
Potential Dangers of CO2 Refrigerated Facilities
CO2 is neither more nor less safe than other refrigerants, but it has its advantages and disadvantages. As for all other refrigerants, the key to a safe system is to design, install and operate the system having identified, evaluated and disposed of all dangers by relying on well-trained personnel to design and operate the refrigeration system. The main danger of CO2 is the ability to generate lethal concentrations within confined spaces. The spaces where CO2 is used, or could potentially be present, must have sensors with alarms to determine the levels of CO2 and O2 so that attendees can be alerted and the space can be adequately ventilated. CO2 detection systems must be used in combination with adequate ventilation to protect workers and arena users. CO2 being heavier than air, the best place for the CO2 sensors is approximately at 1.3 m from the floor which is just under the level where the majority of people breathe. When the sensors detect a dangerous level of CO2 in a room, an alarm should be triggered and the room evacuated. In addition, special precautions must be taken to avoid pits or confined spaces that might allow accumulation of gas without anyone noticing. The two following examples describe conditions often subject to the accumulation of lethal concentrations of CO2: a relief valve whose discharge is restricted by other structures and a CO2 pump located in a lower point of the machinery room.
Fundamental Safety Principles for the Design of Refrigeration Systems
The same safety principles that apply to refrigeration systems using alternative refrigerants apply to CO2:
- Avoid hydraulic shocks.
- Prevent liquids from reaching the compressor.
- Include safety valves (relief valves) to release pressure when it is too high.
- Prevent excessive vibration.
- Support the equipment and piping independently.
- Take into account the very low temperatures and very high pressures in the choice of construction materials.
Unique Properties of CO2 which Affect Safety
- CO2 has unique physical properties that require special precautions.
- CO2 is naturally heavier than air (molecular weight 44 vs. 29 for air vs.17 for ammonia).
- CO2 is odourless even at lethal concentrations.
- CO2 presents unique effects on the respiratory system. Liquid CO2 has a very high expansion coefficient. One must ensure that CO2 is not trapped in the piping between closed valves. An increase in the temperature of the trapped liquid would cause a pressure increase that could easily exceed the pipe’s strength. This precaution also applies to vapour CO2 although at a lower level. The trapped vapour is not taken into account in assessing the safety of other refrigerants while for CO2; one must take it into account.
- Welding or heating must not be allowed on a piping system of a refrigeration system containing CO2.
- CO2 forms a solid when the gas or liquid at high pressure is released to the atmosphere. This solid can clog pipes and prevent depressurization.
- As CO2 systems are always in positive pressure, these systems are less likely to accumulate water. However, water is more soluble in the liquid CO2 phase than in vapour. The result is that there may be ice formation and clogging of the expansion valve.
- The high pressures of CO2 refrigeration systems distinguish them from other refrigeration systems. For example, pressures from 75 to 110 bar can be encountered.
- Safety valves (overpressure) protecting the equipment should be installed near the end of the line and should not be connected together via a main to a vent stack as it is the case for NH3. The rapid loss of pressure occurring through the safety valve can lead to the production of solid CO2, which could obstruct or cause an unacceptable loss of load in the pipe downstream of the valve. The output velocity combined with the ejected CO2 mass can exert a significant force on the piping which must be well anchored in place.
- Proper ventilation must be provided to the premises where CO2 is used. Avoid using CO2 when the gas can accumulate in low points or confined spaces. Leave area immediately in the case of significant release of CO2. Before returning to the site, ensure that CO2 concentrations are low enough. CO2 concentrations can be measured with fixed sensors or portable equipment.
- Individuals who have succumbed following exposure to CO2 must be brought out to open air quickly. Artificial respiration should only be given to individuals who have stopped breathing such as for drowning victims.
Particularities of CO2 | Consequence |
---|---|
CO2 leak in a confined space due to defects, deterioration of aging equipment, mechanical shock, earthquake, vibration due to misalignment of pumps, compressors, etc. |
|
High pressures, sometimes more than 100 bar (1 450 psig) with potential catastrophic failure. |
|
Low temperatures, sometimes less than -70oC |
|
Strong expansion of CO2 in vapour and liquid phase when trapped between closed valves |
|
Formation of solid CO2 at the discharge of pressure relief valves |
|
Challenges to drain the CO2 out of the equipment for maintenance |
|
Accidents
Several ruptures in supermarket CO2 refrigeration system piping with evacuation of occupants have been reported in the United Kingdom without consequences other than the evacuation of the premises by the occupants. In the United States, the explosive rupture of a pipe where the CO2 had solidified, which a technician was trying to melt by heating the pipe with a torch, caused a loss of life.
Typical Configuration of CO2 Refrigerated Arenas
There are two general approaches to the design of refrigeration systems using CO2 as a refrigerant:
- CO2 present in the arena enclosure.
- CO2 confined in the machinery room.
CO2 Present in the Arena Enclosure – Ice Rink Refrigeration
Figure 1 represents a diagram with circulation of liquid CO2 in the slab of ice. The installation includes two circuits of CO2. Liquid CO2 is pumped into a network of tubing which is buried in the floor of the rink. The flow of liquid CO2 is sufficient to allow return of the liquid and vapour towards the vapour/liquid separator tank (Low Pressure Liquid Receiver). The pressure in the separator tank is around 24.1 bar (350 psig). The compressors take suction on the vapour/liquid separator tank to bring the pressure to 103.4 bar (1,500 psig) and the temperature to about 104°C. A series of heat exchangers allows the heat of a glycol solution to warm the ground under the slab of ice, heat the enclosure and produce hot water. Finally, the gas is cooled in a gas cooler located outside (outdoor gas cooler).
The gas returns to the separator tank by passing through an expansion valve which leads to gas liquefaction. The gas/liquid separator tank, the circulation pump of the liquid CO2 in the slab, the compressors and heat exchangers to warm up the glycol solution and produce hot water are inside the machinery room. The gas cooler is outside the machinery room. The supply and return collectors of CO2 as well as the pipes buried in the floor of the rink are within the walls of the arena. The slab of refrigerated concrete supporting the ice acts as the refrigerant vaporizer. The heat exchanger that is buried in the refrigerated slab is composed of a network of copper tubing 1/2" ID (manufactured to withstand greater pressure than standard tubing) and whose exterior is covered with a thin layer of high density polyethylene to protect them from corrosion caused by contact with concrete. The tubing is arranged in the width axis of the rink.
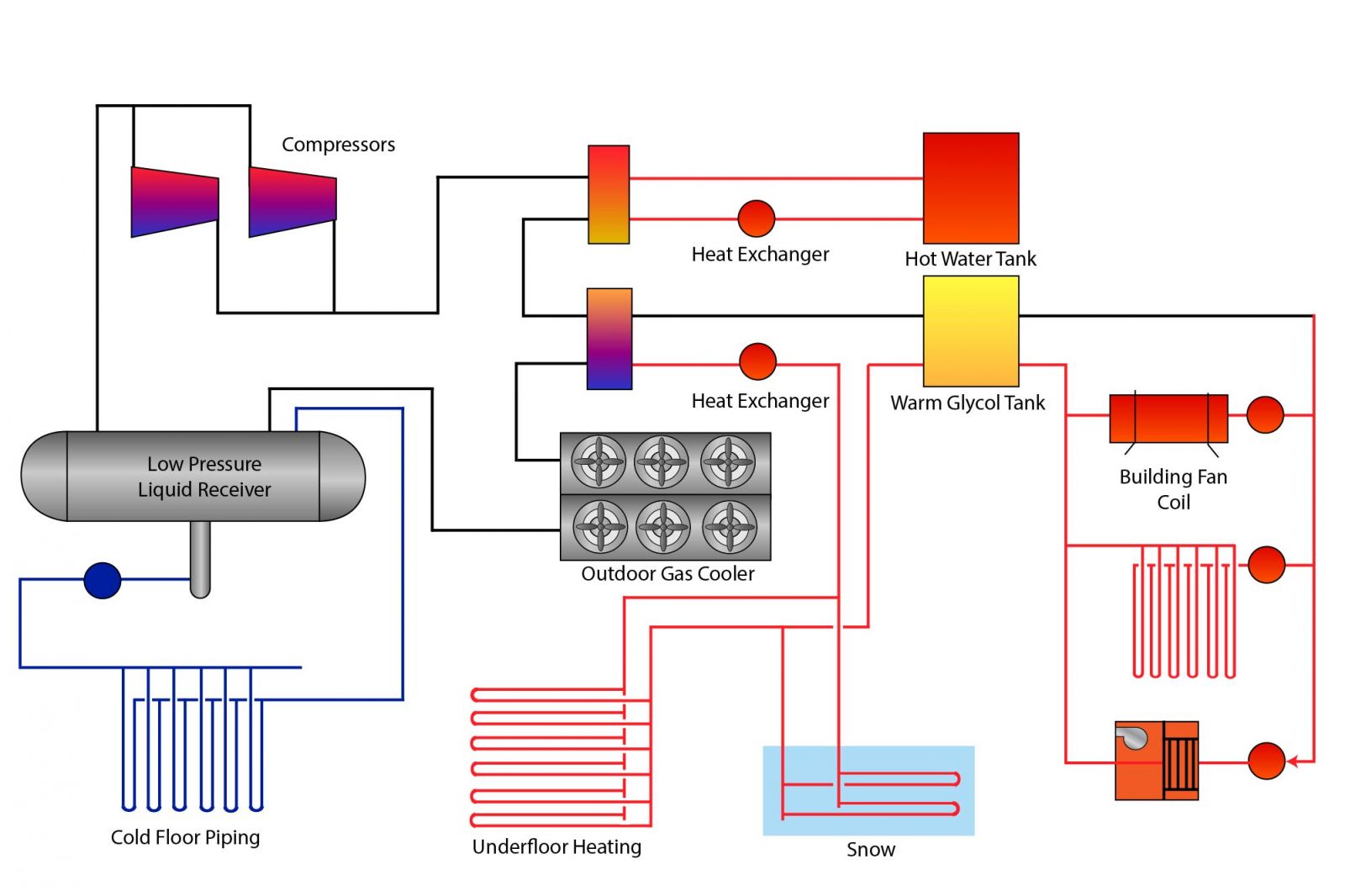
Appendix 5, Figure 1: Diagram of an arena refrigeration system with CO2 under the slab of ice
Text Version
Appendix 5, Figure 1: Diagram of an arena refrigeration system with CO2 under the slab of ice
The installation includes two circuits of CO2. Liquid CO2 is pumped into the network of tubing which is buried into the floor of the rink. The flow of liquid CO2 is sufficient to allow return of the liquid and vapour towards the vapour/liquid separator tank. The pressure in the separator tank is around 24.1 bar (350 psig). The compressors take suction on the vapour/liquid separator tank to bring the pressure to 103.4 bar (1,500 psig) and the temperature to about 104°C. A series of heat exchangers allows the heat of a glycol solution to warm the ground under the slab of ice, heat the enclosure and produce hot water. Finally, the gas is cooled in a gas cooler located outside.
The spacing between the 1/2 " tubing is 4 in c/c and configured into circuits of 2 passes on 85’. These tubing are embedded in the slab whose thickness is 3". Concrete cover over the tubing is about 1". (Figure 2)
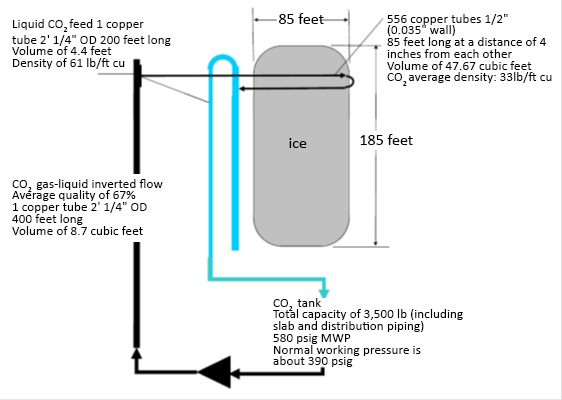
Appendix 5, Figure 2: CO2 supply in tubing under the slab supporting the ice
Text Version
Appendix 5, Figure 2: CO2 supply in tubing under the slab supporting the ice
The heat exchanger that is buried in the refrigerated slab is composed of a network of copper tubing and whose exterior is covered with a thin layer of high density polyethylene to protect them from corrosion caused by contact with concrete. The tubing is arranged in the width axis of the rink.
The channel that contains the CO2 collector is arranged along the axis of the length of ice. This channel is located under the players’ bench. Four CO2 sensors and a fan whose function is to suck gaseous CO2 coming from a leak to reject it outside of the building equip the gutter. The 1/2" piping has several joints in the concrete for « U bend » and assembly rings. These joints are joined by brazing. Figure 3.
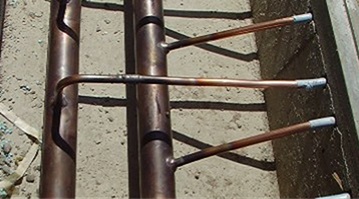
Appendix 5, Figure 3: Gutter for collecting CO2
Text Version
Appendix 5, Figure 3: Gutter for collecting CO2
The channel that contains the CO2 collector is arranged along the axis of the length of ice. The ½ inch piping has several joints in the concrete for U bend and assembly rings. These joints are joined by brazing.
The liquid CO2 refrigerant circulates in the heat exchanger that is buried in the chilled slab and is vapourized at a constant temperature and pressure from the entry point of the slab to its exit point. The refrigerant collector is a copper 2¼" of the return type reversed. Pressure at the pump discharge is 380 psig and 350 psig at the suction, representing a loss of 30 psig in the piping of the slab at maximum load conditions.
Safety Measures
During the summer season, when the ice is not in operation, the vaporizer in the slab is emptied of the CO2 refrigerant (liquid) so that the pressure in the heat exchanger does not exceed the designed pressure of 580 psig when the slab heats up. In case of power failure, as long as the ice covers the refrigerated slab, the pressure will remain at 290 psig. If the pressure in the heat exchanger exceeds the designed pressure; the relief valve would open and release the charge of refrigerant CO2 into the environment.
In summer, the pressure of the refrigerant in the refrigeration system must be kept below the design pressure of the components of the cooling system to avoid having to release the refrigerant charge into the atmosphere. A small refrigerant cooler of 4 HP on the monobloc, cools the air inside the machinery room is used to maintain the temperature and pressure in the refrigerant tank.
The Cooling Refrigerant Recirculation System
The refrigeration system uses a single refrigerant circuit, 7 compressors of 20 HP each which operate in a trans-critical cycle and collectively can develop 70TR at a discharge pressure of 1200 psig and 350 psig suction. The compressors are of a semi-hermetic type, which means that the compressor motor bathes in the R-744 refrigerant which cools it. The refrigerant tank is designed for a pressure of 40 bar (588 psig), the wall thickness of the vessel is 7/8" and the relief valve opens at 550 psig. The refrigerant tank is dimensioned to hold the refrigerant load in the cooling system [1306 kg of R-744].
Potential Hazards
Liquid CO2 leakage on the collectors located in the gutter that shelters them, on the pipes buried under the slab or at their connection point with the feed or return collectors represent a potential hazard to individuals located in the enclosure of the arena.
CO2 Present in the Arena Enclosure – Heating of the Enclosure
A proposed cooling system includes cooling the brine in a CO2-heat exchanger located in the machinery room and the heating of the enclosure by the hot CO2 from the compressor discharge. Only cold brine (similar to conventional ammonia systems) runs under the slab of ice. Compressors, CO2 tanks, gas/liquid separator, plate heat exchanger, CO2/brine exchangers, hot CO2/hot water are located in the machinery room. The air heaters heated by the hot high-pressure CO2 are in the enclosure of the arena (occupied zone) and the gas cooler is outside. The high-pressure CO2 gas is about 82.7 bar (1200 psig).
Potential Hazards
A leak in the hot CO2 piping feeding the air heaters located in the arena enclosure represents a potential hazard for the people who are present.
CO2 Contained in the Machinery Room
This design of the CO2 refrigeration system for arenas implies that all equipment containing CO2, with the exception of the hot CO2 cooler and its piping are inside the machinery room. The system includes a plate heat exchanger to cool the brine circulating in the ice and a glycol solution heat exchanger used for heating the enclosure and for hot water. This CO2 refrigeration system has no equipment containing CO2 in the occupied zone. All equipment containing CO2, with the exception of the gas cooler, are located inside the machinery room in order to prevent the exposure of individuals who are within the walls of the arena.
Potential Hazards
Potential hazards to people in the arena enclosure will be very low if there is a hermetic separation between the machinery room and the arena.
CO2 Leak Simulation inside the Enclosure of the Arena
The objective of these simulations is to determine the behaviour of CO2 following a leak. Three scenarios of CO2 leakage were studied:
- Liquid CO2 leak on a pipe circulating under the slab of ice at the same level as the gutter sheltering the CO2 collectors.
- CO2 gas leak on a pipe feeding an air heater located near the ceiling of the enclosure of the arena.
- Opening of the relief valve.
For scenarios 1 and 2, we assumed a complete failure of a pipe to identify the worst case consequences of such an event. We also assumed, for simplification purposes, that the system would drain itself of its full content of CO2. We are aware that a certain amount of CO2 would remain trapped inside the equipment. This simplification does not alter the general conclusions from the simulations.
Modelling for CO2 Leak Simulations
The simulation of accidental leakage of CO2 is a challenge because of its thermodynamic behaviour, including its phase diagram. At atmospheric pressure, CO2 is a solid that sublimes into a gas. This behaviour must be taken into account during the simulation. The simulations were performed with PHAST (Process Hazard System Tools) software by Det Norske Veritas (DNV) v. 6.7.
Liquid CO2 Leak of a Pipe of the Slab under the Ice
This scenario involves the rupture of a 1/2" pipe at the point of connection with a collector located in the gutter along the strip of ice.
Pipe diameter: ½ inch | Pressure: 400 psig | Temperature: -7,3oC |
---|---|---|
CO2 inventory: 3,500 lb | Flow: 6 kg/s | Duration: 4 min |
Gutter dimensions: 67,1 m (length) x 304,8 mm (depth) x 457,2 mm (width) | Gutter fan: 1,000 SCFM | Leak direction: horizontal with impact, 45o and vertical |
CO2 concentration to simulate: 30,000 ppm | Arena fan: 8,000 SCFM switched on instantly after a leak |
Figure 4 shows the elevation view of the concentration of 30,000 ppm of CO2 according to the horizontal directions (blue), 45o (green) and vertical (orange). One should note that the cloud resulting from the horizontal direction leakage has a height of 1 m and a length of 46 m. These distances are for the first few seconds; the CO2 will continue to accumulate behind the sideboards of the ice rink and will eventually overflow onto the ice rink. The 45o and vertical directions also present hazards because CO2 continues to accumulate near the ground. It should be noted that the concentrations near the ground would be much higher and could potentially exceed the lethal concentrations. In addition, for simulation purposes, we hypothesized the immediate start of the 8,000 SCFM fan. It would probably require at least 2 minutes before the fan would be functional and this fan, located at the roof of the building, would be inefficient for extracting a heavy gas that has accumulated near the ground.
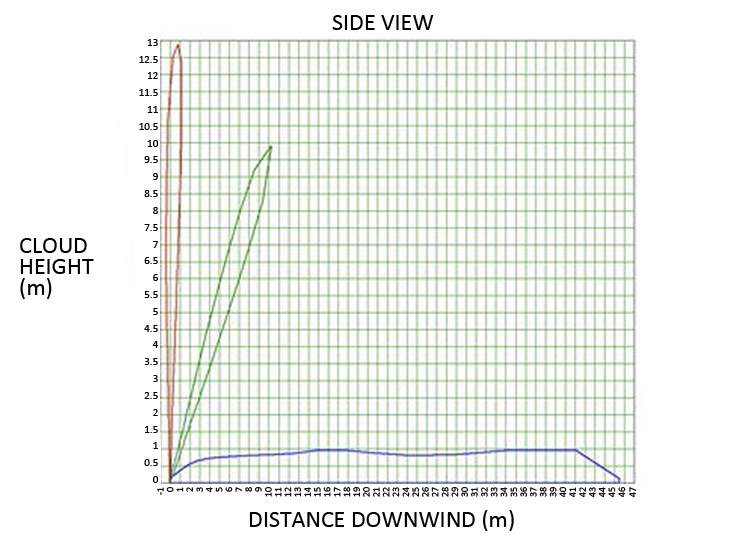
Text Version
Appendix 5, Figure 4: Elevation view of 30,000 ppm after a rupture of a ½ inch CO2 pipe
The figure shows the elevation view of the concentration of 30,000 ppm of CO2 according to the horizontal directions. The cloud resulting from the horizontal direction leakages has a height of 1 metre and a length of 46 metres.
Simulation Summary
These simulations were carried out to determine whether or not it is feasible to create hazardous situations following the accidental release of CO2 inside the walls of the arena (occupied zone) or outside the enclosure. These simulations have shown that it is possible. In the following Table, the confinement loss scenarios, consequences and potential mitigation measures are identified.
Intrinsically Safe CO2 Refrigeration Facilities
This chapter provides recommendations for making CO2 refrigeration systems that are used in arenas inherently safer. Approaches to the design of inherently safer systems have been grouped into four distinct strategies that are presented in order of priority:
Substitute | Contain CO2 in the machinery room - Substitute CO2 with heat transfer fluids to cool the slab under the ice or to heat the enclosure (occupied zone) and player rooms. |
Minimize | Use smaller amounts of CO2 – Use pipes with smaller diameters. |
Moderate | Use more resistant materials (for example, stainless steel instead of copper). Use welding procedures that allow a rigorous inspection of welds. |
Simplify | Designing facilities that eliminate complexities that are not needed, which will reduce the potential for errors. – Reduce the length of piping. |
Table 4: assumes a number of measures that can be applied to design inherently safer installations.
SCENARIO | CONSEQUENCES | POTENTIAL MITIGATION MEASURES |
---|---|---|
The introduction of CO2 into the enclosure of the arena (occupied zone) is not an inherently safe solution. This is to say that the risk will always be present. This risk must be managed by active mitigation measures. However, if the CO2 is contained in the machinery room, the risk to users of the arena is eliminated. The following paragraphs describe the simulated scenarios, their consequences and mitigation measures that could be used. | ||
Rupture of liquid CO2 tubing used to refrigerate the ice slab due to faulty work, defective materials, mechanical shock, earthquake, vandalism | Potential release of CO2 into the enclosure of the arena, the development of dangerous concentrations of an asphyxiating gas at the same level as the ice, players’ benches, lower rows of spectators. Potential loss of life. |
|
Pipe rupture in the enclosure of the arena releasing hot gaseous CO2 from compressor discharge due to faulty work, defective materials, mechanical shock or an earthquake | Potential release of CO2 into the enclosure of the arena, the development of dangerous concentrations of an asphyxiating gas at the same level as the ice, players’ benches, lower rows of spectators. Potential loss of life. |
|
Relief valve opening | Potential release of CO2 outside the arena with potential injury, exposure to asphyxiating gas, frostbite and potential loss of life. |
|
Risk Analysis and Operational Safety Management
CO2 arena refrigeration facilities include risks because of the important volumes of refrigerant, high pressures, low temperatures, the behaviour of this gas if released in the enclosure of the arena and the presence of a potentially vulnerable population (children on skates) that would make difficult the rapid application of an emergency plan. This is why it is necessary, when designing, to make a risk analysis for targeting the issues and developing an process safety program to manage operation of the facilities.
Risk Analysis
The risk analysis should identify the significant hazards associated with CO2 refrigeration systems and measures to reduce and control the risks to all people who may be affected including workers, arena users and the population surrounding the facilities. The risk analysis must be formally registered and shared with the work provider and the competent authorities who need to know such information to manage risks and implement the emergency plan. The risk analysis must be kept up to date.
Training in Health and Safety
The recommendations that have been made previously are intended to ensure the safety of workers, arena users and the public. Although they are not of complex application, it would be necessary to develop and disseminate a course whose objective would be to review the technology to ensure the safety of workers, arena users and the public, which would be intended for refrigeration system designers and arena managers. This training should be sanctioned by the Order of Engineers of Quebec. This program could be developed and distributed by an academic institution.
Conclusion and Recommendations
CO2 is a refrigerant that has potential because of its neutral characteristics on global warming and its potential for energy recovery. CO2 is neither more nor less secure than other refrigerants and it has its advantages and disadvantages. As for all other refrigerants, the key to a secure system is to design, install and operate the system having identified, evaluated and disposed of all dangers by using well-trained personnel to design and operate the refrigeration system. The main danger with CO2 is its ability to generate lethal concentrations within confined spaces.
Simulations were made of CO2 leakage in the enclosure of the arena following the rupture of tubing supplying the refrigerant to cool the slab supporting the ice and pipes feeding the heaters for heating the enclosure. The PHAST, v. 6.7 simulation software used for both determining the flow released to the atmosphere and the dispersion of gas takes into account the thermodynamic data of CO2 and the phase diagram. It is one of the best available tools. The rupture of a 1/2" liquid CO2 pipe at the same level as the gutter where are located the distribution and return headers can lead to an accumulation of gas in excess of 30 000 ppm in the lower parts of the arena including the players’ bench, the ice rink and lower rows of the spectator benches. The gas is very heavy near the emission point, 2.3 relative to the air to 1.5 after reheated. The gas will tend to stratify in the lower areas before dispersing. The rupture of a hot CO2 pipe from the compressors and feeding the air heaters could lead to an accumulation of CO2 in excess of 30 000 ppm in the lower parts of the arena. The problem is however less severe than a ruptured liquid pipe.
After taking into account the behaviour of CO2 following a liquid or gas leak, it can be concluded that:
- The inherently safe solution consists of containing the CO2 in the machinery room and to use heat transfer fluids for cooling the slab of ice and heating the enclosure and the players’ room.
In failure to confine the CO2 in the machinery room, it is recommended to:
- Use piping with a diameter smaller than 1/2" for the cooling of the slab of ice.
- Use a more robust and resilient material than copper.
- Reduce the number of pipe joints.
- Use welding procedures that ensure consistent quality;
- Take into account the potential effects of an earthquake in the refrigeration system design;
- Contain liquid CO2 collectors in a gutter with a robust and resilient cover that can withstand pressure that might be developed, equipped with CO2 sensors with alarm and a fan of adequate capacity whose outlet is directed to a safe place.
- Provide ventilation of the enclosure of the arena with extraction nozzles at the lower parts of the arena;
- Set the discharge of the relief valve to a safe place, fence the area to prevent people from placing themselves in a dangerous position;
- Ensure that the pressure relief valve is at a safe distance from the arena exits and from the machinery room;
- Ensure that the piping is sufficiently anchored to withstand the reaction force resulting from the discharge of CO2 at high speed;
- Ensure that areas where CO2 is used or could potentially be present have detectors with alarms to determine the levels of CO2 and O2 so that people can be alerted and the space adequately ventilated;
- Make a risk a process safety program to manage the operation of facilities;
- Develop a management program of process safety that includes the following elements:
- Accountability: Appoint a person responsible for the prevention programs and emergency plans of the CO2 refrigeration facilities.
- Know the process: Keep the refrigeration documentation to include drawings and procedures up to date.
- Process hazards: Keep the list of process hazards up to date.
- Prestartup safety reviews: Make prestartup safety reviews before start up after prolonged shutdown, repairs or modifications to facilities.
- Change management: Establish a procedure for managing changes to facilities or procedures to ensure that compliant parts are used for maintenance.
- Management of contractors: Establish a procedure for managing contractors working in these facilities.
- Mechanical integrity: Establish a program to maintain the mechanical integrity of the equipment : preventive maintenance.
- Procedures: Develop critical operating and maintenance procedures.
- Training: Provide training for equipment operation, maintenance, emergency plan.
- Emergency plan: Develop an emergency plan that covers the residents, the operating staff and users of the arena. This plan covers communication provided to the population surrounding the facilities, alert, evacuation, sheltering, response.
- Verifications: Make verifications of compliance of the program at a set frequency.
- Develop a training program on the safety of refrigeration systems intended to designers of refrigeration systems and sanctioned by the Order of Engineers of Quebec. This program could be developed and distributed by an academic institution.
Appendix 6: Risk Management Guide for Halocarbon Arena Refrigeration Systems
Development of a Risk Management Guide for Designers of Arena Refrigeration System using Halocarbons as Refrigerants
Jean-Paul Lacoursière, Eng., Stéphanie Lacoursière, Eng., M. Eng.
JP Lacoursière inc.
35, rue Lemoyne, Repentigny, (Québec) Canada J6A 3L4
T: (450)-581-2315; C: (514) 770-2315; F: (450) 581-4539
E-mail: jpla@sympatico.ca
Report No. P00460-1-AB-rev0
This summary report is an overview of the full report of the same title published on March 31, 2013 for the benefit of Natural Resources Canada – Buildings Group – CANMET Center for Energy Technology - 1615, boul. Lionel-Boulet, C.P. 4800, Varennes QC J3X 1S6 under contract 3000505435.
Executive Summary
Hydrochlorofluorocarbons (HCFCs) and hydrofluorocarbons (HFC) were introduced later as a refrigerant. CFCs and HCFCs are partly responsible for the destruction of the ozone layer. The Montreal Protocol is aiming for a complete ban of CFCs and HCFCs including R-22. HFCs, which were developed to replace CFCs and HCFCs, do not destroy the ozone layer but are known as powerful greenhouse gases. HFC refrigeration systems represent an alternative for arena refrigeration when ammonia [NH3 (R717)] or carbon dioxide [CO2 (R744)] present unacceptable risks for the population surrounding the facilities or arena users and that the costs of preventive and mitigation measures are judged unacceptable. The risk assessment must identify the significant hazards associated with the HFC refrigeration system and the measures to reduce and control risks for all individuals who could be affected including workers, arena users and the population surrounding the facilities. In addition, a process safety management program that takes into account maintenance and emergency plans must be put into place.
Chlorofluorocarbons (CFCs) have been used as refrigerants since the 1930’s. Hydrochlorofluorocarbons (HCFCs) and hydrofluorocarbons (HFCs) were introduced later on as refrigerants. CFCs and HCFCs are partly responsible for the destruction of the ozone layer. The Montreal Protocol is aiming for a complete ban of CFCs and HCFCs including R-22. HFCs, which were developed to replace CFCs and HCFCs, do not destroy the ozone layer but are known as powerful greenhouse gases.
HFC refrigeration systems represent an alternative for arena refrigeration when ammonia [NH3 (R717)] or carbon dioxide [CO2 (R744)] present unacceptable risks for the population surrounding the facilities or arena users and that the costs of prevention and mitigation measures are judged unacceptable. Particular precautions must however be taken for a safe use of HFCs in arenas.
Issues and Mandate
The mandate is to develop a technical study on hydrofluorocarbons (HFCs) used for arena refrigeration with main goal to comment on the safety of these facilities for workers, arena users and the public outside of the arena (population surrounding the facilities).
HFCs and their Characteristics
A refrigerant must satisfy many requirements including some that are unrelated to their ability to transfer heat. Stability at conditions of use is an essential property. Flammability and toxicity are important properties in the case of arena refrigeration. In addition, effects on the ozone layer and the potential for greenhouse gases are also important considerations to take into account for the choice of refrigerant.
Refrigerants are classified into safety groups according to the following criteria. Safety classification consists of two alphanumeric characters (e.g., A2 or B1). (ASHRAE Standard 34 - 2010).
Refrigerants are classified into two levels of toxicity – A or B according to the permitted exposure level:
- Class A refrigerants have the lowest toxicity level as indicated by the permitted exposure limit (PEL) of 400 ppm or more, if the toxicity has been defined and a time weighted average exposure level (TWA) (VEMP) of 400 ppm or more.
- Class B refrigerants have a higher toxicity level as indicated by the permitted exposure limit (PEL) of less than 400 ppm, if the toxicity has been defined and a time weighted average exposure level (TWA) (VEMP) of less than 400 ppm.
Refrigerants are classified into three flammability levels (1, 2, 3) and an optional subclass (2L) according to lower flammability limit tests, combustion heat and the optional measurement of combustion speed;
- A refrigerant composed of a single chemical substance is of Class 1 when it has no flame propagation when tested in the air at 60oC and 101.3 kPa. Specific settings apply to refrigerant composed of several chemical substances..
- A refrigerant composed of a single chemical substance is of Class 2 when it encounters the following three conditions :
- Presents a flame propagation when subject to a test in the air at 60oC and 101.3 kPa;
- Presents a lower flammable limit (LFL) >0.10 kg/m3 at 23oC and 101.3 kPa (other conditions may apply if the refrigerant has no LFL at these conditions); and,
- Has a combustion heat <19 000 kJ/kg.
- A refrigerant composed of one chemical substance is of Class 2L when it has a maximum speed of combustion ≤10 cm/s when subjected to a test in the air at 60oC and 101.3 kPa;
- A refrigerant composed of one chemical substance is of Class 3 when it meets the two following conditions:
- Presents a flame propagation when subjected to a test in the air at 60oC and 101.3 kPa.
- Presents a lower flammable limit (LFL) ≤0,10 kg/m3 at 23oC and 101.3 kPa or a combustion heat ³19 000 kJ/kg (other conditions may apply if the refrigerant has no LFL at these conditions).
Other parameters apply concerning life-threatening exposure limits (mortality, sensitive cardiac system, effects on the central nervous system, other effects preventing safe evacuation), and decreasing of the concentration of oxygen (ASHRAE Standard 34 2010).
The following table on hazardous concentrations of CFCs, HCFCs and HFCs is an excerpt from an e-mail providing the main properties of refrigerants and exposure thresholds, Slavko Sebez, Public Health of the National Capital, 2013.
Refrigerants | Name | Workers Regulation (ppm) | Population Threshold Values (ppm) | Important Properties | |||
---|---|---|---|---|---|---|---|
R12 (CFC) | Dichlorodifluorométhane | 1 000 | 15 000 | 1 000 | 3 000 (TEEL-1) | 10 000 (TEEL-2) | Non-flammable |
R22 (HCFC) | Chlorodifluorométhane | 1 000 | n.a. | 1 000 | 1 250 (TEEL-1) | 7 500 (TEEL-2) | Non-flammable |
R32 (HFC) | Difluorométhane | n.a. | n.a. | n.a. | 1 300 (TEEL-1) | 1 300 (TEEL-2) | Non-flammable, simple asphyxiating |
R125 (HFC) | Pentafluoroéthane | n.a. | n.a. | n.a. | n.a. | n.a. | Non-flammable, simple asphyxiating |
R410A( HFC) | R32 and R125 mixture | n.a. | n.a. | n.a. | n.a. | n.a. | Non-flammable, simple asphyxiating |

Text Version
Acronyms
"VEMP" means "Value-weighted average exposure (8 hours) of the "Règlement sur la santé et la sécurité du travail". "IDLH" means "Immediately Dangerous to Life or Health". "No effects" is related to the airbone concentration to which an individual may be exposed to for up to one hour without experiencing adverse effects. "Transitory effects" are related to concentrations higher than AEGL-1, ERPG-1 or TEEL-1. "Irreversible effects" are related to to concentrations higher than AEGL-2, ERPG-2 or TEEL-2. "TLV" means "Threshold Limit Values". "P" egals RSST threshold value not to be exceeded for any period of time whatsoever. "RSST" means "Règlement sur la santé et la sécurité du travail". "CFC" means "Chlorofluocarbons". "HCFC" means "Hydrochlorofluocarbons". "HFC" means "Hydrofluorocarbons". "ppm" means "parts per million". "LEL" means "Lower Explosion Limit". Lastly, "n.a." means "not available".
The dangers of refrigerants are related to their physical and chemical properties at pressures and temperatures associated with arena refrigeration systems and location of refrigeration equipment in relation to zones occupied by the arena users (ASHRAE Standard 15, 2010). Injuries, loss of life and property damage can be caused by several events including:
- The rupture of a component under pressure or an explosion with potential flying debris or collapse of the building.
- The release of refrigerant due to a leaky component (pipe), a leak in a mechanical seal or improper operation.
- The release of refrigerant due to corrosion under insulation of piping.
- A fire or explosion resulting from a deflagration or powered by the refrigerant or lubricating oil.
- The accumulation of lubricating oil in evaporators which can reduce heat transfer or circulation of refrigerant.
Injuries or loss of life may occur due to the release of refrigerant including:
- Suffocation by refrigerants heavier than air released into spaces that are not adequately ventilated.
- Narcotics or sensitization of the cardiac system.
- Toxic effects of refrigerant vapour or their decomposition products following contact with flames or hot surfaces.
- Corrosive attacks to eyes, skin and other tissues.
- The freezing of tissue in contact with cold liquid.
HFCs are generally non-flammable and do not pose a fire or explosion hazard under normal refrigeration system conditions. In some unusual circumstances, some HFCs have flammable characteristics, e.g., R-134a (1,1,1,2 -Tetrafluoroéthane).
Fundamental Safety Principles
The same safety principles that apply to refrigeration systems that use alternative refrigerants apply to HFCs, namely:
- Avoid hydraulic shocks.
- Prevent liquids from reaching the compressor.
- Include safety valves (pressure relief) to release pressure when it is too high.
- Prevent excessive vibration.
- Support the equipment and piping independently.
- Take into account the very low temperatures and very high pressures in the choice of construction materials.
- Dimension pipes (diameter and length) to transport the lubricating oil without excessive pressure loss which would cause a loss of efficiency in the refrigeration system.
- Develop a maintenance program including preventive maintenance for critical equipment.
- Develop an emergency response plan with trained staff and keep it functional.
HFCs have unique physical properties that require specific precautions.
- HFCs are naturally heavier than air. They tend to accumulate in low points if they are released to the atmosphere.
- Copper pipes for HFCs may have a small diameter and be fragile on impacts.
- Vibration generated by the compressors may cause rupture of brazed joints.
- Presence of humidity in the refrigerant can lead to ice formation in the expansion valve.
- Particles of rust or metal can deposit on the seats of solenoid valves, preventing the valve from hermetically sealing.
Typical Configuration of HFC-Cooled Arenas
Figure 1 shows a schematic diagram of an arena refrigeration system with circulation of HFCs.
The refrigeration system includes the cooling of brine circulating under the slab of ice with a HFC heat exchanger located in the machinery room and the heating of the arena and the shower water by hot gaseous HFCs from the compressor discharge.
Compressors, HFC gas/liquid separator tanks, the HFC/brine heat exchanger and the HFC/secondary fluid (ethylene glycol) condenser are located in the machinery room. The air heaters located within the enclosure of the arena (occupied zone) are powered by the secondary fluid loop which recovers heat from the refrigeration system.
After recovery of the heat of the air heaters and/or heat pumps, the excess heat from the secondary fluid loop is rejected to the fluid cooler located outside of the arena.
Potential Hazards
All refrigerant is contained inside the machinery room. The hazard zone is limited to the occupants of this room. There are no hazards that have been identified for the population surrounding the facilities.
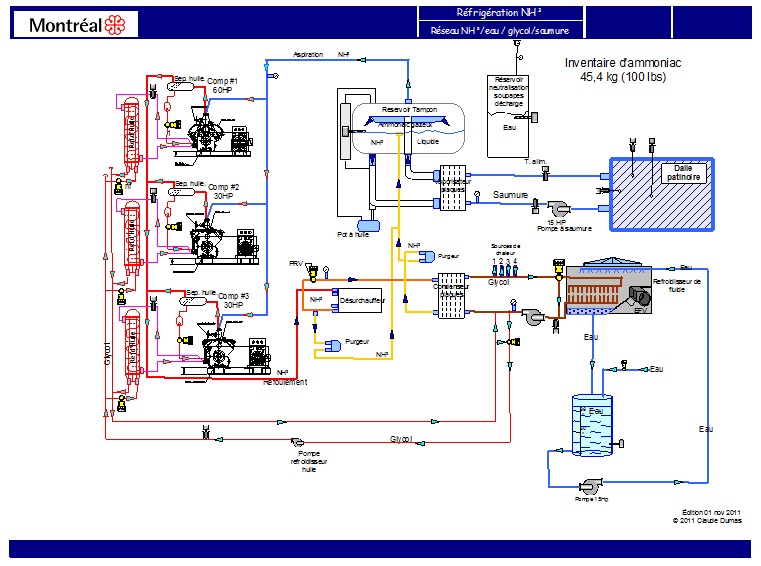
Text Version
Appendix 6, Figure 1: Semi-hermetic monobloc system with heat pump for water heating
Schematic diagram of an arena refrigeration system with circulation of HFCs. The refrigeration system includes the cooling of brine circulating under the slab of ice with a HFC heat exchanger located in the machinery room and the heating of the arena and the shower water by hot gaseous HFCs from the compressor discharge.
Machinery Room
The following clauses from Chapter 6 of the Mechanical Refrigeration Code (CSA B52-05) are reproduced for purposes of understanding the infrastructures where we find HFC refrigeration equipment.
Foundations and condenser supports, compressor-condenser units and motorcompressors must be robust and non-combustible.
Mechanical parts must comply with all regulations relating to workplace hygiene and safety.
The safe inspection and maintenance of refrigeration system equipment shall be provided in at least one of the following ways:
- Floor-mounted equipment shall be installed in a manner that allows sufficient clearance around the equipment for safe maintenance and service.
- Equipment that is not accessible from floor level shall be installed so that it can be safely reached:
- by a permanently installed staircase(s) or ladder(s) with a platform(s) and railings meeting the workplace safety requirements of the jurisdiction where the equipment is installed; or
- by a mobile device(s) for lifting personnel to the equipment. The use of such a device, as an alternative to the fixed means of access specified in Item (b)(i), shall be permitted only if it is normally on the premises at all times, is acceptable under the workplace safety requirements of the jurisdiction, and if the nature of the refrigeration equipment is such that it can be safely serviced in this way.
- Roof- and mezzanine-mounted equipment shall be set back 3 m (10 ft) from any edge where a fall hazard exists, except under the conditions specified in Item (d). If the workplace safety requirements of the jurisdiction of installation impose a greater setback, those requirements shall apply.
- Where roof- and mezzanine-mounted equipment cannot be set back as specified in Item (c), railings and fall-arrest system attachment points shall be provided in accordance with the workplace safety requirements of the jurisdiction of installation.
Each machinery room shall have a door or doors that open outward, are self-closing (and tight fitting if they open into the building), and are of a number large enough to ensure that persons can escape in an emergency. The doors shall not open to a public corridor or any room used for assembly. With the exception of access doors and panels in air ducts and air handler units, there shall be no openings that will permit passage of escaping refrigerant to other parts of the building.
Every machinery room must have at least one door that opens outwards and that has automatic closing (and sealing if the doors open towards the building). The number of doors should be sufficient to enable people to quickly leave the room in case of emergency. The doors must not open on a public corridor or meeting room. With the exception of doors and access panels for air ducts or conform equipment for processing air, the machinery room must have no openings through which the refrigerant can escape.
HFC Leak Detectors
A HFC leak detector must be installed in a place where HFC leaking is most likely to be found (e.g. at 1.3 m from the ground) and must be activated at a value not greater than the VEMP (TLV/TWA). Once activated, the detector must:
- Trigger an alarm that is easy to hear, and
- Activate the fan.
Note: In some cases, several detectors or detection points may be required (e.g. because of the configuration of the machinery room or air flow patterns).
Ventilation
The air in the equipment room must be vented towards the outside. Ventilation required under Code B52-05. It should be noted that HFCs are heavier than air. Ensure fan suction is near the ground. The fan capacity must comply with the requirements of Code B52-05.
Risk Analysis and Management of Operational Safety
HFC refrigeration arena facilities involve risks due to high volumes of refrigerant, high pressures, low temperatures, the behaviour of these gases if they are released in the enclosure of the arena and the presence of potentially vulnerable populations (children on skates) making the rapid implementation of an emergency plan difficult. That is why it is necessary, when designing, to make a risk analysis for targeting issues and to develop an operational safety program to manage facility operations.
Risk Analysis
The risk analysis must identify the significant hazards associated with the HFC refrigeration system and measures to reduce and control the risks to all people who may be affected including workers, arena users and the population surrounding the facilities. The risk analysis must be formally recorded and shared with the work provider and the competent authorities who need to know such information in order to manage risks and implement emergency plans.
The risk analysis must be kept up to date.
Operational Safety Management
The safety of HFC refrigeration facilities requires a holistic management program. The elements of the program presented in the following paragraphs are based on recommended practices by IIAR and FM Global.
- Accountability: Appoint a person responsible for the prevention programs and emergency plan of HFC refrigeration facilities.
- Know the process: Keep the drawings and procedures up to date.
- Process hazards: Keep the list of process hazards up to date.
- Prestartup safety reviews: Make prestart safety reviews before start-up after prolonged shutdown, repairs or modifications to facilities.
- Change management: Establish a procedure for managing changes to facilities or procedures to ensure that compliant parts are used for maintenance.
- Management of contractors: Establish a procedure for managing contractors working in these facilities.
- Mechanical integrity: Establish a program to maintain the mechanical integrity of the equipment : preventive maintenance.
- Procedures: Develop critical operating and maintenance procedures.
- Training: Provide training for equipment operation, maintenance, emergency plan.
- Emergency plan: Develop an emergency plan that considers the population surrounding the facility, the personnel and the users of the arena. This plan covers communications provided to the population, alert, evacuation, sheltering, response.
- Verifications: Make verifications of compliance of the program according to a set frequency.
Emergency Intervention Plan
Safety of HFC refrigeration requires the establishment of an emergency response plan that must at least include the following objectives:
- Ensure that the personnel is well-trained on the specific operating procedures, the various refrigerant hazards, the equipment (compressors, pumps, heat exchangers) and interventions to be made in case of leak or other emergencies.
- Identify and train personnel (operation, maintenance and monitoring (arena staff, guards, etc.) that have to respond in case of refrigerant spills or leaks. Ensure that personnel are aware of the dangers of the refrigerant used in the arena. Ensure that the right equipment is available and accessible including gas detectors, self-contained breathing apparatus (SCBA), protective clothing, and fans. Have training sessions and exercises at a regular frequency.
- Identify people outside the arena that should be alerted during an emergency. This could include fire services, emergency health (ambulances) and environmental authorities.
- Ensure that the critical valves that control the flow of refrigerant are clearly identified.
Conclusions and Recommendations
HFC refrigeration systems are an alternative for arena refrigeration when ammonia [NH3 (R717)] or carbon dioxide [CO2 (R744)] present an unacceptable risk to the population surrounding the facilities or arena users and the costs of prevention and mitigation are judged unacceptable.
It is recommended to:
- Make a risk analysis when designing a HFC refrigeration system for targeting the issues and developing an operational safety program to manage the operation of facilities.
- Develop a process safety management program that includes the following elements :
- Accountability: Appoint a person responsible for the prevention programs and emergency plans of the HFC refrigeration facilities.
- Know the process: Keep the refrigeration documentation which includes drawings and procedures up to date.
- Process hazards: Keep the list of process hazards up to date.
- Prestartup safety reviews: Make prestartup safety reviews before start-up after prolonged shutdown, repairs or modifications to facilities.
- Change management: Establish a procedure for managing changes to facilities or procedures to ensure that compliant parts are used for maintenance.
- Management of contractors: Establish a procedure for managing contractors working in these facilities.
- Mechanical integrity: Establish a program to maintain the mechanical integrity of the equipment - preventive maintenance.
- Procedures : Develop critical operating and maintenance procedures.
- Training: Provide training for equipment operation, maintenance, emergency plan.
- Emergency plan: Develop an emergency plan that considers the population surrounding the facility, the personnel and the users of the arena. This plan covers communications provided to the population, alert, evacuation, sheltering, and response.
Verifications: Make verifications of compliance of the program according to a set frequency.
Page details
- Date modified: