Energy Performance Financing Drives Project at Ford of Canada
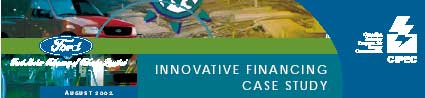
The Company
From the time the first vehicle rolled off a Canadian production line in 1904, the Ford Motor Company of Canada, Limited has been a stalwart of Canadian industry. One of the world's largest and most renowned vehicle manufacturers, the company is dedicated to preserving the environment for tomorrow, while making automobiles today.
Achieving this goal sometimes requires innovative approaches. Such was the case when Ford of Canada decided it was time to upgrade a 50-year-old steam heating system that serviced two vehicle assembly plants in Oakville, Ontario. With an operating efficiency below 60 percent, the company sought ways to improve efficiency and reduce costs.
"The inefficiency of this old heating system was enough motivation for us to turn to the advanced means of heating a plant that are now widely available," says Ford of Canada's Gary Conrad, Power Systems Engineer at the Oakville site. Energy consumption by Canada's manufacturing sector for plant heating and other purposes is a source of carbon dioxide and other greenhouse gas (GHG) emissions that are contributing to climate change. Companies like Ford of Canada are voluntarily taking steps to help reduce GHG emissions improving the efficiency of its operation, company is also cutting costs and improving bottom line.
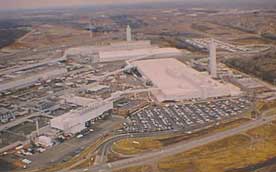
The two ISO-14001-certified plants at Ford's Oakville site are the first in Canada to have the Big Foot gas-fired air-heating technology installed.
Ford's Environmental Commitment
Environmental responsibility is a priority at Ford of Canada. Norm Stewart, Vice-President, Government Relations, and General Counsel at Ford of Canada says, "As a vehicle manufacturer, we have been taking steps in our operations that are aimed at preventing pollution and enhancing environmental protection. Environmental considerations have become an integral part of our mainstream business decisions for our day-to-day operations and part of our continuous improvement philosophy. We seek out innovative, creative solutions to reduce or eliminate the impact of our manufacturing operations on the environment."
Ford of Canada's environmental achievements received special acknowledgement in 1999, when the company accepted a prestigious Leadership Award in the Transportation Manufacturing Category from Canada's Climate Change Voluntary Challenge and Registry Inc. (VCR Inc.). A Gold Level Champion Reporter with VCR Inc., Ford received the award for having all of its Canadian manufacturing facilities certified to the ISO 14001 Environmental Management Systems standard and for dedicating approximately half of its annual worldwide laboratory research funding to environmental issues. These included reducing GHG emissions through the use of alternative fuels, more efficient vehicles and improved manufacturing technology. The company is also a member of the Industrial Energy Innovator's program of Natural Resources Canada's Office of Energy Efficiency and an active member of the Canadian Industry Program for Energy Conservation (CIPEC).
Mr. Conrad notes, "Ford of Canada is continually looking for ways to improve processes and minimize the environmental impact of our facilities and the vehicles we produce." The replacement of the steam heating system at the Oakville site, completed in August 2001, was one more step in this ongoing process. What sets this project apart is that it was financed and implemented by a third party through an innovative technique known as energy performance contracting.
Energy Performance Contracting
Energy performance contracting enables a company to finance large energy efficiency projects without making an initial investment, entering a lease or arranging funding. The concept of energy performance contracting is creative and simple. The process begins when an energy service company (ESCo) audits a company's facilities and operations to identify energy-saving opportunities. The ESCo then submits a proposal to the audited company. If the audited company accepts the recommendations, the two parties enter into a contract that commits the ESCo to undertaking the energy efficiency projects using its own finances. The ESCo will recover its investment over the next few years from the resulting measured energy savings.
The Oakville Retrofit Project
Ford Of Canada's Oakville site consists of four steam-heated plants – the Oakville Assembly Plant (180 000 m2, or 2 million sq. ft.), the Ontario Truck Plant (90 000 m2, or 1 million sq. ft.), a waste-water treatment plant and a boiler (power) house. Before the retrofit project began, the boiler house, built in 1952, supplied both assembly plants with steam heating. Plant engineers realized the system was inefficient compared to contemporary technology.
Meanwhile, Professional Supply Inc. (PSI), which is based in Fremont, Ohio, specialized in innovative industrial heating, ventilating and air-conditioning systems and non-pressurized hot water systems. Working through its Canadian subsidiary, PSI proposed to convert Ford of Canada's steam heating system to a more efficient natural gas system on a performance-contracting basis.
After carefully reviewing PSI's technical and financial proposal and energy analysis, Ford of Canada's Oakville Assembly Plant engineers decided to pursue the project. They signed an Energy Service Agreement with the company. The project then shifted into high gear, and 14 months later the antiquated steam heating plant had been replaced with state-of-the-art technology.
Big Foot to the Rescue
Klas Bockasten, Project Manager with Sandwell Consulting Engineers Ltd. explains, "PSI's solution to the high energy consumption and costs at the Oakville plants was to install several gas-fired air-heating units known as Big Foots." (Sandwell was contracted to provide detailed engineering services for the project.)
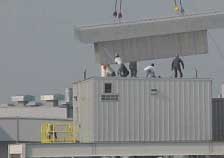
One of the 13 Big Foot air-heating units is delivered and installed on the roof of Ford's Oakville Assembly Plant.
Each Big Foot consists of a large air house containing two 100-horsepower fans. Fresh outside air is heated by a direct-fired natural gas burner and mixed with return air to provide building air balance. Supply air is kept between 10° and 32°C (50° and 90°F) at the discharge head. This tempered air forces the hot air down, keeping the temperature at floor level virtually constant at 21°C (70°F) in winter. In summer, the temperature of the plant at floor level will not exceed the outside air by more than 3°C (5°F).
A total of 13 Big Foot rooftop units were installed (eight at the Oakville Assembly Plant and five at the Ontario Truck Plant), creating a new ductless heating and ventilation system. A central computer monitors the system and controls building and atmospheric conditions and energy consumption. Space temperature is monitored at three levels: ceiling, mid-height and 1.5 m (5 ft.) above the floor. Sensors and control devices are interconnected to enable heating and ventilation equipment to operate as a unified system, rather than as components. Ideal fuel consumption is calculated for each unit and for the total plant. Any deviation from this target can trigger an alarm to indicate excessive fuel usage.
Variable outside air dampers on the rooftop Big Foot installations are controlled by air-pressure sensors throughout the plant, all co-ordinated by the central computer system. Process exhaust fans located on the roof of both plants have been disconnected and replaced with wall-mounted pressure relief dampers, assuring air change throughout the plant. Recirculated air from the plant is modulated through the return air damper.
First Canadian Installation
The new technology has been successfully installed in several U.S. automotive plants, but Ford's Oakville site was the first Canadian installation. The entire project was implemented on a turnkey basis, with the Canadian subsidiary of PSI providing all services – from final design through construction, project start-up, commissioning, site training, maintenance specification and an annual maintenance allotment for the new equipment. Sandwell provided detailed engineering work on a fast-track basis. And the installation contractor – The State Group Limited –installed grillage, gas piping, electrical distribution and other components in preparation for lifting the Big Foot units into place.
"Environmental considerations have become an integral part of our mainstream business decisions for our day-to-day operations and part of our continuous improvement philosophy."
– Norm Stewart, Vice-President, Government Relations, and General Counsel at Ford of Canada
Mr. Conrad, who worked closely with PSI and the sub-contractors in executing the project, reports that the Big Foot installations are expected to reduce energy consumption in the two plants by 225 million Btu per hour. The projected maximum annual emissions reductions are estimated to be
- 102 metric tonnes of oxides of nitrogen
- 13 metric tonnes of carbon monoxide
- 6.6 metric tonnes of particulate matter
- 4.4 metric tonnes of volatile organic compounds
- 0.5 metric tonne of sulphur dioxide
- 12 metric tonnes of carbon dioxide emissions reduction
Conclusion
Installing the Big Foot solution at the Oakville site is part of Ford of Canada's ongoing efforts to reduce energy consumption and emissions. Already, the company has reduced GHG emissions by 4 percent at its assembly facilities, 37 percent at engine and engine component facilities and 8 percent at production metal casting facilities. Ford of Canada is committed to continued reductions in energy consumption of 1 percent per year through 2005.
Leading Canadians to Energy Efficiency at Home, at Work and on the Road
The Office of Energy Efficiency of Natural Resources Canada strengthens and expands Canada's commitment to energy efficiency in order to help address the challenge of climate change.
© Her Majesty the Queen in Right of Canada, 2002
Cat. No. M92-247/2002E ISBN 0-662-32751-9
(Aussi disponible en français sous le titre : Un marché de services éconergétiques rend possible un projet chez Ford du Canada)
Page details
- Date modified: